The basic principle of LED energy-saving lamps is to convert AC power into DC power through a switching power module to supply power to the light-emitting diodes. Based on the basic principle and structural characteristics of LED energy-saving lamps, the US MET Laboratory has proposed a transitional testing solution at this stage: using the traditional energy-saving lamp US certification standard UL1993 (corresponding to Canadian standards CAN/CSA-C22.2No.0, CAN/CSA- C22.2No.74) and power module standards UL1310 or UL1012 (corresponding to Canadian standards CAN/CSA-C22.2No.107) to test and certify LED energy-saving lamps.
1. Technical points in testing
The following is an explanation of the key issues in the certification test of LED energy-saving lamps based on UL1993, UL1310 and UL1012 standards.
1. Materials
LED energy-saving lamps can be made into various shapes. For example, the fluorescent tube type LED energy-saving lamp has the same appearance as ordinary fluorescent tubes. The power module and the light-emitting diode are wrapped in a transparent polymer shell in the shape of a fluorescent tube. The transparent polymer shell plays the role of fire prevention and electric shock prevention in the product. According to the standard requirements, the shell material of the energy-saving lamp must reach the V-1 level or above, so the transparent polymer shell must be made of materials above the V-1 level. It should be noted that in order for the product shell to reach the required V-1 level, its thickness must be greater than or equal to the thickness required by the V-1 level of the raw material. The fireproof level and thickness requirements can be found on the UL yellow card of the raw material. In actual testing, it was found that in order to ensure the brightness of the LED lamp, manufacturers often make the transparent polymer shell very thin, which requires the testing engineer to pay attention to ensuring that the material reaches the thickness required by the fireproof level. Since different raw materials have different thickness requirements for the same fireproof level, some raw materials can meet the higher fireproof level requirements at a smaller thickness. It is recommended that manufacturers can choose suitable raw materials for product shells.
2. Drop test
According to product standards, the product must be tested for a drop that simulates a possible drop during actual use. The product must be dropped from a height of 0.91 meters onto a hardwood board. The product casing must not break to expose the dangerous live parts inside. Manufacturers must consider this strength requirement when selecting materials for product casings.
3. Dielectric strength
The transparent shell surrounds the power module inside, and the transparent shell material must meet the electrical strength requirements. According to the standard requirements, based on the North American voltage of 120 volts, the internal high-voltage live parts and the shell (covered with metal foil for testing) must be able to withstand the AC 1240 volt electrical strength test. In general, the product shell thickness of about 0.8 mm can meet the electrical strength test requirements.
4. Power module
The power module is an important part of the LED energy-saving lamp. The power module mainly adopts switching power supply technology. According to the different types of power modules, different standards can be considered for testing and certification. If the power module is a class II power supply, it can be tested and certified with UL1310. A class II power supply refers to a power supply that uses an isolated transformer, has an output voltage lower than 60 volts DC, and a current less than 150/Vmax amperes. For non-class II power supplies, UL1012 is used for testing and certification. The technical requirements of these two standards are very similar and can be referenced to each other. The internal power modules of most LED lamps use non-isolated parallel power supplies, and the output DC voltage of the power supply is also greater than 60 volts. Therefore, the UL1310 standard is not applicable, but UL1012 is applicable.
5. Insulation requirements
Since the internal space of LED energy-saving lamps is limited, attention should be paid to the insulation requirements between dangerous live parts and accessible metal parts during structural design.
Insulation can be space distance and creepage distance, or insulation sheet. According to standard requirements, the space distance between dangerous live parts and accessible metal parts should reach 3.2 mm, and the creepage distance should reach 6.4 mm. If the distance is not enough, an insulation sheet can be added as additional insulation. The thickness of the insulation sheet should be greater than 0.71 mm. If the thickness is less than 0.71 mm, the product should be able to withstand a 5000V high voltage test.
6. Temperature rise test
Temperature rise test is a must-do item in product safety testing. The standard has certain temperature rise limits for different components. During the product design stage, manufacturers should pay great attention to the heat dissipation of products, especially to certain components (such as insulation sheets, etc.).
If the components work under high temperature conditions for a long time, they are easy to be damaged, which may cause fire or electric shock. The power module inside the lamp is in a closed and narrow space, and the heat dissipation is limited. Therefore, when manufacturers select components, they should pay attention to selecting the appropriate specifications of the components to ensure that the components work under a certain margin, so as to avoid overheating caused by long-term operation under near full load conditions.
7. Structure
The power module of the LED energy-saving lamp is installed inside the shell, and the space is limited. In order to save space, some manufacturers solder the pin-type components on the PCB surface, which is unacceptable. These surface-welded pin-type components are likely to fall off due to cold soldering and other reasons, causing danger. Therefore, socket soldering should be used for these components as much as possible. If surface soldering is unavoidable, additional protection should be provided for this component by fixing it with glue or other methods.
8. Fault testing
Product failure testing is a crucial test item in product certification testing. This test item is to short-circuit or open-circuit some components on the line to simulate the failure that may occur during actual use, so as to evaluate the safety of the product under single fault conditions. In order to meet this safety requirement, when designing the product, it is necessary to consider adding a suitable fuse to the input end of the product to prevent overcurrent from causing fire hazards when the output is short-circuited or the internal components fail.
2. Factory Inspection
North American product certification requires factory inspection, which includes the first factory inspection and subsequent tracking inspection. If the factory is applying for North American product certification for the first time, the first factory inspection is required. The first factory inspection is mainly aimed at the factory's quality assurance system, requiring the factory to have a complete quality assurance system to ensure that the quality of the product is effectively supervised and guaranteed. If the factory has established a quality management system in accordance with ISO9000 standards and passed ISO9000 certification, it can basically meet the management system requirements of the first factory inspection. If the factory has not passed ISO9000 certification, it must have clear procedural documents in raw material procurement, incoming material inspection, inventory management, product design, engineering changes, production line testing, instrument calibration and complaint follow-up, and effectively implement them. Subsequent tracking inspections are mainly aimed at product structure inspections and production line product testing to ensure that the product structure produced by the production line is consistent with the certification sample and passes the relevant production line tests. After the product passes the test certification, the manufacturer must strictly produce the product according to the structure and component list of the certification sample, and any changes that may involve product safety must be notified to the certification body for evaluation. If necessary, retesting and report modification may be required. The product test report has clear requirements for the production line test of the product. Manufacturers must conduct relevant tests in accordance with the requirements, such as high voltage test, ground continuity test, etc.
Previous article:Seven new technology upgrades for the future development of LED backlight
Next article:Analysis of the top ten misunderstandings in the deployment of LED digital signage systems
Recommended ReadingLatest update time:2024-11-16 21:57
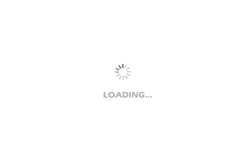
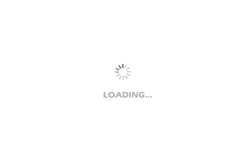
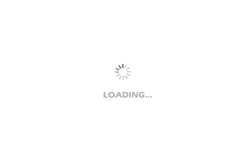
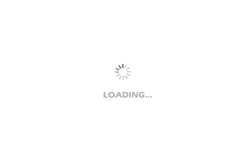
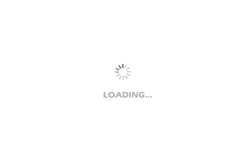
- Popular Resources
- Popular amplifiers
- MathWorks and NXP Collaborate to Launch Model-Based Design Toolbox for Battery Management Systems
- STMicroelectronics' advanced galvanically isolated gate driver STGAP3S provides flexible protection for IGBTs and SiC MOSFETs
- New diaphragm-free solid-state lithium battery technology is launched: the distance between the positive and negative electrodes is less than 0.000001 meters
- [“Source” Observe the Autumn Series] Application and testing of the next generation of semiconductor gallium oxide device photodetectors
- 采用自主设计封装,绝缘电阻显著提高!ROHM开发出更高电压xEV系统的SiC肖特基势垒二极管
- Will GaN replace SiC? PI's disruptive 1700V InnoMux2 is here to demonstrate
- From Isolation to the Third and a Half Generation: Understanding Naxinwei's Gate Driver IC in One Article
- The appeal of 48 V technology: importance, benefits and key factors in system-level applications
- Important breakthrough in recycling of used lithium-ion batteries
- Innolux's intelligent steer-by-wire solution makes cars smarter and safer
- 8051 MCU - Parity Check
- How to efficiently balance the sensitivity of tactile sensing interfaces
- What should I do if the servo motor shakes? What causes the servo motor to shake quickly?
- 【Brushless Motor】Analysis of three-phase BLDC motor and sharing of two popular development boards
- Midea Industrial Technology's subsidiaries Clou Electronics and Hekang New Energy jointly appeared at the Munich Battery Energy Storage Exhibition and Solar Energy Exhibition
- Guoxin Sichen | Application of ferroelectric memory PB85RS2MC in power battery management, with a capacity of 2M
- Analysis of common faults of frequency converter
- In a head-on competition with Qualcomm, what kind of cockpit products has Intel come up with?
- Dalian Rongke's all-vanadium liquid flow battery energy storage equipment industrialization project has entered the sprint stage before production
- Allegro MicroSystems Introduces Advanced Magnetic and Inductive Position Sensing Solutions at Electronica 2024
- Car key in the left hand, liveness detection radar in the right hand, UWB is imperative for cars!
- After a decade of rapid development, domestic CIS has entered the market
- Aegis Dagger Battery + Thor EM-i Super Hybrid, Geely New Energy has thrown out two "king bombs"
- A brief discussion on functional safety - fault, error, and failure
- In the smart car 2.0 cycle, these core industry chains are facing major opportunities!
- The United States and Japan are developing new batteries. CATL faces challenges? How should China's new energy battery industry respond?
- Murata launches high-precision 6-axis inertial sensor for automobiles
- Ford patents pre-charge alarm to help save costs and respond to emergencies
- New real-time microcontroller system from Texas Instruments enables smarter processing in automotive and industrial applications
- 122X32LCD screen printing CBG122032AL00 driver SED1520 screen data
- [Frequently Asked Questions about iMX6ULL Development] What are the requirements for the virtual machine when setting up the iMX6ULL development environment?
- Help with domestic chips that can replace stms105C6T6
- What is the function of this op amp circuit?
- If IAR is opened slowly and has high CPU usage, it is likely that you are using the Chinese path.
- Setup and Hold Time
- I was worried for a long time after looking at the program, and it turns out that the IO port multiplexing function in ch579 does not need to be set.
- The difference between using stm32 JTAG and SWD
- Why is it easy to crack the microcontroller?
- TI-84 Plus CE Graphing Calculator to Support CircuitPython