LED driver power is a voltage converter that converts power supply into a specific voltage and current to drive LEDs to emit light. Usually, the input of LED driver power includes high-voltage power frequency AC (i.e., mains), low-voltage DC, high-voltage DC, low-voltage high-frequency AC (such as the output of electronic transformers), etc. The output of LED driver power is mostly a constant current source that can change voltage as the forward voltage drop of the LED changes. The following is some knowledge about LED driver power for beginners.
1. What is LED driver power supply?
LED driver power is a voltage converter that converts power supply into a specific voltage and current to drive the LED to emit light. Under normal circumstances: the input of LED driver power includes high-voltage power frequency AC (i.e., mains), low-voltage DC, high-voltage DC, low-voltage high-frequency AC (such as the output of an electronic transformer), etc. The output of LED driver power is mostly a constant current source that can change the voltage as the forward voltage drop of the LED changes. The core components of LED power supply include switch controller, inductor, switch components (MOSfet), feedback resistor, input filter device, output filter device, etc. According to the requirements of different occasions, there are also input overvoltage protection circuit, input undervoltage protection circuit, LED open circuit protection, overcurrent protection and other circuits.
2. Characteristics of LED driver power supply
(1) High reliability
Especially the driving power supply of LED street lamps, which is installed at high altitude, is inconvenient to maintain and the cost of maintenance is also high.
(2) High efficiency
LED is an energy-saving product, and the efficiency of the driving power supply must be high. It is very important to heat the junction of the power supply installed in the lamp. The higher the efficiency of the power supply, the less power it consumes, and the less heat it generates in the lamp, which reduces the temperature rise of the lamp. This is beneficial to delaying the light decay of LED.
(3) High power factor
The power factor is the load requirement of the power grid. Generally, there is no mandatory index for electrical appliances below 70 watts. Although a low power factor of a single low-power electrical appliance has little impact on the power grid, the large amount of lighting used at night and the concentration of similar loads will cause serious pollution to the power grid. For 30-40 watt LED driver power supplies, it is said that in the near future, there may be certain index requirements for power factor.
(4) Drive mode
There are two common methods now: one is to use a constant voltage source to supply multiple constant current sources, and each constant current source supplies power to each LED separately. This method has flexible combination, and the failure of one LED does not affect the operation of other LEDs, but the cost will be slightly higher. The other is direct constant current power supply, which is the driving method adopted by "Zhongke Huibao", and the LEDs are connected in series or in parallel. Its advantage is that the cost is lower, but the flexibility is poor, and the problem of a certain LED failure not affecting the operation of other LEDs must be solved. These two forms coexisted for a period of time. The multi-channel constant current output power supply method will be better in terms of cost and performance. Perhaps it will be the mainstream direction in the future.
(5) Surge protection
LEDs are relatively poor at resisting surges, especially reverse voltage. It is also important to strengthen protection in this regard. Some LED lights are installed outdoors, such as LED street lights. Due to the start-up of the grid load and the induction of lightning strikes, various surges will invade from the grid system, and some surges will cause damage to the LEDs. Therefore, it is analyzed that the driver power supply of "Zhongke Huibao" should have certain deficiencies in surge protection. As for the frequent replacement of power supplies and lamps, the LED driver power supply must have the ability to suppress the intrusion of surges and protect the LEDs from damage.
(6) Protection function
In addition to the conventional protection functions of the power supply, it is best to add LED temperature negative feedback in the constant current output to prevent the LED temperature from being too high; it must comply with safety regulations and electromagnetic compatibility requirements.
3. Classification by driving mode
(1) Constant current type
The output current of the constant current drive circuit is constant, but the output DC voltage varies within a certain range with the size of the load resistance. The smaller the load resistance, the lower the output voltage, and the larger the load resistance, the higher the output voltage.
The constant current circuit is not afraid of load short circuit, but it is strictly forbidden to open the load completely;
Constant current drive circuit is ideal for driving LED, but the price is relatively high.
Attention should be paid to the maximum current and voltage used, as this limits the number of LEDs that can be used.
(2) Voltage stabilization
When the parameters in the voltage stabilization circuit are determined, the output voltage is fixed, but the output current changes with the increase or decrease of the load;
The voltage stabilizing circuit is not afraid of open-circuit load, but it is strictly forbidden to completely short-circuit the load;
When driving LEDs with a voltage-stabilizing drive circuit, each string needs to be added with a suitable resistor to make each string of LEDs display an even brightness.
Brightness is affected by changes in rectified voltage.
4. Advantages and disadvantages of overall constant current and channel-by-channel constant current working modes
Compared with the overall constant current, although the channel-by-channel constant current has more disadvantages and higher cost, it can truly protect the LED and extend the life of the LED, so the channel-by-channel constant current is the future trend.
5. Insufficient LED power supply
The reasons why LED driver power supply is currently insufficient:
The technical staff of the company producing LED lighting and related products do not have enough understanding of switching power supplies. The power supplies they make can work normally, but some key evaluations and electromagnetic compatibility considerations are not enough, so there are still certain hidden dangers;
Most LED power supply manufacturers have transformed from ordinary switching power supplies to LED power supplies, and their understanding of the characteristics and uses of LEDs is still insufficient;
There are almost no standards for LEDs at present, most of which refer to the standards for switching power supplies and electronic rectifiers;
At present, most LED power supplies are not standardized, so the quantity is mostly small. The purchase quantity is small, the price is high, and the component suppliers are not very cooperative;
Stability of LED power supply: wide voltage input, high and low temperature operation, over-temperature and over-voltage protection and other issues have not been solved one by one;
First of all, the overall life of the drive circuit, especially the life of key components such as capacitors at high temperatures, which directly affects the life of the power supply;
LED drivers should challenge higher conversion efficiency, especially when driving high-power LEDs, because all power that is not output as light is dissipated as heat. Too low power conversion efficiency affects the energy-saving effect of LEDs.
At present, in applications with lower power (1-5W), the cost of constant current drive power supply accounts for nearly 1/3, which is close to the cost of light source, affecting market promotion to a certain extent.
Two major categories of LED driver power
LED driver power is a voltage converter that converts power supply into a specific voltage and current to drive LED to emit light. Usually, the input of LED driver power includes high-voltage power frequency AC (i.e. mains), low-voltage DC, high-voltage DC, low-voltage high-frequency AC (such as the output of electronic transformer), etc. The output of LED driver power is mostly a constant current source that can change voltage as the forward voltage drop value of the LED changes.
Since the performance and conversion efficiency of LED power supplies of different specifications are different, choosing a suitable and efficient LED power supply can truly show the high-efficiency characteristics of LED light sources. Because low-efficiency LED power supplies themselves consume a lot of electricity, the energy-saving characteristics of LEDs cannot be highlighted in the process of powering LEDs. In short, LED power supplies play an important role in the stability, energy saving, and life of LEDs.
What are the categories of LED power supplies?
1. LED power supplies can be divided into two categories according to the driving method:
A. Voltage stabilization type:
1. After the voltage stabilization circuit determines the various parameters, the output is a fixed voltage, but the output current changes with the increase or decrease of the load
2. Although the voltage stabilizing circuit is not afraid of open-circuit load, it is strictly forbidden to completely short-circuit the load.
3. The voltage change after rectification will affect the brightness of the LED
4. To make each string of LEDs driven by a voltage stabilizing circuit display uniform brightness, it is necessary to add appropriate resistance.
B. Constant current type:
1. Constant current drive circuit is ideal for driving LED, but the disadvantage is that it is more expensive.
2. Although the constant current circuit is not afraid of load short circuit, it is strictly forbidden to completely open the load
3. The output current of the constant current drive circuit is constant, but the output DC voltage varies within a certain range with the size of the load resistance.
4. Limit the number of LEDs used because they have maximum current and voltage tolerances.
2. LED power supplies can be divided into six categories according to circuit structure:
1. Conventional transformer voltage reduction:
The advantage of this type of power supply is its small size, but its disadvantages are its heavy weight and low power efficiency, generally between 45% and 60%. Because of its low reliability, it is rarely used.
2. Capacitor voltage reduction:
This type of LED power supply is easily affected by grid voltage fluctuations, has low power efficiency, and is not suitable for use when the LED is flashing. This is because the circuit uses capacitors to reduce voltage. When used in flashing mode, due to the effects of charging and discharging, the instantaneous current passing through the LED is extremely large, which can easily damage the chip.
3. Electronic transformer voltage reduction:
The disadvantages of this power supply structure are low conversion efficiency, narrow voltage range (usually 180~240V), and large ripple interference.
4. Resistor voltage reduction:
This power supply method has low power efficiency and low system reliability. Because the circuit uses a resistor to reduce voltage, it is greatly disturbed by the change of grid voltage, and it is not easy to make a voltage-stabilized power supply. In addition, the voltage-reducing resistor itself consumes a large part of the energy.
5. RCC step-down switching power supply:
The advantages of this type of LED power supply are wide voltage regulation range and high power efficiency, generally 70%~80%, and wide application. The main disadvantages are that the switching frequency is difficult to control, the load voltage ripple coefficient is large, and the load adaptability is poor in abnormal conditions.
6. PWM controlled switching power supply:
At present, the LED power supply designed with PWM control mode is more ideal, because the output voltage or current of this switching power supply is very stable. The power conversion efficiency is extremely high, generally up to 80%~90%, and the output voltage and current are very stable. This type of LED power supply is mainly composed of four parts: input rectification and filtering part, output rectification and filtering part, PWM voltage regulation control part, and switch energy conversion part. Moreover, this circuit has perfect protection measures and is a high-reliability power supply.
Nine performance characteristics of LED driver power supply
According to the power usage rules of the power grid and the characteristics of the LED driver power supply, the following nine performance characteristics should be considered when selecting and designing the LED driver power supply:
1. High reliability: Especially for the driving power supply of LED street lamps, which is installed at high altitude, it is inconvenient to maintain and the maintenance cost is also high.
2. High-efficiency LED is an energy-saving product, and the efficiency of the driving power supply must be high. This is especially important for the structure where the power supply is installed in the lamp. Because the luminous efficiency of LED decreases as the temperature of the LED increases, the heat dissipation of the LED is very important. The high efficiency of the power supply means that its power consumption is small, and the heat generated in the lamp is small, which also reduces the temperature rise of the lamp. This is beneficial to delaying the light decay of the LED.
3. High power factor The power factor is the load requirement of the power grid. Generally, there is no mandatory index for electrical appliances below 70 watts. Although a low power factor of a single electrical appliance with low power has little impact on the power grid, when everyone turns on lights at night, the same load is too concentrated, which will cause serious pollution to the power grid. For 30-40 watt LED driver power supplies, it is said that in the near future, there may be certain index requirements for power factor.
4. There are two common driving modes: one is that a constant voltage source supplies multiple constant current sources, and each constant current source supplies power to each LED separately. This mode has flexible combination, and the failure of one LED does not affect the operation of other LEDs, but the cost will be slightly higher. The other is direct constant current power supply, and the LEDs are operated in series or parallel. Its advantage is that the cost is lower, but the flexibility is poor, and the problem of a certain LED failure not affecting the operation of other LEDs must be solved. These two forms coexist for a period of time. The multi-channel constant current output power supply mode will be better in terms of cost and performance. Perhaps it will be the mainstream direction in the future.
5. Surge protection LEDs have poor surge resistance, especially reverse voltage resistance. It is also important to strengthen this protection. Some LED lights are installed outdoors, such as LED street lights. Due to the start-up of the grid load and the induction of lightning strikes, various surges will invade from the grid system, and some surges will cause damage to the LEDs. Therefore, the LED driver power supply must have the ability to suppress the intrusion of surges and protect the LEDs from damage.
6. Protection function In addition to the conventional protection function of the power supply, it is best to add LED temperature negative feedback in the constant current output to prevent the LED temperature from being too high.
7. Protection: For external installation, the power supply structure should be waterproof and moisture-proof, and the outer shell should be sun-resistant.
8. The life of the driver should match the life of the LED.
9. It must comply with safety regulations and electromagnetic compatibility requirements.
As LEDs are increasingly used, the performance of LED driver power supplies will become more and more suitable for LED requirements.
Seven principles for determining the quality of LED driver power supply
1. Abandon more than 4 outputs and develop single or dual outputs; abandon large current and ultra-large current and develop small current.
The more output paths there are, the more complicated it is. It is very costly to solve the current interference between different output paths. If it is not solved, the failure rate will be high. In addition, the more output paths there are, the greater the total output current will be. Current is the main cause of heat generation. Voltage itself does not directly cause heat generation. Simply put, the heat generation is proportional to the square of the current. That is to say, if the current increases to 2 times, the heat generation will increase to 4 times. If the current increases to 3 times, the heat generation will increase to 9 times. In summary, the failure rate of LED lamp power supply with single or dual output will be much lower.
2. Intelligent control is one of the advantages of LED lamps, and power supply is the key to intelligent control.
Intelligent control is most mature and effective in the application of LED street lights and LED tunnel lights. Intelligent control can realize stepless control of lamp power in different time periods according to the density of road traffic, which not only meets the application requirements but also achieves huge energy-saving effects, and can save a lot of money for highway management units. The application of tunnel lighting can not only save energy, but also automatically adjust the brightness of tunnel entrances and exits according to the brightness outside the tunnel, providing drivers with a visual transition stage to ensure driving safety.
3. Give up high power and ultra-high power and choose small and medium power sources with higher stability.
Because the greater the power, the greater the heat generated, the more compact the components inside, which is not conducive to heat dissipation, and temperature is the culprit of power supply failure. Moreover, small power supply is relatively mature, and has advantages in stability and cost. In fact, many high-power power supply solutions have not been verified by time and practice. They are hastily launched projects and experimental products, so failures are endless. In contrast, small and medium-power power supplies are much more mature in technical solutions because they were developed earlier.
4. Heat dissipation and protection are the main external factors of power supply failure.
Not only the power supply itself will generate heat, but also the lamp will generate heat. How to properly dissipate these two heat sources is a problem that lamp design engineers must consider. It is necessary to prevent excessive concentration of heat, forming a heat island effect, and affecting the life of the power supply. Using a separate power supply solution is a good choice.
5. Feasibility of maintenance.
Power failure cannot be completely avoided, so Chengdu Chaoyue Optoelectronics has proposed the principle of simple maintenance. Only when the replacement of the power supply is as easy as the replacement of the light source of conventional lighting, can users be happy. Even if the power supply is broken, the mood will not be too bad, and the mood of users determines the fate of LED lamp manufacturers.
6. Protective performance.
Protection is also very important. The penetration of water may cause a short circuit in the power supply. The dust on the outer casing will affect the heat dissipation of the power supply. Exposure to the sun can easily cause high temperature and aging of wires and other components. From actual experience, the failure rate of rotary wiring plugs is relatively high, and most of the failures are caused by water leakage.
7. Modular design.
Modular design has become the trend today, and we must find a way to integrate the module power supply. If the power supply can solve the maintenance problem by plugging and unplugging, it will definitely be welcomed by users. At the same time, it is necessary to establish interface standardization so that LED light power supplies from different manufacturers can be universal.
Summary: It is best to use a split design for LED lamp power supply, and pay attention to the reliability and life of the power supply, even if it increases the cost a little. Only by designing products from the perspective of customers can the company achieve long-term development.
Five principles for simplifying LED design
Chip heating
This is mainly for high-voltage driver chips with built-in power modulators. If the current consumed by the chip is 2mA, and a voltage of 300V is applied to the chip, the power consumption of the chip is 0.6W, which will of course cause the chip to heat up. The maximum current of the driver chip comes from the consumption of the driving power MOS tube. The simple calculation formula is I=cvf (considering the resistance effect of charging, the actual I=2cvf, where c is the cgs capacitance of the power MOS tube, and v is the gate voltage when the power tube is turned on. Therefore, in order to reduce the power consumption of the chip, you must find a way to reduce c, v and f. If c, v and f cannot be changed, then please find a way to distribute the power consumption of the chip to devices outside the chip, and be careful not to introduce additional power consumption. To put it simply, just consider better heat dissipation.
Power tube heating
Regarding this issue, I have also seen someone posting on the forum. The power consumption of the power tube is divided into two parts, switching loss and conduction loss. It should be noted that in most occasions, especially LED mains drive applications, the switching damage is much greater than the conduction loss. The switching loss is related to the cgd and cgs of the power tube, as well as the driving ability and operating frequency of the chip. Therefore, the heating of the power tube can be solved from the following aspects: A. The MOS power tube cannot be selected based on the on-resistance alone, because the smaller the internal resistance, the larger the cgs and cgd capacitance. For example, the cgs of 1N60 is about 250pF, the cgs of 2N60 is about 350pF, and the cgs of 5N60 is about 1200pF. The difference is too big. When choosing a power tube, it is enough. B. The rest is the frequency and chip driving ability. Here we only talk about the influence of frequency. The frequency is also proportional to the conduction loss, so when the power tube is heated, the first thing to think about is whether the frequency is a bit high. Find a way to reduce the frequency! However, please note that when the frequency is reduced, in order to obtain the same load capacity, the peak current must increase or the inductance must also increase, which may cause the inductor to enter the saturation region. If the inductor saturation current is large enough, you can consider changing CCM (continuous current mode) to DCM (discontinuous current mode), which requires adding a load capacitor.
Operating frequency reduction
This is also a common phenomenon for users during the debugging process. Frequency reduction is mainly caused by two aspects. The ratio of input voltage to load voltage is small and the system interference is large. For the former, be careful not to set the load voltage too high, although the efficiency will be higher if the load voltage is high. For the latter, you can try the following aspects: a. Set the minimum current to a smaller value; b. Make the wiring cleaner, especially the key path of sense; c. Select a smaller inductor or choose an inductor with a closed magnetic circuit; d. Add RC low-pass filtering. This has a bad effect. The consistency of C is not good and the deviation is a bit large, but it should be enough for lighting. In any case, frequency reduction has no advantages, only disadvantages, so it must be solved.
Inductor or transformer selection
Finally, we are talking about the key points. I haven't gotten started yet, so I can only talk about the impact of saturation. Many users have reported that for the same drive circuit, there is no problem with the inductor produced by a, but the current of the inductor produced by b becomes smaller. In this case, you need to look at the inductor current waveform. Some engineers did not notice this phenomenon and directly adjusted the sense resistor or the operating frequency to reach the required current. This may seriously affect the service life of the LED. Therefore, before designing, reasonable calculations are necessary. If the theoretically calculated parameters are a bit different from the debugging parameters, consider whether to reduce the frequency and whether the transformer is saturated. When the transformer is saturated, L will become smaller, resulting in a sharp increase in the peak current increment caused by the transmission delay, and the peak current of the LED will also increase. Under the premise that the average current remains unchanged, you can only watch the light decay.
LED current size
Everyone knows that if the LEDripple is too large, the LED life will be affected, but no expert has ever said how big the impact is. I asked the LED factory about this data before, and they said that 30% or less is acceptable, but it has not been verified later. It is recommended to control it as small as possible. If the heat dissipation is not well solved, the LED must be used at a reduced rating. I also hope that an expert can give a specific indicator, otherwise it will affect the promotion of LED.
Common Problems of LED Driver Power Supply
In order to save energy and electricity, LED has been widely promoted, but LED needs a power supply, the quality of which will directly affect the life of the LED, so how to make a good LED driver power supply is the top priority of LED power supply designers. This article analyzes some problems of LED driver power supply, hoping to provide some help to engineers.
1. The driving circuit directly affects the life of LED
The LED drivers we are talking about include digital drivers and analog drivers. Digital drivers refer to digital circuit drivers, including digital dimming control, RGB full-color changes, etc. Analog drivers refer to analog circuit drivers, including AC constant current switching power supplies and DC constant current control circuits. The driving circuit is composed of electronic components, including semiconductor components, resistors, capacitors, inductors, etc. These components have a service life. The failure of any one device will cause the failure of the entire circuit or some functions to fail. The service life of LED is 50,000-100,000 hours. If it is continuously lit at 50,000 hours, it has a service life of nearly 6 years. It is difficult for a switching power supply to reach 6 years. The warranty period of switching power supplies sold on the market is usually 2-3 years. The power supply with a 6-year warranty is military-grade, and the price is 4-6 times that of ordinary power supplies. It is difficult for ordinary lighting manufacturers to afford it. Therefore, most of the faults of LED lamps are driver circuit faults.
2. Heat dissipation problem
LED is a cold light source, and the operating junction temperature cannot exceed the limit. A certain margin must be left when designing. The design of the entire lamp should consider many aspects such as beautiful appearance, convenient installation, light distribution, heat dissipation, etc., and a balance should be sought among many factors, so that the overall lamp is the best. The development time of LED lamps is not long, and there is not much experience to learn. Many designs are constantly being improved. Some LED lamp manufacturers use power supplies that are outsourced or purchased. The lamp designers do not know much about the power supply, so they give the LED a larger heat dissipation space and the power supply a smaller heat dissipation space. Usually, after designing the lamp, they will find a suitable power supply to match it, which brings certain difficulties to the matching of the power supply. It is often encountered that the internal space of the lamp is small or the internal temperature is high, and the cost control is low, so it is impossible to match the suitable power supply. Some LED lamp factories have the ability to develop power supplies. They can evaluate the early stage of designing the lamps and design the power supply at the same time, so as to solve the above problems. In the design, it is necessary to comprehensively consider the heat dissipation of the LED and the heat dissipation of the power supply, and comprehensively control the temperature rise of the lamp, so as to design a better lamp.
3. Difficulties in power supply description
a. Power description. Although LED has high light efficiency, there is still 80-85% heat loss, resulting in a 20-30 degree temperature rise inside the lamp. If the room temperature is 25 degrees, the temperature inside the lamp will be 45-55 degrees. The power supply works in a high temperature environment for a long time. To ensure the life span, the power margin must be increased, usually 1.5-2 times the margin.
b. Component selection. When the internal temperature of the lamp is 45-55 degrees, the internal temperature of the power supply will rise by about 20 degrees, and the temperature near the component must reach 65-75 degrees. Some components will drift in parameters under high temperature conditions, and some will have a shortened lifespan, so the equipment should be selected to be able to be used for a long time at higher temperatures, and special attention should be paid to electrolytic capacitors and wires.
C. Electrical performance description. The parameter description of the switching power supply for LED is mainly the constant current parameter. The size of the current determines the brightness of the LED. If the batch current error is large, the brightness of the whole batch of lamps will be uneven. And the temperature change can also cause the output current of the power supply to shift. Usually the batch error is controlled within +/-5% to ensure the uniform brightness of the lamp. The forward voltage drop of the LED has errors, and the constant current voltage range described by the power supply must include the voltage range of the LED. When multiple LEDs are used in series, the minimum voltage drop multiplied by the number of series connections is the lower limit voltage, and the maximum voltage drop multiplied by the number of series connections is the upper limit voltage. The constant current voltage range of the power supply is slightly wider than this range, and usually a 1-2V margin is left for the upper and lower limits.
d. PCB layout design. The size of the power supply in LED lamps is relatively small (unless the power supply is external), so the requirements for PCB design are relatively high, and there are many factors to consider. The safety distance must be sufficient. The power supply that requires input and output isolation, the primary circuit and the secondary circuit must withstand a voltage of 1500-2000VAC, and at least 3MM of distance must be left on the PCB. If it is a lamp with a metal shell, the layout of the entire power supply must also consider the safety distance between the high-voltage part and the shell. If there is no space to ensure the safety distance, other methods must be used to ensure insulation, such as punching holes in the PCB, adding insulating paper, and potting insulating glue. In addition, the layout must also consider heat balance. The heating components must be evenly distributed and cannot be placed in a concentrated manner to prevent local temperature rise. Electrolytic capacitors are kept away from heat sources to slow down aging and extend their service life.
e. Certification problem. At present, there is no standard for LED lamps in China. The relevant national departments are studying and formulating. The certification of lamps sold in China refers to the standards of lighting lamps. Those exported are CE or UL certified. Some are made according to foreign LED lamp standards. Therefore, it is difficult to design a switching power supply to meet all the above standards at the same time. We can only meet different certifications according to different needs.
4. Use parameters.
When choosing an external power supply, you should mainly consider the constant current and the voltage range of the constant current. The constant current value should be selected to be slightly lower than the standard current of the LED. The voltage range should be moderate, and try not to choose a larger range to avoid power waste.
Three protection methods for LED drive power circuit
1. Use fuses (tubes) to protect LED circuits
Since fuses are disposable, slow to react, poor in effect, and inconvenient to use, fuses are not suitable for LED lamps, because LED lamps are now mainly used in urban lighting projects. It requires the LED protection circuit to be very demanding: when the normal current is exceeded, the protection can be immediately activated, so that the power supply path of the LED is disconnected, so that both the LED and the power supply can be protected, and the power supply can be automatically restored after the entire lamp is normal, without affecting the operation of the LED. The circuit cannot be too complicated, the volume cannot be too large, and the cost must be low. Therefore, it is difficult to implement using fuses.
2. Use transient voltage suppression diodes (TVS for short)
Transient voltage suppression diode is a high-performance protection device in the form of a diode. When its two poles are subjected to a reverse transient high-energy impact, it can immediately reduce the high resistance between its two poles to a low resistance at a very short speed of 10 to the negative 12th power of seconds, absorb up to several kilowatts of surge power, and clamp the voltage between the two poles at a predetermined voltage value, effectively protecting the precision components in the electronic circuit. Transient voltage suppression diodes have the advantages of fast response time, high transient power, low leakage current, good consistency of breakdown voltage deviation, easier to control clamping voltage, no damage limit, and small size.
However, in actual use, it is not easy to find TVS devices that meet the required voltage value. The damage of LED light beads is mainly caused by overheating inside the chip due to excessive current. TVS can only detect overvoltage but not overcurrent. It is difficult to choose the appropriate voltage protection point, so such devices cannot be produced and are difficult to use in practice.
3. Choose a resettable fuse
The resettable fuse is also called a polymer positive temperature thermistor (PTC), which is composed of polymers and conductive particles. After special processing, the conductive particles form a chain-like conductive path in the polymer. When the normal working current passes through (or the component is at normal ambient temperature), the PTC resettable fuse is in a low resistance state; when an abnormal overcurrent passes through the circuit (or the ambient temperature rises), the heat generated by the large current (or the ambient temperature rises) causes the polymer to expand rapidly, thus cutting off the conductive path formed by the conductive particles, and the PTC resettable fuse is in a high resistance state; when the overcurrent (overtemperature state) in the circuit disappears, the polymer cools the LED driver power supply www.leadwayled.com, and the volume returns to normal, in which the conductive particles re-constitute the conductive path, and the PTC resettable fuse is in the initial low resistance state. In the normal working state, the resettable fuse generates very little heat, and in the abnormal working state, it generates very high heat and has a large resistance, which limits the current passing through it, thereby playing a protective role. In a specific circuit, you can choose:
①Branch protection. Generally, LED lights are divided into many series branches. We can add a PTC component in front of each branch for protection. The advantage of this method is high accuracy and good protection reliability.
② Overall protection. Add a PTC element in front of all light beads to protect the entire lamp. The advantage of this method is that it is simple and does not take up space. For civilian products, the results of this protection in actual use are satisfactory.
Previous article:Teach you to learn more about white light LED
Next article:Introducing an efficient LED drive power supply design solution
Recommended ReadingLatest update time:2024-11-16 16:54
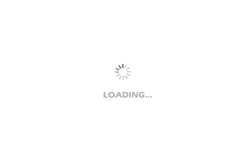
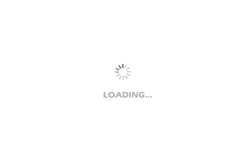
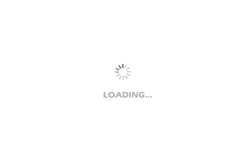
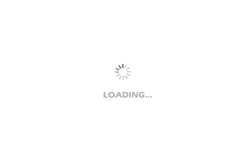
- Popular Resources
- Popular amplifiers
- MathWorks and NXP Collaborate to Launch Model-Based Design Toolbox for Battery Management Systems
- STMicroelectronics' advanced galvanically isolated gate driver STGAP3S provides flexible protection for IGBTs and SiC MOSFETs
- New diaphragm-free solid-state lithium battery technology is launched: the distance between the positive and negative electrodes is less than 0.000001 meters
- [“Source” Observe the Autumn Series] Application and testing of the next generation of semiconductor gallium oxide device photodetectors
- 采用自主设计封装,绝缘电阻显著提高!ROHM开发出更高电压xEV系统的SiC肖特基势垒二极管
- Will GaN replace SiC? PI's disruptive 1700V InnoMux2 is here to demonstrate
- From Isolation to the Third and a Half Generation: Understanding Naxinwei's Gate Driver IC in One Article
- The appeal of 48 V technology: importance, benefits and key factors in system-level applications
- Important breakthrough in recycling of used lithium-ion batteries
- Innolux's intelligent steer-by-wire solution makes cars smarter and safer
- 8051 MCU - Parity Check
- How to efficiently balance the sensitivity of tactile sensing interfaces
- What should I do if the servo motor shakes? What causes the servo motor to shake quickly?
- 【Brushless Motor】Analysis of three-phase BLDC motor and sharing of two popular development boards
- Midea Industrial Technology's subsidiaries Clou Electronics and Hekang New Energy jointly appeared at the Munich Battery Energy Storage Exhibition and Solar Energy Exhibition
- Guoxin Sichen | Application of ferroelectric memory PB85RS2MC in power battery management, with a capacity of 2M
- Analysis of common faults of frequency converter
- In a head-on competition with Qualcomm, what kind of cockpit products has Intel come up with?
- Dalian Rongke's all-vanadium liquid flow battery energy storage equipment industrialization project has entered the sprint stage before production
- Allegro MicroSystems Introduces Advanced Magnetic and Inductive Position Sensing Solutions at Electronica 2024
- Car key in the left hand, liveness detection radar in the right hand, UWB is imperative for cars!
- After a decade of rapid development, domestic CIS has entered the market
- Aegis Dagger Battery + Thor EM-i Super Hybrid, Geely New Energy has thrown out two "king bombs"
- A brief discussion on functional safety - fault, error, and failure
- In the smart car 2.0 cycle, these core industry chains are facing major opportunities!
- The United States and Japan are developing new batteries. CATL faces challenges? How should China's new energy battery industry respond?
- Murata launches high-precision 6-axis inertial sensor for automobiles
- Ford patents pre-charge alarm to help save costs and respond to emergencies
- New real-time microcontroller system from Texas Instruments enables smarter processing in automotive and industrial applications
- What if the uploaded image is not used? See here
- [Xingkong Board Python Programming Learning Main Control Board] Flip Tomato Clock
- How to send more than 20 bytes of data at a time with blue_nrg
- I stayed up late to sort it out. Here is the servo information on the national competition list.
- How to make an overvoltage protection circuit?
- Detailed explanation of starting surge current
- Showing off the goods + the development boards we have used together over the years
- A newbie asks for help, IAR compiles and reports undefined errors
- The motherboard of Huawei P30 looks like this
- RS-485 Transceiver