LED has the advantages of environmental protection, energy saving, high efficiency, long life, safety and reliability. In today's "low-carbon" life, it can play a significant role. Now LED lighting is basically popular. Therefore, it is necessary to understand the use conditions, working principles, driving methods and typical applications of LED in order to maximize the application of LED lighting.
2 LED Working Principle
To design a drive circuit, we must first understand its working principle. The brightness of an LED is mainly related to VF and IF. The volt-ampere characteristics of an LED are shown in Figure 1, where VF is the forward voltage drop of the LED and IF is the forward current. When the forward voltage exceeds the threshold (i.e., the turn-on voltage, about 1.7V in the figure), it can be approximately considered that IF is proportional to VF. As can be seen from the figure, the highest IF of an LED can reach 1A, while VF is usually 2V to 4V.
Figure 1 Relationship between VF and IF of LED
The forward voltage drop of LED varies in a wide range (up to 1V or more), and from the VF-IF curve in the figure above, we can see that a small change in VF will cause a large change in IF, which in turn causes a large change in brightness. Therefore, the luminous characteristics of LEDs are usually described as a function of current rather than a function of voltage. However, the output voltage of a general rectifier circuit will also change with the fluctuation of the grid voltage. Therefore, using a constant voltage source to drive cannot guarantee the consistency of LED brightness and will affect the characteristics of the LED. Therefore, LED drivers usually use constant current sources.
3 LED driving technology
From the working principle of LED, we know that to keep the LED in the best brightness state, a constant current source is needed to drive it. The driving task is to maintain the constant current characteristics and keep the power consumption low. In order to meet the above requirements, the commonly used methods of controlling current are: controlling the current by adjusting the size of the current limiting resistor; adjusting the current by adjusting the reference voltage on the current limiting resistor; PWM modulation to achieve current control. The driving technology of LED is very similar to the technology used in switching power supplies. The LED driving circuit is a power conversion circuit, but it outputs a constant current instead of a constant voltage. In any case, a constant and average current must be output, and the ripple current must be controlled within a certain range.
⑴ Current limiting method
As shown in Figure 2, this is a traditional circuit. After the grid voltage is stepped down, rectified, and filtered, the LED is stabilized by current limiting through resistors. The fatal disadvantage of this circuit is that the power consumption on the resistor R directly affects the efficiency of the system. Coupled with the transformer loss, the system efficiency is about 50%. When the power supply voltage changes within the range of ±10%, the current flowing through the LED will change by ≥25%, and the power on the LED will change by more than 30%. The advantages of resistor current limiting are simple design, low cost, and no electromagnetic interference; however, the current will change with the change of VF, the efficiency is very low, and heat dissipation is difficult.
Figure 2 Current limiting method
(2) Voltage stabilization method
Figure 3 adds an integrated voltage regulator MC7809 to Figure 2, so that the output voltage is basically stable at 9V, and the current limiting resistor R can be very small, which will not cause the LED voltage to be unstable. However, the efficiency of this circuit is still low. Because the voltage drop on MC7809 and R1 still accounts for a large proportion, its efficiency is about 40%. This cannot be called an energy-saving lighting product. In order to achieve both stable operation of LEDs and high efficiency, low-power current limiting components and circuits should be used to improve system efficiency. The advantages of the linear voltage regulation method are simple structure, few external components, medium efficiency and low cost.
Figure 3 Voltage stabilization method
⑶ PWM method
PWM pulse width modulation, that is, using the pulse width modulation method to change the pulse duty cycle of the LED drive current to control the brightness of the light. It is a dimming technology that uses simple digital pulses to repeatedly switch the LED driver on and off. The user only needs to provide different widths and narrowness of digital pulses to change the output current, thereby adjusting the brightness of the white light LED. The characteristic of this drive circuit is that energy is transferred to the load through an inductor, usually by using a PWM control signal to trigger the MOSFET transistor to turn on and off. By changing the PWM duty cycle and the charge and discharge time of the inductor, the ratio of the input voltage to the output voltage is adjusted. Common structures of this type of circuit include buck, boost, buck-boost and other types. The advantages are high efficiency and stability, but it is easy to generate noise audible to the human ear, high cost and complex design.
Figure 4 PWM method
The PWM signal in Figure 4 is connected to the gate of the P-channel MOS tube through the base of the transistor VQ1. The gate drive of the P-channel MOS tube adopts a simple NPN transistor drive amplifier circuit to improve the conduction process of the MOS tube and reduce the power of the driving power supply. When the driving circuit directly drives the MOS tube, it will cause the driven MOS tube to turn on and off quickly, which may cause the oscillation of the voltage between the drain and source of the driven MOS tube. On the one hand, it will cause radio frequency interference, and on the other hand, it may cause the MOS tube to be damaged by excessive voltage and breakdown. To solve this problem, a non-inductive resistor needs to be connected in series between the gate of the driven MOS tube and the output of the driving circuit. When the PWM wave outputs a high level, the transistor VQ1 is turned on, so that the gate voltage of the MOS tube is lower than the source voltage, the source and drain of the MOS tube are turned on, and the LED lights up. When the PWM wave outputs a low level, VQ1 is turned off and the LED goes out.
4 Typical lighting LED driving solutions
At present, the global LED market is mainly controlled by five companies: Nichia, Toyoda Gosei, Cree, Philips Lumileds and Osram. Among lighting LED driver chip manufacturers, the products of China Resources Siwei Technology and Taiwan Dot-Crystal Technology are widely used in China, while those of ON Semiconductor and National Semiconductor are widely used abroad.
(1) LED driver chip from China Resources Silicon Power
The latest PT4207 launched by China Resources Siwei Technology adopts SOP8 package. It is a high-voltage step-down LED driver control chip that can adapt to the input voltage range from 18V to 450V. It can support the series and parallel drive application of hundreds of LEDs, and the duty cycle can reach up to 100% to ensure the high efficiency of the system. The built-in input voltage compensation function greatly improves the LED current stability of PT4207 under different input voltages. PT4207 has a built-in 350mA switch and is equipped with an external MOS switch drive port. For applications below 350mA, no external MOS switch is required. For applications above 350mA, an external MOS tube can be used to expand the current. The LED current can be set by an external resistor. Through the multi-function dimming DIM pin, the LED current can be linearly adjusted using a resistor or DC voltage, or a digital pulse signal can be used for PWM dimming. PT4207 has a variety of protection functions, including load short-circuit protection, open-circuit protection, over-temperature protection, etc. It is suitable for various applications such as AC/DC LED fluorescent lamps, RGB backlight LED drivers, and LED ambient decorative lights. The typical application circuit of PT4207 is shown in Figure 5.
Figure 5 Typical application circuit of LED fluorescent lamp driver chip PT4207
(2) ON Semiconductor LED driver chip
ON Semiconductor NCL30000 is an excellent product with low cost and good performance. This device integrates PFC, DC-DC conversion and LED driver, is simple and easy to use, and its small SOIC package is also conducive to compact design and low cost. The NCL30000 adopts a compact 8-pin surface mount package and uses a critical conduction mode flyback architecture to provide a high power factor greater than 0.95 over a wide AC input voltage range in a single-stage topology. Typical applications include LED driver power supplies, LED recessed lights, triac dimmable LED lamps and power factor correction constant voltage power supplies. Its typical application schematic is shown in Figure 6.
Figure 6 NCL30000 typical application schematic
(3) National Semiconductor LED driver chip
Constant current buck type, Vin range: LM3405 3V -15V/LM3405A 3V-22V; reference current source: 200mV; operating frequency: 0.550/1.6MHZ; PWM dimming. Typical applications are: home lighting, street lighting, advertising decoration, etc. The schematic diagram of LM3405 typical application is shown in Figure 7.
Figure 7 LM3405 typical application schematic
(4) Taiwan Dot-Crystal Technology LED driver chip
DM413 is a full-color driver chip with built-in grayscale generator and PWM pulse width modulation. It is designed for LED lighting, decoration, large-screen display and other applications. Maximum constant current output: 100mA; maximum output withstand voltage: 17V; maximum serial clock frequency: 20MHz; chip operating voltage: 3.3V--5.5V. DM413 has several signal input and output pins and multiple function setting pins. The signal is given to the corresponding input pin of DM413 through the input interface. The three output pins are used to connect LEDs, which can be assigned to three colors: R, G, and B. The same output pin is connected to the same color LED. According to the color matching requirements, each output pin can be connected to one or more LEDs. The controller output interface has three signal lines: a serial data output line, a clock signal output line and a latch signal line. These three lines are connected to the corresponding three pins of the driver chip respectively. Like the general serial shift mechanism, under the control of the clock signal, the serial data is shifted and stored inside the driver chip. When the data transmission and reception are completed, the controller sends a latch signal to the driver chip, causing the LED driver chip to latch the stored data and drive the LED to emit light according to the stored data. This method controls the LED to turn on and off quickly at a high frequency that the human eye cannot distinguish, and sets the proportion of on and off according to the data stored in the chip, that is, to achieve grayscale control. The typical application schematic diagram of DM413 is shown in Figure 8.
Figure 8 DM413 typical application schematic
5 Conclusion
From the above, it can be seen that LED needs to have current-stabilizing and voltage-stabilizing components when working, but such components should have the characteristics of high partial pressure but low power consumption. Therefore, high-efficiency circuits such as capacitors, inductors or active switching circuits should be used as much as possible to ensure the high efficiency of the LED system. The use of a series integrated constant power output circuit can keep the light output of the LED constant within a wide power supply range, but the general IC circuit will reduce the efficiency. The use of an active switching circuit can ensure constant power output when the power supply voltage changes greatly at a high conversion efficiency. Most LED chips today can modulate the brightness from 0 to 100%, and can ensure that the light efficiency is maintained at a high level during the entire dimming process without damaging the life of the LED. At present, the two main solutions for brightness control are linear adjustment of the LED current (analog dimming) or switching the drive current back and forth from 0 to the target current value at a high frequency that cannot be detected by the naked eye (digital dimming). Using pulse width modulation (PWM) to set the cycle and duty cycle may be the simplest way to achieve digital dimming.
Previous article:Light distribution scheme for high-power LED street lights
Next article:How to Replace LDO Regulators with Green LEDs
Recommended ReadingLatest update time:2024-11-16 23:48
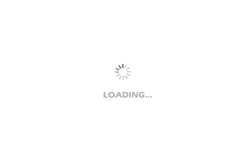
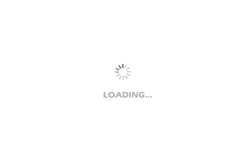
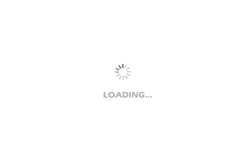
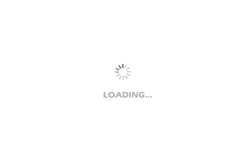
- Popular Resources
- Popular amplifiers
- MathWorks and NXP Collaborate to Launch Model-Based Design Toolbox for Battery Management Systems
- STMicroelectronics' advanced galvanically isolated gate driver STGAP3S provides flexible protection for IGBTs and SiC MOSFETs
- New diaphragm-free solid-state lithium battery technology is launched: the distance between the positive and negative electrodes is less than 0.000001 meters
- [“Source” Observe the Autumn Series] Application and testing of the next generation of semiconductor gallium oxide device photodetectors
- 采用自主设计封装,绝缘电阻显著提高!ROHM开发出更高电压xEV系统的SiC肖特基势垒二极管
- Will GaN replace SiC? PI's disruptive 1700V InnoMux2 is here to demonstrate
- From Isolation to the Third and a Half Generation: Understanding Naxinwei's Gate Driver IC in One Article
- The appeal of 48 V technology: importance, benefits and key factors in system-level applications
- Important breakthrough in recycling of used lithium-ion batteries
- Innolux's intelligent steer-by-wire solution makes cars smarter and safer
- 8051 MCU - Parity Check
- How to efficiently balance the sensitivity of tactile sensing interfaces
- What should I do if the servo motor shakes? What causes the servo motor to shake quickly?
- 【Brushless Motor】Analysis of three-phase BLDC motor and sharing of two popular development boards
- Midea Industrial Technology's subsidiaries Clou Electronics and Hekang New Energy jointly appeared at the Munich Battery Energy Storage Exhibition and Solar Energy Exhibition
- Guoxin Sichen | Application of ferroelectric memory PB85RS2MC in power battery management, with a capacity of 2M
- Analysis of common faults of frequency converter
- In a head-on competition with Qualcomm, what kind of cockpit products has Intel come up with?
- Dalian Rongke's all-vanadium liquid flow battery energy storage equipment industrialization project has entered the sprint stage before production
- Allegro MicroSystems Introduces Advanced Magnetic and Inductive Position Sensing Solutions at Electronica 2024
- Car key in the left hand, liveness detection radar in the right hand, UWB is imperative for cars!
- After a decade of rapid development, domestic CIS has entered the market
- Aegis Dagger Battery + Thor EM-i Super Hybrid, Geely New Energy has thrown out two "king bombs"
- A brief discussion on functional safety - fault, error, and failure
- In the smart car 2.0 cycle, these core industry chains are facing major opportunities!
- The United States and Japan are developing new batteries. CATL faces challenges? How should China's new energy battery industry respond?
- Murata launches high-precision 6-axis inertial sensor for automobiles
- Ford patents pre-charge alarm to help save costs and respond to emergencies
- New real-time microcontroller system from Texas Instruments enables smarter processing in automotive and industrial applications
- [Starting at 13:30 pm] TI wireless connectivity product series application design guidance, online hands-on demo
- Inductance and Q value of transformer
- MSP430 ADC analog-to-digital routines
- DSP online upgrade procedure steps
- The nonlinearity of the diode will cause some new waveforms to be generated. What is the underlying formation principle? Who can explain it to me?
- The weekly review information is here~ The fresh delivery is here
- STM32F030 AD signal acquisition
- Does anyone have a working stm32F7 or H7 fmc interface lcd driver? I've been having a lot of trouble with it recently.
- The output data of the ADC chip is incorrect no matter how I process it. Please help.
- Some knowledge about optical splitters