LED driver circuit design based on AX6066+A433
AX6066 is a converter with primary side feedback and output power between 12W and 65W. AX6066 is suitable for AC/DC power supply applications, which can meet the application requirements of low power consumption and high average working efficiency of AC line under no-load conditions. The chip can control the converter to work in discontinuous state mode. Discontinuous working mode provides a unique safety current limiting function, which is also insensitive to signal jitter on the AC line. Peak current modulation mode does not require slope compensation.
AX6066 works by driving the source of an external high-voltage power tube. This structure is called common-base, common-emitter (source-level) drive. It highlights the two advantages of fast startup and ensuring that the control chip is not connected to high voltage when there is no load. It has no effect on the normal operation of the converter with feedback flyback structure.
The feedback pin accepts current instead of voltage. Under no-load conditions, this design minimizes power dissipation on the primary side by avoiding external resistors that dissipate energy from current to voltage.
Under constant peak current and variable off-time modulation, the average efficiency of AX6066 is the highest between peak power and 22% of peak power. The internal modulation of AX6066 tends to keep its power constant between 22% and 100% of peak load, eliminating design difficulties and making the average efficiency of the converter reach energy star indicators.
Common-base, common-emitter biasing and startup
AX6066 uses a common base, common emitter drive and bias to control the high voltage power tube and provide initial bias at startup. This common base, common emitter structure realizes a universal gate control by controlling the switch connected between the ground and the source of the high voltage power tube at low voltage. There are the following key points to note:
1. A DC voltage should be applied to the gate of the external high-voltage power tube.
2. The external high-voltage power tube is driven by the source, not the gate.
3. All the current of the initial coil must pass through the internal low-voltage driver tube.
AX6066 integrates a 90mΩ low voltage switching field effect transistor and all associated current sensing and driving. The external high voltage power tube is forced to follow the internal fast low voltage driver tube. The drain and gate of the external high voltage driver tube will not affect the shutdown speed because the gate terminal is connected to an independent DC power supply. This common base and common emitter structure allows the external high voltage power tube to be turned off quickly, and the switching loss of the field effect transistor switch will also be reduced.
Feedback function
The modulation and operation mode of the AX6066 are controlled by the current received on the FB pin of the chip. The FB pin is usually used to feed back the output error signal to the modulator inside the chip. The AX6066 receives the current fed back from the FB pin through the internal current mirror and feeds it to the internal feedback processing module, and then to the frequency modulation and current modulation module. The voltage on the FB pin is constant at 0.7V. There must be an output coupling capacitor at the emitter of the transistor to filter out the noise on the AC line. The cutoff frequency of this filter should be at least 10 times the maximum switching frequency of the converter. A 100KΩ resistor is required between FB and GND to eliminate the noise effect of the reverse current flowing to the FB pin when the converter is overloaded and reset. The optocoupler feedback structure with a smaller current transfer ratio has better no-load working state than the feedback structure with a larger current transfer ratio relying on the secondary coil.
Modulation Mode
In normal working mode, the feedback current of FB pin controls the working mode of AX6066. FB feedback current controls the converter to have three working modes: frequency modulation mode, amplitude modulation, and green modulation.
The converter operates in frequency modulation with a larger power load (22% to 100% of the peak rated power). The peak current of the high-voltage power tube will reach its maximum programmable value, and the FB feedback current adjusts the output voltage by changing the operating frequency of the switch. The switching frequency is inversely proportional to the on-time of the switch. The switching frequency is modulated in the range from 30kHz (22% of the peak rated power) to 133kHz (100% of the peak rated power), the timing time is constant, and the rated current IDRV is also constant. The maximum programmable high-voltage power tube current IDRV, PK(max) is determined by the resistor connected to the CL pin.
The converter operates in AM mode at medium power levels (2.5% to 22% of peak rated power). The feedback current at the FB pin regulates the output voltage by modulating the rated current of the high-voltage power tube from 33% to 100% of the maximum programmable current value, and the operating frequency of the switch is fixed at around 30KHz. The AX6066 modulates the voltage on the CL pin from 3V to 1V to change the peak current.
The converter operates in green mode at a low load state (0% to 2.5% of peak rated power). The FB feedback current modulates the output voltage by using the FB current to generate a special trigger pulse. At this time, the peak current of the high-voltage power tube is 33% of the maximum programmable current value. The switching frequency including a trigger pulse is about 30kHz. The duration of the trigger process is modulated by the suppression force of the power supply and the feedback of the FB port. The AX6066 maintains energy conservation under low load and no load conditions by reducing the internal bias power consumption during the trigger process.
Primary Current Sensing
AX6066 uses current mirror technology to detect the initial current on the current modulator. All primary coil currents are connected to the external ground through the DRV pin and the driver power tube. The current on the driver power tube is proportional to the mirror image and controlled by the output of a PWM comparator compared with the CL current. At the beginning of each switching cycle, a shutdown pulse T of about 220ns is generated to the internal current limiter module, allowing the driver tube to open without false triggering limit on the main edge. The conventional capacitor discharge current will also appear in this circuit structure.
Zero Crossing Detection
In order to start the next switching cycle, the modulation needs to meet the following three conditions:
1. The previous switch on edge time must be equal to or greater than the processing time of the internal feedback block determined by the feedback current.
2. The previous switch on edge time must be longer than the minimum internal switching period of AX6066 (usually this period is 7.5us, corresponding to a frequency of 133kHz).
3. Quickly follow the ZCD zero-crossing voltage from high to low. The modulation time must be greater than the waiting time from the last zero-crossing detection to the next zero-crossing detection.
Each switching cycle is preceded by at least one zero detection on the ZCD pin. The modulation allows for damped oscillations between modulation pulses if the switching cycle needs to exceed the limit for damped oscillations and allows for longer pauses between modulation pulses under no-load operating conditions.
The switching frequency cannot exceed 133KHz in general. In order to keep the bulk voltage constant when it exceeds the minimum line voltage, the AX6066 will limit the maximum power by controlling the switching frequency.
The current in the AX6066 control inductor is always kept discontinuous. This design prevents current tailing during startup or short circuit conditions and facilitates maximum power control.
The voltage for zero current detection comes from the voltage on the auxiliary coil divided by a resistor, as shown in Figure 1 below. The phase of the voltage on the auxiliary coil is consistent with the phase of the voltage on the secondary output coil. The function of ZCD detection is to detect the demagnetization of the transformer. When the voltage of ZCD changes from high to low, there will be a 20mV ZCD threshold voltage. The voltage of the ZCD pin will be clamped at a drift voltage of -160mV inside the chip. A delay of 50ns to 200ns can be obtained by adding a capacitor CZCD connected to the ZCD port. This delay can keep the switch of the primary coil consistent with the trough of the voltage waveform of the initial coil.
Figure 1: Zero current detection function block diagram
In conventional AC line converter applications, the recommended peak power of AX6066 is 12W to 65W, and the rated voltage of the external high-voltage power tube is 600V. The power range depends on the application and the withstand voltage of the external high-voltage tube. Finally, the peak current of the initial coil is limited because this current must pass through the AX6066. The limitation of the peak current also limits the rated peak power of the initial coil. The peak power must be less than 65W, not the average power. The peak power is defined as the maximum power of the AX6066 in the modulation state.
The user can program the inductance of the initial coil, peak current, and maximum switching frequency of the AX2029 to obtain the power within the recommended power range. The formula for the maximum input power is given below.
The error sensitivity of IDRV(PK) is twice that of LM and fS(max) in terms of the impact on the accuracy of the regulation limit. If the load requires more power than the programmable power range, the output voltage will drop and the overload timing will be re-initialized.
Maximum timing and surge
The discontinuous operation mode of AX6066 provides an over-current protection when the voltage is low. AX6066 allows the user to program the maximum timing time to provide more protection.
In the case of an AC line voltage drop, if the load is large enough, the maximum timing action will cause the converter to act as if there is an overload condition. In the case of an AC line voltage drop, the MOT's function is to limit the timing of the initial coil switch, which determines the peak current within the primary coil power level range. The range of the MOT's resistance to ground determines the type of response of the AX6066 to a sustained overload error, whether it is a lockout or a shutdown restart, which is the same as the AC line voltage drop and surge.
External shutdown using the MOT pin
Many applications require an external method to shut down the power supply. This function can be achieved by shorting an NPN transistor between MOT and GND. For actual isolation applications, this NPN transistor is an independent optocoupler transistor.
For latch response in overcurrent or surge conditions,
Here,
For shutdown and restart response in overcurrent or surge conditions,
Here,
Overvoltage detection
AX6066 monitors the output voltage by sampling the voltage on the auxiliary coil. After the internal driver tube is turned off, the sampling time is fixed with a 1us delay. This allows the voltage on the auxiliary coil to be sampled at each lower limit transient. This same delay is used to lock the ZCD input to avoid unintentional zero-crossing detection. The ringing effect should be large enough to cross the zero-crossing detection threshold.
The output overvoltage threshold is set by the conversion ratio between the auxiliary coil and the secondary output coil and the voltage divider resistor on the ZCD pin. If the AX6066 detects an overvoltage state, the chip will enter the locked state. In order to resume startup, the VDD voltage of the AX6066 must be powered on again.
Secondary constant current sampling
A433 is a three-terminal programmable shunt voltage regulator diode, which can be programmed from VERF to 36V through two external resistors. The current sinking capability is 1mA~50mA, and it uses a low voltage reference of 196mV. It has a reliable full range temperature coefficient.
Its application advantages:
1. Fewer components and more optimized circuits
2. Low welding cost
3. No high power sampling resistor is required
4. Constant current accuracy is easier to control
5. With excellent transformer, the overall efficiency of the circuit is improved
Figure 2: 18W application circuit diagram based on AX6066+A433
Table 1: Test data of 18W (38V, 420MA) application solution based on AX6066+A433 (the first application solution with harmonics less than 10%)
Conclusion
In view of the growing development of the LED market, higher requirements for driver power supply. AX6066 has a new design concept, with full voltage input, low feedback voltage, high PFC, wide output voltage and current range, high output power, compatible with dimming, and high efficiency.
Previous article:How to choose LED light source
Next article:Thermal Analysis of LEAF Electric Vehicle LED Headlight
Recommended ReadingLatest update time:2024-11-16 19:42
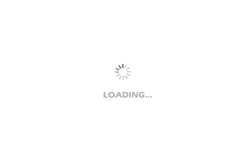
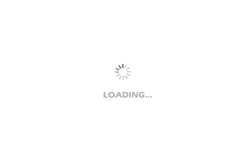
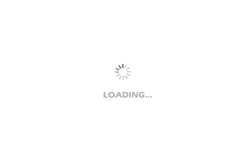
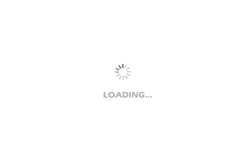
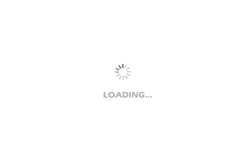
- MathWorks and NXP Collaborate to Launch Model-Based Design Toolbox for Battery Management Systems
- STMicroelectronics' advanced galvanically isolated gate driver STGAP3S provides flexible protection for IGBTs and SiC MOSFETs
- New diaphragm-free solid-state lithium battery technology is launched: the distance between the positive and negative electrodes is less than 0.000001 meters
- [“Source” Observe the Autumn Series] Application and testing of the next generation of semiconductor gallium oxide device photodetectors
- 采用自主设计封装,绝缘电阻显著提高!ROHM开发出更高电压xEV系统的SiC肖特基势垒二极管
- Will GaN replace SiC? PI's disruptive 1700V InnoMux2 is here to demonstrate
- From Isolation to the Third and a Half Generation: Understanding Naxinwei's Gate Driver IC in One Article
- The appeal of 48 V technology: importance, benefits and key factors in system-level applications
- Important breakthrough in recycling of used lithium-ion batteries
- Innolux's intelligent steer-by-wire solution makes cars smarter and safer
- 8051 MCU - Parity Check
- How to efficiently balance the sensitivity of tactile sensing interfaces
- What should I do if the servo motor shakes? What causes the servo motor to shake quickly?
- 【Brushless Motor】Analysis of three-phase BLDC motor and sharing of two popular development boards
- Midea Industrial Technology's subsidiaries Clou Electronics and Hekang New Energy jointly appeared at the Munich Battery Energy Storage Exhibition and Solar Energy Exhibition
- Guoxin Sichen | Application of ferroelectric memory PB85RS2MC in power battery management, with a capacity of 2M
- Analysis of common faults of frequency converter
- In a head-on competition with Qualcomm, what kind of cockpit products has Intel come up with?
- Dalian Rongke's all-vanadium liquid flow battery energy storage equipment industrialization project has entered the sprint stage before production
- Allegro MicroSystems Introduces Advanced Magnetic and Inductive Position Sensing Solutions at Electronica 2024
- Car key in the left hand, liveness detection radar in the right hand, UWB is imperative for cars!
- After a decade of rapid development, domestic CIS has entered the market
- Aegis Dagger Battery + Thor EM-i Super Hybrid, Geely New Energy has thrown out two "king bombs"
- A brief discussion on functional safety - fault, error, and failure
- In the smart car 2.0 cycle, these core industry chains are facing major opportunities!
- The United States and Japan are developing new batteries. CATL faces challenges? How should China's new energy battery industry respond?
- Murata launches high-precision 6-axis inertial sensor for automobiles
- Ford patents pre-charge alarm to help save costs and respond to emergencies
- New real-time microcontroller system from Texas Instruments enables smarter processing in automotive and industrial applications
- RSIC-V IDE MRS User Notes (V): Code Erasure Problem Before Debugging
- There are indeed many people who ask for money, and the most annoying ones are the brainless ones.
- About the compilation speed when compiling STM32 with MDK
- Auto repair oscilloscope measuring the oxygen sensor signal of the car zirconium oxygen belt heater
- Can the same-phase AC amplifier circuit be used for low frequencies?
- Summary: Reading notes on "Operational Amplifier Parameter Analysis and LTspice Application Simulation"
- How to use CPLD to collect asynchronous signals
- Share: Where should the inductor be placed on the power supply PCB?
- [Open Source] GPIO Experiment Tutorial - Crazy Shell ARM Dual Processor Development Board Series
- Does the embedded industry strictly restrict college education?