Imagine if a circuit isn't working, add a decoupling capacitor here and there (like a 0.01 μF ceramic disc capacitor), and it's fixed! Or if a circuit is emitting noise, a shield can solve the problem: wrap the circuit with a piece of metal, "ground" the shield, and the noise disappears!
Unfortunately, there is no such thing in reality. Adding a 0.01μF disc capacitor will only increase the noise; the shield will be completely ineffective, or even worse, the noise will reappear at the far end of the circuit.
This article is the first in a two-part series designed to help you understand and effectively deal with unwanted noise in electronic systems. Here we will consider the mechanisms of noise pickup, because the first step in solving any noise problem is to identify the source and coupling mechanism before implementing an effective solution. Later in Part 2 we will provide specific technical recommendations and principles for effective shielding of electrostatic and magnetically coupled noise.
What kind of noise are we talking about?
There are many sources of noise in any electronic system. There are three main forms of noise: transmitted noise, which is received along with the original signal and cannot be distinguished; intrinsic noise (such as Johnson noise, shot noise, and popcorn noise generated by heat), which originates from the components that make up the circuit; and interference noise, which is picked up from outside the circuit. Interference noise can originate from natural interference (such as lightning) or be coupled in from other electrical equipment in or nearby the system (such as computers, switching power supplies, SCR-controlled heaters, radio transmitters, switch contacts, etc.).
This article examines only the last category, man-made noise, which is the most pervasive system noise in a data acquisition or test system. It is most troublesome in low-level circuits, and no part of the system escapes its effects. However, it is also the only form of noise that is affected by routing and shielding choices.
What-if and Analysis Tools
Although a complete and accurate description of the behavior of an electrical system necessarily requires the use of Maxwell's equations (which means more math), traditional circuit analysis is still useful in most cases. To solve these problems, the following assumptions must be made to ensure that the circuit analysis is valid:
1. All electric fields are confined inside the capacitor.
2. All magnetic fields are confined to the immediate vicinity of the inductor.
3. The circuit size is small relative to the wavelength considered.
Using the above assumptions, we can model the noise coupling channel as a lumped circuit element. The magnetic field coupling the two inductors can be modeled as mutual inductance. The stray capacitance can be modeled as two conductors with an electric field between them. Figure 1 shows an equivalent circuit situation where two short wires are adjacent to each other at system ground.
Figure 1. Noise equivalent circuit for two adjacent wires and a ground plane.
Once the complete noise equivalent circuit for a system is obtained, the problem becomes solving one of the network equations for the desired parameters. All standard linear circuit analysis techniques can be applied, including node equations, loop equations, matrix algebra, state variables, superposition, Laplace transforms, and so on. Manual calculations become difficult when the circuit exceeds 5 and 6 nodes; computer-aided programs such as SPICE and other CAD techniques must be used. Experienced designers can make simplifying assumptions appropriately; but their validity must always be verified with caution.
The lumped element method does not necessarily give an exact numerical answer, but it can clearly show the dependence of noise on system parameters. Drawing the equivalent circuit as accurately as possible can provide ideas on how to reduce the noise level. Once the network equations and CAD program are written, the quantitative impact of noise suppression techniques can be studied.
Despite all the modern technological advances, such as microprocessors and switching power supplies, wires still have resistance and inductance, and capacitance still exists in the real world, and these phenomena must be taken seriously.
Rationale
Noise problems always involve three factors: the noise source (line transients, relays, magnetic fields, etc.), the coupling medium (capacitors, mutual inductance, wires), and the receiver, which is the circuit susceptible to the noise (Figure 2).
Figure 2. Noise pickup always involves a noise source, a coupling medium, and a receiver.
To solve the problem, one or more of these three factors must be eliminated, reduced, or diverted. Before the problem can be solved, the role of these factors in the problem must be fully understood. If the solution is not appropriate, the noise problem will only get worse! Different noise problems require different solutions; adding capacitors or shielding will not necessarily work.
System Noise Type
Noise in any electronic system comes from many sources, including computers, fans, power supplies, adjacent equipment, test devices, and even improperly connected shields and ground wires used to suppress noise. The noise sources and coupling mechanisms we discuss include the following topics:
●Common impedance noise
●Capacitively coupled noise
Magnetic coupling noise
Power line transients
Other noise sources
Common impedance noise
As the name implies, common impedance noise is caused by an impedance that is common to several circuits. Figure 3 shows the basic configuration that can occur when both the pulse output source and the op amp reference terminal are connected to a “ground” point that presents significant impedance to the power supply return terminal. The noise current (the noise return current of circuit 1) will produce a voltage Vnoise across impedance Z, which appears as a noise signal to circuit 2.
Figure 3. How common circuit impedances generate noise.
Typically, the repetition rate of this type of noise depends on the noise source rate. The actual waveform is determined by the characteristics of the impedance Z. For example, if Z is completely resistive, the noise voltage will be proportional to the noise current and have a similar shape (Figure 4a). If Z is RLC, the noise voltage will ring at a frequency of 1/(2πLC) and decay exponentially at a rate determined by L/R (b).
If this type of noise is found in a circuit, the cause can be easily deduced from the repetition rate and waveform. The repetition rate will point to the source of the noise because the noise is synchronous with its source.
For example, the noise waveform shown in (c) (25kHz repetition rate, 25% duty cycle) is typical of a switching power supply that includes a regulation loop and uses pulse width modulation.
Figure 4. Noise effects in common impedance, (a) resistor, (b) RLC circuit, (c) switching noise response.
The waveform helps determine the impedance that actually generates the interfering noise. For example, if the noise waveform is a simple damped sine wave as shown in Figure 5, the following characteristics help us infer the nature of Z:
● A constant resistor R is connected in series with the line. The voltage change V1 is the product of R and the current step I1.
●The natural frequency of oscillation f1 depends on the series L and the incorporated C, f = 1/(2πLC).
●The damping time constant T is determined by L/R.
Figure 5. Waveforms for an underdamped RLC circuit.
Capacitively coupled noise
Noise can also be generated by capacitive coupling of a noise source to another circuit. This type of noise is common when a signal with fast rise and fall times or high frequency content is close to a high impedance circuit. Stray capacitance couples the fast edges of the signal to the adjacent circuit, as shown in the circuit model of Figure 6. The nature of the impedance Z determines the response waveform. Table 1 lists typical capacitances.
Figure 6. Stray capacitance couples noise into high-impedance circuits.
Table 1. Typical capacitors.
Capacitive pickup comes in many ways, shapes, and sizes. Here are a few examples:
●TTL digital signals produce fast edges with a typical rise time of 10 nanoseconds and a voltage swing of 5 V. If Z is a 1 megohm resistor, even 0.1 pF will produce a 5 V spike and a decay time constant of 100 nanoseconds.
● Crosstalk may occur between two adjacent conductors. For example, if the two conductors are a 10-foot (3-meter) cable with a capacitance of 40 pF/foot, the total capacitance is 400 pF. If a 10 V test voltage is applied to one conductor at 1 kHz, 250 mV at 1 kHz will be coupled to the adjacent conductor when Z is a 10 k resistor.
●Noise generated on the AC power line will couple into other circuits through a common impedance. A common case is the coupling of transients through the inter-winding capacitance of a power transformer.
It is amazing how small amounts of capacitance can cause serious problems. For example, consider the case where highly immune CMOS logic is used in an industrial circuit that is subject to 2500 V, 1.5 MHz noise transients (IEEE Standard 472-1974). Assume that there is only 0.1 pF of stray capacitance between the CMOS input and the noise source, as shown in Figure 7. The calculated noise voltage is 2.4 V, and in steady state, an initial transient of 50 V will cause logic operation errors, or even worse!
Figure 7. High voltage transient coupled from test generator into logic.
Magnetic coupling noise
Strong magnetic fields can be found in cables carrying current, distributing AC power, and near machinery, power transformers, fans, etc. A similar relationship exists between magnetically coupled circuits and capacitively coupled circuits, as shown in Figure 8 and Table 2.
● When the noise is magnetically coupled, the voltage noise (Vn) appears in series with the receiver circuit; in the capacitive case, the voltage noise generated between the receiver and the ground voltage is the voltage caused by the noise current in in Z.
● Reducing the receiver impedance Z can reduce capacitively coupled noise. This is different for magnetically coupled circuits; reducing Z does not significantly reduce voltage noise.
Figure 8. Comparison of magnetic noise coupling and capacitive noise coupling.
Table 2. Characteristics of capacitive and magnetic coupling.
This analogy helps us consider the difference between capacitively coupled noise and magnetically coupled noise.
The induced voltage Vn of the magnetic field in a closed loop (single turn) is given by:
Vn = 2πfBA cosθ×10-8 (1)
The units are volts, where f is the frequency of the sinusoidally varying flux density, B is the RMS value of the flux density (in Gauss), A is the area of the closed loop (in cm2), and θ is the angle between B and area A.
For example, consider the circuit in Figure 9. It shows the voltage calculation for two one-foot conductors, one inch apart, placed in a 10-gauss, 60-Hz magnetic field (typical for fans, power wiring, transformers). The maximum induced voltage in the wires is 3 mV.
Figure 9. Example of magnetic noise amplitude.
The above equations show that the noise voltage can be reduced by reducing B, A, or cosθ. To reduce the B term, the distance from the source of the magnetic field can be increased, or in the case of magnetic fields caused by current flowing near the wire pair, the wires can be twisted to reduce the net magnetic field to zero by alternating their direction.
The loop area, A, can be reduced by moving the conductors closer together. For example, if the conductors in this example were 0.1" apart (separated only by insulation), the noise voltage would be reduced to 0.3 mV. If the conductors are twisted together, the area is actually reduced to very small positive and negative increments, thus canceling (actually canceling) the magnetic noise.
The cosθ term can be reduced by properly orienting the receive conductors with respect to the magnetic field. For example, if the conductors are perpendicular to the magnetic field, the noise will be minimized, and if the conductors run together in the same cable (θ = 0), the noise will be maximized.
When two conductors are connected in parallel, with a given mutual inductance M, carrying a current I2 at an angular frequency ω = 2πf, the rms induced voltage Vn is:
Vn = ωMI2 (2)
Figure 10. Magnetic noise caused by current flowing through the cable shield.
Figure 10 shows this relationship in action and why the shield should only be grounded at one end. A 100-foot shielded cable is used to carry a high-level, low-impedance signal (10V) to a 12-bit data acquisition system (1 LSB = 2.4 mV).
The series resistance of the foot is 0.01 ohms, the mutual inductance with the conductor is 0.6 μH/foot, and the source and destination are both grounded. There is a 1 V potential between the two ground points at 60 Hz, causing a current of 1 ampere to flow into the total resistance of the shield of 1 ohm. According to formula (2), the induced noise voltage in the conductor is:
Vn=(2π×0.6×10-6H)(1 A)=23 mV,
That is 10 LSB, which reduces the effective resolution of the system to less than 9 bits. Since the shield is grounded at both ends, the high current flowing into the shield is a direct cause of this noise voltage. And, the 1 volt potential between the ground points is only a conservative assumption! In heavy industrial environments, it is not uncommon to see potentials of 10 to 50 volts between grounds.
Power Line Transients
Another type of system noise is generated by high voltage transients when inductive circuits (such as relays, solenoids, and motors) are turned on and off. When a device with high self-inductance turns off, the collapsing magnetic field can generate kilovolt transients on the power line with frequencies ranging from 0.1 to 3 MHz.
In addition to generating noise in sensitive circuits through capacitive and conductive coupling and radiated energy, these transients can also endanger equipment and personnel. The industry has established protection standards that characterize specific transient waveforms; however, in addition to noise immunity, the system should also address potential interference with the signal when designed. Figure 11 shows four typical waveforms from industry standards.
Other Noise SourcesFinally, there is a group of noise sources that can be considered as miscellaneous or "oddball".
The cable itself can also be a source of noise for low-level signals at high impedance. Charge can build up on the dielectric material within the cable; if the dielectric is not in contact with the conductor, this charge will become a source of noise within the cable unless the cable is kept rigid. This noise is highly dependent on any movement of the cable; Belden Corporation has reported noise levels of 5 to 100 mV. Noise of similar characteristics (5 to 25 mV) has been observed when RG188 coaxial cable was moved and bent in the lab.
Another type of motion-related noise occurs when a cable passes through a magnetic field. When the cable cuts through fixed flux lines or when the flux density B varies, voltages are induced in the cable. This noise is troublesome in high-vibration environments that may cause the cable to move rapidly. If the cable can be prevented from vibrating relative to the magnetic field, the noise will not occur.
Finally, if the instrument is operating near a radio or television station, the signal may be affected by transmission noise. In addition to AM, FM, and TV transmitters, RFI may come from CB radios, ham radios, walkie-talkies, paging systems, etc. Due to the rectification of RF noise, high-frequency noise should be considered as a possible source of mysterious drift in DC circuits; a wideband oscilloscope must be used when investigating drift.
Summarize
This article details the different types of interfering noise that can be present in any electronic system. Table 3 lists the above noise sources and some effective methods to solve the noise problem. It is important to understand the complete noise system (source, coupling medium, receiver, and correlation) before using noise reduction techniques.
Noise reduction does not require magicians, but can be solved through engineers' practice and analysis. Undoubtedly, the most effective method is prevention, that is, applying noise reduction analysis and minimization techniques before building the system.
Previous article:Offline LED spotlight technology designed by PT4201
Next article:A New Current Limit Comparator
Recommended ReadingLatest update time:2024-11-16 21:52
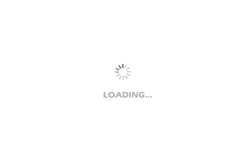
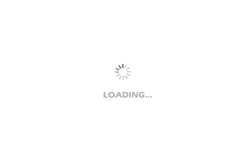
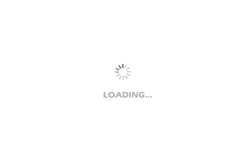
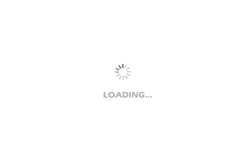
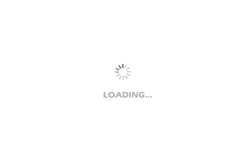
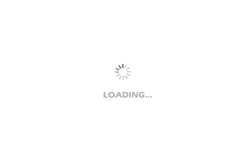
- Popular Resources
- Popular amplifiers
-
Radio Frequency Identification (RFID) System Technology and Application (Written by Ci Xinxin, Wang Subin, and Wang Shuo)
-
Research on the relationship between load variables in microwave heating system based on radio frequency circuit
-
IoT Identification Technology
-
Basics of Machine Learning: From Getting Started to Job Hunting (Hu Huanwu)
- MathWorks and NXP Collaborate to Launch Model-Based Design Toolbox for Battery Management Systems
- STMicroelectronics' advanced galvanically isolated gate driver STGAP3S provides flexible protection for IGBTs and SiC MOSFETs
- New diaphragm-free solid-state lithium battery technology is launched: the distance between the positive and negative electrodes is less than 0.000001 meters
- [“Source” Observe the Autumn Series] Application and testing of the next generation of semiconductor gallium oxide device photodetectors
- 采用自主设计封装,绝缘电阻显著提高!ROHM开发出更高电压xEV系统的SiC肖特基势垒二极管
- Will GaN replace SiC? PI's disruptive 1700V InnoMux2 is here to demonstrate
- From Isolation to the Third and a Half Generation: Understanding Naxinwei's Gate Driver IC in One Article
- The appeal of 48 V technology: importance, benefits and key factors in system-level applications
- Important breakthrough in recycling of used lithium-ion batteries
- Innolux's intelligent steer-by-wire solution makes cars smarter and safer
- 8051 MCU - Parity Check
- How to efficiently balance the sensitivity of tactile sensing interfaces
- What should I do if the servo motor shakes? What causes the servo motor to shake quickly?
- 【Brushless Motor】Analysis of three-phase BLDC motor and sharing of two popular development boards
- Midea Industrial Technology's subsidiaries Clou Electronics and Hekang New Energy jointly appeared at the Munich Battery Energy Storage Exhibition and Solar Energy Exhibition
- Guoxin Sichen | Application of ferroelectric memory PB85RS2MC in power battery management, with a capacity of 2M
- Analysis of common faults of frequency converter
- In a head-on competition with Qualcomm, what kind of cockpit products has Intel come up with?
- Dalian Rongke's all-vanadium liquid flow battery energy storage equipment industrialization project has entered the sprint stage before production
- Allegro MicroSystems Introduces Advanced Magnetic and Inductive Position Sensing Solutions at Electronica 2024
- Car key in the left hand, liveness detection radar in the right hand, UWB is imperative for cars!
- After a decade of rapid development, domestic CIS has entered the market
- Aegis Dagger Battery + Thor EM-i Super Hybrid, Geely New Energy has thrown out two "king bombs"
- A brief discussion on functional safety - fault, error, and failure
- In the smart car 2.0 cycle, these core industry chains are facing major opportunities!
- The United States and Japan are developing new batteries. CATL faces challenges? How should China's new energy battery industry respond?
- Murata launches high-precision 6-axis inertial sensor for automobiles
- Ford patents pre-charge alarm to help save costs and respond to emergencies
- New real-time microcontroller system from Texas Instruments enables smarter processing in automotive and industrial applications
- FPGA Introduction Series 6--Judgment Statement
- Award-winning live broadcast: Embark on the journey from embedded to cloud with PIC and AVR microcontrollers in the Microchip ecosystem
- 【Ended】Microchip Live Broadcast|Unveiling the ISA/IEC 62443 Safety Standard for Industrial Systems
- Interesting Algorithms (C Language Implementation 2nd Edition)
- OEM or research lab? Where does innovation come from?
- Sharing of wireless quality resources!
- Comparison of main control with storage chip SD NAND and eMMC
- There is a small thing in the water heater. If you don't pay attention, it can consume 1000 degrees of electricity in a month???
- Based on GD32E231 smart door lock
- Award: ST MEMS Sensor Forum User Survey