The thermal characteristics of the LED from the PN junction to the environment must be clearly understood to ensure a safe, reliable design and satisfactory performance. There may be multiple thermal interfaces such as bare chips or glue layers in the heat flow path, and their thickness and thermal resistance are difficult to control during production. In addition, the thermal interface between the LED package and the lighting device housing as a heat sink further increases the design challenge. The thermal resistance value of the LED must be understood as early as possible in the prototype stage.
Current, Color and Efficacy
The light output characteristics of an LED depend critically on its operating conditions. An increase in forward current causes the LED to produce more light. But if the forward current remains constant, the light output decreases as the temperature of the LED increases. Figure 1 depicts the relationship between temperature, current, and light output. It also depicts the shift in the color spectrum associated with an LED at its peak wavelength. For monochromatic LEDs used for general lighting, the peak of the blue spectrum shifts, thus changing the so-called color temperature of the LED. This affects the perception of the space illuminated by the LED.
Like many other products, lighting systems are designed with a trade-off between cost and performance. Power distribution and the resulting heat dissipation requirements are largely determined by the energy conversion efficiency of the LED. It is defined as the ratio of the light energy emitted to the input electrical power. Energy efficiency is closely related to another metric parameter, efficacy, which is a price index of usefulness, the ratio of perceived light divided by the electrical power provided. Efficacy is used to evaluate the pros and cons of different light sources. Unfortunately, the efficacy of LEDs decreases as the LED junction temperature increases. Predicting the output luminous flux of an LED is the ultimate goal of lighting design. Thermal management solutions that provide effective heat dissipation can produce more consistent color luminous flux in actual LED applications.
Heat transfer starts from the LED package chip, and the relevant data is provided by the supplier. Figure 2 shows a common heat conduction structure. About 50% of the thermal resistance from the junction to the environment of an LED lamp is caused by the LED package.
Traditional LED standards need to be further improved. Relevant industrial standards are being drafted, but LED suppliers still define the thermal resistance and other temperature-related characteristic parameters of their products in different ways. For example, when the radiant light power as a conditional variable is ignored when determining the thermal resistance of the LED, the thermal resistance value obtained will be lower than the actual thermal resistance value. If the actual thermal resistance value is higher, the corresponding LED junction temperature will also be higher, resulting in insufficient luminous flux. Therefore, it is very important to understand the true LED thermal characteristic parameters.
Measurement: Temperature is more important than light flux
Assume that the temperature of the LED is linearly related to the forward voltage drop across it. Therefore, the temperature change can be accurately inferred by observing the voltage drop. In order to perform this test well, the hardware and software of the test system must meet certain requirements. For example, Mentor Graphics' MicReD commercial automated test system is a typical device that meets such requirements.
Figure 3 depicts a simplified diagram of such a measurement setup (not to scale). The first step in the measurement is to determine the temperature sensitivity of the forward voltage to a very small current, which can be the sensor or measurement current. After that, a large current is applied to the LED, causing it to heat up. The large current is then stopped and the small sensor current is reapplied, while the forward voltage is measured at a high sampling rate until the LED junction temperature is completely stabilized. Due to the rapid thermal response of the LED, the measurement hardware must be able to capture the temperature (voltage) change within a few microseconds after the LED current is stopped. As shown in Figure 3, the LED being measured is in an enclosure, which is a JEDEC standard natural convection chamber, which provides an environment without airflow. A similar setup can also be provided by T3STer. Table 1 summarizes the test steps.
In the electronics industry, the term "Z" stands for impedance, in our case thermal impedance. In a thermal impedance curve, it represents the temperature difference divided by the thermal power dissipation. Therefore, the Z curve in Figure 4 describes the temperature change for 1W of thermal power dissipation.
The thermal impedance curve Zth is generally smooth, but there are still local fluctuations, and engineers need to explain the reasons. And it is composed of a large number of dense data points, so the potential information is very rich. A powerful thermal test system that integrates advanced applied mathematics can provide very useful analytical transformations of Zth and time curves.
The data in the Zth graph makes it possible to calculate the overall graph of thermal capacitance and thermal resistance, also known as the structure function. It is a graphical representation of the thermal impedance network model in the node-to-ambient heat flow path. The form of the structure function maintains a one-to-one correspondence with the actual node-to-ambient heat flow path. The node of the component is always at the origin of the graph. The graph in Figure 5 illustrates this concept.
In LED components, the heat generated by the semiconductor is transferred from itself. The junction is heated, and then the heat passes through many thermal resistors, heating the objects in the heat flow path. In fact, the more thermal resistors the heat passes through, the more heat is heated.
In Figure 5, the initial curve is very steep as the heat sink is heated. This curve is annotated to describe the three stages of LED/MCPCB, encapsulant (thermal grease), and lighting. But within the first stage, the curve describes smaller stages such as Die attach, heat sink, and even the glue that fastens the copper heat sink to the MCPCB. Note that this graph confirms an earlier argument that the thermal resistance of the LED itself accounts for 50% of the total system junction-to-ambient thermal resistance.
Looking at Figure 3 again, note that only the voltage across the LED element is measured. How does the system get thermal data for the entire lighting device? The answer is to monitor and observe the temperature drop curve.
When the temperature of the LED die starts to drop, it drops slowly because there is only one object directly connected to it that affects its temperature. The time it takes for the die temperature to drop depends mainly on the thermal capacitance, which can store heat. The test system monitors small changes in temperature and converts them into thermal resistance/thermal capacitance data points. If they have the same characteristics, similar curves will be seen. Therefore, there are high requirements for the sensitivity of the test system.
From testing to prototyping
Structure functions help engineers evaluate the various components of the overall thermal path. Importantly, they can help reveal problems in the design that could affect the production or reliability of the device.
The structure function can be further transformed into a simplified model, which is an equivalent network including thermal resistance and thermal capacitance, which includes all the values included in the structure function graph. Figure 6 describes a general model of semiconductor components such as power LEDs. Of course, the actual model will have specific values for R and C.
The R/C network model obtained by transient thermal testing can be directly used in thermal design tools to perform thermal simulation on LED systems. In order to meet the market's requirements for more thermal performance data of their products, some semiconductor suppliers have begun to use transient models to describe the thermal performance of their power switches and similar products, which also provides a reference for LED suppliers to follow this practice in the future.
Photometric Measurement Reveals the True Color of LEDs
All previous efforts have brought the lighting device to the point of being released to the market. However, an important question must be answered at this point: How much light is the lighting device expected to emit when it is operating within its specified temperature range? Before the product goes into mass production, the prototype must be provided with complete photometric and radiometric characteristics. With the help of today's automated tools, thermal and optical measurements can be performed simultaneously.
In order to perform simultaneous measurements, it has been explained that thermal testing must be combined with a subsystem that is used to test the LED light output under conditions that meet CIE1 requirements (see Notes). This subsystem consists of a thermostat (similar to a cold plate) and a detector. Both devices are controlled by specific software. A fully integrated thermal/radiant/photometric test system can characterize the thermal resistance and light output characteristics of a lighting device, including radiant heat flow (i.e. output optical power), luminous flux and chromaticity. These values can be measured simultaneously under different reference temperatures and forward current conditions.
Importantly, adding thermal transient testing to the normal cycling photometry test does not significantly increase the test time. This is because the junction temperature of the power LED attached to the cold plate usually stabilizes within 30 to 60 seconds. The heating process before the LED thermal resistance test is a similar process. Therefore, the test time with thermal testing is the same as the time for light output testing alone; all these characteristics must be measured under the condition that the LED is thermally stable.
Temperature: reference, ambient, environment…
The thermal resistance from junction to ambient of a thermal management solution is easily affected by the ambient temperature, thus distorting the test results. Therefore, when predicting the thermal performance of a lighting device, the test ambient temperature, i.e. the reference temperature, must be specified. However, when thermal and photometric/radiometric measurements are done simultaneously, the reference temperature is the temperature of the cold plate.
As explained before, the industrial standardization of LED characteristics is still in progress, which means that suppliers have a lot of freedom in describing their products and providing relevant data. Usually, environmental information is not taken seriously. Data on product performance may be obtained when the lighting device is in optimal lighting, which can be said to ignore some of the effects of real working conditions. For example, the LED data provided by suppliers is usually under an ambient temperature of 25oC, even if the temperature of the mounting surface of the LED after it is installed in the lamp is 50oC or even 80oC. Under working conditions, the actual LED junction temperature may be in the range of 80~100oC, causing a sharp drop in luminous flux.
Figure 7a shows the relationship between the luminous flux and the reference temperature of two white LEDs from the same manufacturer, which have different heat dissipation methods. Heat dissipation method 1 uses a metal PCB board, while heat dissipation method 2 uses a traditional FR4 board. In addition, different thermal interface materials are used between the PCB board and the heat sink of the two LED samples.
The test method to obtain the luminous flux and reference temperature is very simple. During the test, the cold plate directly affects the junction temperature of the LED. Therefore, by changing the temperature of the cold plate, the effect of the junction temperature change on the luminous flux can be observed.
The two LED curves in Figure 7a are not completely parallel. Because the tests were based on the same type of LED, one might expect the performance of the two LEDs to be identical. However, note the plots of luminous flux versus reference temperature. The thermal interface materials used have different temperature effects, which in turn have different impacts on the LED junction temperature. The structure functions at different cold plate temperatures can further reveal the extent and location of these effects.
A lot of testing work is about determining the heating power consumption and thermal resistance value at each reference temperature. If you have this information, you can calculate the corresponding LED junction temperature value. If there is no further testing requirement. Engineers can use the previous information to re-plot the relationship between LED junction temperature and luminous flux.
Redrawing the curve based on the real LED junction temperature will eliminate the deviation in the slope of the luminous flux curve. Figure 7b describes a set of luminous flux and junction temperature curves, and the real junction temperature here is calculated using the real heating power and the real thermal resistance. Now for all LED samples from the same supplier, the characteristic slope obtained from the forward current value is consistent. Small deviations in luminous flux are equivalent to normal manufacturing errors.
Static measurement, photometry and integrating sphere
Characterizing important parameters such as color cast requires not only current and thermal testing, but also a fully controllable small "black chamber". Obviously, it is very important not to let extraneous light affect the sensitive wavelength readings.
The simplest way to measure LED thermal impedance is to use a static test method using a four-wire "Kelvin" test device. First, the LED is in a steady state and the forward current (IF) required to generate the required heating current (IH) level is set. The constant heating current is the LED temperature reaching a stable value, thereby generating a constant luminous flux.
Under the static test conditions defined in the JEDEC JESD51-1 standard, once the LED is in a hot state, its forward current suddenly drops to a very low measurement current level, IM (step 2 in Table 1). In fact, the LED is turned off, generating a negative power. During this phase, the corresponding voltage is measured (step 3 in Table 1). The change in the LED junction temperature is inferred from the change in the LED forward voltage.
Note that when the PN junction forward current is suddenly stopped (during the test), electrical transients will inevitably occur. This transient will last for a short period of time, during which the change in forward voltage cannot describe the change in temperature of the LED chip. Therefore, a time delay must be left for the electrical transient to disappear when measuring.
Figure 8 summarizes the interactions between the variables.
The TERALED thermal/radiation measurement system from Mentor Graphics' MicReD division is used to measure LED radiation and photometric characteristics. Its development purpose is to provide a complete solution for the static test just mentioned. When connected to the T3Ster system, TERALED can complete thermal transient testing, thereby providing structure functions, simplified models and thermal characteristic data, while also obtaining photometric characteristic data.
The TERALED system includes various components necessary to obtain accurate and repeatable measurements of key LED parameters:
High-precision detectors and reference light sources
Filter combination with high precision V filter to provide light flux measurement
Filters with a flat spectral response to measure radiant flux (transmitted optical power)
3 filters for direct measurement of CIE light XY color coordinates
1 temperature-stabilized temperature probe
1 Accumulating Ball ("Black Cavity")
When TERALED is used in stand-alone mode, it can perform photometric measurements. When combined with the T3Ster system, it can perform both thermal and photometric measurements. Figure 9 is a simplified diagram of TERALED and T3Ster system used together.
Conclusion: Balance of heat, light and cost
Behind every successful LED lighting device are the designers' efforts in terms of power LED temperature and heat loss requirements. These important factors affect the life of the product and its luminous characteristics. A lighting device that operates at a low temperature and emits light that meets the requirements can work longer at the end user.
The MicRED T3Ster automated thermal test system can quickly complete thermal resistance measurements and predict the path of heat transfer within lighting equipment. And the T3Ster and TERALED combined thermal and radiometric/photometric measurement system can obtain the perfect balance between lighting equipment operating temperature, optical performance and cost.
Previous article:Analysis of LED lighting and sensor technology
Next article:Interpretation of various chromaticity processing technologies for LED display screens
Recommended ReadingLatest update time:2024-11-16 22:51
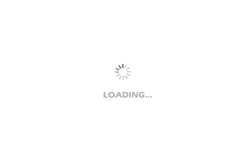
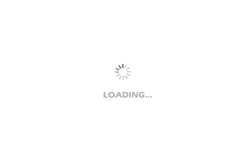
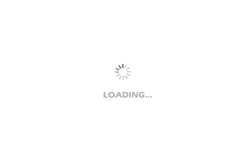
- Popular Resources
- Popular amplifiers
- MathWorks and NXP Collaborate to Launch Model-Based Design Toolbox for Battery Management Systems
- STMicroelectronics' advanced galvanically isolated gate driver STGAP3S provides flexible protection for IGBTs and SiC MOSFETs
- New diaphragm-free solid-state lithium battery technology is launched: the distance between the positive and negative electrodes is less than 0.000001 meters
- [“Source” Observe the Autumn Series] Application and testing of the next generation of semiconductor gallium oxide device photodetectors
- 采用自主设计封装,绝缘电阻显著提高!ROHM开发出更高电压xEV系统的SiC肖特基势垒二极管
- Will GaN replace SiC? PI's disruptive 1700V InnoMux2 is here to demonstrate
- From Isolation to the Third and a Half Generation: Understanding Naxinwei's Gate Driver IC in One Article
- The appeal of 48 V technology: importance, benefits and key factors in system-level applications
- Important breakthrough in recycling of used lithium-ion batteries
- Innolux's intelligent steer-by-wire solution makes cars smarter and safer
- 8051 MCU - Parity Check
- How to efficiently balance the sensitivity of tactile sensing interfaces
- What should I do if the servo motor shakes? What causes the servo motor to shake quickly?
- 【Brushless Motor】Analysis of three-phase BLDC motor and sharing of two popular development boards
- Midea Industrial Technology's subsidiaries Clou Electronics and Hekang New Energy jointly appeared at the Munich Battery Energy Storage Exhibition and Solar Energy Exhibition
- Guoxin Sichen | Application of ferroelectric memory PB85RS2MC in power battery management, with a capacity of 2M
- Analysis of common faults of frequency converter
- In a head-on competition with Qualcomm, what kind of cockpit products has Intel come up with?
- Dalian Rongke's all-vanadium liquid flow battery energy storage equipment industrialization project has entered the sprint stage before production
- Allegro MicroSystems Introduces Advanced Magnetic and Inductive Position Sensing Solutions at Electronica 2024
- Car key in the left hand, liveness detection radar in the right hand, UWB is imperative for cars!
- After a decade of rapid development, domestic CIS has entered the market
- Aegis Dagger Battery + Thor EM-i Super Hybrid, Geely New Energy has thrown out two "king bombs"
- A brief discussion on functional safety - fault, error, and failure
- In the smart car 2.0 cycle, these core industry chains are facing major opportunities!
- The United States and Japan are developing new batteries. CATL faces challenges? How should China's new energy battery industry respond?
- Murata launches high-precision 6-axis inertial sensor for automobiles
- Ford patents pre-charge alarm to help save costs and respond to emergencies
- New real-time microcontroller system from Texas Instruments enables smarter processing in automotive and industrial applications
- Is there anyone who can run the SPI of CH32V103?
- Free gift of old punch card machine (for disassembly and research)
- I need help from an expert to look at the program and tell me how to modify it so that the buzzer can sound three times and then pause for 0.5 seconds before sounding again.
- MSP430G2755 Main Memory Bootloader UART Porting Guide
- McAsp multi-channel understanding
- Please help me look at this oscillator circuit
- About NCP1236 automatic recovery function test after removing short circuit and overload test
- Zigbee IoT module market: Differences between LTE standard Cat.1 and nbiot wireless communication modules
- ADS Installation Issues
- A Brief Discussion on FPGA Resource Evaluation