The production process of epitaxial wafers is very complicated. After the epitaxial wafers are developed, nine points are randomly selected from each epitaxial wafer for testing. The ones that meet the requirements are good products, and the others are defective products (large voltage deviation, short or long wavelength, etc.). Good epitaxial wafers will start to make electrodes (P pole, N pole), and then use laser to cut the epitaxial wafers, and then pick them up 100%, and conduct fully automated sorting according to different voltages, wavelengths, and brightness, that is, forming LED chips (square wafers). Then visual inspection is required to sort out those with a little defect or worn electrodes. These are the scattered crystals behind. At this time, there are wafers on the blue film that do not meet the normal shipping requirements, and they naturally become edge wafers or rough wafers. Defective epitaxial wafers (mainly some parameters do not meet the requirements) are not used to make square wafers, but directly make electrodes (P pole, N pole), and no sorting is done, which is the large LED wafers currently on the market (there are also good things here, such as square wafers, etc.).
Semiconductor manufacturers mainly use polished Si wafers (PW) and epitaxial Si wafers as raw materials for ICs. Epitaxial wafers were used in the early 1980s because they have certain electrical properties that standard PW does not have and eliminate many surface/near-surface defects introduced during crystal growth and subsequent wafer processing.
Historically, epitaxial wafers are produced by Si wafer manufacturers for their own use. They are not used in large quantities in ICs. They require a thin single-crystal Si layer to be deposited on the surface of a single-crystal Si wafer. The thickness of the epitaxial layer is generally 2 to 20 μm, while the thickness of the substrate Si is 610 μm (150 mm diameter wafer) and 725 μm (200 mm wafer).
Epitaxial deposition can be done both in multiple wafers at once (simultaneously) and in single wafers. Single wafer reactors produce the best quality epitaxial layers (good uniformity of thickness and resistivity, few defects); these epitaxial wafers are used in the production of 150 mm "leading edge" products and all important 200 mm products.
Epitaxial products
Epitaxial products are used in four areas. CMOS complementary metal oxide semiconductors support cutting-edge processes that require small device sizes. CMOS products are the largest application area for epitaxial wafers and are used by IC manufacturers for non-recoverable device processes, including microprocessors and logic chips, as well as flash memory and DRAM (dynamic random access memory) for memory applications. Discrete semiconductors are used to manufacture components that require precise Si characteristics. The "exotic" semiconductor category includes some special products that use non-Si materials, many of which use compound semiconductor materials incorporated into the epitaxial layer. Buried layer semiconductors use heavily doped regions in bipolar transistor components for physical isolation, which are also deposited during epitaxial processing.
Currently, epitaxial wafers account for one-third of 200 mm wafers. In 2000, including buried layers, CMOS for logic devices accounted for 69% of all epitaxial wafers, DRAM accounted for 11%, and discrete devices accounted for 20%. By 2005, CMOS logic will account for 55%, DRAM accounted for 30%, and discrete devices accounted for 15%.
LED epitaxial wafer--substrate material
Substrate materials are the cornerstone of the development of semiconductor lighting industry technology. Different substrate materials require different epitaxial growth technologies, chip processing technologies, and device packaging technologies. Substrate materials determine the development path of semiconductor lighting technology. The choice of substrate materials mainly depends on the following nine aspects:
[1] Good structural characteristics: the crystal structure of the epitaxial material and the substrate is the same or similar, the lattice constant mismatch is small, the crystallization performance is good, and the defect density is small;
[2] Good interface properties, conducive to the nucleation of epitaxial materials and strong adhesion;
[3] Good chemical stability, not easy to decompose and corrode in the temperature and atmosphere of epitaxial growth;
[4] Good thermal properties, including good thermal conductivity and small thermal mismatch;
[5] Good electrical conductivity, can be made into up and down structures;
[6] Good optical performance, the light emitted by the device is less absorbed by the substrate;
[7] Good mechanical properties, the device is easy to process, including thinning, polishing and cutting;
[8] Low price;
[9] Large size, generally required to be no less than 2 inches in diameter.
It is very difficult to select a substrate that meets all the above nine aspects at the same time. Therefore, at present, the only way to adapt to the research and development and production of semiconductor light-emitting devices on different substrates is to change the epitaxial growth technology and adjust the device processing technology. There are many substrate materials used for gallium nitride research, but there are currently only three substrates that can be used for production, namely sapphire Al2O3, silicon carbide SiC substrate and Si substrate.
The following factors must be considered comprehensively when evaluating substrate materials:
1. Structural matching between substrate and epitaxial film: the crystal structure of epitaxial material and substrate material is the same or similar, the lattice constant mismatch is small, the crystallization performance is good, and the defect density is low;
2. Matching of thermal expansion coefficients between substrate and epitaxial film: Matching of thermal expansion coefficients is very important. If the thermal expansion coefficients between epitaxial film and substrate material differ too much, it may not only reduce the quality of epitaxial film, but also damage the device due to heat during device operation.
3. The chemical stability of the substrate and the epitaxial film should match: the substrate material should have good chemical stability, not easy to decompose and corrode in the temperature and atmosphere of epitaxial growth, and the quality of the epitaxial film should not be reduced due to chemical reaction with the epitaxial film;
4. Difficulty and cost of material preparation: Considering the needs of industrial development, the preparation of substrate materials should be simple and the cost should not be very high. The substrate size is generally not less than 2 inches.
There are many substrate materials used for GaN-based LEDs, but only three types of substrates can be used for commercialization, namely sapphire, silicon carbide and silicon substrates. Other substrates such as GaN and ZnO are still in the research and development stage and are still some distance away from industrialization.
Gallium Nitride:
The most ideal substrate for GaN growth is GaN single crystal material, which can greatly improve the crystal quality of epitaxial film, reduce dislocation density, increase device life, improve luminous efficiency, and increase device operating current density. However, it is very difficult to prepare GaN single crystals, and there is no effective method so far.
Zinc Oxide:
The reason why ZnO can become a candidate substrate for GaN epitaxy is that the two have very striking similarities. The two have the same crystal structure, very small lattice recognition, and similar bandgap width (small band discontinuity value and small contact barrier). However, the fatal weakness of ZnO as a GaN epitaxial substrate is that it is easy to decompose and corrode in the temperature and atmosphere of GaN epitaxial growth. At present, ZnO semiconductor materials cannot be used to manufacture optoelectronic devices or high-temperature electronic devices, mainly because the material quality does not meet the device level and the P-type doping problem has not been truly solved. Equipment suitable for the growth of ZnO-based semiconductor materials has not yet been successfully developed.
sapphire:
The most common substrate for GaN growth is Al2O3. Its advantages are good chemical stability, no absorption of visible light, moderate price, and relatively mature manufacturing technology. Although poor thermal conductivity does not expose obvious deficiencies when the device is working at low current, it is a very prominent problem when the power device is working at high current.
Silicon Carbide:
SiC is second only to sapphire in the wide application of substrate materials. At present, Professor Jiang Fengyi of Jingneng Optoelectronics in China has grown LED epitaxial wafers that can be used for commercialization on Si substrates. Si substrates are superior to sapphire in thermal conductivity and stability, and their prices are much lower than sapphire. They are a very promising substrate. SiC substrates have good chemical stability, good electrical conductivity, good thermal conductivity, and do not absorb visible light, but their shortcomings are also prominent. For example, the price is too high, the crystal quality is difficult to reach the same level as Al2O3 and Si, and the mechanical processing performance is relatively poor. In addition, SiC substrates absorb ultraviolet light below 380 nanometers and are not suitable for the development of ultraviolet LEDs below 380 nanometers. Due to the beneficial electrical and thermal conductivity of SiC substrates, the heat dissipation problem of power-type GaN LED devices can be better solved, so they occupy an important position in the field of semiconductor lighting technology.
Compared with sapphire, the lattice matching between SiC and GaN epitaxial film is improved. In addition, SiC has blue luminescence characteristics and is a low-resistance material that can be used to make electrodes, making it possible to fully test the epitaxial film before packaging the device, enhancing the competitiveness of SiC as a substrate material. Since SiC's layered structure is easy to cleave, a high-quality cleavage surface can be obtained between the substrate and the epitaxial film, which will greatly simplify the structure of the device; but at the same time, due to its layered structure, steps often appear on the surface of the substrate that introduce a large number of defects to the epitaxial film.
To achieve the goal of luminous efficiency, we must rely on GaN substrate LEDs to achieve low cost, and also use GaN substrates to achieve high efficiency, large area, single lamp high power, and drive the simplification of process technology and greatly improve the yield rate. Once semiconductor lighting becomes a reality, its significance is no less than Edison's invention of the incandescent lamp. Once breakthroughs are made in key technical fields such as substrates, its industrialization process will make great progress.
Previous article:LED connection arrangement directly affects the backlight performance
Next article:Easy to modify LED light sequence circuit design without processor intervention
Recommended ReadingLatest update time:2024-11-16 17:46
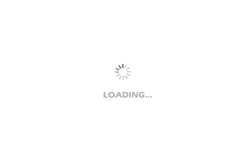
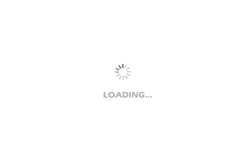
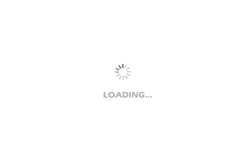
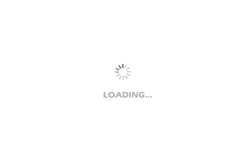
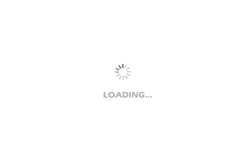
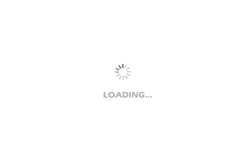
- Popular Resources
- Popular amplifiers
- MathWorks and NXP Collaborate to Launch Model-Based Design Toolbox for Battery Management Systems
- STMicroelectronics' advanced galvanically isolated gate driver STGAP3S provides flexible protection for IGBTs and SiC MOSFETs
- New diaphragm-free solid-state lithium battery technology is launched: the distance between the positive and negative electrodes is less than 0.000001 meters
- [“Source” Observe the Autumn Series] Application and testing of the next generation of semiconductor gallium oxide device photodetectors
- 采用自主设计封装,绝缘电阻显著提高!ROHM开发出更高电压xEV系统的SiC肖特基势垒二极管
- Will GaN replace SiC? PI's disruptive 1700V InnoMux2 is here to demonstrate
- From Isolation to the Third and a Half Generation: Understanding Naxinwei's Gate Driver IC in One Article
- The appeal of 48 V technology: importance, benefits and key factors in system-level applications
- Important breakthrough in recycling of used lithium-ion batteries
- Innolux's intelligent steer-by-wire solution makes cars smarter and safer
- 8051 MCU - Parity Check
- How to efficiently balance the sensitivity of tactile sensing interfaces
- What should I do if the servo motor shakes? What causes the servo motor to shake quickly?
- 【Brushless Motor】Analysis of three-phase BLDC motor and sharing of two popular development boards
- Midea Industrial Technology's subsidiaries Clou Electronics and Hekang New Energy jointly appeared at the Munich Battery Energy Storage Exhibition and Solar Energy Exhibition
- Guoxin Sichen | Application of ferroelectric memory PB85RS2MC in power battery management, with a capacity of 2M
- Analysis of common faults of frequency converter
- In a head-on competition with Qualcomm, what kind of cockpit products has Intel come up with?
- Dalian Rongke's all-vanadium liquid flow battery energy storage equipment industrialization project has entered the sprint stage before production
- Allegro MicroSystems Introduces Advanced Magnetic and Inductive Position Sensing Solutions at Electronica 2024
- Car key in the left hand, liveness detection radar in the right hand, UWB is imperative for cars!
- After a decade of rapid development, domestic CIS has entered the market
- Aegis Dagger Battery + Thor EM-i Super Hybrid, Geely New Energy has thrown out two "king bombs"
- A brief discussion on functional safety - fault, error, and failure
- In the smart car 2.0 cycle, these core industry chains are facing major opportunities!
- The United States and Japan are developing new batteries. CATL faces challenges? How should China's new energy battery industry respond?
- Murata launches high-precision 6-axis inertial sensor for automobiles
- Ford patents pre-charge alarm to help save costs and respond to emergencies
- New real-time microcontroller system from Texas Instruments enables smarter processing in automotive and industrial applications
- I bought a polymer lithium battery (3.7V10A, 1C) on TB. Can I use TP4056 or IP5305, IP5306 module to charge and discharge it?
- Courseware Collection|Tektronix Semiconductor Materials and Devices Seminar (2019-2018)
- RaspberryPi Pico To-Do Board using Micropython
- TTP223_BA6 uses non-isolated power supply + inverter and the lower button fails
- 【TI Recommended Course】#TI.com Online Purchasing Special: Smart Buildings#
- Filtering and Signal Processing Reference Design for MSP430 FRAM Microcontrollers
- [Chuanglong TLT3-EVM Development Board Review] From Development Board to PLC
- This article explains the process of Keil compiling a program
- Support EEWorld 19 Growth Plan and win wonderful gifts!
- Qorvo has launched a series of articles on motor science. Let’s take a look.