Light-emitting diodes (LEDs) appeared in the 1960s. In the early 1990s, due to breakthroughs in epitaxy and chip technology, full colorization appeared, and the device input power and luminous brightness were greatly improved. At present, the LED industry has entered a period of rapid development with high power and high brightness. It is reported that my country's power-type and high-power LEDs have reached the international advanced level of industrialization. The packaging of downstream devices has achieved mass production and has become an important LED packaging base in the world. In the LED industry, the research and production of epitaxial wafers and chips have progressed rapidly, but the research on packaging materials has been relatively neglected. For a long time, the process of LED packaging has not changed much, and there has been no revolutionary breakthrough in packaging materials.
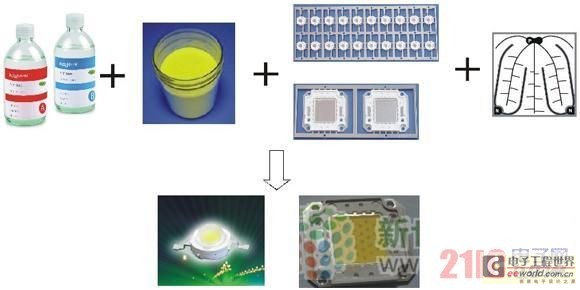
my country started late in the research and production of LED packaging materials and processes, with few varieties, and a large gap between the technical level and production scale and the international level. Currently, there are only epoxy resin packaging materials for low-power LEDs. At present, high-end LED devices and high-power LED packaging silicone materials need to be imported, which are expensive, greatly restricting the development of my country's LED industry. At present, domestic research units and production enterprises related to silicone materials lack understanding of the LED packaging industry, and have carried out little scientific research and development work on products related to LED packaging silicone materials. The existing domestic silicone packaging materials have some defects: low refractive index, poor heat resistance, weak resistance to ultraviolet radiation, insufficient product adhesion, low light transmittance, etc. These defects directly affect the luminous efficiency and life of LED devices. Combined with the performance requirements of LED devices for packaging materials, this paper reviews the research status of high-power LED packaging materials at home and abroad in recent years, and discusses the problems existing in the current high-power LED silicone packaging materials and the next research direction.
1. Performance requirements for LED packaging materials
LED packaging materials must meet the requirements of packaging technology on the one hand, and meet the working requirements of LED on the other hand. At present, traditional epoxy resin packaging materials can no longer meet the requirements of high-power LED packaging in terms of UV resistance and thermal aging performance. Many experts even believe that the backwardness of packaging materials and processes has become a bottleneck for the development of the LED industry. Therefore, it is necessary for us to understand the performance requirements of LED packaging materials.
1.1. Packaging process requirements for material performance
In order to meet the needs of the actual assembly process of LEDs, the packaging material must have appropriate viscosity, adhesion and heat resistance, including: a. Physical properties before curing and general properties after curing. The physical properties before curing are related to operability, among which viscosity and curing characteristics are particularly important. Due to the high expansion rate of polymer materials, the material shrinks significantly after cooling after thermal curing, resulting in stress at the interface with the surrounding materials, which in turn causes peeling and cracks in the material, so it is cured at as low a temperature as possible. b. Surface adhesion; the sealing material exposed on the surface of the package is sticky, which will cause the sealing materials to stick to each other. This situation that cannot be peeled off from the material selection machine will lead to reduced operability. In addition, during use, dust will stick and brightness will be reduced. From the perspective of peeling resistance and crack resistance, we need a softer packaging material, but in general, the softer the material, the higher the viscosity, so we need a material with a good balance between the two, c. Lead-free reflow. In recent years, the requirements for lead-free solder surface treatment have become increasingly higher, which also shows that the requirements for heat resistance of packaging materials have become increasingly higher. Under high temperature counterflow conditions, peeling, cracks, wire breakage, etc. may occur due to coloring and drastic thermal changes.
1.2. Light transmittance
The absorption of visible light by LED packaging materials will result in low light extraction rate. The packaging materials should have low light absorption rate and high transparency. Compared with epoxy resin, silicone resin has higher transparency. Currently, the packaging materials prepared by silicone resin have a transmittance of more than 95% in the ultraviolet region, which increases the light transmittance and luminous intensity of high-power LED devices.
1.3 Refractive index
The difference in refractive index between the LED chip and the packaging material will have a great impact on the light extraction efficiency. Therefore, increasing the refractive index of the material and making it as close to the refractive index of the LED chip as possible will facilitate the transmission of light. Generally speaking, the refractive index of the LED chip (n=2.2-2.4) is much higher than the refractive index of the silicone packaging material (n=1.41). When the chip emits light through the packaging material, a total reflection effect will occur on its interface, causing most of the light to be reflected back into the chip and unable to be effectively exported, directly impairing the brightness efficiency. To solve this problem, the refractive index of the packaging material must be increased to reduce the total reflection loss. Studies have shown that as the refractive index of the packaging material increases, the brightness of the LED will increase. For red LED devices, when the refractive index of the packaging material is 1.7, the external light extraction efficiency can be increased by 44%. Therefore, the importance of developing high-refractive-index transparent materials to reduce the refractive index difference between the chip and the packaging material is obvious.
1.4. Thermal aging and light resistance
In high-power, high-brightness LEDs, the packaging material is not only exposed to strong light, but also affected by heat dissipation. Therefore, the packaging material needs to be both light-resistant and heat-resistant. Even if exposed to high temperatures for a long time, the sealing material is required to ensure that it does not change color and has stable physical properties.
2. Research status of LED packaging materials
2.1 Modified silicone/epoxy resin packaging materials
As the power and brightness of LEDs increase, epoxy resins are increasingly unable to meet the packaging requirements in terms of reliability, UV resistance, and aging resistance. However, epoxy resins have excellent electrical properties and bonding properties, and are especially cheap and low in cost. Therefore, over the past period of time, researchers have not given up on using epoxy resins, but have adopted the method of using silicone to modify epoxy resins to develop packaging materials that combine the advantages of both materials.
Considering that the heat and light of LED chips are the main causes of packaging material aging, some packaging manufacturers use silicone materials in the inner layer close to the chip, and the outer lens material is epoxy resin, PC, PMMA, etc. However, actual applications show that when epoxy resin, PC, and PMMA are used as lens materials, in addition to the obvious lack of aging resistance, there will also be incompatibility with the interface of the inner packaging material, which will cause the luminous efficiency of LED devices to drop sharply after high and low temperature cycle experiments.
Studies have shown that the use of silicone-modified epoxy resin as packaging material can improve the toughness and high and low temperature resistance of the packaging material, and reduce its shrinkage rate and thermal expansion coefficient. There are literature reports that the mixture of addition silicone and epoxy resin is used as a packaging material. The mixture of polyorganosiloxane containing vinyl Si-OH group and epoxy resin with specific structure is used as the base polymer, and a crosslinking agent, catalyst, and diluent are added to prepare the packaging material for LED packaging. It does not change color after heat resistance test, and there is no peeling and cracking phenomenon in -40~120℃ hot and cold shock. The LED luminous efficiency is high. There are also reports on the mixed packaging of epoxy-modified polyorganosiloxane and epoxy compounds. The packaging material prepared by mixing epoxy-modified polyorganosiloxane with fat or alicyclic epoxy compounds and using anhydride as a curing agent has the characteristics of resistance to UV light aging, resistance to hot and cold shock, high transparency, high hardness, and good adhesion to the substrate. It is very suitable for the packaging of blue and white LEDs with wavelength emission peaks below 500nm. LED packaging materials made of packaging resins with specific structures and polysiloxanes can improve the heat resistance and UV light aging resistance of epoxy resins, and can also improve the adhesion and surface adhesion of silicone materials. It is a development approach worthy of attention.
Shin-Etsu Chemical Co., Ltd. of Japan adds vinyl silicone resin containing silanol, hydrogen silicone oil and a small amount of silicone elastomer to epoxy resin, uses platinum catalyst to catalyze the silylation reaction, and uses alkoxy or acyl or silanol aluminum compounds as epoxy curing agents. After injection molding, the LED packaging material with a refractive index of up to 1.41-1.53, a Shore hardness of 40-70 degrees, no dust absorption, low modulus, and low shrinkage is obtained. It will not crack after 1000 times of -40℃/120℃ hot and cold shock.
GE Company of the United States uses phenyltrichlorosilane, methyltrichlorosilane and dimethyldichlorosilane for co-hydrolysis and condensation to produce hydroxy silicone resin; then it is blended with silicone-modified epoxy resin, methylhexahydrophthalic anhydride is used as a curing agent, stannous octoate is used as a curing catalyst, and heated and vulcanized to obtain a packaging material with a refractive index of 1.53. After the material is irradiated with light waves of 380nm for 500h in an artificial aging machine or irradiated with ultraviolet light of 400~450nm for 500h at 150℃, the transmittance is still as high as over 80% (sample thickness 5mm).
In order to improve the heat resistance and thermal conductivity of LED packaging materials, inorganic fillers with a particle size of less than 400mm are often added, such as quartz powder, single crystal silicon, aluminum powder, zinc powder, glass fiber, etc. H.Ito et al. added silica with a particle size of 5-40nm and spherical glass powder with a particle size of 5-100nm to silicone-modified epoxy resin. After vulcanization and molding, the light transmittance of the material can reach 95.7% (25℃), the refractive index is 1.53-1.56 (sample thickness 1mm, wavelength 589.3nm), the linear expansion coefficient is about 10 ...
2.2 Modified silicone resin packaging material
Although the performance of epoxy resin encapsulants can be improved by silicone modification, the molecular structure of silicone-modified epoxy resin contains epoxy groups. As LED encapsulants, they still have disadvantages such as poor radiation resistance and easy yellowing, making it difficult to meet the technical requirements of power LED encapsulation. The optical clarity and thermal stability of silicone materials play an important role in the application of high-brightness LEDs and high reliability. Silicone materials are rapidly replacing epoxy resins and other materials. We provide a wide range of potting materials, lens materials, adhesives, sealants and protective coating products for various LED applications.
Currently, there are two types of silicone sealing materials on the market: high refractive index type and ordinary refractive index type silicone materials, including gel, silicone rubber and modified silicone resin. Ordinary refractive index (about 1.41) silicone is mainly dimethylsiloxane, while high refractive index (about 1.53) is mainly monophenylmethoxyethane. High refractive index silicone materials and silicone resin materials have become the research and product sales hotspots of several large foreign companies producing silicone products. Among the reported high refractive index silicone material systems, the highest refractive index of silicone materials that can be used for LED packaging has reached 1.57.
At present, the mainstream suppliers of silicone LED packaging materials on the market are Shin-Etsu of Japan, Dow Corning of the United States, Momentive and Nusil Technolong. They continue to launch silicone rubber and silicone resin products with a refractive index of more than 1.50. Among them, the two-component resin SR2710 produced by Dow Corning of the United States is hard and a transparent resin for LED components. It has a high refractive index and excellent luminous transparency. The materials used for LED packaging in Dow Corning's products also include transparent packaging materials such as OE-6336 and JCR6175. The "Addition curing silincone resin composition" applied by Shin-Et-Su Chemical Company of Japan uses three siloxanes with different functional groups to prepare a silicone resin product with high transparency, good tensile strength, good elasticity and hardness. Some research reports include: K1 Miyoshi and T. Goto et al. used a chlorosilane co-hydrolysis condensation process to prepare a vinyl silicone resin, and then vulcanized it with a hydrogen-containing silicone oil containing phenyl siloxane chain segments under a platinum catalyst to obtain an LED packaging material. The refractive index of the material can reach 1.51, the Shore D hardness is 75~85 degrees, the bending strength is 95~135MPa, the tensile strength is 5.4 MPa, and the transmittance is reduced from 95% to 92% after 500h of ultraviolet radiation. And the shrinkage rate of this type of silicone material can be reduced by increasing the mass fraction of phenyl in the packaging material, and its resistance to cold and hot cycle impact, excellent mechanical properties and bonding properties can be improved. T.Shiobara et al. used addition liquid silicone rubber for injection molding at 165℃ to obtain a packaging material with a shrinkage rate of 3.37%, a shrinkage ratio of only 0.04, and a refractive index of 1.50~1.60 (wavelength 400nm). E.Tabei et al. even obtained an LED packaging material with a Shore D hardness of up to 50 degrees, an elastic modulus of 350~1500MPa, and a transmittance of 88%~92% (wavelength 400nm sample thickness 4mm). Adding an appropriate amount of inorganic filler to the addition type liquid silicone rubber can improve the heat resistance and radiation resistance of the material. The obtained LED packaging material is vulcanized for 2~5h at a certain temperature, and the production cycle is relatively long. LDBoardman et al. used D4 and 1,3-divinyl-1,1,3,3,-tetramethyldisiloxane to perform ring-opening polymerization under the catalysis of concentrated sulfuric acid to obtain vinyl silicone oil, and then added hydrogen-containing silicone oil, platinum catalyst and photosensitizer in proportion. After mixing evenly, it can be completely cured by irradiating with visible light or ultraviolet light for 15~20min to obtain LED packaging materials with better performance. In the preparation process of organic silicon LED packaging materials, platinum catalysts are generally required, and the commonly used platinum catalysts will turn yellow after being placed for a period of time. Continuing to use will affect the light transmittance of LED packaging materials. In order to overcome this shortcoming, K. Tomoko et al. developed a platinum catalyst with organosiloxane as ligand that is not easy to change color, namely 1,3-dimethyl-1,3-divinylsiloxane platinum complex. Using this catalyst to catalyze the vulcanization molding of addition silicone rubber, LED packaging materials with a refractive index higher than 1.50 and a transmittance of 92% to 100% can be obtained.
From the current market point of view, the amount of addition type phenyl silicone resin encapsulation material in silicone encapsulation material has a significant increasing trend. Silicone resin has good formability before curing. After curing, it has the characteristics of high transparency, refractive index, hardness and strength. After the introduction of difunctional siloxane segments into the molecular structure of silicone resin, it has moderate elasticity, is not easy to crack, and has improved impact resistance. It can replace transparent epoxy resin as an encapsulation material for blue and white LEDs and replace acrylate and polycarbonate for LED lens materials. The number of chain segments of difunctional siloxane segments in this type of silicone resin molecule is 20~100; the ratio of trifunctional siloxane segments to difunctional siloxane segments and olefin-containing siloxane segments is 70~28:70~20:10~2; it can be obtained by co-hydrolysis and polycondensation of phenyltrichlorosilane, methylvinyldichlorosilane and difunctional siloxane oligomers. In addition, there are UV-curable silicone encapsulation materials, which are transparent, heat-resistant, and do not change color or crack during use. They can replace epoxy resins for the encapsulation of white power LEDs. The main component of the encapsulation material is composed of a photoinitiator of an acrylate-based polysiloxane, and may also be composed of MA segments, M segments, and Q segments, or MA-D segments, D segments, and T segments. These polysiloxanes can be used alone or in combination. The photoinitiator can be any photoinitiator with an acrylic functional group, such as 2,2-dihexyloxyacetophenone, methyl ketone, etc., and can be used in combination with a free radical initiator. In addition to the above components, reactive diluents of other components can be used according to the requirements of use.
It is not difficult to see from the above high-refractive index silicone materials for LED packaging that they all selected phenyl-containing polysiloxanes when selecting the base polymer. At present, phenyl-containing polysiloxanes prepared abroad can only be used to produce low-end and medium-end products with low performance requirements, while high-performance phenyl polysiloxanes still need to rely on imports. At present, phenyl monomer siloxanes cannot be mass-produced in China (Jiangsu Hongda Chemical and Zhejiang Quzhou Ruilijie Co., Ltd. are introducing Russian technology to prepare for mass production of phenyl monomers). It is for this reason that although there are not many reports on high-refractive index silicon materials in China, some progress has been gradually made.
Professor Zhang Zhijie of the Institute of Chemistry of the Chinese Academy of Sciences has prepared phenyl vinyl silicone oil with a refractive index of 1.56 in the laboratory; Professor Lai Guoqiao of Hangzhou Normal University and others used methyl hydrogen cyclosiloxane and octamethylcyclotetrasiloxane, methylphenyl mixture and other cyclosiloxanes, in toluene solvent, 40℃~80℃, catalyzed by cation exchange resin, and terminated with tetramethyldihydrogen disiloxane to obtain clear and transparent methylphenyl hydrogen silicone oil, with a refractive index of 1.39~1.51 (25℃), but it is not the silicone and silicone resin products required for LED packaging. In 2005, with the support of the "863 Program", Beijing Kehua New Materials Technology Co., Ltd. and the Institute of Chemistry of the Chinese Academy of Sciences successfully developed an organic silicon epoxy resin composition suitable for LED lens materials with independent intellectual property rights. Its UV resistance and thermal aging performance are much better than other LED lens materials except silicone resin, and the compatibility problem with the silicone interface has been solved, but its refractive index is low, about 1.47. Recently, Chen Shigang and others from Shenzhen Kejunchi Technology Co., Ltd. used a mixture of silicone resin and silicone oil to produce an addition reaction under the condition of a catalyst to obtain a colorless and transparent silicone packaging material with a transmittance of up to 98%. When applied to high-power white light LEDs, the measured luminous flux of the white light LED can reach 42.65lm, achieving a good application effect.
3. Conclusion
Undoubtedly, silicone encapsulation materials are an ideal choice to meet the requirements of LED encapsulation. Silicone materials are rapidly replacing epoxy resins and other organic materials, providing a wide range of potting materials, lens materials, adhesives, sealants and protective coating products for various LED applications. However, with the rapid development of the LED industry, the need for diversified development in brightness, use, packaging process, design, etc. has created a demand for encapsulation materials with different hardness and higher refractive index. At the same time, in order to ensure the reliability after packaging, it is also very important to select the right hardness and adhesive materials. At present, the main research focus of silicone materials for LED encapsulation should be on improving the refractive index, thermal conductivity, mechanical strength and reducing thermal expansion rate of the materials, which will also be a very severe challenge for silicone manufacturing.
Previous article:Analysis of blue and green chips used in LED displays
Next article:Evaluation of key technical parameters of LED downlights (Part 1)
Recommended ReadingLatest update time:2024-11-16 19:34
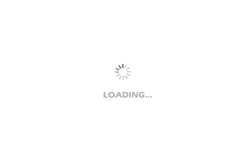
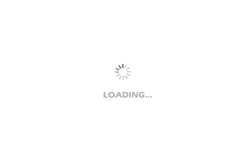
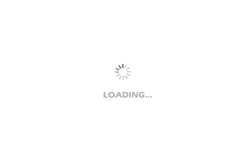
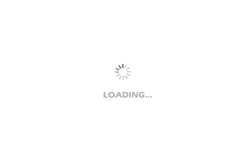
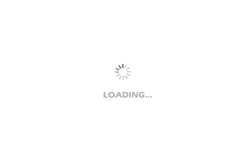
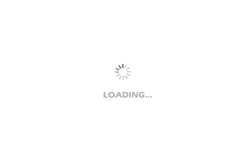
- Popular Resources
- Popular amplifiers
- MathWorks and NXP Collaborate to Launch Model-Based Design Toolbox for Battery Management Systems
- STMicroelectronics' advanced galvanically isolated gate driver STGAP3S provides flexible protection for IGBTs and SiC MOSFETs
- New diaphragm-free solid-state lithium battery technology is launched: the distance between the positive and negative electrodes is less than 0.000001 meters
- [“Source” Observe the Autumn Series] Application and testing of the next generation of semiconductor gallium oxide device photodetectors
- 采用自主设计封装,绝缘电阻显著提高!ROHM开发出更高电压xEV系统的SiC肖特基势垒二极管
- Will GaN replace SiC? PI's disruptive 1700V InnoMux2 is here to demonstrate
- From Isolation to the Third and a Half Generation: Understanding Naxinwei's Gate Driver IC in One Article
- The appeal of 48 V technology: importance, benefits and key factors in system-level applications
- Important breakthrough in recycling of used lithium-ion batteries
- Innolux's intelligent steer-by-wire solution makes cars smarter and safer
- 8051 MCU - Parity Check
- How to efficiently balance the sensitivity of tactile sensing interfaces
- What should I do if the servo motor shakes? What causes the servo motor to shake quickly?
- 【Brushless Motor】Analysis of three-phase BLDC motor and sharing of two popular development boards
- Midea Industrial Technology's subsidiaries Clou Electronics and Hekang New Energy jointly appeared at the Munich Battery Energy Storage Exhibition and Solar Energy Exhibition
- Guoxin Sichen | Application of ferroelectric memory PB85RS2MC in power battery management, with a capacity of 2M
- Analysis of common faults of frequency converter
- In a head-on competition with Qualcomm, what kind of cockpit products has Intel come up with?
- Dalian Rongke's all-vanadium liquid flow battery energy storage equipment industrialization project has entered the sprint stage before production
- Allegro MicroSystems Introduces Advanced Magnetic and Inductive Position Sensing Solutions at Electronica 2024
- Car key in the left hand, liveness detection radar in the right hand, UWB is imperative for cars!
- After a decade of rapid development, domestic CIS has entered the market
- Aegis Dagger Battery + Thor EM-i Super Hybrid, Geely New Energy has thrown out two "king bombs"
- A brief discussion on functional safety - fault, error, and failure
- In the smart car 2.0 cycle, these core industry chains are facing major opportunities!
- The United States and Japan are developing new batteries. CATL faces challenges? How should China's new energy battery industry respond?
- Murata launches high-precision 6-axis inertial sensor for automobiles
- Ford patents pre-charge alarm to help save costs and respond to emergencies
- New real-time microcontroller system from Texas Instruments enables smarter processing in automotive and industrial applications
- Can stm32 separate the kernel from the application (using dynamic link libraries?)
- [CY8CKIT-149 PSoC 4100S Review] + Unboxing
- [NUCLEO-L452RE Review] + Serial Communication and Component Control (and Final Report)
- Why does LSM6DSOX INT2 remain high after triggering the interrupt?
- How to use ftp to update demo
- [NXP Rapid IoT Review] + Summary of Bluetooth protocol stack usage
- EEWORLD University New Course Express Issue 2: Covering multiple fields such as robots, algorithms, black technology, CNC, FPGA, etc.
- Low-power electronic load for fast load transient testing
- PS1 Modchip using micropython
- IMX283 can't be sent out