We all know that motor drive is one of the main application areas of IGBT. Some students may have such confusion:
"IGBT is originally used to drive the motor, so why does it need a driver? What does the IGBT driver do?"
This question is simple to explain, just as it is said in "Simplified Power Electronics": "IGBT is essentially an electronic switch, just like the switch on the wall in your home. Press it once, the switch is closed, and the light comes on; press it again, and the light goes out.
Of course, the IGBT is operated by electronic pulses instead of hands. When a high level comes, the device is turned on; when a low level comes, the device is turned off. Manual operation of the switch may be once or twice a second, while our electronic switch can be turned on and off tens of thousands or even hundreds of thousands of times a second.
So now the question is: where do the electronic pulses that control the IGBT come from?
Some students are about to raise their hands: I know, I know! The control pulse can come from the MCU!
Excellent! You can answer all the questions!
MCU is like our brain, it controls every move of our body. But the neuron signal it sends is very weak and cannot press the switch at all. So the brain needs to transmit this signal to the hand, and the hand muscle movement generates a certain amount of force to press the switch. The IGBT driver is the dexterous and powerful "hand" that controls the IGBT.
So, what does the signal go through on its way from MCU to IGBT driver chip?
first
The output current of MCU is at mA level, while the driving current required by IGBT may reach several amperes. The primary task of IGBT driver is to act as an amplifier and amplify the current.
Secondly
The MCU output level is generally 3.3V, while the general driving voltage of IGBT is 15V. IGBT driver needs to convert 3.3V signal into 15V signal. And this 15V is not ordinary 15V. IGBT generally works in a bridge circuit. The bridge circuit will bear the bus voltage. When the circuit is not switched, the midpoint of the bridge circuit will bear half of the bus voltage; when the upper tube is turned on, the midpoint potential is the same as the bus voltage.
At this time, the job of the upper tube IGBT driver is to generate a 15V voltage signal based on the bus voltage of several hundred volts or thousands of volts. It is like the MCU provides a sapling growing on the ground. The job of the IGBT driver is not only to turn the sapling into a big tree, but also to transplant it to the mountains. Doesn't it sound amazing?
at last
MCU is on the low voltage side, and its power supply voltage is generally 5V. IGBT is on the high voltage side, and the bus voltage can reach several thousand volts. Because there will be a human-machine interface on the low voltage side, the high voltage on the high voltage side must not be allowed to flow to the low voltage side to cause harm to the human body! Sometimes, the IGBT driver needs to have a certain electrical isolation capability as a barrier between the low voltage side and the high voltage side to prevent the secondary side high voltage from causing harm to the human body operating on the primary side. If the IGBT driver does not have insulation capability, an insulation barrier must be added between the MCU and the human-machine interface.
Drivers that can perform the above functions are called compact drivers. For example, Infineon 1ED X3 compact series:
In some application scenarios, the driver needs to provide rich protection functions. First of all, the driver needs to have a pair of "eyes" (fault detection) to observe whether the "light" (load) or "switch" (IGBT) is operating normally. If the load is abnormal, the fault detection immediately sends a signal to the "brain" MCU, and the MCU sends a command to the IGBT driver, which turns off the power device to avoid machine explosion. We call the IGBT driver IC with protection function an enhanced driver. The protection functions of the IGBT driver include undervoltage shutdown, short circuit protection, overvoltage protection, overtemperature protection, Miller clamping, soft shutdown, etc.
We call this type of driver an enhanced driver chip, and representative products include Infineon 1ED34x1MC12M:
Infineon provides complete power device + driver chip solutions.
Infineon's driver chip technology has two categories: non-isolated and isolated. Non-isolated drivers use level-shift technology, which, as the name suggests, can transplant "small saplings" on flat ground to high mountains, but it does not have insulation capabilities. Among them, SOI is a special level-shift technology that makes transistors on an insulating silicon dioxide layer, eliminating the generation of leakage current, so that the driver chip has a strong ability to resist negative pressure.
Isolated drivers can not only complete level conversion, but also have the ability to electrically isolate the primary and secondary sides. Common isolation technologies on the market include optical isolation, magnetic isolation, and capacitive isolation. Infineon's isolated drivers use magnetic isolation technology, which uses two coils as signal receivers for the primary and secondary sides, respectively, with silicon dioxide as the insulating layer in the middle, also known as coreless transformer technology.
At this point, I wonder if you have discovered an interesting phenomenon. The entire power system is like a nesting doll with layers of amplification: the mA-level weak signal sent by the MCU is amplified to several amperes by the IGBT driver chip. There may be a booster circuit behind the driver chip to amplify the drive current to more than ten amperes. This current can be amplified to hundreds or even thousands of amperes through the IGBT, thereby lifting ore, raising elevators, and driving high-speed trains. IGBT drive is a crucial link in the entire system.
For those who are new to IGBT driver chips, it is inevitable that they will be dazzled by the dazzling array of IC models. In fact, it is very simple to choose the right IGBT driver chip. Infineon has an online driver IC selection tool. You only need to enter simple information such as system voltage, current, insulation level, etc., and the tool will push the right product.
Previous article:Toshiba Launches New MOSFET Gate Driver IC to Help Reduce Equipment Size
Next article:Qorvo® Launches Power Solution with Integrated Intelligent Motor Controller and High-Efficiency SiC FETs
Recommended ReadingLatest update time:2024-11-16 11:30
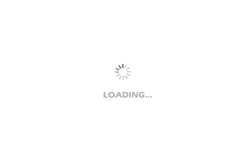
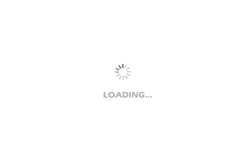
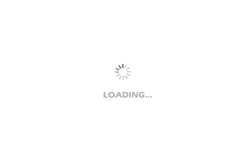
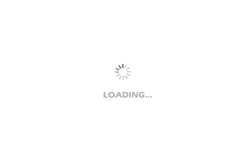
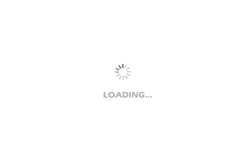
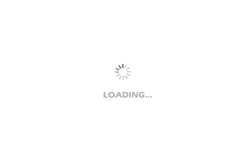
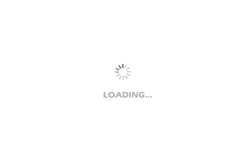
- Popular Resources
- Popular amplifiers
- MathWorks and NXP Collaborate to Launch Model-Based Design Toolbox for Battery Management Systems
- STMicroelectronics' advanced galvanically isolated gate driver STGAP3S provides flexible protection for IGBTs and SiC MOSFETs
- New diaphragm-free solid-state lithium battery technology is launched: the distance between the positive and negative electrodes is less than 0.000001 meters
- [“Source” Observe the Autumn Series] Application and testing of the next generation of semiconductor gallium oxide device photodetectors
- 采用自主设计封装,绝缘电阻显著提高!ROHM开发出更高电压xEV系统的SiC肖特基势垒二极管
- Will GaN replace SiC? PI's disruptive 1700V InnoMux2 is here to demonstrate
- From Isolation to the Third and a Half Generation: Understanding Naxinwei's Gate Driver IC in One Article
- The appeal of 48 V technology: importance, benefits and key factors in system-level applications
- Important breakthrough in recycling of used lithium-ion batteries
- Innolux's intelligent steer-by-wire solution makes cars smarter and safer
- 8051 MCU - Parity Check
- How to efficiently balance the sensitivity of tactile sensing interfaces
- What should I do if the servo motor shakes? What causes the servo motor to shake quickly?
- 【Brushless Motor】Analysis of three-phase BLDC motor and sharing of two popular development boards
- Midea Industrial Technology's subsidiaries Clou Electronics and Hekang New Energy jointly appeared at the Munich Battery Energy Storage Exhibition and Solar Energy Exhibition
- Guoxin Sichen | Application of ferroelectric memory PB85RS2MC in power battery management, with a capacity of 2M
- Analysis of common faults of frequency converter
- In a head-on competition with Qualcomm, what kind of cockpit products has Intel come up with?
- Dalian Rongke's all-vanadium liquid flow battery energy storage equipment industrialization project has entered the sprint stage before production
- Allegro MicroSystems Introduces Advanced Magnetic and Inductive Position Sensing Solutions at Electronica 2024
- Car key in the left hand, liveness detection radar in the right hand, UWB is imperative for cars!
- After a decade of rapid development, domestic CIS has entered the market
- Aegis Dagger Battery + Thor EM-i Super Hybrid, Geely New Energy has thrown out two "king bombs"
- A brief discussion on functional safety - fault, error, and failure
- In the smart car 2.0 cycle, these core industry chains are facing major opportunities!
- The United States and Japan are developing new batteries. CATL faces challenges? How should China's new energy battery industry respond?
- Murata launches high-precision 6-axis inertial sensor for automobiles
- Ford patents pre-charge alarm to help save costs and respond to emergencies
- New real-time microcontroller system from Texas Instruments enables smarter processing in automotive and industrial applications
- How to use wire connectors?
- 7.5KW motor hard start problem?
- Detailed description of high-speed circuit PCB return path
- ADI & Shijian New Infrastructure Series Episode 2 - Answer the Energy Storage Questions to Win Gifts! Let's Start~
- Have you ever encountered problems with function return classes in embedded programming?
- Is it possible to create a SQLite database on the ESP32?
- How does this product function?
- 【Fudan Micro FM33LC046N Review】+ LED and KEY
- STM32F429IGT6 core board schematic diagram
- Ink display driver with 32KB SRAM cache