Innovation in technology and materials
Power transistor technology has continued to improve over time. Devices have become smaller and smaller, while power density has increased. For high-power transistors above 1 kV, bipolar structures have become the preferred choice; below 1 kV, especially at frequencies above 100 kHz, MOSFETs are more commonly used. For high-current applications above this voltage, IGBTs are the choice.
The main challenge in developing such devices is to minimize internal losses by reducing conduction losses due to on-resistance, reducing internal capacitance, and improving reverse recovery performance as switching frequencies continue to rise. Improving breakdown robustness is also very important due to higher breakdown voltage and unclamped switching characteristics (UIS).
In the past, the focus of developing low-voltage MOSFETs below 40 V was to minimize the die size under given on-resistance conditions to reduce unit cost. Therefore, the most important quality factor (Figure of Merit, FOM) is the characteristic on-resistance (RDS(ON)spec) in units of mΩ x mm2. Since the channel resistance has a large impact on the characteristic on-resistance in low-voltage FETs, the industry has focused on configuring as many FET channels as possible on the available area. Planar channels are replaced by vertical "trench gate" channels, and advanced lithography techniques are used to reduce surface dimensions.
However, the approach of reducing the trench FET pitch does not easily achieve the critical figure of merit defined as RDS(ON) x Qg(d) because the improvement in on-resistance per unit area is offset by the increase in gate charge (Qg) per unit area. Therefore, development has shifted to architectures such as trench FET (with an additional decoupled vertical field plate shielding the gate from the drain), trench LDMOS (combining the compactness of trench MOS with backside drain and the lower Qg(d) of LDMOS), and LDMOS with optimized metallization/packaging.
Although silicon-based transistors have continued to improve over the years, the limitations of silicon-based material properties indicate that other available solutions will need to be sought in the next decade. Currently, solutions using wide-bandgap materials (gallium nitride, silicon carbide and diamond) have emerged. These materials can provide better thermal characteristics, lower switching losses, and combine the advantages of more attractive low on-resistance (RDS(ON)) and high breakdown voltage (VBD) performance.
Wide-bandgap materials can also enable major breakthroughs in high-voltage applications. The critical breakdown fields of GaN and SiC are orders of magnitude higher than those of Si, and the devices released to date also have the advantage of higher thermal conductivity (about 3 times higher than Si). SiC is the material of choice for applications above 1 kV, while GaN is best suited for applications below 1 kV. However, there are still some technical hurdles to overcome, such as adding thick GaN layers on silicon to provide high voltage ratings, making enhancement mode transistors, and improving reliability. The first high-voltage GaN high electron mobility transistors (HEMTs) are expected to be available in the next few years.
Innovation in technology and materials
Power transistor technology has continued to improve over time. Devices have become smaller and smaller, while power density has increased. For high-power transistors above 1 kV, bipolar structures have become the preferred choice; below 1 kV, especially at frequencies above 100 kHz, MOSFETs are more commonly used. For high-current applications above this voltage, IGBTs are the choice.
The main challenge in developing such devices is to minimize internal losses by reducing conduction losses due to on-resistance, reducing internal capacitance, and improving reverse recovery performance as switching frequencies continue to rise. Improving breakdown robustness is also very important due to higher breakdown voltage and unclamped switching characteristics (UIS).
In the past, the focus of developing low-voltage MOSFETs below 40 V was to minimize the die size under given on-resistance conditions to reduce unit cost. Therefore, the most important quality factor (Figure of Merit, FOM) is the characteristic on-resistance (RDS(ON)spec) in units of mΩ x mm2. Since the channel resistance has a large impact on the characteristic on-resistance in low-voltage FETs, the industry has focused on configuring as many FET channels as possible on the available area. Planar channels are replaced by vertical "trench gate" channels, and advanced lithography techniques are used to reduce surface dimensions.
However, the approach of reducing the trench FET pitch does not easily achieve the critical figure of merit defined as RDS(ON) x Qg(d) because the improvement in on-resistance per unit area is offset by the increase in gate charge (Qg) per unit area. Therefore, development has shifted to architectures such as trench FET (with an additional decoupled vertical field plate shielding the gate from the drain), trench LDMOS (combining the compactness of trench MOS with backside drain and the lower Qg(d) of LDMOS), and LDMOS with optimized metallization/packaging.
Although silicon-based transistors have continued to improve over the years, the limitations of silicon-based material properties indicate that other available solutions will need to be sought in the next decade. Currently, solutions using wide-bandgap materials (gallium nitride, silicon carbide and diamond) have emerged. These materials can provide better thermal characteristics, lower switching losses, and combine the advantages of more attractive low on-resistance (RDS(ON)) and high breakdown voltage (VBD) performance.
Wide-bandgap materials can also enable major breakthroughs in high-voltage applications. The critical breakdown fields of GaN and SiC are orders of magnitude higher than those of Si, and the devices released to date also have the advantage of higher thermal conductivity (about 3 times higher than Si). SiC is the material of choice for applications above 1 kV, while GaN is best suited for applications below 1 kV. However, there are still some technical hurdles to overcome, such as adding thick GaN layers on silicon to provide high voltage ratings, making enhancement mode transistors, and improving reliability. The first high-voltage GaN high electron mobility transistors (HEMTs) are expected to be available in the next few years.
Power devices are becoming smarter
Smart power IC is a new device that integrates "intelligence" and "power" on a single chip. It is widely used in many fields including power converters, motor control, fluorescent lamp rectifiers, automatic switches, video amplifiers, bridge drive circuits, and display drivers.
China is the world's largest consumer electronics market, and the demand for various electronic products is increasing day by day, which indicates that there will be a huge market for smart power ICs.
Smart power ICs use a combined bipolar/CMOS/DMOS (BCD) process to enable analog, digital, and power system designs to be integrated on a single substrate. Subsequent BCD processes have improved high-voltage isolation, digital feature size (providing higher analog accuracy, logic speed and density, etc.), and power handling capabilities. Modern processes can integrate digital processors, RAM/ROM memory, embedded memory, and power drivers. For example, the BCD process can integrate power, logic, and analog functions on a single chip.
As CMOS geometry continues to shrink, the need for highly embedded intelligence has led to the integration of 16/32-bit processors, multi-Mb ROM/RAM/non-volatile memory, and complex IP. Analog functions are also increasing due to the need for higher-precision sensing mechanisms, high-bit-rate data conversion, different interface protocols, pre-driver/control loops, and precise on-chip voltage/current references for modules. The industry has introduced power drivers with 100 to 200 V and 5 to 10 A. These devices have low on-resistance and high-density, rugged high-voltage isolation architectures using deep trench and silicon-on-insulator (SOI) technology.
Integrated 600 V transistor technology for AC-DC inverters complements technology for sub-100 V applications and is proving to be another important market. Advanced submicron CMOS processes will drive the integration of low-cost, low on-resistance drivers from traditional LDMOS devices to dual and triple low surface field (RESURF) DMOS, super junction LDMOS and LIGBT. [ View related topics on this site: Application of power devices in green energy-saving design [IGBT, MOSFET] ]
Unlimited potential of packaging technology
The main trend in power semiconductor packaging is to enhance interconnection, including wafer-level technologies to reduce impedance/parasitic effects and enhanced on-chip heat dissipation. Thick copper, gold or aluminum wire bonding, ribbon/package adhesion (clip bonding), and power-optimized chip-scale packaging (CSP) are also enhancing the efficiency of the resistive connection between the die and the external electrodes. Figure 1 shows the evolution of packaging technology.
Figure 1 Power packaging integration roadmap
The power module itself is a combination of power electronic devices encapsulated according to certain functional combinations. It is no exaggeration to say that it is a packaging technology. Early power modules integrated multiple thyristors/rectifiers in a single package to provide higher rated power. Major breakthroughs in the past three decades have enabled today's modules to combine power semiconductors with sensing, driving, protection and control functions. For example, the intelligent power module is an advanced hybrid integrated power component with IGBT as the core, consisting of a high-speed, low-power die (IGBT) and an optimized gate drive circuit, as well as a fast protection circuit. The IGBT die in the IPM is of high-speed type, and the drive circuit is close to the IGBT, with a small drive delay, so the IPM has a fast switching speed and low loss. The IPM integrates a real-time detection circuit that can continuously detect the IGBT current and temperature. When a severe overload or even a short circuit occurs, and the temperature is overheated, the IGBT will be softly shut down in a controlled manner, and a fault signal will be issued at the same time. In addition, the IPM also has functions such as bridge arm tube interlocking and drive power undervoltage protection. Although IPM is more expensive, it has the advantages of compact structure, high reliability and ease of use over simple IGBT due to its integrated driving and protection functions.
The direct bonded copper (DBC) technology used in the module enhances electrical performance, while ceramic substrates (such as aluminum oxide and aluminum nitride) can also improve cooling efficiency. Improvements in packaging-assembly technology have also enabled planar co-integration of several bare chips and passive components, as well as vertical stacking technology aimed at increasing system integration. "Un-packaging" technology is another interesting research area, which mechanically integrates several populated substrates without the need for housings, terminals and bases.
Continue to promote process technology advancement
Many manufacturers are actively developing new process technologies. For example, ON Semiconductor has developed a next-generation MOSFET product based on its proprietary Trench 3 process, which can be used in desktops, notebooks, and netbooks, helping to improve energy efficiency and switching performance while reducing die size.
In the next few years, ON Semiconductor will also develop GaN wafer production process/device integration process/manufacturing process/packaging process, insulating silicon wafer production process, contact/isolation trench process module, low inductance packaging, inductor and capacitor integration and other process technologies; at the same time, it will use packaging technology to achieve product innovation, achieve higher I/O density with thinner packaging and lower footprint, continuously improve packaging thermal efficiency and operating temperature range, and make more choices for die size of each package. In addition, it will also reduce material costs with thinner and larger diameter wafers and copper wire clips.
Previous article:Research on the application of WT3000 three-phase power analyzer in power supply testing
Next article:Application of Feedwater Frequency Conversion Control System in 100MW Units
Recommended ReadingLatest update time:2024-11-16 19:59
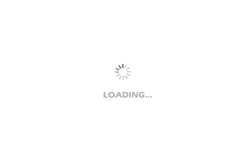
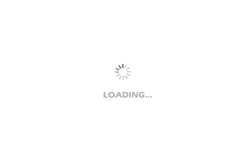
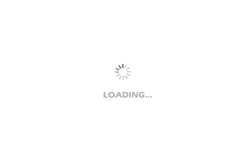
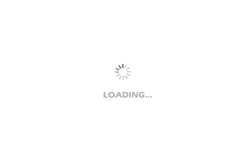
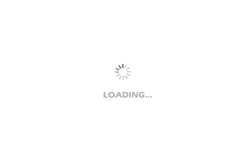
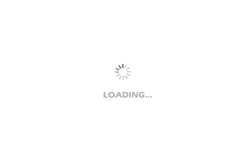
- Popular Resources
- Popular amplifiers
-
Optimization design of SGT_MOSFET peak oscillation in synchronous rectification circuit
-
Study on the Behavioral Model of Silicon Carbide MOSFET Power Module and EMI Prediction of Low-Voltage Auxiliary Power Supply
-
Theory and practice of small-size MOS device models for VLSI simulation
-
Power Electronics Technology 2nd Edition (Li Jie, Chao Xiaojie, Jia Weijuan, Yang Jiayi, Lai Wei)
- MathWorks and NXP Collaborate to Launch Model-Based Design Toolbox for Battery Management Systems
- STMicroelectronics' advanced galvanically isolated gate driver STGAP3S provides flexible protection for IGBTs and SiC MOSFETs
- New diaphragm-free solid-state lithium battery technology is launched: the distance between the positive and negative electrodes is less than 0.000001 meters
- [“Source” Observe the Autumn Series] Application and testing of the next generation of semiconductor gallium oxide device photodetectors
- 采用自主设计封装,绝缘电阻显著提高!ROHM开发出更高电压xEV系统的SiC肖特基势垒二极管
- Will GaN replace SiC? PI's disruptive 1700V InnoMux2 is here to demonstrate
- From Isolation to the Third and a Half Generation: Understanding Naxinwei's Gate Driver IC in One Article
- The appeal of 48 V technology: importance, benefits and key factors in system-level applications
- Important breakthrough in recycling of used lithium-ion batteries
- Innolux's intelligent steer-by-wire solution makes cars smarter and safer
- 8051 MCU - Parity Check
- How to efficiently balance the sensitivity of tactile sensing interfaces
- What should I do if the servo motor shakes? What causes the servo motor to shake quickly?
- 【Brushless Motor】Analysis of three-phase BLDC motor and sharing of two popular development boards
- Midea Industrial Technology's subsidiaries Clou Electronics and Hekang New Energy jointly appeared at the Munich Battery Energy Storage Exhibition and Solar Energy Exhibition
- Guoxin Sichen | Application of ferroelectric memory PB85RS2MC in power battery management, with a capacity of 2M
- Analysis of common faults of frequency converter
- In a head-on competition with Qualcomm, what kind of cockpit products has Intel come up with?
- Dalian Rongke's all-vanadium liquid flow battery energy storage equipment industrialization project has entered the sprint stage before production
- Allegro MicroSystems Introduces Advanced Magnetic and Inductive Position Sensing Solutions at Electronica 2024
- Car key in the left hand, liveness detection radar in the right hand, UWB is imperative for cars!
- After a decade of rapid development, domestic CIS has entered the market
- Aegis Dagger Battery + Thor EM-i Super Hybrid, Geely New Energy has thrown out two "king bombs"
- A brief discussion on functional safety - fault, error, and failure
- In the smart car 2.0 cycle, these core industry chains are facing major opportunities!
- The United States and Japan are developing new batteries. CATL faces challenges? How should China's new energy battery industry respond?
- Murata launches high-precision 6-axis inertial sensor for automobiles
- Ford patents pre-charge alarm to help save costs and respond to emergencies
- New real-time microcontroller system from Texas Instruments enables smarter processing in automotive and industrial applications
- RISC-V MCU Application Development Series Tutorial CH32V103
- Communication between Yitong Chuanglian MODBUS to PROFIBUS gateway and Honeywell DCS system
- Let's take a look
- 【TI Wireless】Micro Dual-Mode Wireless Receiver
- PWM and PFM
- Let’s talk about whether Huawei can survive in the end.
- Can the network cable be directly soldered to the PCB without a crystal plug or can the network cable be plugged into the circuit board with terminals?
- [Revenge RVB2601 creative application development] helloworld_beginner's guide to debugging methods and processes
- What changes will occur if RFID technology is applied to clothing production?
- EEWORLD University Hall----30 Case Studies of MATLAB Intelligent Algorithms