Introduction
For low voltage converter applications up to about 25 A, a single-phase buck controller works very well. Above that, power dissipation and efficiency start to become an issue. A better approach is to use a multiphase buck controller. This article will briefly compare the benefits of using a multiphase buck converter versus a single-phase converter and show what value a multiphase buck converter can provide when the circuit is implemented.
Figure 1 shows a two-phase circuit. The interleaving of the phases is clearly visible in the waveforms of the circuit (Figure 2). This interleaving reduces input and output ripple currents. It also reduces hot spots on the PCB or a particular component. In fact, the two-phase buck converter reduces the RMS-current power dissipation of the FETs and inductors by half. Interleaving the phases also reduces conduction losses.
Figure 1 Two-phase buck converter
Figure 2 Node waveforms of phases 1 and 2
Output filter considerations
The output filter requirements for a multiphase implementation are reduced due to the lower power stage current per phase. For a 40-A two-phase solution, the average current delivered to each inductor is only 20A. Compared to a 40-A single-phase approach, the inductor size and size can be significantly reduced due to the lower average and saturation currents.
Output Ripple Voltage
Ripple current cancellation in the output filter stage results in lower output capacitor ripple voltage than a single-phase converter. This is why multiphase converters are preferred. Equations 1 and 2 calculate the percentage of ripple current canceled in each inductor.
m = D x Phases (1)
and
Where D is the duty cycle, IRip_norm is the normalized ripple current as a function of D, and mp is an integer of m. Figure 3 shows a graph of these equations. For example, using 2 phases at a 20% duty cycle (D) reduces the ripple current by 25%. The amount of ripple voltage that the capacitor must withstand can be calculated by multiplying the ripple current by the equivalent series resistance of the capacitor. Clearly, both the maximum current and voltage requirements are reduced.
Figure 3 Normalized capacitor ripple current as a function of duty cycle
Figure 4 shows the simulation results for a two-phase buck converter at 25% duty cycle. The inductor ripple current is 2.2A, but the output capacitor current is only 1.5A due to ripple current cancellation. When using two phases at 50% duty cycle, there is no ripple current at all in the capacitor.
Figure 4 Inductor ripple current cancellation when D=25%
Load transient performance
Load transient performance is improved due to the reduced energy stored in each output inductor. The reduced ripple voltage due to current cancellation helps to achieve minimal output voltage overshoot and undershoot because many cycles are completed before the loop responds. The lower the ripple current, the less interference.
Input RMS Ripple Current Cancellation
If the input wires connecting the converter are inductive, the input capacitors will supply all the input current to the buck converter. Careful selection of these capacitors is required to meet the RMS ripple current requirements and ensure that they do not overheat. Obviously, for a single-phase converter with a 50% duty cycle, the limiting input RMS ripple current is typically fixed at 50% of the output current. Figure 5 and Equation 3 show that when using a two-phase solution, the limiting RMS ripple current occurs at 25% and 75% duty cycles, which is only 25% of the output current.
The value of a multiphase solution is more clear than a single-phase solution. Smaller capacitors are needed to meet the RMS ripple current requirements of the buck stage.
Figure 5. Normalized input RMS ripple current as a function of duty cycle.
The
LM3754 high power density evaluation board is powered by a 12-V input supply, providing 12V at 40A. The evaluation board measures 2 × 2 inches, and the components occupy an area of 1.4 × 1.3 inches. The switching frequency of each phase is set to 300kHz. Table 1 summarizes these and other operating conditions. The components are placed on a 4-layer board with 1-ounce copper on the layer. There are also pins on the board for remote sensing and another pin for output voltage margin.
Table 1 LM3754 Evaluation Board Operating Conditions
Input Voltage 10.8 to 13.2 V
Output Voltage 1.2 V ± 1%
Output Current 40 A (max)
Switching Frequency 300 kHz
Module Volume 2 × 2 Dimensions
Circuit Area 1.4 × 1.3 Dimensions
Module Height 0.5 Dimensions
Airflow 200 LFM
Number of Phases 2
The LM3754 evaluation board is designed to operate in a high power density configuration, so it utilizes optimized input capacitors that require lower RMS ripple current. In addition, the evaluation board also has lower ripple voltage and higher transient performance. The board layout described in the LM3754 application note should be followed as closely as possible. However, if this layout cannot be followed, pay close attention to the above considerations. Now, we will also explain some other considerations to you, followed by the test results of the test board using the LM3754. Figure 6-11 on pages 12-13 shows these results. These results are what you need to get, or what you need to improve when making the necessary modifications.
Figure 6 12-V input efficiency curve
Board Layout Considerations
High current conductors require sufficient copper to minimize voltage drop and temperature rise. A general guideline is a minimum of 7 mils per ampere for 2 oz copper and 14 mils per ampere for 1 oz copper on internal layers. The input capacitors for each phase should be placed as close as possible to the top MOSFET drain and bottom MOSFET source to ensure minimum ground "bounce".
Signal components connected to the IC
All small signal components connected to the IC should be placed as close to the IC as possible. VREF and VCC coupling capacitors should also be placed as close to the IC as possible. The signal ground (SGND) should be configured to ensure that there is a low impedance path from the signal component ground to the IC ground.
SGND and PGND connections
Good layout practices include a dedicated ground plane; dedicate as much of the board as possible to inner layer 2 as a ground plane. Vias and signal traces should be laid out macroscopically to avoid high impedance points that could pinch off wide copper areas. Keep the power ground (PGND) and SGND separate, connecting them only on the ground plane (inner layer 2).
Gate Drive
The designer should ensure that the bidirectional differential pair wires from the high gate output to and from the top MOSFET gate are connected, which is the switching node. The distance between the control and MOSFET should be as short as possible. The layout of the LG and GND pins should follow the same procedure as when laying out the low side MOSFET wires.
Differential pair routing is also required from the CSM and CS2 pins to the RC network across the output inductor. Note the layout in Reference 1, where the filter capacitors are split into two capacitors for better noise rejection—one placed next to the inductor and the other close to the IC. Close to the switch node, the effective length of these sense lines is shorter. If possible, they should be shielded with a ground plane.
Minimize Switch Nodes
The general rule is to make the switch node area as small as possible, but still be able to carry high currents, so the switch nodes are on multiple layers. Since this small evaluation board can be folded over itself from input to output, the switch nodes are on the outer layers, and the IC is directly below the switch nodes. Therefore, it is necessary to keep the switch nodes away from the sense lines, and also away from the IC. In this way, the switch nodes are placed properly, outward toward the edge of the board.
Conclusion
There are many benefits to using multiphase buck converters, such as high efficiency due to low transition losses, low output ripple voltage, high transient performance, and lower input capacitor ripple current rating requirements. Some examples of multiphase buck converters that can provide you with these benefits include the LM3754, LM5119, and LM25119 series.
Figure 7 12-V input power consumption
Figure 8 Switching node voltage
Figure 9 Output voltage ripple
Figure 10 Transient response: 10-A load step, 20 µs (overshoot/undershoot approximately 27 mV)
Figure 11 40-A load 1.2-V output Vout startup diagram
References
“LM3753/54 Evaluation Board” by Robert Sheehan and Michael Null, National Semiconductor, published in the December 2009 online edition of Application Notes 2021, available for download at: http://www.national.com/an/AN/AN-2021.pdf
Previous article:Comparison of the main photovoltaic power generation technologies
Next article:Energy-saving control system of locomotive ventilator based on P87C591
Recommended ReadingLatest update time:2024-11-16 21:54
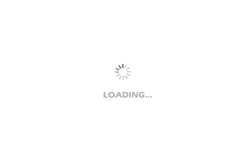
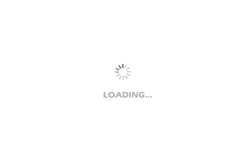
- Popular Resources
- Popular amplifiers
-
Wireless Sensor Network Technology and Applications (Edited by Mou Si, Yin Hong, and Su Xing)
-
Principles and Key Technologies of Lithium-ion Batteries (Edited by Huang Kelong, Wang Zhaoxiang and Liu Suqin)
-
Analog Engineer\'s Pocket Reference TI Chinese Edition
-
TI\'s switching power supply EMI conduction solution
- MathWorks and NXP Collaborate to Launch Model-Based Design Toolbox for Battery Management Systems
- STMicroelectronics' advanced galvanically isolated gate driver STGAP3S provides flexible protection for IGBTs and SiC MOSFETs
- New diaphragm-free solid-state lithium battery technology is launched: the distance between the positive and negative electrodes is less than 0.000001 meters
- [“Source” Observe the Autumn Series] Application and testing of the next generation of semiconductor gallium oxide device photodetectors
- 采用自主设计封装,绝缘电阻显著提高!ROHM开发出更高电压xEV系统的SiC肖特基势垒二极管
- Will GaN replace SiC? PI's disruptive 1700V InnoMux2 is here to demonstrate
- From Isolation to the Third and a Half Generation: Understanding Naxinwei's Gate Driver IC in One Article
- The appeal of 48 V technology: importance, benefits and key factors in system-level applications
- Important breakthrough in recycling of used lithium-ion batteries
- Innolux's intelligent steer-by-wire solution makes cars smarter and safer
- 8051 MCU - Parity Check
- How to efficiently balance the sensitivity of tactile sensing interfaces
- What should I do if the servo motor shakes? What causes the servo motor to shake quickly?
- 【Brushless Motor】Analysis of three-phase BLDC motor and sharing of two popular development boards
- Midea Industrial Technology's subsidiaries Clou Electronics and Hekang New Energy jointly appeared at the Munich Battery Energy Storage Exhibition and Solar Energy Exhibition
- Guoxin Sichen | Application of ferroelectric memory PB85RS2MC in power battery management, with a capacity of 2M
- Analysis of common faults of frequency converter
- In a head-on competition with Qualcomm, what kind of cockpit products has Intel come up with?
- Dalian Rongke's all-vanadium liquid flow battery energy storage equipment industrialization project has entered the sprint stage before production
- Allegro MicroSystems Introduces Advanced Magnetic and Inductive Position Sensing Solutions at Electronica 2024
- Car key in the left hand, liveness detection radar in the right hand, UWB is imperative for cars!
- After a decade of rapid development, domestic CIS has entered the market
- Aegis Dagger Battery + Thor EM-i Super Hybrid, Geely New Energy has thrown out two "king bombs"
- A brief discussion on functional safety - fault, error, and failure
- In the smart car 2.0 cycle, these core industry chains are facing major opportunities!
- The United States and Japan are developing new batteries. CATL faces challenges? How should China's new energy battery industry respond?
- Murata launches high-precision 6-axis inertial sensor for automobiles
- Ford patents pre-charge alarm to help save costs and respond to emergencies
- New real-time microcontroller system from Texas Instruments enables smarter processing in automotive and industrial applications
- Share some difficult problems with the LM25116EN chip
- [RVB2601 Creative Application Development] Dynamically loading MBRE Postscript
- Distance of ESD tip discharge needle
- Bone Vibration Sensor LIS25BA-Anti-Wind Noise Example
- SensorTile.box Trial (3) Expert Mode Trial
- Introduction to CEDV Electricity Calculation Method
- [Anxinke UWB indoor positioning module NodeMCU-BU01] 04: Test results and problems of connecting to OLED screen
- Live picture broadcast at 1pm today|STM32 National Seminar Beijing Station, you can start the wonderful moments!
- Design of scalable modular multiplication operator with base 4.pdf
- Looking for a cost-effective security encryption chip!!!