Switching power supplies have become increasingly popular due to their small size, light weight, and high efficiency. MOSFET has become one of the most commonly used power switching devices in switching power supplies due to its fast switching speed, easy parallel connection, and low required driving power. The quality of the drive circuit directly affects the reliability and performance indicators of the switching power supply. The requirements for a good MOSFET drive circuit are:
(1) When the switch is turned on, the drive circuit should be able to provide a sufficiently large charging current to quickly raise the voltage between the gate and source of the MOSFET to the required value, ensuring that the switch can be turned on quickly and there is no high-frequency oscillation on the rising edge;
(2) During the on-time of the switch tube, the driving circuit can ensure that the voltage between the gate and source of the MOSFET remains stable so that it can be turned on reliably;
(3) At the moment of shutdown, the drive circuit can provide a path with the lowest possible impedance for the rapid discharge of the MOSFET gate-source capacitance voltage, ensuring that the switch tube can be turned off quickly;
(4) During the shutdown period, the driving circuit should preferably provide a certain negative voltage to avoid interference and misleading conduction;
(5) In addition, the driving circuit structure is required to be simple and reliable, with low loss and preferably isolation.
This article introduces and discusses several simple and feasible MOSFET tube drive circuits used by the author in the development of switching power supplies.
Introduction and analysis of several MOSFET drive circuits
Non-isolated complementary drive circuit
Figure 1 (a) is a commonly used low-power drive circuit, which is simple, reliable and low-cost. It is suitable for low-power switching devices that do not require isolation. The drive circuit shown in Figure 1 (b) has a fast switching speed and strong driving ability. In order to prevent the two MOSFET tubes from directly connecting, a small resistor of 0.5 to 1Ω is usually connected in series for current limiting. This circuit is suitable for medium-power switching devices that do not require isolation. The structures of these two circuits are very simple.
Power MOSFET is a voltage-type control device. It will turn on as long as the voltage applied between the gate and the source exceeds its threshold voltage. Due to the existence of junction capacitance in MOSFET, the sudden rise of the voltage across the drain and source when it is turned off will generate interference voltage across the gate and source through the junction capacitance. The commonly used complementary drive circuit has a small turn-off loop impedance and a fast turn-off speed, but it cannot provide negative voltage, so its anti-interference performance is poor. In order to improve the anti-interference performance of the circuit, a circuit consisting of V1, V2, and R can be added to this drive circuit to generate a negative voltage. The circuit schematic is shown in Figure 2 (a).
When V1 is turned on, V2 is turned off, the gate and source of the upper tube of the two MOSFETs are discharged, and the gate and source of the lower tube are charged, that is, the upper tube is turned off and the lower tube is turned on, and the driven power tube is turned off; conversely, when V1 is turned off, V2 is turned on, the upper tube is turned on, and the lower tube is turned off, so that the driven tube is turned on. Because the gates and sources of the upper and lower tubes are discharged through different circuits, the circuit containing V2 will continue to exit saturation until it is turned off, so for S1, the turn-on is slower than the turn-off, and for S2, the turn-on is faster than the turn-off, so the heating degree of the two tubes is not exactly the same, and S1 heats more seriously than S2.
The disadvantage of this drive circuit is that it requires dual power supplies, and because the value of R cannot be too large, otherwise V1 will be deeply saturated and the shutdown speed will be affected, there will be a certain loss on R.
There is another similar circuit as shown in Figure 2 (b). The improvement is that it only needs a single power supply. The negative voltage generated is provided by a 5.2V voltage regulator. At the same time, the PNP tube is replaced by an NPN tube. In the two MOSFETs in this circuit, the upper tube generates less heat than the lower tube. Its working principle is the same as the driving circuit analyzed above, so it will not be repeated.
Isolated drive circuit
(1) Forward drive circuit
The circuit schematic is shown in Figure 3 (a), N3 is the demagnetization winding, S2 is the driven power tube. R2 is a damping resistor to prevent the voltage oscillation of the gate and source of the power tube. Because the transformer leakage inductance is small and considering the speed, R2 is generally small, so it is ignored in the analysis. Its working waveform is divided into two cases, one is the case where the demagnetization winding is turned on, see Figure 4 (a); the other is the case where the demagnetization winding is not turned on, see Figure 4 (b).
The equivalent circuit diagram is shown in Figure 3 (b). The secondary side of the pulse transformer is connected in parallel with a resistor R1, which serves as a dummy load for the forward converter to eliminate the oscillation of the output voltage during the shutdown period and misleading the turn-on, as shown in Figure 5. At the same time, it can also be used as an energy discharge circuit when the power MOSFET is turned off. The turn-on speed of the drive circuit is mainly related to the size of the driven S2 gate and source equivalent input capacitance, the speed of the drive signal of S1, and the current that S1 can provide. From simulation and analysis, it can be seen that the smaller the duty cycle D, the larger R1, and the larger L, the smaller the magnetizing current, the smaller the U1 value, and the slower the shutdown speed.
The circuit has the following advantages: ① The circuit structure is simple and reliable, and isolated driving is realized. ② Only a single power supply is needed to provide positive voltage when turned on and negative voltage when turned off. ③ When the duty cycle is fixed, through reasonable parameter design, this drive circuit also has a faster switching speed. The disadvantages of this circuit are: First, since the secondary side of the isolation transformer requires a dummy load to prevent oscillation, the circuit loss is large; second, when the duty cycle changes, the turn-off speed changes more. When the pulse width is narrow, the turn-off speed of the MOSFET gate slows down due to the reduction of stored energy. Table 1 shows the changes in the turn-off time toff (the time it takes for the drive voltage to drop from 10 volts to 0 volts) at different duty cycles.
(2) Complementary drive circuit with isolation transformer
As shown in Figure 6 (a), V1 and V2 work in a complementary manner, capacitor C plays the role of isolating DC, and T1 is a high-frequency, high-magnetic-rate magnetic ring or magnetic tank. The voltage on the isolation transformer is (1-D) Ui when it is turned on, and DUi when it is turned off. If the reliable conduction voltage of the main power tube S is 12V, the primary and secondary turns ratio N1/N2 of the isolation transformer is 12/(1-D)/Ui. In order to ensure the stability of the GS voltage during the conduction period, the C value can be slightly larger. The experimental waveform is shown in Figure 7 (a). This circuit has the following advantages:
①The circuit structure is relatively simple and reliable, and has electrical isolation. When the pulse width changes, the driver's shutdown capability will not change.
②This circuit only needs one power supply, that is, single power supply operation. The function of the DC blocking capacitor C can provide a negative voltage when turning off the driven tube, thereby accelerating the shutdown of the power tube and having a higher anti-interference ability.
Table 1 Variation of toff at different duty cycles
However, a major disadvantage of this circuit is that the amplitude of the output voltage will change with the change of the duty cycle. When D is small, the negative voltage is small, the anti-interference performance of the circuit becomes poor, and the forward voltage is high. It should be noted that its amplitude does not exceed the allowable voltage of the MOSFET gate. When D is greater than 0.5, the forward voltage of the driving voltage is less than its negative voltage. At this time, it should be noted that its negative voltage value does not exceed the allowable voltage of the MOSFET gate. Therefore, this circuit is more suitable for occasions where the duty cycle is fixed or the duty cycle range is not large and the duty cycle is less than 0.5.
6 (b) is a driving circuit suitable for duty cycle greater than 0.5, where Z2 is a voltage stabilizing diode. At this time, the negative voltage value of the secondary winding is relatively large, and the voltage stabilization value of Z2 is the required negative voltage value. The excess voltage drops on capacitor C2. The experimental waveform is shown in Figure 7 (b).
(3) Driving circuit composed of integrated chip UC3724/3725
The circuit configuration diagram is shown in Figure 8.
Among them, UC3724 is used to generate high-frequency carrier signal, and the carrier frequency is determined by capacitor CT and resistor RT. Generally, the carrier frequency is less than 600kHz, and high-frequency modulation waves are generated at both ends of pins 4 and 6. After being isolated by a high-frequency small magnetic ring transformer, they are sent to pins 7 and 8 of the UC3725 chip, and then demodulated by UC3725 to obtain the driving signal. There is a Schottky rectifier bridge inside UC3725, which simultaneously rectifies the high-frequency modulation waves of pins 7 and 8 into a DC voltage to provide the required power for driving.
Generally speaking, the higher the carrier frequency, the smaller the driving delay, but if it is too high, the anti-interference performance will be worse; the larger the magnetizing inductance of the isolation transformer, the smaller the magnetizing current, and the less heat UC3724 generates, but if it is too large, the number of turns will increase, resulting in a greater impact of parasitic parameters, which will also reduce the anti-interference ability. Therefore, according to experimental research, it is generally better to take a carrier frequency of (400-500) kHz for signals with a switching frequency less than 100kHz, and the transformer should use a high-frequency toroidal core with a higher magnetic permeability such as 5K, 7K, etc., and the primary magnetizing inductance should be about 1 millihenry. This drive circuit is only suitable for signal frequencies less than 100kHz. If the signal frequency is too high relative to the carrier frequency, the relative delay is too much, and the required driving power increases. The UC3724 and UC3725 chips will generate a lot of heat and have a high temperature rise. Therefore, a switching frequency of more than 100kHz is only suitable for MOSFETs with smaller pole capacitance. For situations where the switching frequency is less than 100kHz around 1kVA, it is a drive circuit with good performance. The circuit has the following characteristics: single power supply operation, isolation of control signal and drive, simple structure and small size, and is particularly suitable for occasions where the duty cycle changes unpredictably or the signal frequency also changes.
Conclusion
The several MOSFET drive circuits introduced in this article have the following advantages: simple and reliable structure; single power supply operation; suitable for small and medium power switching power supplies. The above circuits have been applied to the principle prototypes of actual switching power supplies of different powers and have been tested experimentally.
Previous article:Principle and maintenance of high frequency switching power supply system
Next article:Analysis of the single-chip TOP223 series switching power supply
Recommended ReadingLatest update time:2024-11-16 15:35
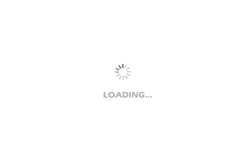
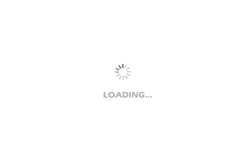
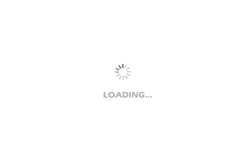
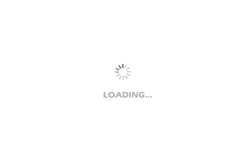
- Popular Resources
- Popular amplifiers
-
Optimization design of SGT_MOSFET peak oscillation in synchronous rectification circuit
-
Study on the Behavioral Model of Silicon Carbide MOSFET Power Module and EMI Prediction of Low-Voltage Auxiliary Power Supply
-
Theory and practice of small-size MOS device models for VLSI simulation
-
Power Electronics Technology 2nd Edition (Li Jie, Chao Xiaojie, Jia Weijuan, Yang Jiayi, Lai Wei)
- MathWorks and NXP Collaborate to Launch Model-Based Design Toolbox for Battery Management Systems
- STMicroelectronics' advanced galvanically isolated gate driver STGAP3S provides flexible protection for IGBTs and SiC MOSFETs
- New diaphragm-free solid-state lithium battery technology is launched: the distance between the positive and negative electrodes is less than 0.000001 meters
- [“Source” Observe the Autumn Series] Application and testing of the next generation of semiconductor gallium oxide device photodetectors
- 采用自主设计封装,绝缘电阻显著提高!ROHM开发出更高电压xEV系统的SiC肖特基势垒二极管
- Will GaN replace SiC? PI's disruptive 1700V InnoMux2 is here to demonstrate
- From Isolation to the Third and a Half Generation: Understanding Naxinwei's Gate Driver IC in One Article
- The appeal of 48 V technology: importance, benefits and key factors in system-level applications
- Important breakthrough in recycling of used lithium-ion batteries
- Innolux's intelligent steer-by-wire solution makes cars smarter and safer
- 8051 MCU - Parity Check
- How to efficiently balance the sensitivity of tactile sensing interfaces
- What should I do if the servo motor shakes? What causes the servo motor to shake quickly?
- 【Brushless Motor】Analysis of three-phase BLDC motor and sharing of two popular development boards
- Midea Industrial Technology's subsidiaries Clou Electronics and Hekang New Energy jointly appeared at the Munich Battery Energy Storage Exhibition and Solar Energy Exhibition
- Guoxin Sichen | Application of ferroelectric memory PB85RS2MC in power battery management, with a capacity of 2M
- Analysis of common faults of frequency converter
- In a head-on competition with Qualcomm, what kind of cockpit products has Intel come up with?
- Dalian Rongke's all-vanadium liquid flow battery energy storage equipment industrialization project has entered the sprint stage before production
- Allegro MicroSystems Introduces Advanced Magnetic and Inductive Position Sensing Solutions at Electronica 2024
- Car key in the left hand, liveness detection radar in the right hand, UWB is imperative for cars!
- After a decade of rapid development, domestic CIS has entered the market
- Aegis Dagger Battery + Thor EM-i Super Hybrid, Geely New Energy has thrown out two "king bombs"
- A brief discussion on functional safety - fault, error, and failure
- In the smart car 2.0 cycle, these core industry chains are facing major opportunities!
- The United States and Japan are developing new batteries. CATL faces challenges? How should China's new energy battery industry respond?
- Murata launches high-precision 6-axis inertial sensor for automobiles
- Ford patents pre-charge alarm to help save costs and respond to emergencies
- New real-time microcontroller system from Texas Instruments enables smarter processing in automotive and industrial applications
- MSP430 FLL - Frequency Locked Loop
- 530M power supply quality resources one-click download, limited time free points
- How to obtain a package in an existing PCB diagram
- msp430 library serial keyboard
- PSIM simulation software oscilloscope setting problem + measurement problem, how to set up the oscilloscope to see the output waveform?
- Design RF circuit boards, you need to know these tips!
- Talk to your boss about a pay raise
- How Tiny Data Converters Give You More Value in Smaller Size
- Industrial waste gas monitoring system based on ZigBee wireless sensor network
- Electric energy measurement solution based on C2000 built-in 12-bit ADC