From a technical point of view, there are two main types of LED backlight technology for LCD TVs: side-entry and direct-down. Although each technology has its own advantages, side-lighting LED backlight modules are becoming a mainstream trend when considering aspects such as cost.
The design of side-lighting LED backlight modules should consider reducing costs as much as possible while meeting optical indicators, while also reflecting the light and thin characteristics of side-lighting LED backlight sources. Therefore, the luminous efficiency and color gamut of LEDs have an important influence on the selection of backlight LEDs for LCD TVs. The connection arrangement of LEDs is generally divided into three main structures, namely series connection, parallel connection, and a mixture of series and parallel connection, each of which has its own advantages and disadvantages.
LED series
Advantages: The current is equal everywhere and the LED brightness is basically the same
Disadvantage: If one LED is open, all LEDs will not work.
The advantage of LED series connection is that the LED current is equal throughout the entire series circuit. Because there are batch differences and individual differences in the production process of LEDs, when the consistency of LEDs varies greatly, although the voltages applied to different LEDs are different, the brightness of the LEDs is basically the same because the current passing through each LED is the same. However, the series connection of LEDs also has significant disadvantages. If one of the LEDs is open, then all LEDs will not work. The use of LED series connection requires the LED driver to output a relatively high voltage. Generally, the closer the LED driver output voltage is to the total forward voltage in the series connection, the higher the efficiency of the LED drive. However, the series connection of LEDs requires that the LED voltage output by the driver circuit must be greater than the total LED forward voltage in the series circuit, which also has a slight impact on the system efficiency.
It is worth noting that when a short circuit occurs in the series connection, the constant current control will not have any problems, but the constant voltage control will stop working. When a short circuit occurs in the series connection, both the constant current control and the constant voltage control will have problems, which is a problem that must be paid attention to when designing the drive circuit. When a certain LED is short-circuited due to poor quality or other reasons, if a constant voltage source drive method is used, then since the output voltage of the driver remains unchanged, the voltage distributed across the remaining LEDs will inevitably increase, and the output current of the driver will increase, which may cause damage to all the remaining LEDs. If a constant current LED driver is used, when a certain LED is short-circuited due to poor quality, since the output current of the driver remains unchanged, all the remaining LEDs in this series circuit will work normally. When a certain LED is open-circuited due to poor quality or other faults, all the LEDs connected in series will not light up. A simple way to solve this problem is to connect a Zener diode in parallel across each LED. Of course, the breakdown voltage of the parallel Zener diode needs to be higher than the conduction voltage of the LED, otherwise the LED will not light up. This solution will increase additional power consumption and cost, so it is not suitable for large-scale applications of LEDs.
LEDs in Parallel
Advantages: An open circuit in one LED will not affect the operation of other LEDs
Disadvantage: Requires LED driver to output larger current
When the current of each LED needs to be adjusted individually, a common anode or common cathode parallel connection method is used. The advantage of the parallel method is that when one LED is in an open circuit state, it will not affect the operation of other LEDs. Its disadvantage is that it requires the LED driver to output a larger current. Since the parallel method distributes the same voltage across all LEDs, when the consistency of the LEDs varies greatly, the current passing through each LED will be inconsistent, and the brightness of the LED will also be significantly different. Due to the limitations of LED manufacturing technology, this difference is inevitable. Therefore, when the LED is working, the uneven current distribution of each LED due to the inherent disadvantages of the parallel method may cause the LED with excessive current to have a sharp reduction in life or even burn out.
When a certain LED is short-circuited, if a constant voltage source LED driver is used, the output current of the driver circuit will decrease, and all the remaining LEDs can still work normally. If a constant current source is used for LED driving, since the output current of the driver circuit remains unchanged, the current allocated to the remaining LEDs will increase, which may cause damage to the remaining LEDs. The solution to this problem is to connect as many LEDs in parallel as possible. When a certain LED is short-circuited, the current increment of the remaining LEDs is not large, and it will not affect the normal operation of the remaining LEDs too much. Therefore, when LEDs are connected in parallel, it is not suitable to use a constant current source for driving. When a certain LED is short-circuited, all the remaining LEDs will not work. But there is a special case. If the number of LEDs connected in parallel is large, the current passing through the short-circuited LED is large, and the instantaneous heat will burn the short-circuited LED into a short circuit, then the remaining LEDs can still work.
LED Hybrid
Advantages: Comprehensively reflects the advantages of series and parallel
Disadvantages: more complex design
In products that require a large number of LEDs, if only LEDs are connected in series, the LED driver circuit will need to output a higher voltage. If only LEDs are connected in parallel, the LED driver circuit will need to output a larger current. Simply connecting all LEDs in series or in parallel will not only limit the amount of LEDs used, but will also increase the complexity of the drive circuit design and the cost. Usually, a hybrid connection is used to solve this problem. The hybrid connection method is proposed based on the advantages of both series and parallel connections. There are two main forms: series connection first and then parallel connection, and parallel connection first and then series connection.
The number of LEDs in series and parallel is evenly distributed, and the voltage distributed on a string of LEDs is the same. The current passing through each LED in the same string is also basically the same, and the LED brightness is consistent. At the same time, the current passing through each string of LEDs is also similar. When one LED in a series is short-circuited, regardless of whether a voltage-stabilized drive or a constant-current drive is used, this string of LEDs is equivalent to one LED less, and the current passing through this string of LEDs will increase greatly, which can easily damage this string of LEDs. After a large current passes through the damaged string of LEDs, it often appears as a circuit breaker due to the large current passing through. After disconnecting a string of LEDs, if a voltage-stabilized drive is used, the output current of the driver will decrease without affecting the normal operation of all the remaining LEDs.
If a constant-current LED driver is used, since the output current of the driver remains unchanged, the current distributed to the remaining LEDs will increase, which can easily damage all the remaining LEDs. The solution is to connect as many LEDs in parallel as possible. When a certain LED is disconnected, the current distributed to the remaining LEDs is not large, so as not to affect the normal operation of the remaining LEDs. There is another way to connect the parallel-parallel mode, which is to evenly distribute the LEDs, connect them in parallel, and then connect each group in series. When one LED is short-circuited, no matter whether it is a voltage-stabilized drive or a constant-current drive, all the LEDs connected in parallel will not light up. If a constant-current LED drive is used, since the output current of the driver remains unchanged, the remaining LEDs will work normally except for the parallel branch connected in parallel with the short-circuited LED. Assuming that there are a large number of LEDs in parallel, the drive current of the driver is large, and the current through the short-circuited LED will increase. After the large current passes through the short-circuited LED, it is easy to become a short circuit. Since there are many LEDs in parallel, disconnecting the parallel branch of one LED will not distribute the current evenly, and it can still work normally, then only one of all the LEDs will not light up. If a voltage-stabilized drive is used, at the moment when the LED is short-circuited, the load end is equivalent to losing one parallel LED, and the voltage applied to the remaining LEDs increases, and the output current of the driver will increase greatly, which is likely to damage all LEDs immediately, or it is possible to burn only the short-circuited LED into a short circuit, and the output current of the driver will return to normal. Since there are many LEDs connected in parallel, the average current increment of this parallel branch after disconnecting one LED is not large, and it can still work normally, and only one LED in the entire LED array is not lit.
The selection of the driver and the load LED series-parallel mode is very important. Constant current driving power LED is not suitable for parallel load but for series load. Similarly, constant voltage LED driver is not suitable for series load but for parallel connection. Different connection methods have different characteristics and different requirements for the driver. Especially when the circuit is working in the case of a single LED failure, the reliability of the overall light emission, the ability of the entire group of LEDs to continue to work, and the reduction of damage and LED failure rate are very important.
The use of different LED connection methods is crucial for the use of LEDs and the design requirements of the drive circuit. Therefore, in the actual combination of backlight circuits, the correct selection of LED connection methods has a positive significance for improving its luminous effect, working reliability, simplifying the design and processing of the drive circuit, and improving the efficiency of the entire circuit. For LED backlight LCD TVs, it is very important to ensure its viewing life, so how to ensure the reliability of the backlight is a key factor.
Previous article:White LED driver analysis and application
Next article:Introduction to LED epitaxial wafers and methods for identifying quality
Recommended ReadingLatest update time:2024-11-16 19:43
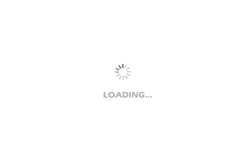
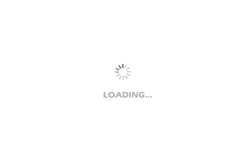
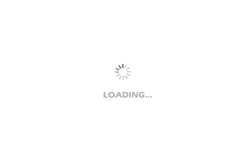
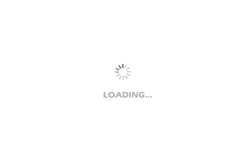
- Popular Resources
- Popular amplifiers
- MathWorks and NXP Collaborate to Launch Model-Based Design Toolbox for Battery Management Systems
- STMicroelectronics' advanced galvanically isolated gate driver STGAP3S provides flexible protection for IGBTs and SiC MOSFETs
- New diaphragm-free solid-state lithium battery technology is launched: the distance between the positive and negative electrodes is less than 0.000001 meters
- [“Source” Observe the Autumn Series] Application and testing of the next generation of semiconductor gallium oxide device photodetectors
- 采用自主设计封装,绝缘电阻显著提高!ROHM开发出更高电压xEV系统的SiC肖特基势垒二极管
- Will GaN replace SiC? PI's disruptive 1700V InnoMux2 is here to demonstrate
- From Isolation to the Third and a Half Generation: Understanding Naxinwei's Gate Driver IC in One Article
- The appeal of 48 V technology: importance, benefits and key factors in system-level applications
- Important breakthrough in recycling of used lithium-ion batteries
- Innolux's intelligent steer-by-wire solution makes cars smarter and safer
- 8051 MCU - Parity Check
- How to efficiently balance the sensitivity of tactile sensing interfaces
- What should I do if the servo motor shakes? What causes the servo motor to shake quickly?
- 【Brushless Motor】Analysis of three-phase BLDC motor and sharing of two popular development boards
- Midea Industrial Technology's subsidiaries Clou Electronics and Hekang New Energy jointly appeared at the Munich Battery Energy Storage Exhibition and Solar Energy Exhibition
- Guoxin Sichen | Application of ferroelectric memory PB85RS2MC in power battery management, with a capacity of 2M
- Analysis of common faults of frequency converter
- In a head-on competition with Qualcomm, what kind of cockpit products has Intel come up with?
- Dalian Rongke's all-vanadium liquid flow battery energy storage equipment industrialization project has entered the sprint stage before production
- Allegro MicroSystems Introduces Advanced Magnetic and Inductive Position Sensing Solutions at Electronica 2024
- Car key in the left hand, liveness detection radar in the right hand, UWB is imperative for cars!
- After a decade of rapid development, domestic CIS has entered the market
- Aegis Dagger Battery + Thor EM-i Super Hybrid, Geely New Energy has thrown out two "king bombs"
- A brief discussion on functional safety - fault, error, and failure
- In the smart car 2.0 cycle, these core industry chains are facing major opportunities!
- The United States and Japan are developing new batteries. CATL faces challenges? How should China's new energy battery industry respond?
- Murata launches high-precision 6-axis inertial sensor for automobiles
- Ford patents pre-charge alarm to help save costs and respond to emergencies
- New real-time microcontroller system from Texas Instruments enables smarter processing in automotive and industrial applications
- Crazy Shell AI open source drone GPIO (remote control indicator light control)
- Where can I get an evaluation board for Toshiba's rice-sized Bluetooth module?
- 16. Low-power intelligent TWS in-ear detection chip VK233DS, Shenzhen Yongjia Microelectronics is the first choice
- [Atria AT32WB415 Series Bluetooth BLE 5.0 MCU] PWM breathing light
- 30V8A stepper motor driver, step angle 1.8 degrees, required accuracy 0.1 degrees, should I choose chip or H bridge
- Can the 66AK2L06 SoC enable miniaturization of test and measurement equipment?
- Circuit diagram of leakage alarm automatic control socket
- How to detect mosquitoes using ultrasonic sensor circuit
- 2021 National College Student Electronics Competition Released
- Share the application manuals, library functions, routines and selection tables of the full range of MM32 MCU products of Lingdong Microelectronics