LEDs for lighting applications today have the brightness, efficiency, lifespan, color temperature, and white point stability required for general lighting. Therefore, these LEDs are used in the vast majority of general lighting application designs, including pavement, parking areas, and indoor directional lighting. In these applications, LED-based lighting reduces the total cost of ownership (TCO) due to the lack of maintenance (because LEDs have a much longer lifespan than traditional bulbs) and reduced energy consumption.
There are more than 20 billion light fixtures in the world that use incandescent, halogen or fluorescent lamps. Many of these fixtures are used for directional lighting, but they all use lamps that emit light in all directions. According to the U.S. Department of Energy (DOE), recessed ceiling lights are the most commonly installed lighting fixtures in new residential construction. In addition, the DOE reports that recessed ceiling lights that use non-reflector lamps are generally only 50% efficient, which means that half of the light produced by these lamps is wasted in the fixture.
In contrast, lighting-class LEDs provide efficient, directional illumination for at least 50,000 hours. Indoor lighting designed to take advantage of all the benefits of lighting-class LEDs has the following advantages:
1 More efficient than all incandescent and halogen lamps
2 Comparable performance to even the best CFL (compact fluorescent) downlights
3 Compared to these lamps, the life span before maintenance is 5 to 50 times longer
4 Reduce the impact of light on the environment: no mercury, less pollution from power stations, and low waste disposal costs.
Lighting or lamp?
Designing LEDs in general lighting requires a choice between two approaches: designing a complete LED-based lighting or designing an LED-based lamp that fits into an existing fixture. Generally speaking, a complete lighting design will have better optical, thermal, and electrical performance than a retrofit lamp because the existing fixture does not constrain the design. It is up to the designer to decide whether the overall system performance of the new lighting or the convenience of the retrofit lamp is more important for the target application.
Design method for existing lighting
If the target application is better suited to constructing new LED lighting, then designing the lighting to match or exceed the light output of existing lighting has multiple advantages. First, the existing design has been optimized for the target application and can provide guidance when determining design goals around light output, cost, and operating environment. Second, the form factor of the existing design is already recognized. If the form factor is the same, it is easier for the end user to convert to LED lighting.
Unfortunately, some LED lighting manufacturers have misreported or exaggerated the efficiency and life characteristics of LED lighting. The lighting industry encountered similar problems in the early years when CFL replaced light bulbs. The lack of industry standards and the huge differences in the quality of early products delayed the adoption of CFL technology for many years. The U.S. Department of Energy realized that the same standards and quality issues may exist in early LED lighting, and these problems may have delayed the use of LED lighting in a similar way. In response, the U.S. Department of Energy launched the "DOE SSL Commercial Product Testing Program (CPTP)" to test the indicators claimed by LED lighting manufacturers. The program anonymously tests the following four characteristics of LED lighting: lighting light output (lumens),
Lighting efficacy (lumens per watt), correlated color temperature (degrees Kelvin), color rendering index.
DOE's CPTP sets a good precedent for LED lighting design by focusing on the available light output of the lighting, rather than just the light output of the lighting.
The concept of lamp may be outdated
LED light has a long lifespan that could make the concept of a lamp obsolete. Lighting-class LEDs do not fail catastrophically like light bulbs. Instead, lighting-class LEDs have a lifespan of at least 50,000 hours before gradually degrading to 70% of their initial light output flux (also known as lumen maintenance), which translates to 5.7 years of continuous lighting!
However, in most lighting environments, the lights are turned off regularly. This off period can extend the life of the LED to more than 30 years, as shown in curve 1. After so many years, the LED lighting will "burn out", and at that time, the lighting under LED lighting technology will be brighter and more efficient, and it is likely to save TCO compared with the old LED lighting.
Don't forget: Those 50,000 hours of LED lighting life saves a lot of environmental impact. At least 25 times fewer incandescent bulbs are sent to landfills, and use 5 times less energy. (About 50% of energy in the U.S. comes from burning coal, which releases mercury into the air.) Or, at least 5 times fewer C bulbs containing mercury are sent for disposal.
As mentioned earlier, the lack of maintenance is a key benefit of LED lighting. Therefore, designing LED lighting to maximize its lifespan and save TCO is an excellent strategy to address the obstacle of high initial cost of LED lighting.
Table 1 lists the general steps for designing high-power LED lighting. The rest of this article discusses these design steps in turn. To better illustrate these design concepts, this article gives a calculation example of replacing a 23W CFL recessed ceiling lamp with LED lighting. This design step can be repeated not only for this example, but for all types of lighting.
Step 1: Determine lighting needs
LED lighting must meet or exceed the lighting requirements of the target application. Therefore, the lighting requirements must be determined before the design goals are established. For some applications, there are existing lighting standards that can directly determine the requirements. For other applications, determining the characteristics of existing lighting is a good approach.
Table 2 lists the key characteristics to consider when characterizing existing lighting. Light output and power characteristics are always critical, while other characteristics may or may not be important depending on the application.
All lighting companies can provide data files or documents detailing the key characteristics of their various luminaires. "Potentially critical" characteristics are more subjective or are not listed in the manufacturer's documentation. In this case, it is up to the designer to determine the characteristics of the existing lighting.
Figure 1 illustrates the key features of the CFL downlight example.
Table 3 gives the full characteristics of the existing lighting.
Step 2: Determine the design goals
Once the lighting requirements are determined, the design goals for LED lighting can be determined. As with defining lighting requirements, key design goals are related to light output and power consumption. Make sure to include other design goals that may also be important for the target application, including operating environment, bill of materials (BOM) cost, and service life.
Table 4 lists the design goals using LED lighting as an example.
Step 3: Estimate the efficiency of the optical, thermal, and electrical systems
One of the most important parameters in the design process is how many LEDs are needed to meet the design goals. Other design decisions revolve around the number of LEDs, as the number of LEDs directly affects light output, power consumption, and lighting costs.
It is tempting to look at the typical luminous flux listed in the LED data sheet and divide the design target lumens by that number. However, this approach is too simplistic and the design will not meet the lighting requirements of the application.
The luminous flux of an LED depends on many factors, including drive current and junction temperature. To accurately calculate the required amount, you must first estimate the inefficiencies of the optical, thermal, and electrical systems. Personal experience from previous prototype designs, or the example quantities provided in this article, can be used as a guide to estimate these losses. This section briefly describes the process of estimating these system losses.
Optical system efficiency
The efficiency of an optical system is estimated by examining the light losses. The two main sources of light losses to estimate are:
1. Secondary optics
Secondary optics are all optical systems that are not part of the LED itself, such as lenses or diffusers on the LED. The losses associated with secondary optics vary depending on the specific components used. Typical optical efficiency through various secondary optical components is between 85% and 90%.
2. Light loss in the lamp
Lamp light loss occurs when light hits the lamp housing before reaching the target object. Some of the light is absorbed by the lamp housing and some is reflected back to the lamp. The efficiency of the fixture is determined by the layout of the lighting, the shape of the lamp housing and the material of the lamp housing. As shown in Figure 2, LED light is directional and can achieve much higher efficiency than is possible with omnidirectional lighting.
For the example lighting, there is only secondary light loss if the lighting requires secondary optics. The main purpose of secondary optics is to change the light output image of the LED. Curve 2 compares the beam angle of the Cree XLamp XR-E LED to the light output image of the target luminaire. The beam angle of the bare LED is very similar to that of the target luminaire, so secondary optics are not needed. Therefore, for this example lighting, there is no light loss due to secondary optics.
To calculate the luminaire loss for this CFL example, we assume that the luminaire reflector cup has a reflectivity of 85% and 60% of the light will hit the reflector cup. Therefore, the optical efficiency is:
Heat loss
The relative flux output of an LED decreases as the junction temperature increases. Most LED data sheets list typical luminous flux values at 25°C, while most LED applications use higher junction temperatures. When the junction temperature Tj > 25°C, the luminous flux will definitely be worse than the value given in the LED data sheet.
LED data sheets include a curve that gives the relative light output versus junction temperature, such as the XLamp XR-E white LED shown in Curve 3. The curve gives other characteristic values by selecting a specific relative light output or a specific junction temperature.
For this CFL example, the lighting is designed for a commercial building with roof ventilation only. This design prioritizes light output, efficacy, and lifetime based on the listed design goals.
XLamp XR-E LEDs are rated to provide an average lumen maintenance of 70% after 50,000 hours with a junction temperature at or below 80°C. Therefore, the maximum suitable junction temperature for the CFL example is 80°C. The corresponding minimum relative luminous flux is 85%, as shown in Curve 3. This 85% relative luminous flux is an estimate of the thermal efficacy of the lighting in this example.
Electrical loss
LED driver electronics convert an available power source, such as AC from a wall outlet or a battery, into a regulated current source. This process, like all power sources, is not 100% efficient. Electrical losses in the driver reduce the overall lighting efficacy because the input power is wasted as heat rather than light. Electrical losses should be considered when you start designing an LED system.
Typical LED drivers have efficiencies between 80% and 90%. Drivers with efficiencies above 90% cost significantly more. Note that driver efficiency can vary with output load, as shown in Curve 4. Drivers should be specified for operation at greater than 50% output load to maximize efficiency and minimize cost.
Curve 4 shows the relationship between LED driver efficiency and load.
For indoor applications, an estimate of 87% driver efficiency is a good estimate. Drivers used outdoors or for very long lifetimes may have lower efficiencies.
Table 5 summarizes the efficiencies of the optical, thermal, and electrical systems of the example lighting.
Step 4: Calculate the number of LEDs needed
Actual lumens required
Once all system efficiencies are estimated, the actual number of LED lumens required to achieve the design goals can be calculated. For this calculation, only the optical efficiency (optical and thermal) is used. The electrical efficiency only affects the total power consumption and lamp efficacy, not the amount of light output of the lighting. The calculation for the "actual lumens required" for the example lighting is as follows:
Actual lumens required = target lumens / (optical efficiency × thermal efficiency) = 810 / (91% × 85%) = 1,050lm
Working current
Another thing to determine is the operating current of the LED. The operating current is important in determining the efficacy and life of LED lighting. Increasing the operating current increases the light output of each LED, thereby reducing the number of LEDs required. However, increasing the operating current also brings several disadvantages, as shown in Table 6. Depending on the application, these disadvantages may be acceptable in consideration of the higher lumen output per LED.
For the example luminaire, life and efficacy were the top design priorities and the luminaire was operated at the minimum operating current listed in the XLamp XR-E data sheet (350 mA) to maximize LED efficacy and lifetime.
Number of LEDs
After the operating current is determined, the lumen output of each LED can be calculated. Since the heat loss of the LED has been taken into account in the calculation of the actual required lumen number, the number given in the LED supplier's documentation can be used directly.
For this calculation, use the minimum flux listed for the LED order code rather than the typical number given in the data sheet. Most LED companies sell based on a minimum flux range. Designing to this minimum number ensures that all lighting made with that LED order code will meet the target requirements.
The lighting in this example uses XLamp XR-E LEDs with a 4000K CCT and a minimum luminous flux of 67.2 at 350 mA (P2 flux bin). The number of LEDs is calculated as follows.
Number of LEDs = Actual lumens required / Lumens per LED = 1,050 lm / 67.2 lm = 16 LEDs
Step 5: Consider all possible designs and choose the best one
After the LED count is calculated, consider all possible designs that meet the design goals. Since each LED is a small lighting fixture with a much longer lifespan than traditional lighting, LEDs can be integrated into lighting with new and unconventional design elements. Designers can take full advantage of the directionality of LED light and the large number of available secondary optics to construct original designs.
At the same time, don’t forget that there are many different regulations that constrain design choices. Giving a complete list of worldwide standards that apply to LED lighting is beyond the scope of this article, however, Table 7 below gives examples of regulations used in some parts of the world.
The rest of this section describes the three options for each system (optical, thermal, and electrical) of this example LED lighting. For each system, a guide to selecting the best option is given.
Optical system options
1. Bare LED and existing lamp reflector
As mentioned previously, the angles of existing CFL fixtures are very similar to those of LEDs, so there is an option to not use secondary optics. This option provides the lowest cost and minimal light loss in the system. Fewer components and less labor are used, making the lighting installation simpler and less expensive.
The disadvantage is that multiple lighting shadow effects will occur, which will be explained below. In addition, this method cannot be used if the light distribution of the LED is very different from the light distribution of the target lighting.
2. LED with secondary optics and existing lamp reflector
Secondary optics are additional optical components in addition to the LED primary optics that are used to shape the light output of the LED. Common types of secondary optics are reflective (light bounces off a surface) or refractive (light is bent through a refractive material, usually glass or plastic). Secondary optics can be purchased as standard, off-the-shelf parts, or designed custom using ray tracing simulations with illumination models.
Using a secondary optic for each LED, the beam angle of each LED can be tailored to produce the exact light pattern output desired. For example, the beam angle of each LED can be narrowed to optimize the lighting for spot lighting rather than general lighting.
This approach has several disadvantages. First, the cost of the lighting is higher because of the added components and more complicated assembly. Second, because the optics are attached to each LED, multiple lighting shadows may still exist. Finally, the secondary optics reduce the efficacy of the optical system.
3. Bare LED, existing lamp reflector and diffuser
Instead of using an optic for each LED, the entire LED array can use a diffuser to spread the light. The advantage of this approach is that the beam angle is wider than that achievable with bare LEDs and it eliminates the multi-lighting shadowing effect.
The disadvantages of option 2 are higher cost and lower efficiency of the optical system. Since diffusers can only scatter light, not focus it, this approach is not an option if the light distribution must be narrower than that of a bare LED.
Illuminance distribution, multi-source shadowing, and aesthetics usually determine the choice of optical system. If the light output must be narrower than that of a bare LED, only option 2 is the right choice. Otherwise, option 1 is better in terms of cost, efficacy, and brightness. However, both options 1 and 2 have multi-source shadowing effects.
Additionally, while users viewing options 1 and 2 see individual LEDs, users using option 3 see only a diffuse, even illumination.
Multi-source shadow effect
The multi-source shadow effect is the phenomenon where multiple shadows appear on a surface when an object is located between multiple lighting sources. Most people have seen multiple light bulbs installed above a bathroom sink and noticed that they had multiple shadows on the wall behind them. This is the multi-source shadow effect.
LEDs placed very close together will create multiple shadows that are close to each other. In the target application, the appearance of these close shadows may be undesirable. The designer must decide how important the multiple shadow effect is for the target application and whether the additional optical loss of adding a full reflector to reduce this effect is worth it.
Thermal System Options
1. Existing lamp cover
The lowest cost option is to reuse existing design luminaire covers as covers and heat sinks for LED lighting.
This is obviously not an option for new lighting designs. In addition, most existing covers are made of steel, which is a poor conductor of heat. Generally speaking, steel covers are not a good choice for heat dissipation.
2. Ready-made heat sink
Another option is to purchase an off-the-shelf heat sink. This off-the-shelf heat sink has a proven design and is fully specified by the manufacturer. However, its performance, size, and shape may not be optimized for the target application.
3. Customized heat sink
Customization offers the best opportunity to optimize the heat sink for the application, but has several disadvantages.
This option requires the designer to have access to thermal simulation software, or to have assistance from a third party with experience in thermal design. Tooling and manufacturing charges may make the unit cost of a custom heat sink higher than that of an off-the-shelf design.
The cost of the target lighting, the available heat sink development time, and the target maximum ambient temperature often determine the choice of thermal system. Generally, option 2 is better in situations where cost reduction is more important than maximum ambient temperature. Option 3 is better in situations where maximum ambient temperature is more important (such as outdoor lighting or difficult indoor lighting).
The LED lighting in this example uses an off-the-shelf heat sink with a thermal resistance of 0.47°C/W. Using this heat sink thermal resistance value, the maximum ambient temperature can be calculated using the following formula:
Tj=Ta + (Rth ba×Ptotal) + (Rth j-sp×PLED)
Where, Tj is the LED junction temperature, Ta is the ambient temperature, Rthba is the thermal resistance of the heat sink, PLED is the power consumption of a single LED, PLED = operating current × typical Vf under the operating current, Ptotal = total power consumption = number of LEDs × PLED, Rthj-sp = LED package thermal resistance.
The lighting values in the example are:
Tj,MAX=80℃
Rth ba=0.47℃/W
PLED = 0.35 A × 3.3 V = 1.155 W
Ptotal = 16 × 1.155 W = 18.48 W
Rth j-sp=8℃/W
Ta MAX=Tj MAX-(Rth ba×Ptotal)-(Rth j-sp×PLED)
= 80℃-(0.47℃/W×18.48 W)-(8℃/W×1.155 W)
= 80℃- 8.6856℃-9.24℃
= 62℃
For this indoor application, the maximum ambient temperature of 62°C for lighting in this example is acceptable. For working environments that require a higher maximum ambient temperature, either the maximum junction temperature can be increased (which may affect the service life) or the thermal system (Rth ba ) can be improved (for example, by choosing a better heat sink).
Electrical System Options
1. Off-the-shelf LED drivers
Using an off-the-shelf LED driver will result in the fastest design time, as they are already available and have reference circuit designs, all parts are tested for electromagnetic interference (EMI) and safety, and generally the cost per unit is the lowest in volume.
The downside is that existing LED driver efficiencies are typically in the mid-80% range. Depending on the vendor and application, lifetime and operating temperature can also be an issue.
2. Next generation LED drivers
As LED lighting becomes more popular, more semiconductor companies are turning their attention to optimizing LED design. It is also possible to choose to cooperate with such a company on the development of the next generation of LED drivers, which is more efficient and can obtain full approval from regulatory authorities.
However, waiting for product development may delay the development of LED lighting. In addition, smaller companies may not be able to find driver companies to jointly develop unlisted products.
3. Customized design
For thermal design, a completely custom electrical system may be an option. This may be more efficient than what can be achieved using off-the-shelf parts, but has many potential drawbacks.
Development and certification approvals are the responsibility of the designer. Even after development, the cost per unit may be higher than existing solutions. Also, don’t forget that during the development of LED lighting, driver companies will continue to develop more efficient and cheaper drivers.
The available development resources and target efficiency often determine the choice of electrical system. In the current high-power LED environment, the improvement of total lighting efficiency is more affected by the LED itself than by the driver. It may be beneficial to complete the product as soon as possible rather than trying to wait until the electrical design is more perfect.
Step 6: Final Steps
Table 8 details the final steps in building and evaluating a prototype lighting, which can be followed once design decisions have been made.
Previous article:Advantages and application fields of wireless LED display information release system
Next article:Comparison of high frequency electrodeless lamps and LED light sources in the field of street lighting
Recommended ReadingLatest update time:2024-11-16 19:58
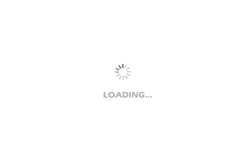
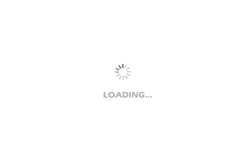
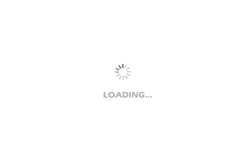
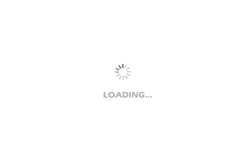
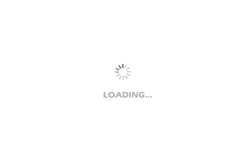
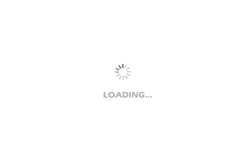
- Popular Resources
- Popular amplifiers
- MathWorks and NXP Collaborate to Launch Model-Based Design Toolbox for Battery Management Systems
- STMicroelectronics' advanced galvanically isolated gate driver STGAP3S provides flexible protection for IGBTs and SiC MOSFETs
- New diaphragm-free solid-state lithium battery technology is launched: the distance between the positive and negative electrodes is less than 0.000001 meters
- [“Source” Observe the Autumn Series] Application and testing of the next generation of semiconductor gallium oxide device photodetectors
- 采用自主设计封装,绝缘电阻显著提高!ROHM开发出更高电压xEV系统的SiC肖特基势垒二极管
- Will GaN replace SiC? PI's disruptive 1700V InnoMux2 is here to demonstrate
- From Isolation to the Third and a Half Generation: Understanding Naxinwei's Gate Driver IC in One Article
- The appeal of 48 V technology: importance, benefits and key factors in system-level applications
- Important breakthrough in recycling of used lithium-ion batteries
- Innolux's intelligent steer-by-wire solution makes cars smarter and safer
- 8051 MCU - Parity Check
- How to efficiently balance the sensitivity of tactile sensing interfaces
- What should I do if the servo motor shakes? What causes the servo motor to shake quickly?
- 【Brushless Motor】Analysis of three-phase BLDC motor and sharing of two popular development boards
- Midea Industrial Technology's subsidiaries Clou Electronics and Hekang New Energy jointly appeared at the Munich Battery Energy Storage Exhibition and Solar Energy Exhibition
- Guoxin Sichen | Application of ferroelectric memory PB85RS2MC in power battery management, with a capacity of 2M
- Analysis of common faults of frequency converter
- In a head-on competition with Qualcomm, what kind of cockpit products has Intel come up with?
- Dalian Rongke's all-vanadium liquid flow battery energy storage equipment industrialization project has entered the sprint stage before production
- Allegro MicroSystems Introduces Advanced Magnetic and Inductive Position Sensing Solutions at Electronica 2024
- Car key in the left hand, liveness detection radar in the right hand, UWB is imperative for cars!
- After a decade of rapid development, domestic CIS has entered the market
- Aegis Dagger Battery + Thor EM-i Super Hybrid, Geely New Energy has thrown out two "king bombs"
- A brief discussion on functional safety - fault, error, and failure
- In the smart car 2.0 cycle, these core industry chains are facing major opportunities!
- The United States and Japan are developing new batteries. CATL faces challenges? How should China's new energy battery industry respond?
- Murata launches high-precision 6-axis inertial sensor for automobiles
- Ford patents pre-charge alarm to help save costs and respond to emergencies
- New real-time microcontroller system from Texas Instruments enables smarter processing in automotive and industrial applications
- Flathead RVB2601 board-web playback
- After magnifying the CPU internals 10,000 times
- [Modification] Both the boost board and the purifier are troublesome in voltage
- Where does the magnetic flux go in this case and what is its impact?
- EEWORLD University ---- ROS Courses
- TTI&TE Live: The development and latest applications of sensors in industrial motors
- Qorvo Biotechnologies Receives FDA Emergency Use Authorization (EUA) for Rapid COVID-19 Antigen Test
- TI 28335 and AD7606 communicate via SPI serial data
- 【i.MX6ULL】Driver Development 4——Light up the LED (Register Version)
- [Raspberry Pi 3B+ Review] Connect to WIFI & Log in to VNC & Update System Support