First, the leakage current of the LED is too large, causing the PN junction to fail, making the LED lamp fail to light up. This situation generally does not affect the operation of other LED lamps;
Secondly, the internal connection leads of the LED lamp are disconnected, resulting in a dead light without current passing through the LED. This situation will affect the normal operation of other LED lamps. The reason is that the operating voltage of the LED lamp is low (the operating voltage of red, yellow and orange LEDs is 1.8V-2.2V, and the operating voltage of blue, green and white LEDs is 2.8-3.2V). Generally, they must be connected in series or parallel to adapt to different operating voltages. The more LED lamps are connected in series, the greater the impact. As long as one of the LED lamps has an open internal connection, the entire string of LED lamps in the series circuit will not light up. It can be seen that this situation is much more serious than the first situation.
LED dead lights are the key to product quality and reliability. How to reduce and eliminate dead lights and improve product quality and reliability is a key issue that packaging and application companies need to solve. The following is an analysis and discussion of some of the causes of dead lights.
1. Static electricity damages the LED chip , causing the PN junction of the LED chip to fail, increasing the leakage current and turning it into a resistor.
Static electricity is a very harmful devil. Countless electronic components are damaged by static electricity around the world, causing tens of millions of dollars in economic losses. Therefore, preventing static electricity from damaging electronic components is a very important task in the electronics industry. LED packaging and application companies must not take it lightly. Any problem in any link will cause damage to the LED, causing the LED performance to deteriorate or even fail. We know that the static electricity of the human body ( ESD ) can reach about 3,000 volts, which is enough to break down and damage the LED chip. In the LED packaging production line, it is also very important whether the grounding resistance of various equipment meets the requirements. Generally, the grounding resistance is required to be 4 ohms, and in some high-requirement occasions, the grounding resistance must even reach ≤2 ohms.
These requirements are familiar to people in the electronics industry. The key is whether they are in place during actual implementation and whether there are records. According to the author's understanding, most private enterprises do not take adequate anti-static measures, which is why most enterprises cannot find ground resistance test records. Even if they do a ground resistance test, it is only once a year, or once every few years, or when there is a problem, the ground resistance is checked. However, it is not known that ground resistance testing is a very important task, at least 4 times a year (once a quarter), and some places with high requirements need to do a ground resistance test every month.
Soil resistance varies with the seasons. In spring and summer, there is a lot of rain, so the wet soil grounding resistance is easier to reach. In autumn and winter, the dry soil has less moisture, and the grounding resistance may exceed the specified value. Recording is to save the original data so that it can be checked in the future. It complies with the ISO2000 quality management system. You can design a table for testing grounding resistance. Both packaging companies and LED application companies need to do grounding resistance testing. Just fill in the names of various equipment in the table, measure the grounding resistance of each device and record it, and the tester can sign and archive it.Static electricity from the human body can also cause great damage to LEDs. When working, you should wear anti-static clothing and wear an anti-static ring. The anti-static ring should be well grounded. There is an anti-static ring that does not need to be grounded, but the anti-static effect is not good. It is recommended not to use this product. If the staff violates the operating procedures, they should receive corresponding warning education, which also serves as a warning to others. The amount of static electricity on the human body is related to the different fabrics of the clothes people wear and their physical constitution. When we take off our clothes in the dark night of autumn and winter, it is easy to see the discharge between the clothes. The voltage of this static discharge is 3,000 volts.
The ESD value of silicon carbide substrate chips is only 1100 volts, and the ESD value of sapphire substrate chips is even lower, only 500-600 volts. If we pick up a good chip or LED with our hands (without any protective measures), the result is predictable. The chip or LED will be damaged to varying degrees. Sometimes a good device will break inexplicably after passing through our hands. This is caused by static electricity.
If the packaging company does not strictly follow the grounding regulations, it will suffer the loss, which will cause the product qualification rate to drop and reduce the economic benefits of the company. Similarly, if the equipment and personnel of the company using LED are not grounded properly, it will also cause damage to the LED, and rework is inevitable. According to the requirements of the LED standard manual, the lead of the LED should be no less than 3-5 mm away from the colloid for bending or welding, but most application companies do not do this, and only directly weld with a thickness of a PCB board (≤2 mm) apart, which will also cause damage or damage to the LED, because the excessively high welding temperature will affect the chip, deteriorate the chip characteristics, reduce the luminous efficiency , and even damage the LED. This phenomenon is common. Some small businesses use manual soldering and use a 40-watt ordinary soldering iron. The soldering temperature cannot be controlled and the soldering iron temperature is above 300-400℃. Excessively high soldering temperature can also cause dead lights. The expansion coefficient of LED leads at high temperatures is several times higher than the expansion coefficient at around 150℃. The internal gold wire solder joints will be pulled apart due to excessive thermal expansion and contraction, causing dead lights.
2. Analysis of the reasons for the LED lamp dead light phenomenon caused by open circuit of internal connection solder joints2.1 The direct cause of LED lamp failure is the incomplete production process of packaging enterprises and backward material inspection methods.
Generally, LEDs are packaged in brackets. The brackets are made of copper or iron metal materials and stamped by precision molds. Since copper is expensive, the cost is naturally high. In order to reduce manufacturing costs, most of the market uses cold-rolled low-carbon steel to stamp LED brackets. Iron brackets must be silver-plated. Silver plating has two functions: one is to prevent oxidation and rust, and the other is to facilitate welding. The electroplating quality of the bracket is very critical. It is related to the life of the LED. The treatment before electroplating should be strictly carried out according to the operating procedures. Rust removal, oil removal, phosphating and other processes should be meticulous. The current should be controlled during electroplating, and the thickness of the silver plating layer should be controlled. Too thick a coating will cost a lot, and too thin a coating will affect the quality.
Because general LED packaging companies do not have the ability to inspect the electroplating quality of brackets, this gives some electroplating companies an opportunity to make the silver plating layer of the electroplated bracket thinner and reduce costs. General packaging companies lack IQC inspection methods for brackets and do not have instruments to detect the thickness and fastness of the bracket plating layer, so it is easier to get away with it. I have seen some brackets rust after being placed in the warehouse for a few months, not to mention being used, which shows how poor the quality of electroplating is. Products made with such brackets will definitely not last long, not to mention 30,000 to 50,000 hours, even 10,000 hours will be a problem.
The reason is very simple. Every year there is a period of south wind. In such weather, the air is humid, which can easily cause poorly plated metal parts to rust, making LED components ineffective. Even if the LED is packaged, the silver coating is too thin and the adhesion is not strong, and the solder joints are separated from the bracket, causing the lamp to die. This is what we encounter when the lamp that is used well does not light up. In fact, it is because the internal solder joints are separated from the bracket.
2.2 Every step in the packaging process must be carefully performed. Any negligence in any link will cause the light to die.
In the process of soldering and bonding, too much or too little silver glue (for single solder joint chips) is not good. Too much glue will return to the gold pad of the chip, causing a short circuit, and too little glue will make the chip not stick firmly. The same is true for the insulating glue of double solder joint chips. Too much insulating glue will return to the gold pad of the chip, causing a cold solder joint during welding and thus a dead light. Too little glue will make the chip not stick firmly, so the glue must be applied just right, neither too much nor too little.
The welding process is also critical. The pressure, time, temperature, and power of the gold wire ball welder must be matched just right. Except for the fixed time, the other three parameters are adjustable. The pressure should be adjusted moderately. Too much pressure can easily crush the chip, and too little pressure can easily cause cold soldering. The welding temperature is generally adjusted to 280℃. The power adjustment refers to the ultrasonic power adjustment. Too much or too little is not good. Moderate is the degree. In short, the adjustment of various parameters of the gold wire ball welder is qualified when the welded material is tested by a spring torque tester for ≥6 grams.
Every year, the parameters of the gold wire ball welding machine are tested and calibrated to ensure that the welding parameters are in the best state. In addition, there are also requirements for the arc of the welding wire. The arc height of the single-solder chip is 1.5-2 chip thicknesses, and the arc height of the double-solder chip is 2-3 chip thicknesses. The height of the arc will also cause quality problems of the LED. If the arc height is too low, it is easy to cause the dead light phenomenon during welding, and if the arc height is too high, the resistance to current shock is poor.
3. How to identify the dead light of cold solder joint
Use a lighter to heat the LED lead wire of the LED lamp that is not lit to 200-300℃, remove the lighter, and connect the positive and negative poles of the LED with a 3V button battery. If the LED lamp can light up at this time, but as the temperature of the lead wire decreases, the LED lamp changes from bright to dark, this proves that the LED lamp is poorly soldered. The reason why heating can light up is that it uses the principle of thermal expansion and contraction of metals. When the LED lead wire is heated, it expands and stretches to connect with the internal solder joints. At this time, turn on the power supply , and the LED can emit light normally. As the temperature drops, the LED lead wire shrinks and returns to the normal temperature state, disconnecting from the internal solder joints, and the LED lamp cannot light up. This method has been tried and tested many times and is effective.
Solder the two leads of the dead light with cold solder joints to a metal bar, soak it in concentrated sulfuric acid to dissolve the colloid on the outside of the LED, take it out after the colloid is completely dissolved, and observe the welding conditions of each soldering point under a magnifying glass or microscope. This way, you can find out whether the problem is with the first or second soldering, whether the parameters of the gold wire ball soldering machine are set incorrectly, or other reasons, so as to improve the method and process to prevent the cold solder joint phenomenon from happening again.
Users of LED products may also encounter the phenomenon of dead lights. This is the phenomenon of dead lights after using LED products for a period of time. There are two reasons for dead lights. Open circuit dead lights are caused by poor welding quality or problems with the quality of bracket electroplating. The increase in leakage current of LED chips can also cause LED lights to not light up. In order to reduce costs, many LED products now do not have anti-static protection, so it is easy for the chips to be damaged by induced static electricity. Thunderstorms on rainy days are prone to induction of high-voltage static electricity in the power supply line, and spike pulses superimposed on the power supply line, which will cause LED products to suffer varying degrees of damage.
In short, there are many reasons for dead lights, which cannot be listed one by one. Dead lights may occur in every link from packaging, application, to use. How to improve the quality of LED products is an issue that packaging companies and application companies should attach great importance to and seriously study. From chip and bracket selection to LED packaging, the entire process should be operated in accordance with the ISO2000 quality system. Only in this way can the quality of LED products be comprehensively improved, and long life and high reliability can be achieved. In the circuit design of the application, choosing varistors and PPTC components to improve the protection circuit, increasing the number of parallel paths, using constant current switching power supplies , and adding temperature protection are all effective measures to improve the reliability of LED products. As long as the packaging and application companies operate strictly in accordance with the ISO2000 quality system, the quality of LED products will definitely be taken to a new level.
Previous article:High quality and high efficiency LED power supply design
Next article:ON Semiconductor LED Area Lighting Application Solutions
Recommended ReadingLatest update time:2024-11-16 15:47
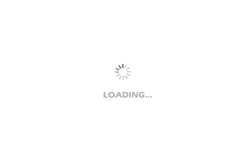
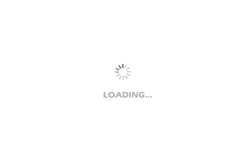
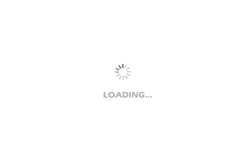
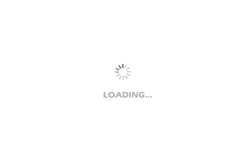
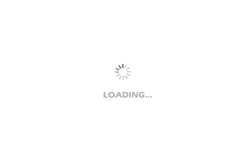
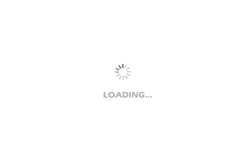
- Popular Resources
- Popular amplifiers
- MathWorks and NXP Collaborate to Launch Model-Based Design Toolbox for Battery Management Systems
- STMicroelectronics' advanced galvanically isolated gate driver STGAP3S provides flexible protection for IGBTs and SiC MOSFETs
- New diaphragm-free solid-state lithium battery technology is launched: the distance between the positive and negative electrodes is less than 0.000001 meters
- [“Source” Observe the Autumn Series] Application and testing of the next generation of semiconductor gallium oxide device photodetectors
- 采用自主设计封装,绝缘电阻显著提高!ROHM开发出更高电压xEV系统的SiC肖特基势垒二极管
- Will GaN replace SiC? PI's disruptive 1700V InnoMux2 is here to demonstrate
- From Isolation to the Third and a Half Generation: Understanding Naxinwei's Gate Driver IC in One Article
- The appeal of 48 V technology: importance, benefits and key factors in system-level applications
- Important breakthrough in recycling of used lithium-ion batteries
- Innolux's intelligent steer-by-wire solution makes cars smarter and safer
- 8051 MCU - Parity Check
- How to efficiently balance the sensitivity of tactile sensing interfaces
- What should I do if the servo motor shakes? What causes the servo motor to shake quickly?
- 【Brushless Motor】Analysis of three-phase BLDC motor and sharing of two popular development boards
- Midea Industrial Technology's subsidiaries Clou Electronics and Hekang New Energy jointly appeared at the Munich Battery Energy Storage Exhibition and Solar Energy Exhibition
- Guoxin Sichen | Application of ferroelectric memory PB85RS2MC in power battery management, with a capacity of 2M
- Analysis of common faults of frequency converter
- In a head-on competition with Qualcomm, what kind of cockpit products has Intel come up with?
- Dalian Rongke's all-vanadium liquid flow battery energy storage equipment industrialization project has entered the sprint stage before production
- Allegro MicroSystems Introduces Advanced Magnetic and Inductive Position Sensing Solutions at Electronica 2024
- Car key in the left hand, liveness detection radar in the right hand, UWB is imperative for cars!
- After a decade of rapid development, domestic CIS has entered the market
- Aegis Dagger Battery + Thor EM-i Super Hybrid, Geely New Energy has thrown out two "king bombs"
- A brief discussion on functional safety - fault, error, and failure
- In the smart car 2.0 cycle, these core industry chains are facing major opportunities!
- The United States and Japan are developing new batteries. CATL faces challenges? How should China's new energy battery industry respond?
- Murata launches high-precision 6-axis inertial sensor for automobiles
- Ford patents pre-charge alarm to help save costs and respond to emergencies
- New real-time microcontroller system from Texas Instruments enables smarter processing in automotive and industrial applications
- When the comparator output is connected to the logic OR gate input, it cannot generate a high voltage signal (logic "1"), how to solve it?
- [NXP Rapid IoT Review] "Smart Home Control System Based on Rapid IoT" - Review Summary
- Advantages of TI's multi-channel PA controller AMC7932 in MIMO systems
- 555 classic circuit diagram: DC-AC converter diagram composed of 555 circuit
- Is there any mobile phone positioning software that you would recommend?
- TI Live: A detailed discussion of a candidate solution for "electric vehicle on-board charger". Will it be popular among engineers?
- DSPC6678 on-chip storage space allocation mechanism
- EEWORLD University Hall ---- Computer Control Devices Zhang Guangxin of Zhejiang University
- The most worrying thing happened: ARM complies with new US regulations and stops cooperating with Huawei
- Summary of remote firmware upgrade for MSP430, STM8L, cortex-M0 core