Circuit Functionality and Benefits
The circuit shown in Figure 1 is a full-featured, high voltage (up to 44 V), flexible, programmable analog output solution that meets most requirements for programmable logic controller (PLC) and distributed control system (DCS) applications.
Circuit Description
Common changes
Circuit Evaluation and Testing
- System Demonstration Platform (EVAL-SDP-CB1Z)
- CN-0204 Circuit Evaluation Board (EVAL-CN0204-SDPZ)
- CN-0204 Evaluation Software
- Software for controlling external test and measurement equipment (not included on CD)
- Agilent 34401A 6.5 Digital Multimeter
- Agilent E3631A 0 V-6 V/5 A, ±25 V/1 A triple output DC power supply
- PC with USB port (Windows® 2000 or Windows XP)
- National Instruments GPIB to USB-B Interface and Cable
Load the evaluation software by placing the CN0204 evaluation software CD into the CD drive of the PC. Open "My Computer", locate the drive that contains the evaluation software CD, and open the Readme file. Follow the instructions in the Readme file to install and use the evaluation software.
Figure 5 shows a functional block diagram of the test setup. The pdf file “EVAL-CN0204-SDPZ-SCH” contains the detailed circuit schematics for the CN0204 evaluation board. This file is included in the CN-0204 Design Support Package: www.analog.com/CN0204-DesignSupport
the 120-pin connector on the EVAL-CN0204-SDPZ circuit board to the connector marked “CON A” or “CON B” on the EVAL-SDP-CB1Z (SDP) evaluation board. Nylon hardware should be used to secure the two boards together using the holes provided at the ends of the 120-pin connector. After setting the dc output power supply to +25 V, −25 V, and +6 V outputs, turn off the power supply.
Figure 5. Test setup functional block diagram
After setting up the test equipment, connect the CN4 pin labeled "VOUT" or the CN1 pin labeled "IOUT" to the input of the Agilent 34401A. Depending on the input signal type (current or voltage), ensure that the cables on the front panel of the Agilent 34401A are connected correctly. Testing INL, DNL, and total error takes quite a while because all the levels of the AD5662 16-bit DAC need to be set and measured by the 34401A.
Previous article:LM3406/LM3406HV Application Examples
Next article:Methods to prevent damage caused by thermal runaway
Recommended ReadingLatest update time:2024-11-16 22:35
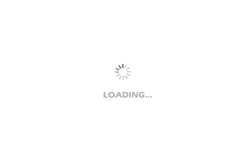
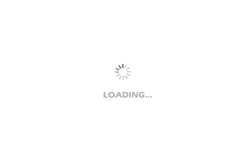
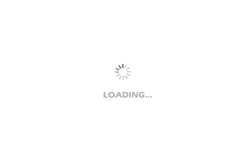
- Popular Resources
- Popular amplifiers
- MathWorks and NXP Collaborate to Launch Model-Based Design Toolbox for Battery Management Systems
- STMicroelectronics' advanced galvanically isolated gate driver STGAP3S provides flexible protection for IGBTs and SiC MOSFETs
- New diaphragm-free solid-state lithium battery technology is launched: the distance between the positive and negative electrodes is less than 0.000001 meters
- [“Source” Observe the Autumn Series] Application and testing of the next generation of semiconductor gallium oxide device photodetectors
- 采用自主设计封装,绝缘电阻显著提高!ROHM开发出更高电压xEV系统的SiC肖特基势垒二极管
- Will GaN replace SiC? PI's disruptive 1700V InnoMux2 is here to demonstrate
- From Isolation to the Third and a Half Generation: Understanding Naxinwei's Gate Driver IC in One Article
- The appeal of 48 V technology: importance, benefits and key factors in system-level applications
- Important breakthrough in recycling of used lithium-ion batteries
- Innolux's intelligent steer-by-wire solution makes cars smarter and safer
- 8051 MCU - Parity Check
- How to efficiently balance the sensitivity of tactile sensing interfaces
- What should I do if the servo motor shakes? What causes the servo motor to shake quickly?
- 【Brushless Motor】Analysis of three-phase BLDC motor and sharing of two popular development boards
- Midea Industrial Technology's subsidiaries Clou Electronics and Hekang New Energy jointly appeared at the Munich Battery Energy Storage Exhibition and Solar Energy Exhibition
- Guoxin Sichen | Application of ferroelectric memory PB85RS2MC in power battery management, with a capacity of 2M
- Analysis of common faults of frequency converter
- In a head-on competition with Qualcomm, what kind of cockpit products has Intel come up with?
- Dalian Rongke's all-vanadium liquid flow battery energy storage equipment industrialization project has entered the sprint stage before production
- Allegro MicroSystems Introduces Advanced Magnetic and Inductive Position Sensing Solutions at Electronica 2024
- Car key in the left hand, liveness detection radar in the right hand, UWB is imperative for cars!
- After a decade of rapid development, domestic CIS has entered the market
- Aegis Dagger Battery + Thor EM-i Super Hybrid, Geely New Energy has thrown out two "king bombs"
- A brief discussion on functional safety - fault, error, and failure
- In the smart car 2.0 cycle, these core industry chains are facing major opportunities!
- The United States and Japan are developing new batteries. CATL faces challenges? How should China's new energy battery industry respond?
- Murata launches high-precision 6-axis inertial sensor for automobiles
- Ford patents pre-charge alarm to help save costs and respond to emergencies
- New real-time microcontroller system from Texas Instruments enables smarter processing in automotive and industrial applications
- What is it like to have an engineer boyfriend or girlfriend?
- How to copy PCB to another PCB with network label in AD09
- Eliminating Software Failures with MSP432
- About the algorithm problem of brightness meter
- Qinhengwei CH549 minimum system schematic PCB
- Wen's Oscillation Problem
- Keil also released a community version
- Faint
- About STC8A8K64S4A12EEPROM allocation
- [Sipeed LicheeRV 86 Panel Review] 1. Unboxing Review