In the frequency range of 10MHz to 3000MHz, most absorbers use lossy magnetic materials (such as carbonyl iron or ferrite powders) to reduce their surface currents. These surface currents are caused by the interaction between harmful EMI and conductors, and their presence can also cause secondary radiation of electromagnetic fields, so in order to ensure that the product meets the relevant regulations, they are usually reduced. In addition, these surface currents may interfere with other circuits and prevent the normal operation of the system.
Comparing the performance of absorbers provided by different manufacturers is expensive and time-consuming. Given that EMI test labs can cost thousands of dollars per day, trial and error testing must be kept to a minimum. Therefore, bringing several potential absorbers to the EMI lab to determine the best one has proven to be a very expensive solution. The simple surface current reduction test fixture (SCRF) described in this article allows a quick and easy comparison of the performance of various absorber samples, thereby narrowing down the absorber selection to the best one or two for a specific EMI problem within a certain frequency range. The SCRF consists
of two electrostatically shielded magnetic field loop antennas that are carefully placed at right angles to each other to achieve 70 dB or more of isolation over the relevant frequency range. One of the loop antennas in the SCRF is connected to a swept RF source, while the other loop antenna is connected to an RF swept receiver. If a conductor plate similar to the product shell is placed in a fixed position close to the two loop antennas, a current will be generated on the conductor surface, and the secondary radiation generated by the surface current will be received by the loop antenna. The typical value of the increase in the antenna receiving signal caused by this is about 20dB to 30dB. On this basis, if a sample of a certain EMI absorbing material is covered on the conductor plate and the above test process is repeated, the reduction in the secondary radiation of the electromagnetic field can be measured. We can use this reduction in secondary radiation to compare the absorbing performance of different absorbing materials.
Construction of the test device
It is not difficult to process and manufacture a probe as shown in Figure 1. The probe is made by winding a #24AWG wire with a solid Teflon@ insulation layer around a 1.5 cm mandrel twice. Increasing the diameter and the number of turns will increase the measurement sensitivity of the probe, but the corresponding cost is a reduction in the maximum operating frequency.
Figure 1. Laboratory-made shielded ring (frequency range: 2MHz-600MHz)
One end of the ring antenna is soldered to the core of the coaxial line, and the other end is soldered to the shield of the coaxial line. Except for a small gap in a part of the ring directly opposite the connection point between the ring antenna and the coaxial line, the rest of the ring antenna is completely covered by copper tape. Without this small gap, the ring antenna will be completely short-circuited, the electric field and magnetic field will be shielded, and the ring antenna will not be able to complete the measurement. In addition, the connection between the copper tape and the shield of the coaxial line and between the front and back overlapping copper tapes is completed by using a large amount of solder. According to the above method, we can process two identical loop antennas. The probe shown in Figure 1 is applicable to the frequency range between 3MHz and 600MHz.
It is more economical and time-saving to order the appropriate probe through commercial channels. The samples of shielded ring antennas provided by some manufacturers listed below will clearly state their respective applicable frequency ranges, which can be used as a reference.
ARA Technologies, Deer Park, NY; www.aratech-inc.com
Com-Power, Lake Forest, CA; www.com-power.com
Credence Tecnologies, Soquel, CA; www.credencetech.com
Electro-Metrics, Johnstown, NY; www.electro-metrics.com
EMC Test Systems, Cedar Park, TX; www.emctest.com
Fischer Customer Communications, Torrance, CA; www.fischercc.com
As shown in Figure 2, whether you choose to manufacture or purchase the loop antennas, the two loop antennas must be carefully placed in a perpendicular position to minimize coupling between the two antennas; and the platform used to support the test setup can be simply made of wood and plastic. As mentioned earlier, one probe in the test setup will be connected to the RF swept source, and the other probe will be connected to the swept receiver. If the test lab is equipped with a vector network analyzer, then as long as the isolation between its RF signal source and receiving port is greater than 70dB, a network analyzer that combines spectrum analyzer function and swept frequency signal source function can perform this test task well. In addition, the loop antenna must be fixed on a dielectric material, such as wood and plastic during the test. The basic test setup is not complicated. By inserting screws into a wooden block, a simple test setup as shown in Figure 2 can be obtained.
Figure 2. Relative position of two loop antennas when coupling is minimized without a conductive plate
The most difficult step in building the test setup is to adjust the relative position of the antennas to obtain the minimum coupling between the two antennas. First, we can adhere one probe to the support platform. Then, carefully adjust the position of the second probe on the two-dimensional surface of the support platform to minimize the coupling between the two probes. Once the approximate position of the second probe is determined, we can fix it by applying high-temperature, fast-setting hot melt adhesive. Because the hot melt adhesive just applied has not yet solidified, we can continue to manually fine-tune the position of the second probe; when the hot melt adhesive solidifies, the second probe can be accurately placed at the position with the minimum coupling. After an hour of careful trial and error and adjustments, we were able to achieve 80dB of isolation over two decades using the hot melt method. In addition, adding one or more clip-on magnetic rings to the coaxial line of the test setup would help us achieve the required isolation of at least 70dB over a wider frequency range.
The distance between the two closest points of the loop antenna is not particularly important, and a distance of half the diameter of the loop antenna or a full diameter will give good performance. Once the spacing between the two loop antennas is determined and the isolation between the two loop antennas temporarily fixed to the test platform is greater than 70dB, a metal plate of similar material can be selected based on the surface to which the absorber will be attached and placed close to the two loop antennas, as shown in Figure 3. The best position of the metal plate is the position where the coupling between the two loop antennas is the strongest. If the resulting increase in coupling between the two loop antennas can reach 20dB or more, it will be very beneficial to improve the overall measurement accuracy, especially for high-performance absorbers under test.
Figure 3. Surface current on the conductor plate increases coupling by 20-30dB
Test
In order to measure the absorbing performance of a given material, it needs to be attached to the metal plate of the SCRF device. The reduction in EMI reflections can be directly measured by the receiver by comparing the value measured by the test device without the absorber attached.
Although a vector network analyzer that can provide both RF swept source and receiver functions is an ideal test instrument, a scalar network analyzer that covers the required frequency range is also a good solution. If the above test equipment is not available, we can also use a cheaper spectrum analyzer and its tracking source to complete the comparison of EMI absorber performance. All three test instruments described above can perform swept frequency measurements over the frequency range covered by the loop magnetic field antenna. In addition, if the interference only occurs at a few frequency points, even if the relevant swept frequency equipment is not available, we can complete the relevant test tasks with a signal generator and some test receivers.
Test Results
Using the surface current reduction device, we compared the performance of different EMI absorber samples from Brigitflex Inc. and ARC Technologies. The metal surface selected for the test was a single-sided or double-sided copper FR-4 type printed circuit board (PCB). The size of each side of the copper-clad PCB board was approximately three to five times the diameter of the loop antenna. The copper-clad side of the PCB board faced the loop antenna. The reduction in reflection of the copper-clad FR-4 PCB board caused by material A in the SCRF device is shown in Figure 4 compared with the case without absorber. The slightly higher curve in the figure is the reference curve, while the slightly lower curve is the curve after adding the loss caused by the absorbing material to be tested. Similarly, measuring material B in the test setup shown in Figure 4 can obtain a larger attenuation loss as shown in Figure 5.
Figure 4. Material A shows a surface current reduction of 4-6dB
Figure 5. Material B shows a surface current reduction of 6-9dB
This paper designs and processes a simple surface current reduction test device that can be used to compare the absorbing performance of different EMI absorbing materials in a laboratory environment. Although the reduction in surface current caused by the absorbing material is not exactly equal to the measured value of the expected EMI reduction, this method can quickly determine the material with the best absorbing performance in a specific frequency range.
Previous article:Analysis of wireless charging system design principles and implementation
Next article:Circuit Simulation Techniques in Altium Designer
Recommended ReadingLatest update time:2024-11-16 19:27
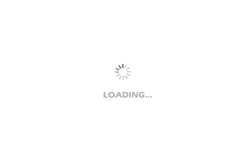
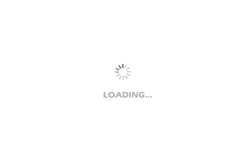
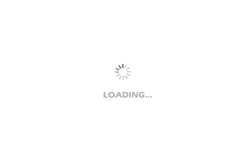
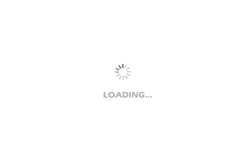
- Popular Resources
- Popular amplifiers
-
Study on the Behavioral Model of Silicon Carbide MOSFET Power Module and EMI Prediction of Low-Voltage Auxiliary Power Supply
-
Cable radiated EMI modeling considering mutual coupling effects_Junpeng Ji
-
Design of broadband hybrid active EMI filter for switching power supply_Liao Yuehong
-
Switching power supply conducted EMI simulation and filter circuit design_Jiang Yunfu
- MathWorks and NXP Collaborate to Launch Model-Based Design Toolbox for Battery Management Systems
- STMicroelectronics' advanced galvanically isolated gate driver STGAP3S provides flexible protection for IGBTs and SiC MOSFETs
- New diaphragm-free solid-state lithium battery technology is launched: the distance between the positive and negative electrodes is less than 0.000001 meters
- [“Source” Observe the Autumn Series] Application and testing of the next generation of semiconductor gallium oxide device photodetectors
- 采用自主设计封装,绝缘电阻显著提高!ROHM开发出更高电压xEV系统的SiC肖特基势垒二极管
- Will GaN replace SiC? PI's disruptive 1700V InnoMux2 is here to demonstrate
- From Isolation to the Third and a Half Generation: Understanding Naxinwei's Gate Driver IC in One Article
- The appeal of 48 V technology: importance, benefits and key factors in system-level applications
- Important breakthrough in recycling of used lithium-ion batteries
- Innolux's intelligent steer-by-wire solution makes cars smarter and safer
- 8051 MCU - Parity Check
- How to efficiently balance the sensitivity of tactile sensing interfaces
- What should I do if the servo motor shakes? What causes the servo motor to shake quickly?
- 【Brushless Motor】Analysis of three-phase BLDC motor and sharing of two popular development boards
- Midea Industrial Technology's subsidiaries Clou Electronics and Hekang New Energy jointly appeared at the Munich Battery Energy Storage Exhibition and Solar Energy Exhibition
- Guoxin Sichen | Application of ferroelectric memory PB85RS2MC in power battery management, with a capacity of 2M
- Analysis of common faults of frequency converter
- In a head-on competition with Qualcomm, what kind of cockpit products has Intel come up with?
- Dalian Rongke's all-vanadium liquid flow battery energy storage equipment industrialization project has entered the sprint stage before production
- Allegro MicroSystems Introduces Advanced Magnetic and Inductive Position Sensing Solutions at Electronica 2024
- Car key in the left hand, liveness detection radar in the right hand, UWB is imperative for cars!
- After a decade of rapid development, domestic CIS has entered the market
- Aegis Dagger Battery + Thor EM-i Super Hybrid, Geely New Energy has thrown out two "king bombs"
- A brief discussion on functional safety - fault, error, and failure
- In the smart car 2.0 cycle, these core industry chains are facing major opportunities!
- The United States and Japan are developing new batteries. CATL faces challenges? How should China's new energy battery industry respond?
- Murata launches high-precision 6-axis inertial sensor for automobiles
- Ford patents pre-charge alarm to help save costs and respond to emergencies
- New real-time microcontroller system from Texas Instruments enables smarter processing in automotive and industrial applications
- MM32F103 BUG reminder to avoid falling into the pit 2? Please answer
- Maybe I'm the only one who has messed up a development board with code.
- Teach you how to implement serial port burning of TMS320F28035
- How to enable traditional surface power supply to use type-c PD fast charging charger?
- How to use Cadence Allegro to form a dot-shaped copper layer
- What is the manufacturing process level of a microcontroller like STM32?
- LM27762 Charge Pump with Integrated Positive and Negative LDO
- Transfer a video "There is a kind of beauty called mathematics"
- Let novices quickly understand Zigbee----Zigbee Overview
- #RecommendChinaCore# Activity sharing summary