For the common incandescent bulbs, fluorescent bulbs, and energy-saving bulbs, even if the product itself may generate heat during operation, the high heat of the components can still be effectively isolated, so that the light source and the power socket will not cause unexpected public safety problems due to heat. However, LED solid-state lighting is different. First, the high temperature of LED components concentrated at a single point must be treated with more active means to dissipate heat, and at the same time, an active and effective heat treatment mechanism must be used to avoid public safety problems in lamps...
Traditional light sources or lamps often have the problem of generating high heat during operation, such as halogen bulbs or incandescent bulbs. In the case of incandescent bulbs, the tungsten filament is heated in a specially treated lamp bulb environment to produce light.
In fact, high temperature is generated on the filament rather than the lamp holder. Even though the lamp holder will indirectly generate high temperature due to the radiant heat and heat conduction of the tungsten filament on the glass or metal of the lamp ball, the generated temperature is within an acceptable safety range. In addition, due to the non-direct contact conduction, the safety is relatively high.
LED solid-state light source heat treatment issues are more complicated than traditional lamps
However, when switching to LED solid-state light source lamps, heat treatment may become a new application safety issue. Most people think that LED has the advantages of high energy conversion efficiency and low driving energy, so it is naturally safer to use. However, in fact, in order to achieve the application purpose of daily lighting, LED solid-state light sources must increase the power of a single component to enhance the output lumen of a single component . For example, lighting manufacturers will adopt the form of multi-LED component integration to enhance the output effect, and the simultaneous operation of multiple components can also improve the problem of LED solid-state light source light type biased towards point light source, so that LED solid-state light source technology lamps can produce a surface light source effect like a light bulb.
At the development site, in order to enhance the output lumen of a single component, a higher current must be applied to make the PN junction of the LED chip produce more lumens, but a higher current will also increase the temperature of the single-point LED component and make it more difficult to handle. Even in order to improve the light performance and luminous efficiency of the lamp , the use of multiple components will also aggravate the high temperature problem of the LED lamp , making the heat dissipation problem more difficult to handle.
Looking at the current development trend of the LED lighting market, most LED light source module manufacturers will first focus on developing niche market products because of their high unit price and high profit. They can also quickly enter the LED light source market with more advanced development technology through technological differences. For example, recessed lights, wall lights, and ceiling lights for interior decoration and situational lighting applications have become the most common design form of LED light source lamps. The energy saving effect of replacing traditional lamps is also the most concerned by relevant industry players.
Basically, LED light source lamps must focus on thermal management design. For recessed lamps, wall lamps, and ceiling lamps that may be used in closed or semi-closed dead-loop environments, this poses a more stringent challenge. Lamp developers must invest more resources in materials, product configuration, active/passive heat dissipation mechanisms, driver chip design, etc. to avoid safety problems with their products.
LED embedded lamps are small in size and often use multiple components to integrate, so the heat dissipation design of the module is more difficult.
NTC continuously monitors operating temperature to maintain LED light Safe to use
If LED lamps are not equipped with adequate thermal management design, the lamp life may be drastically reduced due to frequent high-temperature operation during use, resulting in the need to frequently replace faulty LED lamps. In serious cases, it may even lead to public safety accidents, as the high temperature operation may cause the circuit or surrounding decorations to catch fire!
During the product development phase, intelligent LED lighting control technology can be used to actively monitor the temperature performance of LED lamps and the overall light source module to simplify the thermal management of the device. At the same time, when the temperature of the lamp and the surrounding environment rises to the dangerous zone, the lamp must reduce the power and reduce the LED brightness output, thereby improving the safety of LED solid-state light source lamps.
Considering a simpler design, if the driver function used in the lamp itself is more focused on power conversion and LED component driving, and does not have an embedded temperature control microprocessor and heat dissipation processing module, in order to avoid increasing the cost of product raw materials, LED lamps can integrate NTC (Negative Temperature Coefficient ) negative temperature coefficient Thermistor Sensors circuit, which is a relatively cost-effective and safe design solution.
The purpose of the so-called NTC circuit is to monitor the temperature of the LED module lamp through an electronic circuit, and to improve the safety of LED lamps by shutting down the LED solid-state light source module through a default temperature warning or automatically processing the driving status. At the same time, the NTC circuit can also reduce the complexity of the design.
Since the temperature coefficient of the NTC circuit is very large, it can detect tiny temperature changes and is widely used in related circuit designs that require measurement, control, and compensation of temperature. In the design of LED light source modules, the NTC circuit is basically used to measure the temperature changes around the product of LED solid-state light source lamps. As for the measurement status, the voltage status that changes with the NTC directly measures the corresponding relationship between the voltage and the temperature of the NTC circuit.
When the temperature of the NTC and the surrounding circuits or the entire module increases, the resistance of the NTC monitoring circuit will decrease immediately. The product can provide feedback on the relevant safety control mechanism based on this dependency, such as reducing the driving current of the LED light-emitting component or directly forcing the lamp to turn off the lighting, and automatically restore the lighting state after the lamp temperature problem improves, thereby ensuring the safety of the lamp.
NTC THERMISTOR components are manufactured in SMD form.
Monitor the temperature of LED lamps and can also be imported into MCU microcontrollers to achieve intelligent monitoring
For the improvement of the aforementioned NTC circuit, if you want to achieve a better protection design, it is also a relatively pragmatic approach to combine it with an MCU for a more sophisticated safety design. In the development project, the status of the LED light source module can be divided into whether the light is turned on normally or turned off, and combined with the program logic judgment of temperature warning and temperature measurement, a more complete smart lighting management mechanism can be constructed.
For example, if a lamp temperature warning appears, temperature measurement shows that the module temperature is still within an acceptable range and can be maintained in a normal manner, with the operating temperature naturally dissipated through the heat sink. When the warning informs that the measured temperature has reached the benchmark for active cooling, the MCU must control the cooling fan. Even when the temperature reaches a dangerous value, the system must directly shut down the driver power supply through the MCU, allowing the entire electronic circuit and LED components to temporarily stop running and dissipate heat naturally.
To determine whether the lamp is turned on or off, a simple judgment bit can be used to make changes and understand the current usage status of the product. The more critical part is the temperature measurement. The measured temperature must be compared with the system's reference table in real time to confirm the normal or abnormal degree of the current module status. After calculating the temperature interval, temperature control management is automatically performed accordingly.
Similarly, when the temperature enters the danger zone, the control mechanism should immediately shut down the light source and re-confirm the temperature 60 seconds or 180 seconds after the system is shut down. When the temperature of the LED solid-state light source module reaches the normal value, the LED light source is re-driven to continue providing lighting.
The housing of the embedded lamp is made of extruded aluminum or heat sink design, which can play a role in self-heating.
Previous article:Several key technical issues that need to be solved in LED lighting applications
Next article:How to strike a balance between LED lighting and luminous efficiency?
Recommended ReadingLatest update time:2024-11-16 21:55
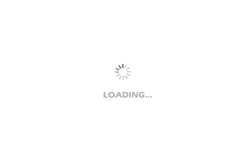
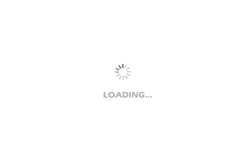
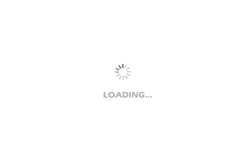
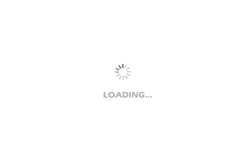
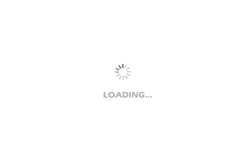
- Popular Resources
- Popular amplifiers
- MathWorks and NXP Collaborate to Launch Model-Based Design Toolbox for Battery Management Systems
- STMicroelectronics' advanced galvanically isolated gate driver STGAP3S provides flexible protection for IGBTs and SiC MOSFETs
- New diaphragm-free solid-state lithium battery technology is launched: the distance between the positive and negative electrodes is less than 0.000001 meters
- [“Source” Observe the Autumn Series] Application and testing of the next generation of semiconductor gallium oxide device photodetectors
- 采用自主设计封装,绝缘电阻显著提高!ROHM开发出更高电压xEV系统的SiC肖特基势垒二极管
- Will GaN replace SiC? PI's disruptive 1700V InnoMux2 is here to demonstrate
- From Isolation to the Third and a Half Generation: Understanding Naxinwei's Gate Driver IC in One Article
- The appeal of 48 V technology: importance, benefits and key factors in system-level applications
- Important breakthrough in recycling of used lithium-ion batteries
- Innolux's intelligent steer-by-wire solution makes cars smarter and safer
- 8051 MCU - Parity Check
- How to efficiently balance the sensitivity of tactile sensing interfaces
- What should I do if the servo motor shakes? What causes the servo motor to shake quickly?
- 【Brushless Motor】Analysis of three-phase BLDC motor and sharing of two popular development boards
- Midea Industrial Technology's subsidiaries Clou Electronics and Hekang New Energy jointly appeared at the Munich Battery Energy Storage Exhibition and Solar Energy Exhibition
- Guoxin Sichen | Application of ferroelectric memory PB85RS2MC in power battery management, with a capacity of 2M
- Analysis of common faults of frequency converter
- In a head-on competition with Qualcomm, what kind of cockpit products has Intel come up with?
- Dalian Rongke's all-vanadium liquid flow battery energy storage equipment industrialization project has entered the sprint stage before production
- Allegro MicroSystems Introduces Advanced Magnetic and Inductive Position Sensing Solutions at Electronica 2024
- Car key in the left hand, liveness detection radar in the right hand, UWB is imperative for cars!
- After a decade of rapid development, domestic CIS has entered the market
- Aegis Dagger Battery + Thor EM-i Super Hybrid, Geely New Energy has thrown out two "king bombs"
- A brief discussion on functional safety - fault, error, and failure
- In the smart car 2.0 cycle, these core industry chains are facing major opportunities!
- The United States and Japan are developing new batteries. CATL faces challenges? How should China's new energy battery industry respond?
- Murata launches high-precision 6-axis inertial sensor for automobiles
- Ford patents pre-charge alarm to help save costs and respond to emergencies
- New real-time microcontroller system from Texas Instruments enables smarter processing in automotive and industrial applications
- Factory Automation Linear Position Sensors Feature Requirements in Various Industries
- Zhuhai is looking for embedded engineers
- Baud rate adaptation of TI DSP chip SCI module
- Shenzhen Industry Exhibition Recruitment: Product Engineer, Technical Support Engineer
- Thank you for being there + looking forward to EEWORLD in 2020
- Playing with Zynq Serial 38——[ex57] Zynq AXI HP bus bandwidth test
- Discussion about littleFS in Micropython official forum
- [GD32E231 DIY Contest] (Part 3): TIMER2_CH1 PWM output
- Application of LoRa technology and Bluetooth technology in electronic display boards
- SensorTile.boxr's personal experience