Introduction
As the laptop backlight that everyone is familiar with is composed of many LED lamp beads, the color difference problem is becoming more and more obvious. If the LED lamp beads used are not from the same batch, it is easy to cause problems such as different wavelengths and color differences. This problem is inevitable even if the LED lamp beads from the same batch are used. For the testing of LED chips, an integrating sphere test system is generally used.
Using an integrating sphere to measure parameters such as luminous flux can make the measurement results more reliable. The integrating sphere can reduce and eliminate errors caused by differences in the shape and divergence angle of light. Such high-precision and cautious measurements have also driven LED integrating sphere manufacturers to increasingly choose higher-performance power supplies to be configured in the system to power the LED to be tested.
LED integrating sphere test system
LED integrating spheres mainly measure parameters such as the luminous efficiency, color rendering and color difference of LED lamps, which characterize the performance indicators of LED light sources. In the daily large-scale testing of the production line, there are always two problems: one is how to improve the test efficiency and the other is how to better protect the LED to be tested during the measurement.
It is understood that in the current power supply industry, the total time from the power supply turning on to power the LED lamp to the software control system collecting stable voltage and current values is about 600ms. Is there a possibility of breakthrough on this basis? The answer is yes. So what methods can be used to achieve it? In fact, the power supply configured in the system to power the LED to be tested plays a very important role.
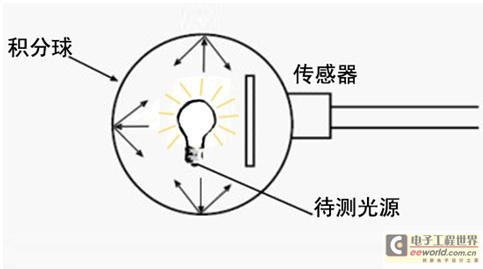
LED integrating sphere test system schematic diagram
1. Configuring a professional power supply can suppress overshoot and improve test efficiency.
At the moment of power on, due to the existence of the loop response time, the power supply output does not stop output when it reaches the set output voltage value. Therefore, during this period of time, the voltage will overshoot. Excessive overshoot voltage will affect the life of the LED, and even break down the LED in severe cases.
For low-power LED lamps, the constant current working current is usually between tens and hundreds of mA. When working at a low current, the current and voltage climbing speeds decrease accordingly. Sometimes, the time it takes to light up the LED is even longer than the time it takes to add up the time from normal power supply to the LED lamp to the time the software control system collects the stable voltage and current values.
In the face of the above two problems, if measures to improve the loop speed are taken to speed up the climbing speed and improve the test efficiency, it usually leads to more serious overshoot. However, if the overshoot problem is taken care of, the overall test efficiency will decrease. Such a problem can be solved by configuring a power supply for professional LED testing. For example, the IT6874A power supply of ITECH can solve this problem. The following two figures are waveforms of the voltage rising stage when the IT6874A DC power supply powers 80V/20mA and 80V/400mA LEDs.
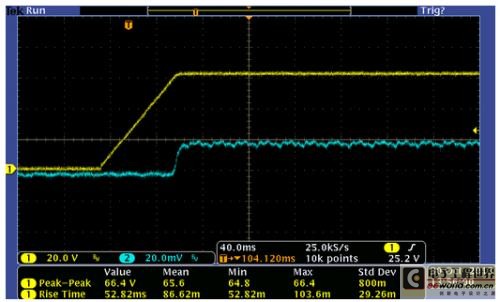
Figure 1: LED (80V/20mA) IT6874A ramp-up time: about 80ms
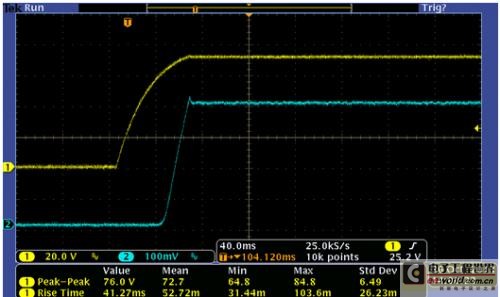
Figure 2: LED (80V/400mA) IT6874A ramp-up time: about 50ms
From the above figure, it can be seen that the IT6874A DC power supply of Itech can basically meet the test requirements of high speed and no overshoot within 100ms, while the general power supply takes about 600ms. The IT6874A DC power supply of Itech has increased this number by nearly 6 times, which is of great significance to the improvement of test efficiency.
2. Configuring a professional power supply makes the value collected by the integrating sphere test system more stable
When using the integrating sphere test, the stability of the power supply in the system is also very important. Stability is mainly reflected in:
(1) The error range of the power supply
When performing the integrating sphere test, if the accuracy of the power supply used is higher, the measured data will be closer to the true value during batch testing, and the deviation between the LEDs to be tested will also be more accurate. For example, when testing LED lamps, assuming that the allowable error range of the power supply readback value is 20mV, when measuring two LED lamps (theoretical rated indicators are both 350mA), the measured value of #1-LED may be 330mA, and the measured value of #2-LED may be 370mA. Assuming that the actual values of these two LED lamps are both 352mA, it can be seen that the values of 330mA and 370mA are far from the actual values, and also cause the performance indicators of the two LED lamps to deviate greatly. If a power supply with higher accuracy is used, assuming that the allowable error range of the voltage readback value is 10mV, the value obtained by testing the same two LED lamps may be between 342mV and 362mV, which is closer in value and can more truly reflect the performance indicators of a single LED lamp and the deviation range of consistency between multiple LEDs.
The voltage accuracy of the IT6874A series power supply of ITECH is as high as 0.5% and the current accuracy is as high as 0.1%. Such high accuracy can bring more accurate test results.
(2) Stability of collected values
What does stability of collected values mean? Let's take an example. For example, the power supply can light up the LED lamp within 400ms (the parameters of the LED lamp to be tested are 80V/20mA). At this time, the voltage value collected by the integrating sphere test system software is 80.099V. When the LED lamp is turned off and turned on again, the value read by the software may be 82.152V. Therefore, using an oscilloscope alone, we can only see that the waveform rises to the rated current and voltage values, but it cannot guarantee that the values collected by the software also reach a stable range. This will affect the test of LED lamp performance indicators during LED mass production testing due to the instability of the power supply value. Generally, software engineering developers will delay to 500-600ms to ensure the stability of the values during continuous reading operations. Therefore, the time required for the integrating sphere test is about 600ms, rather than the 400ms measured by the oscilloscope.
The ITECH IT6874A DC power supply can ensure that the time from lighting the LED lamp to reading the stable voltage and current values is less than 150ms. IT6874A
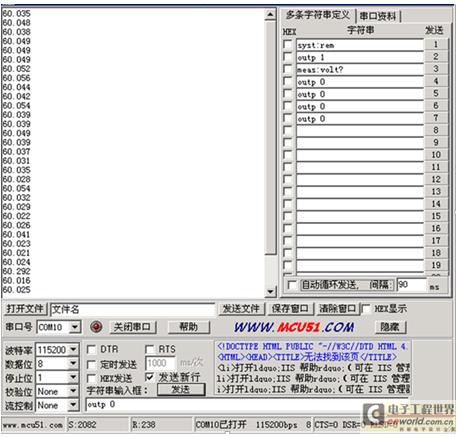
measures LED lamp parameters: 60V/20mA takes about 150ms.
It can be seen that it is of great significance to configure a power supply professionally used for LED testing in the LED integrating sphere test system. The ITECH IT6874A DC power supply breaks through the defects of general power supplies in the LED integrating sphere test system, can perfectly suppress the overshoot at the start-up moment, and greatly improve the test efficiency.
About ITECH
ITECH is the fourth largest instrument company in the United States.
In terms of products, ITECH is mainly committed to the research of power supplies, electronic loads, and some test systems and test software related to power supply testing. It has a product series with outstanding performance and strong stability, programmable single-channel and multi-channel electronic loads, programmable single-channel and multi-channel power supplies, and some products related to power supply testing, such as ATE test systems, battery test systems, and professional test software for new energy, etc. In addition, it also provides sales of some general instruments, such as LCR meters, oscilloscopes, spectrum analyzers, etc. In terms of services, the marketing and service network of ITECH products is spread all over the world. There are ITECH marketing and service outlets in the United States, France, Israel, South Korea, India, Taipei and mainland China, providing customers with the most intimate product sales and after-sales services.
Reference address:The influence of the power supply configured in the LED integrating sphere test system on the test
As the laptop backlight that everyone is familiar with is composed of many LED lamp beads, the color difference problem is becoming more and more obvious. If the LED lamp beads used are not from the same batch, it is easy to cause problems such as different wavelengths and color differences. This problem is inevitable even if the LED lamp beads from the same batch are used. For the testing of LED chips, an integrating sphere test system is generally used.
Using an integrating sphere to measure parameters such as luminous flux can make the measurement results more reliable. The integrating sphere can reduce and eliminate errors caused by differences in the shape and divergence angle of light. Such high-precision and cautious measurements have also driven LED integrating sphere manufacturers to increasingly choose higher-performance power supplies to be configured in the system to power the LED to be tested.
LED integrating sphere test system
LED integrating spheres mainly measure parameters such as the luminous efficiency, color rendering and color difference of LED lamps, which characterize the performance indicators of LED light sources. In the daily large-scale testing of the production line, there are always two problems: one is how to improve the test efficiency and the other is how to better protect the LED to be tested during the measurement.
It is understood that in the current power supply industry, the total time from the power supply turning on to power the LED lamp to the software control system collecting stable voltage and current values is about 600ms. Is there a possibility of breakthrough on this basis? The answer is yes. So what methods can be used to achieve it? In fact, the power supply configured in the system to power the LED to be tested plays a very important role.
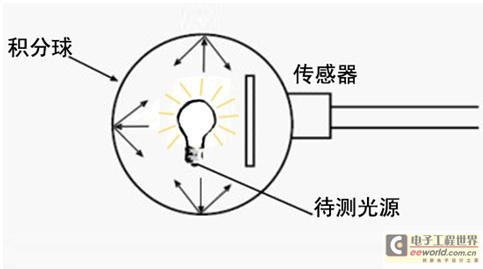
LED integrating sphere test system schematic diagram
1. Configuring a professional power supply can suppress overshoot and improve test efficiency.
At the moment of power on, due to the existence of the loop response time, the power supply output does not stop output when it reaches the set output voltage value. Therefore, during this period of time, the voltage will overshoot. Excessive overshoot voltage will affect the life of the LED, and even break down the LED in severe cases.
For low-power LED lamps, the constant current working current is usually between tens and hundreds of mA. When working at a low current, the current and voltage climbing speeds decrease accordingly. Sometimes, the time it takes to light up the LED is even longer than the time it takes to add up the time from normal power supply to the LED lamp to the time the software control system collects the stable voltage and current values.
In the face of the above two problems, if measures to improve the loop speed are taken to speed up the climbing speed and improve the test efficiency, it usually leads to more serious overshoot. However, if the overshoot problem is taken care of, the overall test efficiency will decrease. Such a problem can be solved by configuring a power supply for professional LED testing. For example, the IT6874A power supply of ITECH can solve this problem. The following two figures are waveforms of the voltage rising stage when the IT6874A DC power supply powers 80V/20mA and 80V/400mA LEDs.
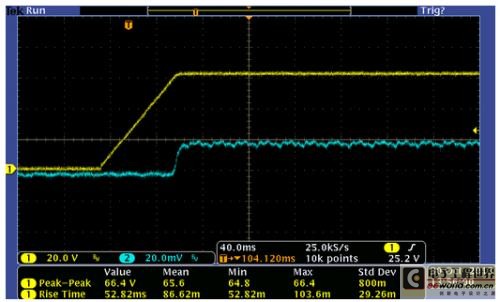
Figure 1: LED (80V/20mA) IT6874A ramp-up time: about 80ms
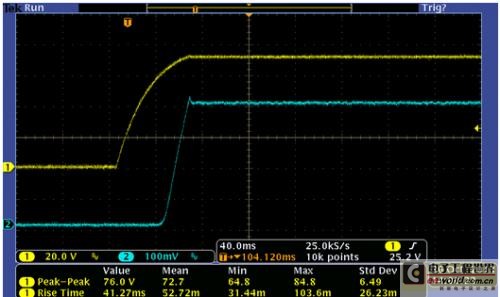
Figure 2: LED (80V/400mA) IT6874A ramp-up time: about 50ms
From the above figure, it can be seen that the IT6874A DC power supply of Itech can basically meet the test requirements of high speed and no overshoot within 100ms, while the general power supply takes about 600ms. The IT6874A DC power supply of Itech has increased this number by nearly 6 times, which is of great significance to the improvement of test efficiency.
2. Configuring a professional power supply makes the value collected by the integrating sphere test system more stable
When using the integrating sphere test, the stability of the power supply in the system is also very important. Stability is mainly reflected in:
(1) The error range of the power supply
When performing the integrating sphere test, if the accuracy of the power supply used is higher, the measured data will be closer to the true value during batch testing, and the deviation between the LEDs to be tested will also be more accurate. For example, when testing LED lamps, assuming that the allowable error range of the power supply readback value is 20mV, when measuring two LED lamps (theoretical rated indicators are both 350mA), the measured value of #1-LED may be 330mA, and the measured value of #2-LED may be 370mA. Assuming that the actual values of these two LED lamps are both 352mA, it can be seen that the values of 330mA and 370mA are far from the actual values, and also cause the performance indicators of the two LED lamps to deviate greatly. If a power supply with higher accuracy is used, assuming that the allowable error range of the voltage readback value is 10mV, the value obtained by testing the same two LED lamps may be between 342mV and 362mV, which is closer in value and can more truly reflect the performance indicators of a single LED lamp and the deviation range of consistency between multiple LEDs.
The voltage accuracy of the IT6874A series power supply of ITECH is as high as 0.5% and the current accuracy is as high as 0.1%. Such high accuracy can bring more accurate test results.
(2) Stability of collected values
What does stability of collected values mean? Let's take an example. For example, the power supply can light up the LED lamp within 400ms (the parameters of the LED lamp to be tested are 80V/20mA). At this time, the voltage value collected by the integrating sphere test system software is 80.099V. When the LED lamp is turned off and turned on again, the value read by the software may be 82.152V. Therefore, using an oscilloscope alone, we can only see that the waveform rises to the rated current and voltage values, but it cannot guarantee that the values collected by the software also reach a stable range. This will affect the test of LED lamp performance indicators during LED mass production testing due to the instability of the power supply value. Generally, software engineering developers will delay to 500-600ms to ensure the stability of the values during continuous reading operations. Therefore, the time required for the integrating sphere test is about 600ms, rather than the 400ms measured by the oscilloscope.
The ITECH IT6874A DC power supply can ensure that the time from lighting the LED lamp to reading the stable voltage and current values is less than 150ms. IT6874A
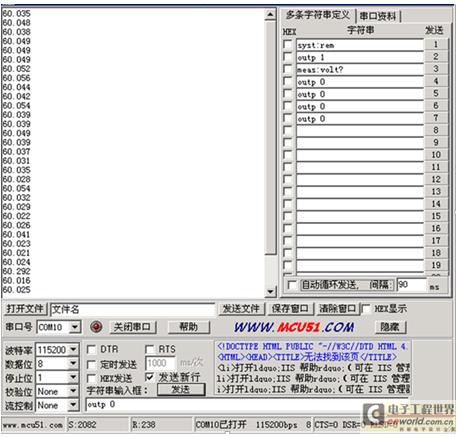
measures LED lamp parameters: 60V/20mA takes about 150ms.
It can be seen that it is of great significance to configure a power supply professionally used for LED testing in the LED integrating sphere test system. The ITECH IT6874A DC power supply breaks through the defects of general power supplies in the LED integrating sphere test system, can perfectly suppress the overshoot at the start-up moment, and greatly improve the test efficiency.
About ITECH
ITECH is the fourth largest instrument company in the United States.
In terms of products, ITECH is mainly committed to the research of power supplies, electronic loads, and some test systems and test software related to power supply testing. It has a product series with outstanding performance and strong stability, programmable single-channel and multi-channel electronic loads, programmable single-channel and multi-channel power supplies, and some products related to power supply testing, such as ATE test systems, battery test systems, and professional test software for new energy, etc. In addition, it also provides sales of some general instruments, such as LCR meters, oscilloscopes, spectrum analyzers, etc. In terms of services, the marketing and service network of ITECH products is spread all over the world. There are ITECH marketing and service outlets in the United States, France, Israel, South Korea, India, Taipei and mainland China, providing customers with the most intimate product sales and after-sales services.
Previous article:AMETEK Sorensen Solutions for Laser Diode Testing
Next article:Vibration signal measurement system of PVDF sensor and WSN
- Popular Resources
- Popular amplifiers
Recommended Content
Latest Test Measurement Articles
- Keysight Technologies Helps Samsung Electronics Successfully Validate FiRa® 2.0 Safe Distance Measurement Test Case
- From probes to power supplies, Tektronix is leading the way in comprehensive innovation in power electronics testing
- Seizing the Opportunities in the Chinese Application Market: NI's Challenges and Answers
- Tektronix Launches Breakthrough Power Measurement Tools to Accelerate Innovation as Global Electrification Accelerates
- Not all oscilloscopes are created equal: Why ADCs and low noise floor matter
- Enable TekHSI high-speed interface function to accelerate the remote transmission of waveform data
- How to measure the quality of soft start thyristor
- How to use a multimeter to judge whether a soft starter is good or bad
- What are the advantages and disadvantages of non-contact temperature sensors?
MoreSelected Circuit Diagrams
MorePopular Articles
- Innolux's intelligent steer-by-wire solution makes cars smarter and safer
- 8051 MCU - Parity Check
- How to efficiently balance the sensitivity of tactile sensing interfaces
- What should I do if the servo motor shakes? What causes the servo motor to shake quickly?
- 【Brushless Motor】Analysis of three-phase BLDC motor and sharing of two popular development boards
- Midea Industrial Technology's subsidiaries Clou Electronics and Hekang New Energy jointly appeared at the Munich Battery Energy Storage Exhibition and Solar Energy Exhibition
- Guoxin Sichen | Application of ferroelectric memory PB85RS2MC in power battery management, with a capacity of 2M
- Analysis of common faults of frequency converter
- In a head-on competition with Qualcomm, what kind of cockpit products has Intel come up with?
- Dalian Rongke's all-vanadium liquid flow battery energy storage equipment industrialization project has entered the sprint stage before production
MoreDaily News
- Allegro MicroSystems Introduces Advanced Magnetic and Inductive Position Sensing Solutions at Electronica 2024
- Car key in the left hand, liveness detection radar in the right hand, UWB is imperative for cars!
- After a decade of rapid development, domestic CIS has entered the market
- Aegis Dagger Battery + Thor EM-i Super Hybrid, Geely New Energy has thrown out two "king bombs"
- A brief discussion on functional safety - fault, error, and failure
- In the smart car 2.0 cycle, these core industry chains are facing major opportunities!
- The United States and Japan are developing new batteries. CATL faces challenges? How should China's new energy battery industry respond?
- Murata launches high-precision 6-axis inertial sensor for automobiles
- Ford patents pre-charge alarm to help save costs and respond to emergencies
- New real-time microcontroller system from Texas Instruments enables smarter processing in automotive and industrial applications
Guess you like
- How UWB calculates location
- [Repost] When choosing a finished power module, should you use an isolated or non-isolated power solution?
- Qorvo Q&A on Connectivity: Reducing Wi-Fi Interference
- What device is used to heat the chip on the motherboard in low temperature outdoor conditions?
- CB5654 Development Board Evaluation 3 - Building a Development Environment
- Two-phase brushless DC motor speed control system based on DSP and CPLD
- 15. [Learn LPC1768 library functions]
- Anxinke PB-02 module review (1) - Compilation environment construction & appearance display
- 3. [Record] Two library files that must be installed by the GCC compiler
- APM32E103 MINI development board information (software resource package, schematic diagram, user manual, etc.)