1 Introduction
With the continuous progress of modern power electronics technology and the development of information technology, inverter power supplies are increasingly widely used in many fields such as communications, navigation, aviation, medical treatment, and military affairs. At the same time, users have higher and higher requirements for the performance of inverter power supplies. As the core of the inverter power supply, the inverter control system plays an extremely critical role in improving the performance of the power supply. The controller of the inverter power supply has experienced the development from analog controller to digital controller. Compared with the analog controller, the digital controller has the advantages of high control accuracy, convenient parameter adjustment, and flexible control strategy change. Especially with the emergence of dedicated control DSP, the control technology of the inverter power supply has developed in the direction of full digitalization, intelligence, and networking. This paper selects the newly launched digital signal processor TMS320F2812 of TI as the main controller of the power supply, and designs a control system with simple structure and convenient expansion to achieve precise control of the inverter power supply.
2 System composition
The power supply designed in this paper is a 400Hz inverter medium frequency power supply. The overall structure of the power supply is shown in Figure 1. The main circuit adopts an AC-DC-AC structure, including components such as a rectifier, a DC filter, an inverter, a transformer, and an AC filter. The AC-DC part converts the 50 Hz AC mains into a stable DC after bridge rectification, a smoothing reactor, and an electrolytic capacitor filter. The bridge rectifier circuit is a semi-controlled structure. The DC-AC inverter part adopts a full-bridge structure, and the inverter uses IGBT as a switching device. Taking advantage of the high switching frequency of the IGBT, the inverter is controlled by a sinusoidal pulse width modulation (SPWM) method to convert the stable DC into an AC output with pulse width modulation. The output SPWM wave has a constant amplitude and a width that changes according to the sinusoidal law. The AC output of the inverter is filtered by a transformer and a filter circuit to obtain a pure sinusoidal AC.
The control part structure with TMS320F2812 as the core is shown in Figure 2. The TMS320F2812 minimum system mainly includes clock circuit, reset circuit and external memory expansion circuit. The clock circuit uses an external clock, and selects a 30MHz crystal oscillator as the external frequency setting. After the external clock is multiplied by PLL, it provides the clock for the system. The system can select the working mode of the phase-locked loop and the multiplication coefficient through the phase-locked loop control register. The design of the reset circuit mainly uses the system reset pin (RS) for the convenience of operation. When the contact switch S is pressed, the pin generates a low level, and the corresponding reset signal will be generated; when the contact switch S is not activated, the pin is high. The external memory expansion circuit mainly uses the high-speed SRAM chip produced by ISSI, model IS61LV25616AL, with a storage time of 10ns, a capacity of 256K bytes, 16 bits, an operating voltage of 3.3V, and works in zero-wait working mode.
Figure 1 Overall structure diagram of power supply
Figure 2 DSP expansion system block diagram
3 Hardware Design
The hardware design of the control system is mainly carried out around the main controller TMS320F2812. The peripheral circuits of TMS320F2812 mainly include AD sampling circuit and SCI communication circuit.
3.1 A/D sampling circuit
The ADC module of TMS320F2812 is a 12-bit pipelined analog-to-digital converter with a total of 16 channels. According to actual needs, this system uses 9 AD conversion channels ADCIN00~ADCIN08, and the signals to be sampled are 3 phase voltages, DC voltage, 3 line currents, DC current, and temperature. Each A/D sampling circuit includes a sensor, an A/D conditioning circuit, and an on-chip A/D converter. The AC voltage sampling circuit is shown in Figure 3. The output three-phase AC voltage is tested for instantaneous value. The sine wave feedback signal sent from the secondary side of the transformer is sampled by the transformer, and after voltage division and bias processing, it is converted into a 0~3.3 V signal and sent to the A/D conversion port of the DSP. There is a synchronization problem between the instantaneous value sampling result of the AC and the detected signal. In this system, the capture unit of TMS320F2812 and the non-maskable interrupt NMI (Non-Maskable Interrupt) are used to realize the AC instantaneous value sampling that tracks the frequency change.
Figure 3 AC voltage sampling circuit
3.2 SCI Circuit
The TMS320F2812 device includes a serial communication interface SCI module, which is a programmable full-duplex serial communication interface. The SCI module supports digital communication between the CPU and its asynchronous peripherals using a standard format. The SCI module includes two pins: the SCI transmit data pin SCITXD and the SCI receive data pin SCIRXD. The serial communication interface circuit of the TMS320F2812 is shown in Figure 4.
Figure 4 Serial communication interface circuit
4 Software Design
4.1 Control strategy
This system adopts a current dual-loop SPWM control modulation scheme with output voltage instantaneous value and inductor current feedback. Among them, the voltage outer loop feedback adopts fuzzy proportional integral regulation, and the feedback signal of the current inner loop is the inductor current IL, which adopts fuzzy proportional regulation [3]. The instantaneous signal U0 of the output voltage is directly fed back after conditioning and sampling to generate Uf, and after comparison with the reference sinusoidal voltage Uref, it is synthesized by the voltage regulator as the given signal Ig of the current inner loop. The error ei obtained by comparing the given signal Ig with the inductor current feedback value If is sent to the current regulator, and the signal Us is generated after P regulation. It is used as a modulation wave to intersect with the triangular carrier to generate an SPWM switching signal to control the conduction and shutdown of each bridge arm IGBT tube.
4.2 Software Implementation
Figure 5 Overall structure flow chart of system software
The SPWM signal of the inverter bridge is implemented by the event manager EVA module on the TMS320F2812 chip. The control and adjustment of the waveform need to be completed in the SPWM adjustment cycle, which belongs to the timer management event. When calculating the voltage regulator and current regulator, it is also necessary to obtain and process the sampled values in real time, and the A/D module on the chip is mainly used here. In addition, the SCI module can be used to communicate with the microcontroller. Various types of protection require continuous query of various state quantities and take corresponding actions according to their specific values. The overall flow chart of the system software is shown in Figure 5.
This system has very high requirements for the real-time processing capability of the software, and most of the functional modules are completed in the interrupt subroutine. Moreover, due to the large number of functional modules in the system, each module should be executed in strict sequence according to the requirements of the system to ensure that the modules do not interfere with each other and work in coordination. There are three main interrupts used: INI2.6 level interrupt is the underflow interrupt of timer 1 of the EVA module. The corresponding interrupt subroutine is the most important one. In this subroutine, the control of the inverter is mainly completed. Once an error occurs, the output of the entire system will be distorted, so its interrupt priority is the highest; INT1.6 level interrupt is the interrupt of the ADC module. In this subroutine, the conversion results of the output voltage and output inductor current are read; INT9.1 level interrupt is the receiving interrupt of the SCI-A module. In this interrupt subroutine, the real-time data after A/D conversion is mainly received.
5 Experimental Results
By building a small-capacity test machine, the design of each link of the control system has been tested in a similar working site. After continuous adjustments during the test process, the software and hardware designs have basically become perfect. The control parameters set for the final large-capacity 30kVA prototype are as follows: input voltage 220V/50Hz, output voltage 115V/400Hz, carrier frequency 18kHz, output power 30kVA, output filter capacitor C = 300 F, output filter inductor L = 70 H. Figures 6 and 7 are the power supply output voltage waveforms for resistive load and inductive load, respectively. After harmonic analysis of the output voltage, the THD value of the output voltage reaches the required performance indicator THD≤3%. The results prove the feasibility of the control system.
Figure 6 Power supply output voltage waveform when resistive load
Figure 7 Power supply output voltage waveform with inductive load
6 Conclusion
This system uses the most advanced TMS320F2812 DSP in the control field as the controller. Compared with the previous single-chip microcomputer, TMS320F2812 has more integrated peripheral functions and faster speed. Moreover, its price has also dropped significantly in recent years. Therefore, the inverter power control system designed in this paper has many advantages such as simple operation, no pollution, low noise, high efficiency, cost saving, easy expansion, etc., and has a good application prospect.
The author's innovation: In view of the user's performance requirements for medium-frequency inverter power supply, the author uses the latest digital signal processor TMS320F2812 in the control field as the controller, and systematically and comprehensively introduces the method of designing an inverter power supply control system from both software and hardware aspects. The hardware circuit of this system is very simple, which realizes the full digital control of the inverter power supply, makes the modularization of the inverter power supply possible, and also lays a good foundation for the large-capacity expansion of the power supply.
Previous article:Design and implementation of ZVS high frequency converter in new microwave oven power supply
Next article:Development of AC voltage stabilized power supply using instantaneous comparison method
Recommended ReadingLatest update time:2024-11-16 17:55
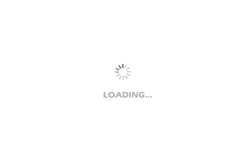
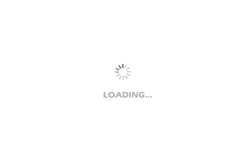
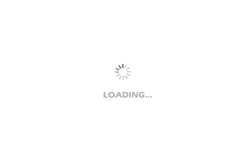
- Popular Resources
- Popular amplifiers
- MathWorks and NXP Collaborate to Launch Model-Based Design Toolbox for Battery Management Systems
- STMicroelectronics' advanced galvanically isolated gate driver STGAP3S provides flexible protection for IGBTs and SiC MOSFETs
- New diaphragm-free solid-state lithium battery technology is launched: the distance between the positive and negative electrodes is less than 0.000001 meters
- [“Source” Observe the Autumn Series] Application and testing of the next generation of semiconductor gallium oxide device photodetectors
- 采用自主设计封装,绝缘电阻显著提高!ROHM开发出更高电压xEV系统的SiC肖特基势垒二极管
- Will GaN replace SiC? PI's disruptive 1700V InnoMux2 is here to demonstrate
- From Isolation to the Third and a Half Generation: Understanding Naxinwei's Gate Driver IC in One Article
- The appeal of 48 V technology: importance, benefits and key factors in system-level applications
- Important breakthrough in recycling of used lithium-ion batteries
- Innolux's intelligent steer-by-wire solution makes cars smarter and safer
- 8051 MCU - Parity Check
- How to efficiently balance the sensitivity of tactile sensing interfaces
- What should I do if the servo motor shakes? What causes the servo motor to shake quickly?
- 【Brushless Motor】Analysis of three-phase BLDC motor and sharing of two popular development boards
- Midea Industrial Technology's subsidiaries Clou Electronics and Hekang New Energy jointly appeared at the Munich Battery Energy Storage Exhibition and Solar Energy Exhibition
- Guoxin Sichen | Application of ferroelectric memory PB85RS2MC in power battery management, with a capacity of 2M
- Analysis of common faults of frequency converter
- In a head-on competition with Qualcomm, what kind of cockpit products has Intel come up with?
- Dalian Rongke's all-vanadium liquid flow battery energy storage equipment industrialization project has entered the sprint stage before production
- Allegro MicroSystems Introduces Advanced Magnetic and Inductive Position Sensing Solutions at Electronica 2024
- Car key in the left hand, liveness detection radar in the right hand, UWB is imperative for cars!
- After a decade of rapid development, domestic CIS has entered the market
- Aegis Dagger Battery + Thor EM-i Super Hybrid, Geely New Energy has thrown out two "king bombs"
- A brief discussion on functional safety - fault, error, and failure
- In the smart car 2.0 cycle, these core industry chains are facing major opportunities!
- The United States and Japan are developing new batteries. CATL faces challenges? How should China's new energy battery industry respond?
- Murata launches high-precision 6-axis inertial sensor for automobiles
- Ford patents pre-charge alarm to help save costs and respond to emergencies
- New real-time microcontroller system from Texas Instruments enables smarter processing in automotive and industrial applications
- DSP28335 - Two cases of copying programs from flash to ram: partial copy and full copy
- LM331 practical application problem help? ?
- Want to learn electronic repair
- 【Silicon Labs Development Kit Review】+ Development Environment Installation and Setup
- 【TI荐课】#Amplifier Protection Series#
- Four Ways to Develop Zynq.docx
- Code statistics of the most popular programming languages on GitHub
- This is a good comprehensive DC information that I have personally read
- [Allwinner V853 heterogeneous AI intelligent vision development board evaluation] Cross-compilation environment settings and applications
- LM2776 output voltage is abnormal