In the mobile phone market, it has become almost standard to integrate high-pixel image processors into mobile phones. As the resolution of these image processors increases, the industry also increases the demand for high-brightness flash. Xenon flash bulbs have always been the main lighting choice for digital cameras, but for the mobile phone market, the space available on the circuit board for non-phone functional components is really limited, making the larger xenon lamp solution impractical. Fortunately, mobile phone manufacturers have recently made significant technological breakthroughs in high-power white light diodes. Today, manufacturers of white light LED flash diodes have introduced products with light output exceeding 70 lumens and can handle pulse currents exceeding or equivalent to 1A. However, these technological breakthroughs also bring many questions to the designer, including how much circuit board space is available? What flash-related functions need to be added? How much power can the flash driver use? How many lumens are needed to take a good photo? If the above questions can be answered, the designer will be more comfortable when choosing a flash LED driver.
Solution size
The first question facing cell phone designers is how much board space is available for the camera flash? In the field of LED flash drivers, the two most common boost technologies are switched capacitor boost (charge pump) and inductive boost. Of the two boost topologies, the switched capacitor solution is generally smaller, and most switched capacitors consist of four ceramic capacitors and two external resistors. The recommended capacitance value for these applications is 4.7μF, and the voltage rating is 10V (helps reduce DC bias losses). These capacitors are available in 0603 form factors and are available from most capacitor manufacturers. The overall solution size of a flash driver using switched capacitors is generally about 25mm2. For example, the National Semiconductor LM2758, which uses a chip-scale package, has an overall solution size of less than 15mm2. Another advantage of the switched capacitor solution is that it is extremely thin. Generally, depending on the packaging method of the flash driver, the capacitor is usually the tallest component in the entire solution.
The solution size of inductive flash driver is generally larger than that of switched capacitor driver. A typical inductive flash LED driver solution occupies about 35mm2~40mm2 of board area. Inductive driver generally requires two capacitors (input and output), with an average capacitance of 10μF and a 0805 size. Inductive boost requires a rectifier section to handle the peak inductor current and output voltage. In synchronous boost topology, the flash IC usually integrates a pass FET (typically a PFET), and this integration usually makes the IC package size larger than asynchronous solution. In asynchronous topology, the pass section is implemented in the form of Schottky diode. Compared with the boost using switched capacitor, the extra space occupied by inductive boost comes mainly from the inductor itself. For applications with flash current close to 1A, the required inductor is generally 2.2μH~4.7μF, and the saturation current must be greater than 1.5A. However, these inductors are typically no smaller than 3mm x 3mm and are usually the tallest components in the entire solution, with 1.2mm being a common height.
Features
Once the topology of the flash driver is determined, the next issue to consider is the features required for the design. The first feature to consider is the type of control interface. Basic flash drivers generally have two control pins to implement 3-4 different operating modes (such as off, reminder light, flashlight and flashlight). If the designer does not need to adjust the brightness dynamically, these simple control components are sufficient. On the other hand, if the system requires a higher level of control, most flash circuits include some type of serial control interface. One of the most common serial interfaces is the Inter-Integrated Circuit interface (I2C). I2C or I2C compatible interfaces not only control basic on/off functions, but also allow users to dynamically set the brightness of the flashlight and flashlight. In addition, if the design includes features such as flash fuse timing, inductor current limiting or overvoltage protection level, these can also be configured through the I2C interface. In addition, these serial interfaces become more important when the general-purpose input/output (GPIO) lines of the microcontroller/microprocessor are not sufficient.
Many LED drivers, including National Semiconductor's LM3553, offer additional control pins to further assist designers in solving system-level problems. Today's typical image processors have an external strobe (strobe/flash) pin to indicate that the system is taking a picture. This strobe signal can be directly connected to multiple LED strobe drivers through the strobe enable pin. This direct connection between the image processor and the LED driver eliminates all delays that occur between the two components, which are generally caused by controller or software limitations.
On a system level, today's cell phone systems need to manage the amount of current drawn from the battery during talk/data transmission. The current drawn by the Tx/Rx power amplifiers plus the current drawn by the flash driver during talk/data transmission can often exceed the maximum current the battery can provide. Most cell phone designs can allow the load battery voltage to drop to 3.2V without entering a reset state (VBATT-LOADED = VBATT_UNLOADED (IBATT * RBATT_ESR)). To prevent a reset caused by the battery's ESR voltage drop, some newer flash LED drivers have added a transmit pin (Tx) that can help reduce the current drawn by the LED driver during talk/data transmission. By adding the Tx pin, the flash driver can force the diode current to remain low for a very short time (less than 100μs) to prevent the phone from accidentally entering a reset state during a call.
efficiency
Efficiency is an old topic in mobile phone design. The higher the efficiency of the system, the longer the talk time available to the user. Inductive boost technology enables the driver to achieve the highest efficiency over a wide range of input voltage and output current. In contrast, switched capacitor components are limited to a few fixed quantization gains (2x, 1.5x, 1x channel modes), so that the average converter efficiency that can be achieved is lower than that of inductive boost under the same input range. When evaluating an LED driver, the meaning of efficiency is a little different.
Converter efficiency or LED driver efficiency?
When it comes to flash LED drivers, certain efficiency losses must be considered before calculating the true efficiency of the solution. In order to obtain a regulated flash or flashlight/video camera LED current, the boost converter must use a current sink/source or a tightly controlled reference voltage, together with a resistor to establish the load current. However, both of these different methods have their own advantages and disadvantages, and it must be noted that the power losses caused by these two methods are not included in the efficiency calculation of the boost converter. However, the efficiency of the overall solution or LED does take these power losses into account.
Equation 1 and Equation 2
The first thing to note is that even two different converters can have absolutely the same converter efficiency, and their LED driving efficiency will only differ by 5% to 10%. In other words, if the efficiency of two converters is equal, as long as one has lower losses caused by the current regulation element, it is the more efficient converter.
LED driving efficiency or luminous efficiency?
However, LED driver efficiency alone does not tell the full story of overall performance. For example, consider two different flash LED drivers and two different flash LEDs. The first driver has an 85% converter efficiency and an LED voltage of 4V at 1A, while the other has an 80% converter efficiency and an LED voltage (also at 1A) of 3V. At a given current, both LEDs produce the same amount of light output and have a 350mV feedback voltage. Using Equation 1 and citing a worst-case input voltage or 3.2V, the first driver draws 1.6A from the battery, while the second driver only draws 1.3A from the battery. Despite the higher efficiency of the first flash driver, it would need to draw 300mA more to produce the same amount of light output as the second flash driver. This example highlights the impact of LED efficiency. The LED in Example 2 is 33% more efficient at producing light than the LED in Example 1.
When the flash LED driver is operating in continuous video shooting or flashlight lighting mode, the operation time may be relatively long, so the efficiency of the converter becomes very important. However, under normal flash conditions, the operation time is only a moment, so the importance of converter efficiency is reduced. On the contrary, the efficiency that is more concerned here is whether it can give the flash driver more output power at a given input power to produce a brighter flash. High-efficiency flash LEDs combined with efficient flash drivers can minimize the flash current drawn from the battery, so that mobile phone designers can more flexibly manage power for other parts of the system.
Optimization of light output
Optimizing the light output of an LED flash driver involves two main factors (three if you include cost): the light level required by the phone's image processor, and how much power is available for illumination? For a given input power budget, there are three ways to improve the brightness of the flash to help designers achieve the desired lighting requirements. These are LED selection, LED current drive, and LED configuration, which all play a vital role in optimizing the flash LED driver.
Selecting LEDs
As mentioned above, the first optimization element is to select an LED with high luminous efficacy. An LED with higher luminous efficacy can emit more luminous flux (lumens) at a given power. At a given current, the luminous efficacy is equal to the LED luminous flux divided by the product of the LED drive current and the forward voltage. Luminous flux curves can be found in the specification sheets provided by most LED manufacturers1.
When selecting LEDs, mobile phone designers should not only consider the optical performance of the LED, but also must consider the size and cost of the LED, as well as the complexity of the lens that maximizes the LED illumination.
Increase drive current
After selecting the LED, the second way to increase light output is to increase the actual drive current. Using the luminous flux curve in Figure 2, it can be found that when the diode current is increased from 500mA to 1A, the light output will increase by about 30 lumens. However, increasing the diode current will also bring some adverse effects. If the diode current is doubled, the increased diode current and forward voltage will cause the LED power to increase by more than double, and this LED power increase will increase the system's input power requirements. Figure 3 shows the effect of forward current on LED forward voltage.
In order to enhance the optimization of the LED driver current system, an estimated input current must be established first. Once the minimum input voltage and maximum input current are calculated, data can be found from the LED forward voltage to LED current curve (Figure 3) to further calculate the maximum allowable drive current of the flash LED driver.
Formula 3
POUT CONV IIN VIN = ILED VLED + VFEEDBACK
example
VIN = 3.2V, IIN = 1.5A,CONV = 85% VFEEDBACK = 350mV
Input power = 4.8W, Maximum output power = 4.08W
From the curve in the figure, we can see that the output power generated by the LED at 3.6V and 1A current is equal to 3.95W (PLED + PFEEDBACK), which is very close to the maximum allowable value.
Configuration
If you already have a high luminous flux and high efficacy LED, but the required luminance is still not achieved after optimizing the flash current, then you can get closer to the goal by adding a second or third LED to the design. Looking again at the luminous flux vs. LED current curve, you can see that the curve is not completely linear. The luminous flux produced by two LEDs operating at only half the flash current will produce more than one LED operating at the full flash current. In addition, the total power of two LEDs operating at half the flash current is lower than that of one LED operating at the full flash current. This can provide a greater total output current for the two LEDs within the given input power budget. The two LEDs can be driven in parallel or series configurations.
example
The following 3 configurations all have a 350Mv VFB and can also produce 73 lumens.
1 LED @ 1A: POUT = (3.6 1A) + (1A 350mV) = 4.08W
2 LEDs @ 350mA (parallel): POUT = (3.3V 2 350mA) + (350mA 350mV2) = 2.56W
2 LEDs @ 350mA (serial): POUT = (3.3V 2 350mA) + (350mA 350mV) = 2.43W
The VFBs of the following three configurations are all 350Mv, and their output powers are very close.
1 LED@1A:POUT = (3.6 1A) + (1A 350mV) = 4.08W 73 lumens
2 LEDs @ 525mA (parallel): POUT = (3.425V 2 525mA) + (525mA 350mV2) = 3.96W 90 lumens
2 LEDs @ 550mA (serial): POUT = (3.45V 2 550mA) + (550mA 350mV) = 3.99W 94 lumens
When driving two LEDs, the series configuration offers many advantages over the parallel configuration. Driving the two LEDs in series ensures that the current flowing through both flash LEDs is the same. In the parallel configuration, the typical matching of the two current sources to the LED current is 1% to 3%. However, most flash drivers have only one current sink. If the two LEDs are connected to a single current source/current sink, the mismatch in the LED forward voltage will cause a serious LED current mismatch. To solve this problem, a series current-locking resistor is added. However, adding a series resistor to the LED will reduce both the output current budget and the amount of available flash current, resulting in a weaker flash. In addition, if the LED current is the same in the series and parallel configurations, driving two LEDs in series can also reduce the output power dissipation caused by the current control element (resistor or current sink) by half (PFB-Series = ILED VFB and PFB-Parallel = ILED VFB2).
Summarize
Adding a white LED camera flash to a cell phone system involves many design choices, and the topology that will be chosen is indirectly determined when determining the board space that the flash can occupy. In addition, features such as transmit and flash enable pins allow other subsystems to help handle some of the current management and flash timing, thereby reducing the workload on the battery and microcontroller/processor. Furthermore, optically efficient LEDs combined with efficient boost converters can help increase the illumination of the flash system. If a single LED is not enough to provide sufficient illumination in a dim environment, a second LED can be added to the design to solve the problem of insufficient brightness. When selecting an LED flash driver, the above issues should be considered early in the design. As long as these issues are resolved early, all worries can be swept away.
Previous article:LLC LED Driver Simplifies Design
Next article:Using high voltage LEDs to improve bulb efficiency
Recommended ReadingLatest update time:2024-11-16 22:56
How to Reduce Output Ripple in LED Driver Design
Usually, aluminum electrolytic capacitors are used for output capacitors to achieve large capacity. However, electrolytic capacitors are not very effective in suppressing high-frequency noise, and their ESR is relatively large, so a ceramic capacitor is connected in parallel next to it to make up for the shortcoming
[Power Management]
What is an H-bridge? Introduction to H-bridge motor drive circuit
What is an H-bridge
? The circuit is named after the letter H. It usually contains four independently controlled switching components. For example, the following figure shows four MOSFET switching components Q1, Q2, Q3, and Q4.
They are usually used to drive loads with large currents, such as motors.
[Embedded]
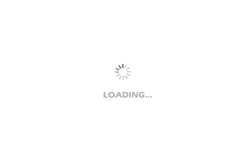
PI's flicker-free dimming LED driver IC solution
The advantages of LED such as high brightness, low power consumption, miniaturization and long life have promoted the rapid development of this technology, but LED lighting technology still faces challenges such as high cost, excessive heat sink, low luminous efficiency and dimming. During the design process, engin
[Power Management]
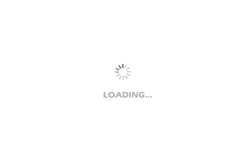
Tips for selecting LED driver power supply
According to the characteristics of power grid, LED characteristics and related LED products, the following points should be considered when selecting LED driver power supply : General Principles a. According to the characteristics of LED current and voltage, it is ideal to use constant current drive. It can avoid
[Power Management]
Providing efficient current drive for high brightness LEDs
High Brightness LED Development Background
In recent years, high brightness LED (HB LED) has become increasingly popular as a light source in various lighting systems. This is because high brightness LED has a high degree of reliability and a service life of tens or even tens of thousands of hours, which is
[Power Management]
Working principle of servo drive
With the emergence of fully digital AC servo systems, AC servo motors are increasingly used in digital control systems. In order to adapt to the development trend of digital control, most motion control systems use fully digital AC servo motors as actuator motors. The control method is implemented using pulse trains
[Embedded]
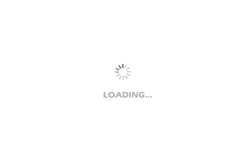
Research on dimming technology of switchable LED driver
As the number of LED lighting devices grows, the number of integrated circuit devices that provide controlled power to LEDs continues to grow. Saving energy is an important global issue today, and power-hungry linear current sources no longer meet this requirement, so switching LED drivers have become the industry sta
[Power Management]
C51 program for microcontroller driving 74HC595
//This subroutine is for 74HC595 to send characters. This program sends the lowest bit first!
//The clock pin of chip 74HC595 is pin 11
//The data pin of chip 74HC595 is pin 14
//The latch pin of chip 74HC595 is pin 12
//When multiple 74HC595s are connected in series, the signal will be latched only
[Microcontroller]
- Popular Resources
- Popular amplifiers
-
Siemens Motion Control Technology and Engineering Applications (Tongxue, edited by Wu Xiaojun)
-
Modern Product Design Guide
-
Modern arc welding power supply and its control
-
Small AC Servo Motor Control Circuit Design (by Masaru Ishijima; translated by Xue Liang and Zhu Jianjun, by Masaru Ishijima, Xue Liang, and Zhu Jianjun)
Recommended Content
Latest Power Management Articles
- MathWorks and NXP Collaborate to Launch Model-Based Design Toolbox for Battery Management Systems
- STMicroelectronics' advanced galvanically isolated gate driver STGAP3S provides flexible protection for IGBTs and SiC MOSFETs
- New diaphragm-free solid-state lithium battery technology is launched: the distance between the positive and negative electrodes is less than 0.000001 meters
- [“Source” Observe the Autumn Series] Application and testing of the next generation of semiconductor gallium oxide device photodetectors
- 采用自主设计封装,绝缘电阻显著提高!ROHM开发出更高电压xEV系统的SiC肖特基势垒二极管
- Will GaN replace SiC? PI's disruptive 1700V InnoMux2 is here to demonstrate
- From Isolation to the Third and a Half Generation: Understanding Naxinwei's Gate Driver IC in One Article
- The appeal of 48 V technology: importance, benefits and key factors in system-level applications
- Important breakthrough in recycling of used lithium-ion batteries
MoreSelected Circuit Diagrams
MorePopular Articles
- Innolux's intelligent steer-by-wire solution makes cars smarter and safer
- 8051 MCU - Parity Check
- How to efficiently balance the sensitivity of tactile sensing interfaces
- What should I do if the servo motor shakes? What causes the servo motor to shake quickly?
- 【Brushless Motor】Analysis of three-phase BLDC motor and sharing of two popular development boards
- Midea Industrial Technology's subsidiaries Clou Electronics and Hekang New Energy jointly appeared at the Munich Battery Energy Storage Exhibition and Solar Energy Exhibition
- Guoxin Sichen | Application of ferroelectric memory PB85RS2MC in power battery management, with a capacity of 2M
- Analysis of common faults of frequency converter
- In a head-on competition with Qualcomm, what kind of cockpit products has Intel come up with?
- Dalian Rongke's all-vanadium liquid flow battery energy storage equipment industrialization project has entered the sprint stage before production
MoreDaily News
- Allegro MicroSystems Introduces Advanced Magnetic and Inductive Position Sensing Solutions at Electronica 2024
- Car key in the left hand, liveness detection radar in the right hand, UWB is imperative for cars!
- After a decade of rapid development, domestic CIS has entered the market
- Aegis Dagger Battery + Thor EM-i Super Hybrid, Geely New Energy has thrown out two "king bombs"
- A brief discussion on functional safety - fault, error, and failure
- In the smart car 2.0 cycle, these core industry chains are facing major opportunities!
- The United States and Japan are developing new batteries. CATL faces challenges? How should China's new energy battery industry respond?
- Murata launches high-precision 6-axis inertial sensor for automobiles
- Ford patents pre-charge alarm to help save costs and respond to emergencies
- New real-time microcontroller system from Texas Instruments enables smarter processing in automotive and industrial applications
Guess you like
- Who is the source manufacturer of the 3651 orthogonal convex tooth sensor? Is there anyone who can be its agent?
- Which is faster for switching, MOS or Darlington?
- How to understand MOS tube parameters
- Various library files for TI DSP28335
- When BLE meets MEMS——BLE communication under MATLAB software
- What do you think is a valuable life?
- C64x+ CACHE consistency maintenance operations
- [Fudan Micro FM33LG0 Series Development Board Review] Unboxing + Great Lighting + HELLO WORLD!
- IAR FOR MSP430 Tutorial
- Using IQmath with TMS320F28x7x