0 Introduction
The research of biosensors has great application prospects. In recent years, with the discovery of electron spin phenomenon, GMR devices prepared by semiconductor microelectronics technology have aroused more and more research interests in the field of biological detection, making it one of the alternatives to traditional biological detection methods. Due to its unique physical properties, GMR sensors are more sensitive and repeatable than electronic sensors, have a wider operating temperature, operating voltage, and excellent resistance to mechanical shock and vibration, and the working point of GMR sensors will not shift over time. The preparation cost and detection cost of GMR sensors are low, and the demand for samples is very small. The array composed of GMR sensors can also be combined with existing IC processes to improve the integration of the overall equipment and perform multi-target detection. At the same time, compared with the traditional fluorescence detection method, the magnetic label does not have strong environmental noise, the label itself will not gradually fade, and does not require expensive optical scanning equipment and professional operators. Therefore, both the performance of the sensor itself and the characteristics of the magnetic label determine that the research on GMR sensor arrays in the field of biological detection has high application value and practical significance.
1 Basic principles of giant magnetoresistive array sensor biodetection
1.1 Giant Magnetoresistance (GMR) Effect
In 1988, researchers at Perezon University discovered the GMR effect, a quantum effect observed in a structure where ferromagnetic layers and non-ferromagnetic layers are alternately stacked. It refers to the characteristic that the magnetoresistance of certain magnetic or alloy materials decreases sharply under a certain magnetic field, while Aρ/ρ increases sharply. The increase is generally about 10 times higher than the magnetoresistance of ordinary magnetic and alloy materials. The theory of the GMR effect is very complex, and many mechanisms are still unclear. The generally accepted explanation is the two-stream model, as shown in Figure 1. The direction of the magnetic moments in multiple ferromagnetic layers is controlled by the applied external magnetic field. When the magnetic moments of the ferromagnetic layers are arranged in antiparallel, as shown in Figure 1 (a), the spin scattering of the carriers is the largest, and the resistance of the multilayer film is the highest; when the magnetic moments of the ferromagnetic layers are arranged in parallel, as shown in Figure 1 (b), the spin scattering of the carriers is the smallest, and the resistance of the multilayer film is the lowest.
At present, according to their structure, GMR materials can be divided into multilayer films with interlayer coupling characteristics (such as Fe/Cr), spin valve multilayer films (such as FeMn/FeNi/Cu/FeNi), granular multilayer films (such as Fe-Co) and perovskite oxide multilayer films (such as AMnO3), etc.
1.2 Electronic properties of giant magnetoresistance (GMR)
Figure 2 shows the change in resistance of a typical multilayer GMR material under an external magnetic field. The output in Figure 2 shows that whether the external magnetic field changes in the positive or reverse direction, it can bring about the same change in magnetoresistance, that is, the GMR effect is omnipolar. The slope of the curve reflects the degree of magnetic sensitivity, usually in units of V (mV) / Oe. When the resistance value does not continue to change with the magnetic field, the magnetic material has reached its magnetic saturation region. The offset in the two curves is caused by the hysteresis of the magnetic material. The change in resistance from zero magnetic field to saturation magnetic field is called magnetoresistance.
[page]
1.3 Basic modes of biodetection using GMR array sensors
GMR array sensors are used for biological detection. Magnetic particles are used as markers. Direct labeling or two-step labeling is used. Under the condition of applying an external magnetic field in a certain direction, the parasitic magnetic field generated by the magnetic marker is detected by a magnetic sensitive sensor, thereby achieving qualitative and quantitative analysis of biological targets. Figure 3 introduces the specific steps of magnetic labeling detection: The direct labeling method is shown in Figure 3 (a). The direct labeling method is to directly bind the marker to the probe. First, a specific biological probe is bound to the sensor surface, and then the sample solution that has been pre-bound to the magnetic particles is added to the reaction pool of the sensor. The specific target molecules in the solution are captured by the probe to complete the labeling.
The two-step labeling method is shown in Figure 3(b). Taking DNA detection as an example, in the first step, a DNA probe chain of known sequence is bound to the surface of a chip embedded with a spin valve sensor, and a DNA target chain solution labeled with biotin is added for sufficient hybridization; in the second step, magnetic particles coated with anti-biotin are added to form a biotin-anti-biotin covalent bond, thereby selectively capturing the magnetic label.
After the labeling reaction is completed, an external gradient magnetic field is used to separate the excess magnetic particles that are not involved in the labeling, and then an excitation magnetic field is applied to magnetize the magnetic markers (magnetic particles). The parasitic magnetic field generated by the magnetized magnetic markers causes the sensor resistance to change, resulting in a signal output that reflects the biological reaction. [page]
2 GMR biological detection system design
At present, research on biomagnetic field detection equipment based on different technologies has been carried out both internationally and domestically, involving spin valve sensors (Spin Valves), inductive sensors (Inductive Sensors), superconducting quantum interference devices (SQUIDs), anisotropic magnetoresistance (AMR) ring sensors, small-scale Hall combination sensors (Hall Crosses) and tunnel junction (TMR) sensors.
In 1998, as a project supported by the Defense Advanced Research Projects Agency (DAR-PA) of the United States, the U.S. Naval Research Laboratory cooperated with NVE Corporation, and David R. Baselt et al. conducted research on biosensors based on giant magnetoresistance technology, and designed and prepared two generations of magnetic bead array counters (BARcⅡ, BARcⅢ) of GMR sensors for biological hybridization analysis, and used them to measure DNA-DNA at the single molecule level, as well as the binding force of antibody-antigen pairs and receptor-ligand pairs. Research institutions such as Bielefeld University in Germany, Florida State University in the United States, Stanford University in the United States, and the National Institute of Computer Systems and Engineering (INESC-MN) in Portugal have also successively carried out biological detection research on magnetic sensor arrays. Since 2005, many domestic universities and research institutes, such as the Institute of Physics of the Chinese Academy of Sciences, Tsinghua University, Tongji University, University of Electronic Science and Technology of China, and Sun Yat-sen University, have conducted extensive research on giant magnetoresistance biosensor array design, sensor material selection, the relationship between magnetic labels and sensor size, and output signal processing, and have achieved the detection of single nanoscale particles and applied for related patents.
Figure 4(a) shows a spin valve sensor array prepared by Guanxiong Li et al. on the surface of a chip of approximately 7 mm × 8 mm. The array contains 60 submicron strip spin valve sensors arranged in two vertical columns, with 30 sensor units in each column. Aluminum with a thickness of approximately 300 nm is deposited at both ends of each unit by ion beam as leads, and the uncovered strip area in the middle serves as a biological reaction zone for sensing the magnetic field component in the same direction as its easy axis.
Figure 4(b) shows a sensor array (BARCⅢ) containing 66 GMR units designed and prepared by David R. Baselt et al. It is divided into 8 reaction zones, with 8 units in each zone, and can perform multi-channel detection. The unit is circular, with a diameter of 200μm, and is formed by a resistor snake with a length of 8 mm and a width of 1.6μm. [page]
Usually, the entire GMR biodetection system consists of a microfluidic part, a GMR array, a driving part, and an analysis and processing part. In order to reduce the impact of the external environment on the stability of the sensor output, the sensor unit is often combined with the reference unit to form a Wheatstone bridge. As shown in Figure 5, the GMR resistor pair forms a Wheatstone half-bridge, in which the surface of one resistor is covered with a soft magnetic shielding layer and is not affected by the external magnetic field; the other resistor is used as a strain resistor. Under the action of the GMR effect, the resistance value changes with the external magnetic field, resulting in the bridge outputting a differential voltage value of the microvolt level. The output voltage is filtered, amplified, and then transmitted to the back-end acquisition and detection equipment for further analysis.
In 2005, D. K. Wood and others from the Department of Physics at the University of California developed a new generation of sub-micro GMR biosensors that can detect small-sized magnetic beads (200 nm in diameter) with higher sensitivity. Although the magnetic biodetection system has achieved certain results, it is still a long way from practical application.
By integrating existing technologies and improving the performance of magnetic bioassay systems, improvements can be made in sensor characteristics, selection of magnetic particles, and design of peripheral circuits.
3.1 Sensor sensitivity
The sensitivity of a GMR sensor refers to its ability to sense weak signals. Since the magnetic marker is very small, the parasitic magnetic field it generates is also very weak, so a highly sensitive magnetic material must be used to prepare the sensor. The two most basic parameters for measuring GMR performance are:
(1) The maximum GMR value that can be achieved at a certain temperature;
(2) The saturation external magnetic field strength required to obtain the maximum GMR effect.
Among various giant magnetoresistance materials, the saturation magnetic field of multilayer and granular films is as high as several Tesla, but their magnetic field sensitivity is low; the saturation field of oxide ceramic materials is extremely high, making it difficult to achieve practical application; the saturation magnetic field of spin valve materials is relatively low, only a few or tens of Oersteds, but the GMR is not high at room temperature. Therefore, seeking alloy systems or artificial thin film structures with high GMR values, low saturation magnetic fields, and high magnetic field sensitivity is the difficulty and focus of the practical application of GMR sensors for biological detection.
At present, considering the difficulty of production and the stability of performance, sensor arrays mostly use GMR multilayer film coupling structure and spin valve structure. With the gradual deepening of research work, structures with higher magnetoresistance, such as tunneling magnetoresistance (TMR), rare earth oxides, microcrystalline or amorphous soft magnetic alloy films, and high-sensitivity sensors using giant magnetoimpedance effect (GMI), will be used in magnetic biological array detection in the future.
3.2 Size and magnetic content of magnetic particles
In the whole system, the biospecific reaction is reflected by the presence and quantity of magnetic particles. The magnetic particles currently used (such as γ-Fe2O3, Fe3O4, NiFe, etc.) can be divided into two categories: micron-sized and submicron-sized. Larger magnetic particles (about 1-3 μm) are easier to achieve uniformity in shape. Although the content of magnetic substances is low (about 15%), the magnetic field component generated by the magnetic particles on the sensor surface is still large due to the relatively large volume. In addition, the large volume is also convenient for microscopic counting. Its disadvantage is that it cannot be bound to the sensor surface at a high density, so fewer biological molecules are detected. Nanoscale magnetic particles have a high magnetic content (70% to 80%), but due to the limitations of the preparation process, the size and shape of the same batch vary greatly, which is very unfavorable for quantitative analysis. Moreover, small nanomagnetic particles tend to cluster quickly, resulting in output signal distortion. However, the use of more sensitive sensors and more advanced detection and analysis systems can partially meet the application requirements of small-volume magnetic particles. In 2005, Guanxi Li et al. from Stanford University in the United States experimentally verified that when the size of the spin valve sensor array is close to the size of the magnetic particles (superparamagnetic Fe3O4 particles with a diameter of 16 nm), the sensor output signal is in a relatively ideal positive proportional relationship with the number of bound particles, thus reflecting the quantitative analysis capability of the spin valve sensor array in biological detection using small-volume nanomagnetic labels.
3.3 Physical parameters of the sensor array
The appropriate layer thickness of the GMR sensor can ensure that the two magnetic layers are antiparallel coupled, thereby ensuring that the device is in a high resistance state in the absence of an external magnetic field. In addition, because the resistance value of the GMR sensor mainly depends on electron spin scattering, its layer thickness must be smaller than the mean free path of electrons in most materials (about a few nanometers). The layer thickness of a typical GMR magnetic sensor is about 2 to 6 nm.
At the same time, the use of sensors with the same scale as biological molecules (proteins, DNA, RNA and viruses are all in the scale range of 1 to 100 nm) can effectively increase the sensitivity of detection. At present, it is still very difficult to reduce the size of sensors due to the complexity of preparation. Domestic research institutions use traditional optical lithography technology, which is limited by factors such as light wavelength and numerical aperture, and it is difficult to produce patterns with a line width less than 100 nm. However, more advanced extreme far-ultraviolet lithography, electron beam direct writing, ion projection lithography, X-ray lithography, electron beam projection and other technologies can overcome the above limitations, but the system is complex and the cost is very expensive. Therefore, new preparation technologies such as immersion lithography systems, microcontact printing, and nanoimprint lithography based on improved traditional lithography technology will be the most promising technology for batch acquisition of nanoscale GMR sensor arrays on the surface of substrates.
In addition to the physical parameters of the sensor itself, the GMR sensor is also very sensitive to the distance of the magnetic field. The parasitic magnetic field of the magnetic particles decays in the third order with the distance from the sensor's sensitive layer. Therefore, the distance between the sensor and the magnetic marker should be minimized to reduce the excessive requirements for sensor sensitivity. However, in actual detection, in order to prevent the sensor surface from being corroded by biological solutions and firmly bind to biological probes, the sensor surface must be covered with a protective layer (7 nm. PEI/PMMA; 1μm silicon nitride) and a biological binding layer (metal material, glass, quartz or silicon wafer with silicon oxide on the surface). Therefore, the discovery of ultra-thin inert materials and biological binding materials and the improvement of processes are also essential conditions for improving the performance of magnetic biological detection systems. [page]
3.4 External magnetic field
During the detection, an external excitation magnetic field is required to magnetize the superparamagnetic particles. For different magnetic sensors, the magnetic excitation field can be parallel to the sensor surface or perpendicular to the sensor surface. The parallel method is relatively better than the perpendicular method. When there are no magnetic particles above the sensor, the parallel method will not generate signal output, and even if the excitation field is deflected at a certain angle, it will not cause the generation of on-chip components. In addition, the excitation field can use a DC excitation field or an AC excitation field. Under the action of the AC excitation field, the sensor outputs an AC signal. Through the phase-locked amplification technology, a higher signal-to-noise ratio can be obtained, which is convenient for signal extraction. However, compared with the DC excitation field, the AC excitation field will cause electromagnetic interference, and it is necessary to design an AC EMI filter and rectifier filter circuit at the back end, which increases the complexity of the circuit. In addition, the frequency of the external AC excitation magnetic field needs to be balanced. If it is too high, the inductive impedance elements (such as electromagnets) in the system will greatly weaken the signal output by the bridge; if the excitation magnetic field frequency is too low, it will increase the 1/f noise. For some GMR sensors, an external bias magnetic field is also required to fix the free layer, control the sensor to work in the linear range, and prevent the initial polarization of the magnetic particles. However, for sub-micron sensors, since their free layer is already in a single magnetic domain state, no bias field needs to be applied, thereby increasing the degree of freedom of magnetization of the free layer and increasing the sensitivity of the sensor in the easy axis.
3.5 Using signal amplification technology
Since the signal output by the GMR sensor array is very weak, and 1/f noise and shot noise are inevitably present in the signal, in order to accurately measure the amplitude and phase of the biological signal buried in the noise, a phase-locked amplifier consisting of a pre-low noise
4 Conclusion
The research work on the detection of magnetically labeled biomolecules using GMR sensor arrays has been carried out for nearly ten years. Here, the basic principles, development status, and various factors affecting the detection effect of the detection method are introduced and analyzed. At present, the key to restricting the biological detection performance of GMR sensor arrays is the problem of preparation process and materials. In further research, it is necessary to use new GMR sensors with the same scale and high sensitivity as biomolecules, study new biofunctional protective films, and layout more dense arrays with larger effective biological binding surfaces on the chip on the basis of avoiding mutual interference, improve the linearity of the sensor, and ensure the uniformity of the morphology of submicron superparamagnetic particles, so as to effectively promote the application of GMR sensor arrays in biological detection.
Previous article:Design of a crude oil ultrasonic flowmeter
Next article:Design of telerehabilitation information collection system based on fuzzy control
Recommended ReadingLatest update time:2024-11-16 22:47
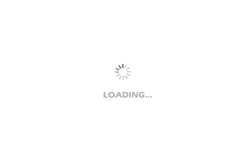
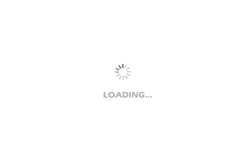
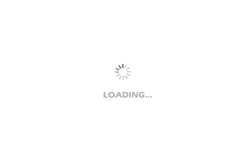
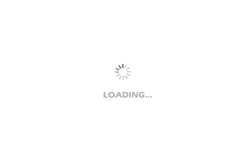
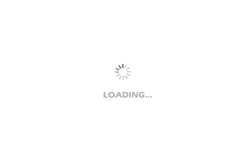
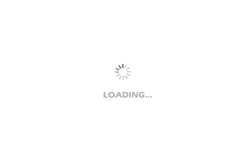
- Popular Resources
- Popular amplifiers
-
Analysis and Implementation of MAC Protocol for Wireless Sensor Networks (by Yang Zhijun, Xie Xianjie, and Ding Hongwei)
-
Introduction to Internet of Things Engineering 2nd Edition (Gongyi Wu)
-
西门子S7-12001500 PLC SCL语言编程从入门到精通 (北岛李工)
-
Modern Motor Control Technology (Wang Chengyuan, Xia Jiakuan, Sun Yibiao)
- Keysight Technologies Helps Samsung Electronics Successfully Validate FiRa® 2.0 Safe Distance Measurement Test Case
- From probes to power supplies, Tektronix is leading the way in comprehensive innovation in power electronics testing
- Seizing the Opportunities in the Chinese Application Market: NI's Challenges and Answers
- Tektronix Launches Breakthrough Power Measurement Tools to Accelerate Innovation as Global Electrification Accelerates
- Not all oscilloscopes are created equal: Why ADCs and low noise floor matter
- Enable TekHSI high-speed interface function to accelerate the remote transmission of waveform data
- How to measure the quality of soft start thyristor
- How to use a multimeter to judge whether a soft starter is good or bad
- What are the advantages and disadvantages of non-contact temperature sensors?
- Innolux's intelligent steer-by-wire solution makes cars smarter and safer
- 8051 MCU - Parity Check
- How to efficiently balance the sensitivity of tactile sensing interfaces
- What should I do if the servo motor shakes? What causes the servo motor to shake quickly?
- 【Brushless Motor】Analysis of three-phase BLDC motor and sharing of two popular development boards
- Midea Industrial Technology's subsidiaries Clou Electronics and Hekang New Energy jointly appeared at the Munich Battery Energy Storage Exhibition and Solar Energy Exhibition
- Guoxin Sichen | Application of ferroelectric memory PB85RS2MC in power battery management, with a capacity of 2M
- Analysis of common faults of frequency converter
- In a head-on competition with Qualcomm, what kind of cockpit products has Intel come up with?
- Dalian Rongke's all-vanadium liquid flow battery energy storage equipment industrialization project has entered the sprint stage before production
- Allegro MicroSystems Introduces Advanced Magnetic and Inductive Position Sensing Solutions at Electronica 2024
- Car key in the left hand, liveness detection radar in the right hand, UWB is imperative for cars!
- After a decade of rapid development, domestic CIS has entered the market
- Aegis Dagger Battery + Thor EM-i Super Hybrid, Geely New Energy has thrown out two "king bombs"
- A brief discussion on functional safety - fault, error, and failure
- In the smart car 2.0 cycle, these core industry chains are facing major opportunities!
- The United States and Japan are developing new batteries. CATL faces challenges? How should China's new energy battery industry respond?
- Murata launches high-precision 6-axis inertial sensor for automobiles
- Ford patents pre-charge alarm to help save costs and respond to emergencies
- New real-time microcontroller system from Texas Instruments enables smarter processing in automotive and industrial applications
- The problem of MCLK frequency of LIS25BA
- 【GD32307E-START】Development practice->UART sends HELLOWORD to the world
- Electromagnetic waves and antennas
- The voltage difference of bq4050 with load is very high, almost 1V. How to solve this problem? It is two strings of batteries.
- 2.4 GHz CDMA Radio Transceiver CYWUSB6934 Application Circuit
- It feels like USB3 isn't popular yet, and USB4 is here!
- On Unjust Death and Redress
- LED stepless color temperature adjustment solution GP9101
- How much does it cost to build a 5G base station? The total investment is staggering
- What is the difference between feedback and howling?