Driven by the energy-saving and environmental awareness and the latest energy efficiency regulations around the world, improving energy efficiency has become an industry consensus. Compared with hard switching technologies such as flyback, forward, dual-switch flyback, dual-switch forward and full-bridge, soft switching technologies such as dual inductor plus single capacitor (LLC), active clamp flyback, active clamp forward, asymmetric half bridge (AHB) and phase-shifted full bridge can provide higher energy efficiency. Therefore, in applications that focus on high energy efficiency, soft switching technology is increasingly favored by designers.
On the other hand, the half-bridge configuration is best suited for low- to medium-power applications that offer high efficiency/high power density. There are two basic types of MOSFET drivers involved in the half-bridge configuration, high-side and low-side. High-side means that the source of the MOSFET can float between ground and the high-voltage input, while low-side means that the source of the MOSFET is always grounded, see Figure 1. When the high-side switch turns from off to on, the MOSFET source voltage rises from ground to the high-voltage input, which means that the voltage applied to the MOSFET gate must also float up. This requires some form of isolation or floating gate drive circuit. In contrast, the source of the low-side MOSFET is always grounded, so the gate drive voltage can also be referenced to ground, which makes driving the gate of the low-side MOSFET much simpler.
Figure 1: LLC half-bridge topology circuit diagram.
All soft switching topologies use power switches with floating reference pins (such as MOSFET source pins). In the LLC half-bridge topology shown in Figure 1, the high-side MOSFET switch is connected to the high voltage input terminal and cannot be driven by the main power controller. Instead, a separately selected drive circuit is required. This drive circuit is the interface between the control circuit and the power switch, amplifying the control signal to the required level to drive the power switch tube and providing electrical isolation between the power switch tube and the logic level control circuit when required. There are two common high-side MOSFET drive solutions, one is a transformer-based solution, and the other is a silicon integrated circuit (IC) driver-based solution. This article will discuss the design considerations for the high-side MOSFET drive solutions of these two half-bridge topologies, compare the two drive solutions from multiple angles, and provide ON Semiconductor's recommended solutions.
Transformer Drive Solution
The transformer-based high-side MOSFET drive solution involves some important considerations during the design process. For example, since it is a floating drive with a ground reference point, if there is a 400 V power factor correction (PFC) circuit in the design, 500 V isolation must be maintained. In addition, the leakage inductance must be minimized, otherwise the delay between the output and input windings may damage the power MOSFET. Faraday's law must be followed to keep the V*T product constant, otherwise saturation will occur. Sufficient margin must be maintained to prevent saturation, especially in the case of AC high voltage input and transient loads. A high permeability core must be used to minimize the excitation current (IM). The sink current capability must be maintained to enable faster switching speeds.
Transformer-based drive schemes include two main types, namely single drive (DRV) input and dual drive input, see Figure 2a and Figure 2b. In the single drive input scheme, an AC coupling capacitor (CC) is required to reset the flux of the drive transformer. The gate-source voltage (VGS) amplitude in this scheme depends on the duty cycle; in addition, -VC is closed in steady state, and the current sinking capability is limited at startup. This scheme requires a fast time constant (LM//RGS * CC) to prevent flux walking caused by fast transient events. In addition, during the design process, it is also necessary to pay attention to the ringing between the coupling capacitor and the drive transformer during the skip cycle mode or undervoltage lockout (UVLO), and a diode is required to suppress the ringing.
Single drive input includes single drive input with DC recovery and single drive input with PNP shutdown. Among them, the VGS of single drive input with DC recovery depends on the duty cycle in steady state, but the current sinking capability is limited; the latter uses a combination of PNP transistor + diode to help improve the switching off operation. In addition, for single drive input, the AND gate cannot be ignored. If the AND gate driving capability is limited, a totem-pole driver should be added.
Figure 2b shows the circuit diagram of a dual-polarity symmetrical drive input scheme. In this scheme, the two inputs (DRVA and DRVB) are opposite in polarity and symmetrical in position, so unlike the single drive input scheme, no AC coupling capacitor is required. This scheme is suitable for push-pull circuits such as LLC-HB, but not for asymmetrical circuits such as asymmetrical half-bridge or active clamping. This scheme requires attention to the driving transformer flux during line/load transients, and still requires strong turn-off capability. It is necessary to pay attention to the delay caused by leakage inductance, minimize the leakage inductance, and use dual output windings instead of a single output winding. Another disadvantage of this scheme is that the turn-off resistor (Roff) voltage drop will cause additional power loss.
Figure 2: Circuit comparison of transformer drive solutions with single drive input (a) and dual drive input (b).
In general, the transformer drive solution has many advantages. First, the transformer is stronger than the bare chip. Second, it is less sensitive to stray noise and high dV/dt pulses. Of course, the cost may also be cheaper. However, its disadvantage is that the circuit is complex, and it is necessary to pay attention to extreme line/load conditions and shutdown mode, leakage inductance and isolation, and whether the current sinking capability is strong enough.
Silicon chip drive solution
Similar to the transformer drive solution, the silicon integrated circuit drive solution also includes two types: single drive input and dual drive input, as shown in Figure 3a and Figure 3b respectively. However, these silicon half-bridge drivers can be used as both high-side MOSFET drivers and low-side MOSFET drivers. The silicon chip high-side MOSFET drive solution adopts a compact, high-performance package, integrating most of the functions required to drive the high-side MOSFET in a single chip, and can provide fast switching speeds, latch-off functions, and extremely low delay between input commands and gate drive outputs, and low power dissipation after adding a few external components.
Figure 3: Circuit diagram of silicon chip drive solution: a dual input; b single input.
But while providing these advantages, the silicon chip driver solution also has some limitations, such as the voltage inside the silicon chip reaches 600 V, the need for high-side isolation, and the need to match the propagation delay between the high-side driver and the low-side driver to avoid the use of any unbalanced transformer. In addition, the high-side driver requires a bootstrap supply and requires high anti-interference ability to suppress the negative voltage impact of the high-side driver. For high-voltage isolation, it is necessary to add a pulse trigger, a level converter, and a synchronous rectification trigger to the circuit. Among them, the level converter maintains a voltage of up to 600 V. For matching delay, a delay time is added to the low-side driver channel to compensate for the high-side delay caused by the pulse trigger, level converter, and synchronous rectification trigger. As for the negative voltage of the high-side driver, we focus on the half-bridge branch for research. The load connected to the half-bridge branch is an inductive load, similar to the LLC half-bridge, or in the simplest case, a synchronous buck structure. In terms of the actual operation of the buck converter, parasitic parameters such as parasitic inductance and parasitic capacitance are everywhere. The negative voltage on the bridge pin will generate a negative current inside the driver IC, and the negative voltage will increase with each pulse width until the silicon driver (or driver IC) fails. If the negative pulse can be kept in the appropriate area over a wide temperature range, the driver will work properly; otherwise, the driver will not work properly or may be damaged.
ON Semiconductor defines the electrical parameters of driver ICs over the full temperature range of -40°C to +125°C, and the related high-end MOSFET silicon drivers (see Table 1) have strong negative voltage characteristics. In comparison, many competitors only define electrical parameters at an ambient operating temperature of +25°C, do not always provide temperature characterization, and many competitors' electrical parameter values extracted from the characteristic curves are likely to not take into account process variations.
Table 1: ON Semiconductor silicon driver cross-reference for high-side MOSFET driving.
Comparison of solutions and ON Semiconductor recommendations
We use the 24
V@10
A LLC half-bridge circuit
using a transformer drive solution and a silicon driver solution
as examples to compare the two solutions. Both solutions use the LLC controller NCP1395 with dual DRV outputs. The difference is that the former uses a transformer to drive the MOSFET of the LLC converter, while the latter uses the NCP5181 driver IC to drive the MOSFET of the LLC converter. The waveforms of the two look similar, but when comparing the waveforms when the high-side MOSFET is turned off, it can be found that the driver IC turns off the MOSFET faster, and the driver IC turns off the MOSFET 70 ns faster, thereby reducing switching losses; and when the high-side MOSFET is turned on, the driver IC can maintain a safe and sufficient dead time between the high-side and low-side MOSFETs, which is better than the transformer drive solution. In terms of energy efficiency, there is no significant difference in the energy efficiency of the two solutions at the same input power (see Reference 1 for details).
Which of these two solutions should we choose? Actually, both solutions can be used if they are carefully designed. As the leading supplier of high-performance and energy-efficient silicon solutions for green electronics, ON Semiconductor recommends choosing silicon chip driver solutions, because silicon solutions can simplify wiring and design, eliminate the problem of manual insertion of transformers, and eliminate problems such as isolation damage, flux loss, and unexpected ringing after shutdown in transformer solutions. In addition, if slim design is to be supported, the height of the transformer in a flat power supply is a problem, while silicon chip driver solutions do not have this problem.
Summary:
For applications that require high energy efficiency, the half-bridge topology using soft switching technology is increasingly favored by designers. However, to drive the high-side MOSFET in the half-bridge topology, designers are faced with the choice of different driver solutions such as transformers or silicon chips. This article analyzes the design considerations, related issues and solutions of different driver solutions, and compares the two driver solutions from multiple perspectives. Although both drive solutions can work well if carefully designed, ON Semiconductor recommends choosing a silicon chip drive solution such as NCP5181, which can simplify wiring and design while avoiding many problems of transformer drive solutions, helping designers shorten design cycles and speed up product launch.
Previous article:Design of high-power LED driver circuit based on TNY279
Next article:Design of I2C touch screen based on embedded system
Recommended ReadingLatest update time:2024-11-16 16:02
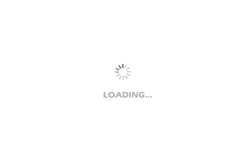
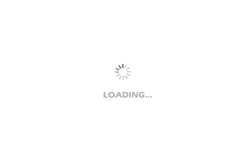
- Popular Resources
- Popular amplifiers
-
Power Electronics Technology 2nd Edition (Li Jie, Chao Xiaojie, Jia Weijuan, Yang Jiayi, Lai Wei)
-
Power Electronics Technology 3rd Edition (Edited by He Yikang and Pan Zaiping)
-
Hand-drawn revealing the basic principles and symbols of electronic circuits
-
Introduction to Transformer Natural Language Processing: Solving Problems with Hugging Face Libraries and Models
- MathWorks and NXP Collaborate to Launch Model-Based Design Toolbox for Battery Management Systems
- STMicroelectronics' advanced galvanically isolated gate driver STGAP3S provides flexible protection for IGBTs and SiC MOSFETs
- New diaphragm-free solid-state lithium battery technology is launched: the distance between the positive and negative electrodes is less than 0.000001 meters
- [“Source” Observe the Autumn Series] Application and testing of the next generation of semiconductor gallium oxide device photodetectors
- 采用自主设计封装,绝缘电阻显著提高!ROHM开发出更高电压xEV系统的SiC肖特基势垒二极管
- Will GaN replace SiC? PI's disruptive 1700V InnoMux2 is here to demonstrate
- From Isolation to the Third and a Half Generation: Understanding Naxinwei's Gate Driver IC in One Article
- The appeal of 48 V technology: importance, benefits and key factors in system-level applications
- Important breakthrough in recycling of used lithium-ion batteries
- Innolux's intelligent steer-by-wire solution makes cars smarter and safer
- 8051 MCU - Parity Check
- How to efficiently balance the sensitivity of tactile sensing interfaces
- What should I do if the servo motor shakes? What causes the servo motor to shake quickly?
- 【Brushless Motor】Analysis of three-phase BLDC motor and sharing of two popular development boards
- Midea Industrial Technology's subsidiaries Clou Electronics and Hekang New Energy jointly appeared at the Munich Battery Energy Storage Exhibition and Solar Energy Exhibition
- Guoxin Sichen | Application of ferroelectric memory PB85RS2MC in power battery management, with a capacity of 2M
- Analysis of common faults of frequency converter
- In a head-on competition with Qualcomm, what kind of cockpit products has Intel come up with?
- Dalian Rongke's all-vanadium liquid flow battery energy storage equipment industrialization project has entered the sprint stage before production
- Allegro MicroSystems Introduces Advanced Magnetic and Inductive Position Sensing Solutions at Electronica 2024
- Car key in the left hand, liveness detection radar in the right hand, UWB is imperative for cars!
- After a decade of rapid development, domestic CIS has entered the market
- Aegis Dagger Battery + Thor EM-i Super Hybrid, Geely New Energy has thrown out two "king bombs"
- A brief discussion on functional safety - fault, error, and failure
- In the smart car 2.0 cycle, these core industry chains are facing major opportunities!
- The United States and Japan are developing new batteries. CATL faces challenges? How should China's new energy battery industry respond?
- Murata launches high-precision 6-axis inertial sensor for automobiles
- Ford patents pre-charge alarm to help save costs and respond to emergencies
- New real-time microcontroller system from Texas Instruments enables smarter processing in automotive and industrial applications
- View Circuit-ADC and System (1)
- Teach you to understand the role of resistors in circuits
- EEWORLD University Hall----High-efficiency power architecture for smart door locks, battery-free light switches and wireless sensors
- 【E840-DTU】TCP connection
- Tank-1 test stand description (for burning and testing ESP8266 series)
- How to implement software reset and restart on HGI MCU
- Understanding digital signal processing
- [SAMR21 New Gameplay] 10. Serial Port Communication-3
- Can you give me an example of how to read the development board data in real time via TCP protocol on PC?
- AC7801 chip serial port printing problem