Solid-state drive (SSD) designers face many conflicting requirements when it comes to powering the drive. The first is the size of the power supply, which cannot increase the form factor of the SSD, as SSDs must generally be physically compatible with the mechanical hard disk drives (HDDs) they replace. The second is the ever-increasing system efficiency requirements, both in standby mode (no reads or writes to the SSD) and in maximum power mode (reads and writes at peak performance). These efficiencies are often backed by specific SSD certifications, such as Energy Star, and are critical to market acceptance. The final issue is how the power supply responds to the changing needs of the end user. Can the power supply respond quickly enough to deliver strong power to the SSD when going from idle to high-performance states? Or will the SSD "hang" if the host suddenly reads or writes to the SSD at high speed or with large amounts of data? This article will analyze three SSD power supply solutions, measuring and comparing their size, efficiency, and response time to arrive at the best SSD power supply solution.
SSD Architecture
Figure 1 shows an example diagram of an SSD system installed in a server. A 12V bus powers a switch-mode power supply (SMPS), which provides 3.3V to the SSD. NAND flash is used as memory because of its low cost and ability to store data without power. An ASIC or other processor communicates with the host and manages the data flow. 2.5V and 1.8V are common requirements for ASICs.
Figure 1: SSD power supply system
First, the SMPS must be a synchronous buck converter, not a linear regulator or asynchronous buck converter, to provide high efficiency at high load currents. Second, it must also have a power-save mode to keep efficiency above a minimum (even when the SSD is idle). Third, it must operate from a medium-voltage, 12V input bus and provide output voltages as low as 1.8V or even lower, depending on the needs of the ASIC. Finally, the SMPS should optimize its size, efficiency, and response time to meet the needs of the SSD system.
size
As SSDs begin to gain market acceptance, they are required to be backward compatible with mechanical hard disks in terms of size and functionality. When a user's mechanical hard disk fails (sometimes it may not be used for a year), SSDs become a high-reliability alternative. Users only need to order an SSD of the same size as the failed mechanical hard disk, and the reliability of their personal computer or server can be upgraded immediately.
As SSD prices continue to fall, they are no longer just replacements for mechanical hard drives that have reached the end of their lifespan. SSDs are now entering high-reliability market segments such as enterprise servers and consumer applications such as laptops. For these applications, miniaturization is important and SSDs no longer have to be exactly the same size as mechanical hard drives.
In either case, small solution size is a big selling point for SSDs. Although not the largest subsystem in an SSD, the power supply still takes up a lot of board space because the SSD circuits are powered by several separate SMPSs. The traditional long inductors required reach the size limits of Z-direction-making (a three-dimensional problem).
efficiency
An important overhead cost of a server is its power consumption. This includes the power consumed by the drive (hard disk) and the power consumed to maintain the appropriate temperature in the server room for heat dissipation. With the continuous rise in electricity prices and the emphasis on "green" operations, higher and higher requirements are placed on the energy efficiency of SSDs.
In laptops, more efficient SSDs can lead to longer battery life and cooler body temperatures. Both of these are very desirable selling points that end users can easily understand and are willing to pay for. Especially for laptops, the power consumption and efficiency of the SSD when idle is critical, as these parameters greatly affect the battery life. Compared to mechanical hard drive systems, SSDs provide longer battery life, cooler laptops, and lower hard drive failure rates.
Response time
Even if the device is low and efficient when idle, what about when a server or laptop wakes up and reads or writes to the SSD? Can the power supply go from idle to full power quickly enough to avoid an SSD reset due to a supply voltage drop?
This is a very tricky design challenge for SMPS designers. On the one hand, the SMPS should be close to the power-off state, and the number of circuits operating should be as small as possible to minimize the power consumption in the device idle mode. On the other hand, the SMPS circuit should be biased and ready to respond quickly to the user's SSD read and write operations. Such conflicting requirements require careful balancing and trade-offs. ICs designed specifically to meet SSD requirements can provide the best solution.
Three SSD power solutions
We focus on the SMPS that drives NAND flash memory using 3.3V voltage, taking into account other power requirements of SSDs. We analyze that there are three power solutions that can be applied to various SSDs: full-featured solutions, minimum volume solutions, and high-efficiency dedicated solutions. To evaluate the response time of each solution, we use a load current step from 10 mA to 1 A, which is also the typical load current when the SSD goes from idle to accepting read and write operations.
One SSD application requires very tight electromagnetic interference (EMI) control and very low radiation. It may be used in a hospital or airplane environment. In this environment, numerous devices transmit data wirelessly and generate electromagnetic interference of various frequencies. For this type of application, the SSD should strictly control its switching frequency to control the radiation within a narrow band, so that it is easier to control, reduce or eliminate them. This power solution is called a full-featured solution because it includes complex functions that are not necessary in most SSD applications. The TPS62110 is an example of such a full-featured solution, and its efficiency characteristics are shown in Figure 2 and the response time is shown in Figure 3. The size of this full-featured solution is about 175 mm2, but its maximum component height is 3.2 mm due to the relatively large inductance required.
Figure 2: Full-featured SSD power solution efficiency.
Figure 3: Full-featured SSD power solution response time.
The second SSD application requires the smallest overall solution size. It can be used in high-performance laptops or to match the size of a special mechanical hard disk. To achieve a small size, we need an SSD optimized power solution. This solution increases the switching frequency to make the output filter more compact and reduces the functions to the minimum requirements. The TPS62140 achieves both goals and supports a solution size of only 74 mm2 with a maximum height of 2 mm. Figure 4-5 shows the efficiency and response time of this solution.
Figure 4: Minimum size SSD power solution efficiency.
Figure 5: Minimum size SSD power solution response time.
The third SSD power solution requires the highest efficiency over the entire load range. This requirement is extremely important in a server environment where heat dissipation and power cost overhead are a big issue, but a slightly larger solution size can be used. Fortunately, the minimum size power solution includes a function that selects the switching frequency of the device to achieve the minimum solution size or the highest efficiency. If operating at the highest switching frequency (as in the second example), the solution size is absolutely minimum. However, the switching losses of the power stage will increase due to the high operating frequency, resulting in reduced efficiency. If operating in the highest efficiency mode, the solution size becomes 85 mm2 with a maximum height of 1.4 mm. Figure 6-7 shows the efficiency and response time of this highest efficiency solution.
Figure 6: Efficiency of the highest efficiency SSD power solution.
Figure 7: Response time of the most efficient SSD power solution.
Figure 8 and Table 1 show the comparison of these three solutions:
Figure 8: Efficiency comparison of full-featured, smallest size, and highest efficiency solutions.
Table 1: Performance comparison of full-featured, smallest size, and highest efficiency solutions.
These three SSD power solutions have distinct and obvious advantages and disadvantages. The full-featured solution can strictly control electromagnetic interference, which is a basic requirement for some applications. In addition, it has higher efficiency, especially when the load current is stronger. However, the efficiency gradually decreases when the load decreases, and the solution size (area) and height are larger than the other two solutions. It is a completely acceptable solution in applications with strict EMI regulations or radiation requirements, or when small size is not required.
The last two solutions are optimized to achieve the highest performance SSD system. The smallest solution and the most efficient solution have faster response times and lower voltages than the full-featured solution. This allows the host ASIC to start the SSD faster without the SMPS output voltage, and to read and write to it more quickly, leaving a trim window to trigger a system reset. Of the two solutions, the smallest solution is ideal for SSDs that require the absolute smallest solution size. This leaves the most area for other components of the SSD system, resulting in a larger storage capacity SSD. If a slightly larger SMPS solution can be used, the most efficient solution can achieve higher efficiency than the full-featured solution while occupying only half the area. At high load currents, its efficiency is not limited by the SMPS itself, but by the selected inductor (for example: Coilcraft LPS4414-332). At higher loads, the resistive losses (inductor DCR and MOSFET Rds-on) exceed the frequency-dependent losses. Therefore, the efficiency advantage of low switching frequency operation is reduced as the load increases. When using a larger inductor with lower DCR, the highest efficiency solution exceeds the full-featured solution efficiency across the entire load range. As in the third example, it has the same efficiency as the full-featured solution at heavy loads, but with half the solution size and height.
One of the ultimate challenges facing SSD designers is designing power supplies for SSDs of varying capacity, which require currents that vary with capacity. If an SSD only requires 500mA, a 3A SSD power supply is beyond design needs and is too expensive. SSDs of varying capacity require an adjustable power supply to enable design reuse and reduce the NRE costs associated with new SMPS designs. Fortunately, the SMPS ICs used for both the smallest size solutions and the most efficient solutions are pin-to-pin compatible with both high and low load current versions. When designing smaller capacity SSDs, low current SMPS ICs can be used to reduce bill of materials costs. Similarly, using high current SMPS integrated circuit versions can immediately increase the output current capability of the SMPS to power larger capacity SSDs.
in conclusion
When determining the power supply, SSD system designers need to carefully consider their design goals. Will the SSD be used in a highly stable, EMI-sensitive environment (such as a hospital, etc.)? Will the SSD be required to completely match the volume factor and size of a mechanical hard disk to achieve the purpose of directly replacing the mechanical hard disk? Will the SSD be used in a server room where the price of electricity is constantly soaring? Based on these considerations (EMI, size and efficiency), we must balance and compromise between three different types of optimized SSD power solutions. After considering these design goals, the optimal switching power supply can achieve the highest performance of the SSD and meet the needs of many applications.
Previous article:Detailed explanation of the circuit and components of the phase-shift controlled full-bridge PWM converter
Next article:Design and implementation of current and voltage transmitter based on CAN bus
Recommended ReadingLatest update time:2024-11-16 19:33
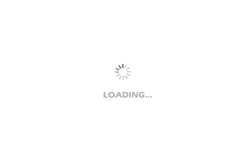
![[MCU framework][drivers layer][oled][SSD1306] Instructions for using oled](https://6.eewimg.cn/news/statics/images/loading.gif)
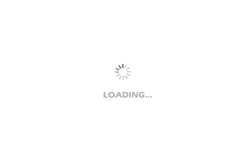
- MathWorks and NXP Collaborate to Launch Model-Based Design Toolbox for Battery Management Systems
- STMicroelectronics' advanced galvanically isolated gate driver STGAP3S provides flexible protection for IGBTs and SiC MOSFETs
- New diaphragm-free solid-state lithium battery technology is launched: the distance between the positive and negative electrodes is less than 0.000001 meters
- [“Source” Observe the Autumn Series] Application and testing of the next generation of semiconductor gallium oxide device photodetectors
- 采用自主设计封装,绝缘电阻显著提高!ROHM开发出更高电压xEV系统的SiC肖特基势垒二极管
- Will GaN replace SiC? PI's disruptive 1700V InnoMux2 is here to demonstrate
- From Isolation to the Third and a Half Generation: Understanding Naxinwei's Gate Driver IC in One Article
- The appeal of 48 V technology: importance, benefits and key factors in system-level applications
- Important breakthrough in recycling of used lithium-ion batteries
- Innolux's intelligent steer-by-wire solution makes cars smarter and safer
- 8051 MCU - Parity Check
- How to efficiently balance the sensitivity of tactile sensing interfaces
- What should I do if the servo motor shakes? What causes the servo motor to shake quickly?
- 【Brushless Motor】Analysis of three-phase BLDC motor and sharing of two popular development boards
- Midea Industrial Technology's subsidiaries Clou Electronics and Hekang New Energy jointly appeared at the Munich Battery Energy Storage Exhibition and Solar Energy Exhibition
- Guoxin Sichen | Application of ferroelectric memory PB85RS2MC in power battery management, with a capacity of 2M
- Analysis of common faults of frequency converter
- In a head-on competition with Qualcomm, what kind of cockpit products has Intel come up with?
- Dalian Rongke's all-vanadium liquid flow battery energy storage equipment industrialization project has entered the sprint stage before production
- Allegro MicroSystems Introduces Advanced Magnetic and Inductive Position Sensing Solutions at Electronica 2024
- Car key in the left hand, liveness detection radar in the right hand, UWB is imperative for cars!
- After a decade of rapid development, domestic CIS has entered the market
- Aegis Dagger Battery + Thor EM-i Super Hybrid, Geely New Energy has thrown out two "king bombs"
- A brief discussion on functional safety - fault, error, and failure
- In the smart car 2.0 cycle, these core industry chains are facing major opportunities!
- The United States and Japan are developing new batteries. CATL faces challenges? How should China's new energy battery industry respond?
- Murata launches high-precision 6-axis inertial sensor for automobiles
- Ford patents pre-charge alarm to help save costs and respond to emergencies
- New real-time microcontroller system from Texas Instruments enables smarter processing in automotive and industrial applications
- How to deal with impedance continuity of PCB traces?
- Develop and study Hongmeng system-data collection
- Why can't CCS5.5 be installed?
- [National Technology N32G457 Review] DHT22 temperature and humidity detection
- What is the relationship between MCIMX6Y2CVM05AB and IMX6ULL?
- MSP430 FRAM Microcontrollers Enable Energy Harvesting
- Lesson 3: Exploring the Cellular Communication Module OpenCPU
- MSP-EXP430F5529LPPWM library function + clock configuration
- [Raspberry Pi 4B Review] Raspberry Pi 4 IP address setting, source replacement, adding power button and heat dissipation.
- Design of ESD protection structure for CMOS circuits