Combining a high-side pre-FET driver and power FETs is an ideal solution for controlling automotive lighting.
The resistance of the tungsten filament in an incandescent light bulb can vary by more than a 1:10 ratio with temperature. To protect components from overheating and degradation over time, an electronic switch with programmable short-circuit and overcurrent regulation is extremely useful. Standard and re-settable fuses interrupt power to the load upon detection of an overcurrent condition and may take a variable amount of time to reset. An electronic switch can be programmed to react more predictably.
Fuse-based systems can only be set to a well-defined reset value and cannot accommodate the 10:1 current ratios that electronic solutions can. Electronic switches can be programmed to automatically retry periodically in the event of an overcurrent condition or to check if the fault has been corrected. At the same time, monitoring, detecting, and reporting the nature of the fault can help easily identify system problems.
The multi-channel pre-FET driver and external power FET concept provides system flexibility for optimizing load control power consumption and cost. Independent selection of power consumption and different FET resistances helps prevent interactions and system failures due to single channel failures compared to a fully integrated solution.
The pre-FET driver power switch combination allows the system to control the FET switching characteristics and handles any electromagnetic interference (EMI) issues when using external RC components on the gate drive output.
Load Controlled Pre-FET Driver and N-Channel Power FET Combination
A pre-FET driver (for example, TI's TPIC44H01) is used to control four different loads in the system. This combination can control resistive loads well through temperature coefficient. Typically, the load is connected on the low-voltage side, and the power FET is configured on the high-voltage side to power the load. Each channel can be controlled by a parallel input signal from a microcontroller or a serial programming register. In a parallel structure, a general-purpose I/O or timer-based output is used to control the load current.
The gate drive output is typically a constant current source and is drawn into the output to control the FET gate capacitance charge and discharge characteristics. An external resistor in series with the output limits the number of rise and fall times of the FET switch transitions. This effect keeps the slew rate under control and can also help reduce rapid current changes during the switching extremes that can increase electromagnetic interference (increasing switching losses and power dissipation). These outputs are internally controlled below the maximum output voltage of 17V to protect the external FET gate from source breakdown damage. Compared to an integrated solution, the combination of the pre-FET driver and the power FET can be configured to prevent dynamic and static faults in the application.
Dynamic fault threshold for inrush current
Incandescent lighting requires a dynamic fault threshold to compensate for high inrush currents and prevent false triggering of overcurrent conditions at the beginning of turn-on. The use of an RC network with a switch can set the threshold of this dynamic fault (see Figure 1). By using this approach, the short-circuit current can be optimized for different incandescent bulbs. The VPEAK voltage is set when the initial overcurrent threshold is set, and then decays when the resistor divider value set on the VCOMP terminal is a constant RC time constant. This variable overcurrent threshold waveform is generated by a parallel or serial input bit of the appropriate channel every time the gate goes from the "off" state to the "on" state.
Figure 1
When the particular channel is in the “off” state, the programmed VPEAK(X) value is reflected on VCOMP(X). If a particular channel is turned on, the reference voltage for over-current detection is dynamic and is represented by the internal VPEAK setting and the external component values at the VCOMP(X) terminal.
An overcurrent fault threshold expressed as a voltage is adjusted over time to compensate for changes in the bulb filament resistance (see Figure 2).
Figure 2
Fault detection and protection
Fault detection is critical for load protection in all systems. Being able to independently detect faults for short-circuit loads and overcurrent conditions in the "on" state and open-circuit loads in the "off" state for each channel will allow the system to react appropriately. This detection also allows the faulty channel to be isolated to avoid affecting other normal channels, especially when thermal interaction issues are involved.
"Open" state failure
To detect short-circuit loads on each channel, the external power FET supply voltage is monitored to ensure when the switch is fully "on" and when the voltage is set to a few positive voltages (typically 5V). If the short-circuit load occurs after the switch transition, the fault is asserted for longer than the fault mask time before the system reacts properly (including "turning off" the FET so that it does not exceed the safe operating area parameters). To prevent false fault reports during switch transitions, a de-glitch filter is activated to mask the fault when the transition time is exhausted. The de-glitch masking time can be programmed to compensate for all slew rate control implementations.
Overcurrent fault monitoring and reporting is flagged when the drain-source voltage on an external pin exceeds a programmed voltage level. This approach requires the FET resistor to be in the "on" state and requires all load current to produce the drain-source voltage. The detection of this fault is masked during a programmed period called the fault mask timer. If the fault persists for longer than the mask timer, the overcurrent fault is reported and the correct action is taken to "turn off" the FET. This arrangement prevents the FET from exceeding the maximum recommended junction temperature of the device.
When an over-current condition is detected, the FET can be protected by either “turning off” the device or activating an option setting that will automatically retry and “turn on” the FET at a low duty cycle. This allows the system to constantly check that the fault has been removed without destroying the FET. Figure 3 shows the schematic of this over-current detection protection.
Figure 3
"Closed" state failure
Monitoring for open load faults in the OFF state provides the system with information about the load integrity. Detection of open load faults for each channel is achieved by monitoring the supply voltage of the external power FET when the switch is fully in the OFF state. An internal supply activates a small constant current through the load to ground and biases the SRCx node below the open load detection threshold.
If an open load or high impedance is detected, a small constant current will bias the SRCx node above the open load detection threshold, thereby detecting the fault (see Figure 4).
Figure 4
Likewise, to prevent false fault reporting during switching transitions, a deglitch filter is activated during power transitions to mask faults. The deglitch masking time can be programmed to compensate for all slew rate control implementations. If the open load occurs after the switching transition, the fault is asserted longer than the fault masking time before the system takes the correct action. The correct action is to keep the FET in the “off” state.
In all systems, it is important to monitor the power supply line for overvoltage conditions and “turn off” the field effect transistor to prevent possible damage to the load and the FET (see Figure 5).
Figure 5
The combination of a pre-FET driver and a power FET can be used to drive a solenoid load. If no external protection is implemented when the gate is "off", damage to the power FET may occur. By recirculating the solenoid energy and installing a rectifier in the load, the FET can be protected. However, this may take some time to decay the load energy, so this method is not recommended in fast pulse width modulation (PWM) operation.
For fast "off", "actively" turning the power FET "on" requires the implementation of an active clamp. This dissipates the stored energy and quickly adds several watts of power to the FET in less than a millisecond. Alternatively, avalanche breakdown of the external power FET can be used to slowly dissipate the energy after "off", but this approach is not recommended for high frequency pulse width modulation (PWM) operation.
in conclusion
The high side pre-field FET driver and power FET combination is widely used to control loads such as incandescent bulbs, relay solenoids, and transmission solenoids for automotive electronics. This combination may also be used in industrial and commercial applications that require load control through serial bus communication or parallel input control. The ability to isolate each power FET from thermal interactions is very beneficial in situations where a single channel short circuit or thermal shutdown fault will not interrupt the function of other load control channels.
Previous article:MOSFET Selection Strategy in Synchronous Boost Converter Design
Next article:Impact of Size Reduction on Trench MOSFET Performance
Recommended ReadingLatest update time:2024-11-16 18:08
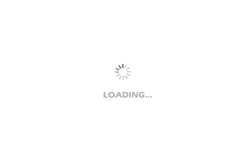
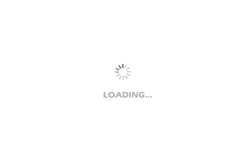
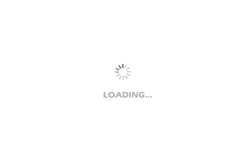
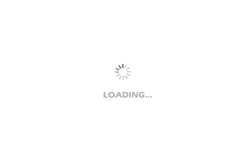
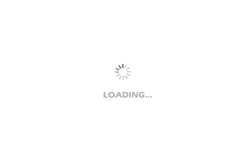
- Popular Resources
- Popular amplifiers
-
Virtualization Technology Practice Guide - High-efficiency and low-cost solutions for small and medium-sized enterprises (Wang Chunhai)
-
Optimization design of SGT_MOSFET peak oscillation in synchronous rectification circuit
-
Study on the Behavioral Model of Silicon Carbide MOSFET Power Module and EMI Prediction of Low-Voltage Auxiliary Power Supply
-
Theory and practice of small-size MOS device models for VLSI simulation
- MathWorks and NXP Collaborate to Launch Model-Based Design Toolbox for Battery Management Systems
- STMicroelectronics' advanced galvanically isolated gate driver STGAP3S provides flexible protection for IGBTs and SiC MOSFETs
- New diaphragm-free solid-state lithium battery technology is launched: the distance between the positive and negative electrodes is less than 0.000001 meters
- [“Source” Observe the Autumn Series] Application and testing of the next generation of semiconductor gallium oxide device photodetectors
- 采用自主设计封装,绝缘电阻显著提高!ROHM开发出更高电压xEV系统的SiC肖特基势垒二极管
- Will GaN replace SiC? PI's disruptive 1700V InnoMux2 is here to demonstrate
- From Isolation to the Third and a Half Generation: Understanding Naxinwei's Gate Driver IC in One Article
- The appeal of 48 V technology: importance, benefits and key factors in system-level applications
- Important breakthrough in recycling of used lithium-ion batteries
- Innolux's intelligent steer-by-wire solution makes cars smarter and safer
- 8051 MCU - Parity Check
- How to efficiently balance the sensitivity of tactile sensing interfaces
- What should I do if the servo motor shakes? What causes the servo motor to shake quickly?
- 【Brushless Motor】Analysis of three-phase BLDC motor and sharing of two popular development boards
- Midea Industrial Technology's subsidiaries Clou Electronics and Hekang New Energy jointly appeared at the Munich Battery Energy Storage Exhibition and Solar Energy Exhibition
- Guoxin Sichen | Application of ferroelectric memory PB85RS2MC in power battery management, with a capacity of 2M
- Analysis of common faults of frequency converter
- In a head-on competition with Qualcomm, what kind of cockpit products has Intel come up with?
- Dalian Rongke's all-vanadium liquid flow battery energy storage equipment industrialization project has entered the sprint stage before production
- Allegro MicroSystems Introduces Advanced Magnetic and Inductive Position Sensing Solutions at Electronica 2024
- Car key in the left hand, liveness detection radar in the right hand, UWB is imperative for cars!
- After a decade of rapid development, domestic CIS has entered the market
- Aegis Dagger Battery + Thor EM-i Super Hybrid, Geely New Energy has thrown out two "king bombs"
- A brief discussion on functional safety - fault, error, and failure
- In the smart car 2.0 cycle, these core industry chains are facing major opportunities!
- The United States and Japan are developing new batteries. CATL faces challenges? How should China's new energy battery industry respond?
- Murata launches high-precision 6-axis inertial sensor for automobiles
- Ford patents pre-charge alarm to help save costs and respond to emergencies
- New real-time microcontroller system from Texas Instruments enables smarter processing in automotive and industrial applications
- Senior Electronic Engineer (FPGA) Recruitment
- Should I choose a slow-blow or fast-blow fuse for the power module?
- Join [Micron VIP] and win a 200 yuan JD card!
- [GD32L233C-START Review] 8. TRNG True Random Number Generation
- How to set the grid of PCB more efficiently
- Input Considerations for SAR ADCs
- Enabling BLE in ESP-S3 using micropython
- The LM5118 buck-boost circuit has poor load capacity?
- GD32L233C Review: Unboxing
- What do you think about FAE career change?