In recent years, the increasing demand for power has directly led to the latest trend of using digital control for AC-DC and DC-DC power conversion. Digital control provides design flexibility, high performance and high reliability. In order to achieve more efficient power supplies, different topologies are being considered for DC-DC conversion. This article will discuss the digital control of inductor, inductor, capacitor (LLC) resonant converters, the advantages of resonant converters, and the overall advantages of digital control. Digital Control Addresses the Demand for Power Since many power supplies operate at loads far below the maximum load or the load at which they operate most efficiently most of the time, improved efficiency is often required in normal mode and low-power modes. For example, the 80 PLUS program requires 115V power supplies to achieve at least 80% efficiency at 20%, 50% and 100% of rated load. Achieving higher efficiency at these operating points can result in bronze, silver, gold or platinum ratings. For 230V power supplies, the minimum bronze standard requires efficiency of 81% at 20% load, 85% at 50% load and 81% at 100% load. The U.S. Department of Energy has extended its push for more efficient products to data centers through the ENERGY STAR Data Center Energy Efficiency Program. The program is designed to address all energy-intensive aspects of a facility, including information technology (IT) equipment and supporting infrastructure such as uninterruptible power supplies (UPS). Many procurement specifications require that purchased products meet these standards or be certified to other recognized energy efficiency standards, forcing suppliers to meet these levels or lose market share. Therefore, achieving higher efficiency is urgent. Reducing operating costs alone is enough to drive energy efficiency improvements. Applications in the medium and high power range (200 to 1000W), such as telecommunications, are increasingly implementing lower power supplies to control operating costs for powering and cooling equipment. To achieve the highest efficiency, many designers are turning to digital control, which also provides design flexibility, high performance, and high reliability. With low-pin-count digital signal controllers (DSCs), such as Microchip Technology's dsPIC DSCs, complex control can be achieved through the digital signal processing (DSP) capabilities and intelligent power peripherals of these devices. Before adding digital control, it is necessary to understand the basic principles of resonant converters. Advantages of Resonant Converters Converters that operate in resonant mode (where the impedance between the input and output of the circuit is minimal) offer higher efficiency. With resonant converters, the power dissipation in the MOSFET is greatly reduced by providing a sinusoidal voltage or current to the MOSFET and switching it close to the zero crossing of the sinusoidal voltage or current. Switching the MOSFET when the drain-source voltage is close to zero (i.e., zero voltage switching, ZVS) and transitioning the MOSFET from one state to another when the current through the switch is zero (i.e., zero current switching, ZCS) minimizes the MOSFET switching losses. This soft switching approach also reduces noise in the system and provides enhanced immunity to electromagnetic interference (EMI). ZVS is the preferred choice for high-voltage, high-power systems. In a resonant switching converter, reactive elements (capacitors and inductors) are added around the switch to generate a sinusoidal voltage or current. The three main categories of resonant converters are: series resonant converter (SRC), parallel resonant converter (PRC), and a combination of the two, series-parallel resonant converter (SPRC). Figure 1 shows a block diagram of an advanced resonant converter and the three types of resonant tanks. Figure 1 : Advanced resonant converter structures have many different forms of resonant tanks. As the name implies, in a series resonant converter, the load is in series with the resonant inductor and capacitor. The gain of the resonant tank is ≤ 1. When the SRC operates at no load, its output voltage cannot be regulated. For ZVS, the circuit needs to operate above the resonant frequency in the inductive region. At low line voltages, the SRC operates close to the resonant frequency. In a PRC, the load is connected in parallel with the resonant capacitor. The PRC can operate at no load output, but unlike the SRC, its output voltage can be regulated at no load. For ZVS, the PRC also needs to operate above the resonant frequency in the inductive region. Similar to the SRC, the PRC operates close to the resonant frequency at low line voltages, but the PRC differs in that it has larger circulating currents. The series inductor and shunt capacitor provide inherent short-circuit protection. In an SPRC, the resonant circuit is a combination of series and shunt converters, which can be either LCC or LLC configurations. Similar to the SRC and PRC, the SPRC LCC design cannot be optimized at high input voltages. Therefore, the LLC is the preferred solution for many applications. The LLC resonant tank is shown in Figure 1. The LLC converter can be operated at the resonant frequency at the nominal input voltage and is capable of operating at no load. In addition, it can be designed to operate over a wide input voltage range. Zero voltage and zero current switching are achieved throughout the entire operating range. The performance of a resonant converter can be measured by several parameters. The quality factor (Q) of a resonant circuit is a dimensionless parameter that describes the amount of damping in the circuit. It is defined as the ratio of the power stored to the power dissipated in the circuit. A higher Q value indicates a narrower bandwidth of the resonant tank. Quality is a key parameter for the gain of a resonant circuit, also known as the voltage conversion ratio or M. By considering a series of M curves generated when λ, the normalized frequency, or the Q value is varied, an indication of the performance of the resonant converter can be obtained before all parameters are calculated. M is defined as follows: M(fsw)=f(fn,λ,Q) Where, fn=normalized frequency, f/fr; λ=inductance ratio, Lr/Lm; Q=quality factor, a function of the output impedance. As shown in Figure 2, the LLC circuit with Q as a parameter actually has two resonant frequencies, one determined by the series inductor Lr and capacitor Cr (Q is 0.5) and the other determined by the parallel inductor Lm. Lr and Cr have a resonant frequency when fn=1 (fr), and Lm+Lr and Cr have a resonant frequency when fn is approximately equal to 0.5. Figure 2: Depending on the quality factor (Q), different gains can be obtained from the resonant tank. The Y-axis is the resonant tank gain (M). All Q curves intersect at the resonant frequency (fn=1). The different operating modes of the LLC include: at the resonant frequency, below the resonant frequency, and above the resonant frequency. When operating at the resonant frequency, the MOSFET switches at the resonant frequency within a very narrow timing window (determined by the selected components). The losses generated at this time are very low. When operating below the resonant frequency, the circuit characteristics are similar to those when operating at the resonant frequency, but the loop current is limited by the magnetizing current for a period of time during the cycle. If a MOSFET is used instead of a diode on the secondary side for synchronous rectification, the gate must be turned off at the appropriate time. This usually requires current sensing techniques, such as measuring the voltage drop across the MOSFET. When operating above the resonant frequency, the loop current is greater than the magnetizing current and is no longer limited by the magnetizing current. In this region, the synchronous switch can be turned on and off at the same time as the primary side switch, simplifying their control. Due to the use of zero voltage switching, an inherent advantage of LLC resonant power supplies is that electromagnetic interference and radio interference are very low. Efficient digital control topology uses current digital signal controllers to easily implement full digital control of power conversion and system management functions of LLC resonant converters.
The actual LLC circuit components and parts, in addition to those shown in Figure 1, include the DC input, switching network, LLC resonant tank, transformer, rectifier, filter, and load. Figure 3 shows the digital control added to the LLC resonant converter. This design represents a design that can be specified for telecom circuits. In these applications, LLC converters are widely used as DC/DC converters following the power factor correction (PFC) circuit in AC-DC systems. The typical PFC output voltage is about 400V and can be directly fed into the LLC converter. The wide input range allows the use of large capacitance capacitors with small size. The design specifications are summarized in Table 1. Figure 3: The reference design high-level block diagram illustrates how the digitally controlled feedback loop is added to the LLC resonant converter. Table 1: The reference design specifications meet the needs of many telecom power supplies. The dsPIC33FJ GS provides digital computing capabilities for the resonant converter. Its 40MIPS performance and intelligent power peripherals make it an ideal choice for this application. Peripherals include high-speed PWM (16-bit, cycle resolution of 1ns) and phase-shiftable outputs. The switching circuit in the reference design uses a half-bridge topology, so the half-bridge voltage swings between 0V and Vd=400Vdc nominal. The resonant tank consists of capacitors, inductors, and the magnetizing inductance of the isolation transformer. Because the design uses the magnetizing inductance of the transformer, no external inductor is required, reducing system cost. The design also uses the leakage inductance of the transformer as the secondary inductor, eliminating the need for an additional external inductor, saving further cost. If the resonant tank is properly tuned to the switching frequency, the resonant tank presents a finite impedance to the fundamental frequency and very high impedance to all other harmonic frequencies. The impedance of the tank causes a phase shift between the voltage and current, allowing zero voltage switching. Zero voltage switching of the primary MOSFET is shown in Figure 4. Figure 4: In this reference design, the half-bridge MOSFET switches without any conduction losses due to the phase shift between the resonant tank current and the MOSFET voltage. Synchronous rectifiers are used in the secondary side design instead of diodes to reduce conduction losses on the secondary side. This reduces the losses caused by the forward resistance (Rf) and the forward voltage of the diode. Figure 5 shows the switching waveforms of the synchronous rectifier. Figure 5: To eliminate turn-off losses in the secondary-side (synchronous) rectifier, the MOSFET drain-source voltage is increased after the MOSFET current reaches zero. The legend is the same as Figure 4, i.e., green line = MOSFET gate-source voltage, purple line = MOSFET drain-source voltage, and yellow line = MOSFET current. For synchronous rectification, digital control performs the MOSFET switching without the need for current sensing circuitry on the secondary side. This allows full-wave rectifier designs to be more efficient and less expensive. Figure 6 shows the efficiency over a range of load currents. Additional benefits include increased flexibility in compensator design, as the DSC also implements duty-cycle controlled soft-start. Figure 6: LLC efficiency at two different operating voltage inputs shows its insensitivity to input voltage. Efficiency of more than 80% is achieved at output load currents below 2A. Maximum efficiency is 95% at higher loads, and the efficiency curve is extremely flat from 7 to 17A of output load current. Because power conversion control can be implemented in easily reprogrammable software, digital solutions give designers the freedom to innovate and easily modify or adapt their designs. In addition to enabling the addition of cost-effective, value-creating new features, precise digital control can also improve the reliability of the power supply. Using reference designs can reduce development time, time to market, and mitigate manufacturing issues that may arise from the beginning of the design. This article summarizes the performance advantages of LLC resonant converters, making this design method an ideal choice for improving energy efficiency in medium and high power telecommunications applications. At the same time, adding digital control also provides electronic systems with the design flexibility, high performance and high reliability that designers expect. To easily achieve the above two points, reference designs provide the easiest way to evaluate the system and shorten the time to market, or more appropriately, shorten the time to achieve higher efficiency.
Reference address:LLC resonant converter improves DC-DC efficiency
The actual LLC circuit components and parts, in addition to those shown in Figure 1, include the DC input, switching network, LLC resonant tank, transformer, rectifier, filter, and load. Figure 3 shows the digital control added to the LLC resonant converter. This design represents a design that can be specified for telecom circuits. In these applications, LLC converters are widely used as DC/DC converters following the power factor correction (PFC) circuit in AC-DC systems. The typical PFC output voltage is about 400V and can be directly fed into the LLC converter. The wide input range allows the use of large capacitance capacitors with small size. The design specifications are summarized in Table 1. Figure 3: The reference design high-level block diagram illustrates how the digitally controlled feedback loop is added to the LLC resonant converter. Table 1: The reference design specifications meet the needs of many telecom power supplies. The dsPIC33FJ GS provides digital computing capabilities for the resonant converter. Its 40MIPS performance and intelligent power peripherals make it an ideal choice for this application. Peripherals include high-speed PWM (16-bit, cycle resolution of 1ns) and phase-shiftable outputs. The switching circuit in the reference design uses a half-bridge topology, so the half-bridge voltage swings between 0V and Vd=400Vdc nominal. The resonant tank consists of capacitors, inductors, and the magnetizing inductance of the isolation transformer. Because the design uses the magnetizing inductance of the transformer, no external inductor is required, reducing system cost. The design also uses the leakage inductance of the transformer as the secondary inductor, eliminating the need for an additional external inductor, saving further cost. If the resonant tank is properly tuned to the switching frequency, the resonant tank presents a finite impedance to the fundamental frequency and very high impedance to all other harmonic frequencies. The impedance of the tank causes a phase shift between the voltage and current, allowing zero voltage switching. Zero voltage switching of the primary MOSFET is shown in Figure 4. Figure 4: In this reference design, the half-bridge MOSFET switches without any conduction losses due to the phase shift between the resonant tank current and the MOSFET voltage. Synchronous rectifiers are used in the secondary side design instead of diodes to reduce conduction losses on the secondary side. This reduces the losses caused by the forward resistance (Rf) and the forward voltage of the diode. Figure 5 shows the switching waveforms of the synchronous rectifier. Figure 5: To eliminate turn-off losses in the secondary-side (synchronous) rectifier, the MOSFET drain-source voltage is increased after the MOSFET current reaches zero. The legend is the same as Figure 4, i.e., green line = MOSFET gate-source voltage, purple line = MOSFET drain-source voltage, and yellow line = MOSFET current. For synchronous rectification, digital control performs the MOSFET switching without the need for current sensing circuitry on the secondary side. This allows full-wave rectifier designs to be more efficient and less expensive. Figure 6 shows the efficiency over a range of load currents. Additional benefits include increased flexibility in compensator design, as the DSC also implements duty-cycle controlled soft-start. Figure 6: LLC efficiency at two different operating voltage inputs shows its insensitivity to input voltage. Efficiency of more than 80% is achieved at output load currents below 2A. Maximum efficiency is 95% at higher loads, and the efficiency curve is extremely flat from 7 to 17A of output load current. Because power conversion control can be implemented in easily reprogrammable software, digital solutions give designers the freedom to innovate and easily modify or adapt their designs. In addition to enabling the addition of cost-effective, value-creating new features, precise digital control can also improve the reliability of the power supply. Using reference designs can reduce development time, time to market, and mitigate manufacturing issues that may arise from the beginning of the design. This article summarizes the performance advantages of LLC resonant converters, making this design method an ideal choice for improving energy efficiency in medium and high power telecommunications applications. At the same time, adding digital control also provides electronic systems with the design flexibility, high performance and high reliability that designers expect. To easily achieve the above two points, reference designs provide the easiest way to evaluate the system and shorten the time to market, or more appropriately, shorten the time to achieve higher efficiency.
Previous article:A flicker-free, electrolytic capacitor-free AC-DC LED driver that reduces LED current
Next article:Integrate power management and conversion to simplify power system design
Recommended ReadingLatest update time:2024-11-17 11:40
Isolated DC-DC converter combining the advantages of DPA and IBA
Introduction
Terminal systems such as advanced telecommunications and wireless architectures, network and communication technologies, and high-speed service platforms require continuous improvement and newer products. With the market's requirements, newer and faster ASICs, DSPs, FPGAs, high-speed microproc
[Power Management]
Driving High-Performance ASICs and Microprocessors with Multiphase DC-DC Converters
Multi-phase DC-DC converter leads
Today's high-performance ASICs and microprocessors have been widely used in various fields such as industrial control, communications, and aerospace. However, due to their high power consumption, sometimes up to 150W or even more, for a power supply voltage of 1V to 1.5V, t
[Power Management]
A design scheme for high-frequency push-pull DC-DC converters used in vehicles
introduction With the increase in the types of electrical equipment used in modern cars and the increase in power levels, more and more types of power supplies are required, including AC power and DC power. These power supplies all require a switching converter to increase the DC voltage of +12VDC or +24VDC provide
[Power Management]
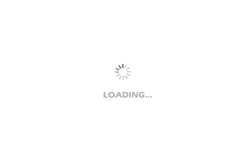
Driver selection for different DC-DC LED lighting applications
In recent years, the application areas of high-brightness LEDs have continued to increase, covering a range from mobile device backlighting, medium and large-sized LCD backlighting, automotive interior and exterior lighting to general lighting. Common DC-DC LED lighting applications include landscape lighting, internal
[Analog Electronics]
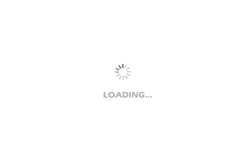
Design of DC-DC Converter Based on MAX1524
1 Introduction
MAX1524 is a small, step-up DC-DC converter produced by MAXIM, USA. It can be applied to various topologies such as step-up, SEPIC, and flyback. With fixed on-time and minimum off-time, it can provide high efficiency under a wide range of input/output voltage combinations and load currents. Th
[Microcontroller]
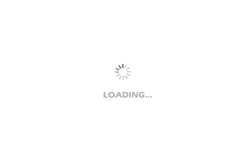
Research on a Quasi-Z-Source DC-DC Converter
With the rapid development of science and technology, switching power supplies have been widely used in many fields such as automatic control, aerospace, and new energy due to their advantages such as low cost, miniaturization, high efficiency, high reliability, and wide voltage regulation range. The traditional topo
[Power Management]
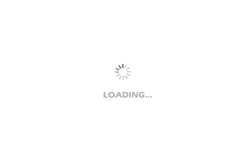
- Popular Resources
- Popular amplifiers
-
New Energy Vehicle Detection and Diagnosis Experiment (Edited by Mao Caiyun, Zhou Xien, and Long Jiwen)
-
Virtualization Technology Practice Guide - High-efficiency and low-cost solutions for small and medium-sized enterprises (Wang Chunhai)
-
Design of an adaptive constant on-time buck DC-DC converter with high efficiency and low power consumption
-
Research on design technology of high-efficiency step-up DC-DC converter with wide load range
Recommended Content
Latest Power Management Articles
- MathWorks and NXP Collaborate to Launch Model-Based Design Toolbox for Battery Management Systems
- STMicroelectronics' advanced galvanically isolated gate driver STGAP3S provides flexible protection for IGBTs and SiC MOSFETs
- New diaphragm-free solid-state lithium battery technology is launched: the distance between the positive and negative electrodes is less than 0.000001 meters
- [“Source” Observe the Autumn Series] Application and testing of the next generation of semiconductor gallium oxide device photodetectors
- 采用自主设计封装,绝缘电阻显著提高!ROHM开发出更高电压xEV系统的SiC肖特基势垒二极管
- Will GaN replace SiC? PI's disruptive 1700V InnoMux2 is here to demonstrate
- From Isolation to the Third and a Half Generation: Understanding Naxinwei's Gate Driver IC in One Article
- The appeal of 48 V technology: importance, benefits and key factors in system-level applications
- Important breakthrough in recycling of used lithium-ion batteries
MoreSelected Circuit Diagrams
MorePopular Articles
- Innolux's intelligent steer-by-wire solution makes cars smarter and safer
- 8051 MCU - Parity Check
- How to efficiently balance the sensitivity of tactile sensing interfaces
- What should I do if the servo motor shakes? What causes the servo motor to shake quickly?
- 【Brushless Motor】Analysis of three-phase BLDC motor and sharing of two popular development boards
- Midea Industrial Technology's subsidiaries Clou Electronics and Hekang New Energy jointly appeared at the Munich Battery Energy Storage Exhibition and Solar Energy Exhibition
- Guoxin Sichen | Application of ferroelectric memory PB85RS2MC in power battery management, with a capacity of 2M
- Analysis of common faults of frequency converter
- In a head-on competition with Qualcomm, what kind of cockpit products has Intel come up with?
- Dalian Rongke's all-vanadium liquid flow battery energy storage equipment industrialization project has entered the sprint stage before production
MoreDaily News
- New breakthrough! Ultra-fast memory accelerates Intel Xeon 6-core processors
- New breakthrough! Ultra-fast memory accelerates Intel Xeon 6-core processors
- Consolidating vRAN sites onto a single server helps operators reduce total cost of ownership
- Consolidating vRAN sites onto a single server helps operators reduce total cost of ownership
- Allegro MicroSystems Introduces Advanced Magnetic and Inductive Position Sensing Solutions at Electronica 2024
- Car key in the left hand, liveness detection radar in the right hand, UWB is imperative for cars!
- After a decade of rapid development, domestic CIS has entered the market
- Aegis Dagger Battery + Thor EM-i Super Hybrid, Geely New Energy has thrown out two "king bombs"
- A brief discussion on functional safety - fault, error, and failure
- In the smart car 2.0 cycle, these core industry chains are facing major opportunities!
Guess you like
- The problem of maintaining three minutes after clearing
- TLP3547 Evaluation Board Evaluation 3: Operating Temperature Rise Test
- Arduino-style pyb
- Application of CAN bus in automobiles
- A new embedded GUI
- How to measure analog voltage using the ADC of MSP430?
- ADI New Chinese Information (November 2019)
- Please recommend a camera and FPGA development board for image processing
- Board-to-board connector manufacturers recommend
- ADC2000 Automotive Diagnostic Computer