LED aluminum substrate design selection
LED circuit design In order to better solve the heat dissipation problem, LEDs and some high- power ICs need to use aluminum-based circuit boards.
Aluminum substrate PCB consists of circuit layer (copper foil layer), thermal insulation layer and metal base layer. The circuit layer is required to have a large current carrying capacity, so thicker copper foil should be used, with a thickness of 35μm~280μm in general; the thermal insulation layer is the core technology of PCB aluminum substrate, which is generally composed of special polymers filled with special ceramics, with low thermal resistance, excellent viscoelastic properties, resistance to thermal aging, and the ability to withstand mechanical and thermal stress. The thermal insulation layer of high-performance PCB aluminum substrates such as IMS-H01, IMS-H02 and LED-0601 uses this technology, which makes it have extremely excellent thermal conductivity and high-strength electrical insulation performance; the metal base layer is the supporting component of the aluminum substrate, which is required to have high thermal conductivity, generally aluminum plate, and copper plate can also be used (copper plate can provide better thermal conductivity), suitable for conventional mechanical processing such as drilling, punching and cutting. The process requirements are: gold plating, tin spraying, OSP anti-oxidation, immersion gold, lead-free ROHS process, etc.
Substrate: Aluminum substrate Product features: thin insulation layer, low thermal resistance; non-magnetic; good heat dissipation; high mechanical strength Product standard thickness: 0.8, 1.0, 1.2, 1.5, 2.0, 2.5, 3.0mm Copper foil thickness: 1.8um35um70um105um140um Features: high heat dissipation, electromagnetic shielding, high mechanical strength, excellent processing performance. Application: LED dedicated power hybrid IC (HIC).
The aluminum substrate is used to carry the heat conduction of LED and devices. The heat dissipation mainly depends on the area. For concentrated heat conduction, you can choose a plate with high thermal conductivity, such as the American Bergis plate; for slow heat conduction or heat dissipation, ordinary domestic materials can be used. The price difference is large. It takes about 4,000 yuan per square meter to produce a finished product of Bergis plate, while ordinary domestic materials cost more than 1,000 yuan per square meter. The voltage used by LED is generally not very high, so you can choose a 1mil thick insulation layer with a withstand voltage greater than 2000V.
Thermal reference design methodology:
Why thermal design?
The impact of high temperature on electronic products: insulation performance degradation; component damage; thermal aging of materials; cracking of low-melting-point welds and solder joints falling off. The impact of
temperature on components: Generally speaking, the resistance value decreases with increasing temperature; high temperature will reduce the service life of capacitors; high temperature will reduce the performance of transformer and choke insulation materials. Generally, the allowable temperature of transformers and chokes should be lower than 95C; excessive temperature will also cause changes in the alloy structure of solder joints - IMC thickening, solder joints becoming brittle, and mechanical strength reduction; the increase in junction temperature will
rapidly increase the current amplification factor of
the transistor
, resulting in an increase in collector current, which will further increase the junction temperature and eventually lead to component failure.
Purpose of thermal design
Control the temperature of all electronic components inside the product so that it does not exceed the maximum temperature specified by the standards and specifications under the working environment conditions. The calculation of the maximum allowable temperature should be based on the stress analysis of the components and be consistent with the reliability requirements of the product and the failure rate assigned to each component.
LED heat dissipation The design is generally based on fluid dynamics software simulation and basic design.
Resistance to fluid flow: Due to the viscosity of the fluid and the influence of the solid boundary, the fluid encounters resistance during the flow process. This resistance is called flow resistance, which can be divided into two types: along-the-line resistance and local resistance.
Along-the-path resistance: The friction resistance of the fluid along the entire process in an area where the boundary remains unchanged along the path.
Local resistance: In areas where boundaries change dramatically, such as sudden expansion or contraction of the cross section, elbows and other local locations, the flow resistance is caused by the rapid change in the fluid state of the fluid.
Usually, LEDs use heat sinks to dissipate heat naturally. The design of the heat sink is divided into three steps:
1: Design the contour according to the relevant constraints.
2: Optimize the radiator tooth thickness, tooth shape, tooth spacing, and substrate thickness according to the relevant design criteria of the radiator.
3: Perform verification calculations.
Radiator design method
Design Method of Natural Cooling Radiator
Taking into account the thicker temperature boundary layer during natural cooling, if the tooth spacing is too small, the thermal boundary layers of the two teeth are easy to cross, affecting the convection on the tooth surface. Therefore, under normal circumstances, it is recommended that the tooth spacing of the radiator for natural cooling be greater than 12mm. If the radiator tooth height is less than 10mm, the tooth spacing of the radiator can be determined as tooth spacing ≥ 1.2 times the tooth height.
The heat exchange capacity of the natural cooling radiator surface is weak. Adding corrugations on the surface of the heat dissipation teeth will not have much impact on the natural convection effect, so it is recommended not to add corrugated teeth on the surface of the heat dissipation teeth.
The surface of the natural convection radiator is generally treated with blackening to increase the emissivity of the heat dissipation surface and enhance radiation heat transfer.
Since natural convection takes a long time to reach thermal equilibrium, the base and tooth thickness of the natural convection radiator should be sufficient to resist the impact of instantaneous heat load. It is recommended to be greater than 5mm.
Previous article:A brief discussion on several LED street lamp power supply design solutions
Next article:LED lighting knowledge: Boost and Buck-Boost timing
Recommended ReadingLatest update time:2024-11-16 18:03
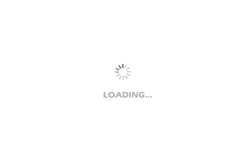
- MathWorks and NXP Collaborate to Launch Model-Based Design Toolbox for Battery Management Systems
- STMicroelectronics' advanced galvanically isolated gate driver STGAP3S provides flexible protection for IGBTs and SiC MOSFETs
- New diaphragm-free solid-state lithium battery technology is launched: the distance between the positive and negative electrodes is less than 0.000001 meters
- [“Source” Observe the Autumn Series] Application and testing of the next generation of semiconductor gallium oxide device photodetectors
- 采用自主设计封装,绝缘电阻显著提高!ROHM开发出更高电压xEV系统的SiC肖特基势垒二极管
- Will GaN replace SiC? PI's disruptive 1700V InnoMux2 is here to demonstrate
- From Isolation to the Third and a Half Generation: Understanding Naxinwei's Gate Driver IC in One Article
- The appeal of 48 V technology: importance, benefits and key factors in system-level applications
- Important breakthrough in recycling of used lithium-ion batteries
- Innolux's intelligent steer-by-wire solution makes cars smarter and safer
- 8051 MCU - Parity Check
- How to efficiently balance the sensitivity of tactile sensing interfaces
- What should I do if the servo motor shakes? What causes the servo motor to shake quickly?
- 【Brushless Motor】Analysis of three-phase BLDC motor and sharing of two popular development boards
- Midea Industrial Technology's subsidiaries Clou Electronics and Hekang New Energy jointly appeared at the Munich Battery Energy Storage Exhibition and Solar Energy Exhibition
- Guoxin Sichen | Application of ferroelectric memory PB85RS2MC in power battery management, with a capacity of 2M
- Analysis of common faults of frequency converter
- In a head-on competition with Qualcomm, what kind of cockpit products has Intel come up with?
- Dalian Rongke's all-vanadium liquid flow battery energy storage equipment industrialization project has entered the sprint stage before production
- Allegro MicroSystems Introduces Advanced Magnetic and Inductive Position Sensing Solutions at Electronica 2024
- Car key in the left hand, liveness detection radar in the right hand, UWB is imperative for cars!
- After a decade of rapid development, domestic CIS has entered the market
- Aegis Dagger Battery + Thor EM-i Super Hybrid, Geely New Energy has thrown out two "king bombs"
- A brief discussion on functional safety - fault, error, and failure
- In the smart car 2.0 cycle, these core industry chains are facing major opportunities!
- The United States and Japan are developing new batteries. CATL faces challenges? How should China's new energy battery industry respond?
- Murata launches high-precision 6-axis inertial sensor for automobiles
- Ford patents pre-charge alarm to help save costs and respond to emergencies
- New real-time microcontroller system from Texas Instruments enables smarter processing in automotive and industrial applications
- STM32 timer triggers ADC to collect data and send it to the host computer
- [RVB2601 Creative Application Development] Recording Box
- Discussing STM32H750 Part 4 (Briefly Talking about CANFD Part 1)
- RK903 & RK901 & AP6xxx Series WiFi Module Configuration
- EEWORLD University Hall----Design considerations for a robust interface between J6 and vehicle displays via FPD-Link
- There are generally only these reasons why switching power supplies howl!
- 5 Tips for Converting Embedded Hardware to Software
- [Analog Electronics Course Selection Test] + User Experience
- ECG 12-lead
- What is the relationship between baud rate and USB or network bit rate? For example, 900 (Baud, symbol/s) is used in some places...