An automated test system (ATS) is a system in which the test instrument, under the control of a computer, provides stimulus to the object under test in a certain timing and sequence, and measures the response of the object under the stimulus. GPIB, VXI, and PXI are the most commonly used standard buses for automatic test systems. The comparison of test platforms built by these buses is shown in Table 1. The emergence of VXI in the 1980s brought high-end measurement and test application equipment into the modular stage. The price of VXI is relatively high. With the development of technology, PXI continues the spirit of modularization and provides a new choice for measurement and test equipment with a more compact architecture design, faster bus speed, and lower price. GPIB is a bus protocol for communication between controllers and programmable instruments, also known as the IEEE2488 standard. It is widely used because of its simple use and high transmission rate. With the improvement of the IEEE488 standard, the transmission rate of the GPIB bus has increased and the cost of instruments with GPIB interfaces has continued to decline. PXI and GPIB are currently widely used test buses in industry. They are stable in performance, easy to operate, flexible in assembly, high in equipment utilization, and low in price, making them suitable for building cost-effective automatic test systems. In addition, the rapid development and continuous improvement of virtual instrument technology and the graphical operation interface of the LabVIEW software platform are very helpful for engineers to quickly master design and programming methods and complete project tasks well and quickly. Therefore, virtual instrument technology has also been widely used in the field of industrial measurement.
Therefore, this paper proposes a PXI plus GPIB bus test system based on LabVIEW platform.
The design idea of the GPIB bus automatic test system is to use the LabVIEW development platform, adopt the software design method of virtual instruments, realize the real-time control of various test instruments by the industrial computer through the GPIB bus interface and the corresponding control circuit, complete the automatic test of various performance indicators of the tested circuit, and give full play to the ability of the industrial computer to automatically analyze and process data. Finally, the data is saved in the form of electronic documents and a test report is generated and printed out.
1 Test system design
1.1 Overall framework design
The test system adopts PXI and GPIB bus interfaces, data acquisition cards and corresponding relay control circuits in hardware design to realize the real-time control of various test instruments by industrial computers. In software design, through the LabVIEW development platform, the software design method of virtual instruments is adopted to organically integrate the hardware resources of industrial computers with the instrument hardware, and the data analysis, display and storage are realized through software, solving the technical problem of realizing database management in LabVIEW.
The testing process should be completed in an automated way.
The automatic test mainly uses the relevant PXI board of NI to complete the detection work under the default setting state. The design idea is to control the connection of the test equipment by controlling the opening and closing of the relay through the digital I/O port. After the required test items are connected, the data acquisition and processing program written by LabVIEW is used to obtain the measurement data, and the measurement results are displayed on the display interface, which is convenient for users to analyze and process and draw corresponding conclusions. Finally, the measurement results are saved in the database, which is convenient for later analysis and writing test reports.
1.2 Signal conditioning unit design
There are multiple differential input signals in the circuit under test. When a signal source is used to generate analog signals, differential conversion is required. The differential conversion circuit is shown in Figure 1.
The analysis is as follows:
Practice has proved that this circuit scheme is feasible.
1.3 Measurement and control equipment hardware
The main equipment used in the automatic test is NI's PXI equipment, using the PXI-1042 chassis and PXI-8196 controller to achieve measurement control. The PXI-8196 controller is an embedded controller with a 2.0 GHz Intel Pentium M760 processor, equipped with dual-channel DDR2 memory, a maximum memory capacity of 2 GB, integrated with 4 USB 2.0 ports, a GPIB interface, as well as serial and parallel ports, pre-installed with the Microsoft Windows XP Professional operating system, and is used in application environments that require a lot of analysis work or system development, such as ATE, military/aerospace, communications, industrial and consumer electronics applications. The data acquisition card uses NI's PXI-6259 data acquisition module, which has 16-bit 1 MS/s (multi-channel), 1.25 MS/s (single channel), 32 SE/16 DI, 48-channel digital I/O timing hardware (≥10 MHz), TTL level, 4-channel 16-bit analog output (2.8 MS/s), and an output range of -10 to +10 V. The arbitrary waveform generator uses NI's PXI-5412, which can provide -6 to +6 V signals and provide sine, square wave and other signals to each signal channel under test. The oscilloscope PXI-5152 has 2 single-ended input channels, each with a real-time sampling rate of 1 GS/s. The dynamic signal analyzer uses NI's PXI-4461, which has 2 differential input channels and 2 analog input channels; the real-time sampling rate of the channel is 204.8 KS/s. This card is used to create a universal dynamic signal analyzer interface for manual measurement.
2 Test System Software Design
2.1 Measurement and control software design tools
The measurement and control software of this system is developed on Visual Basic and LabVIEW software development platforms, and the measurement result data is stored in the SQL database. The software system architecture is shown in Figure 2.
In the PXI measurement and control computer, LabVIEW and various data acquisition and processing modules of NI are used to measure the circuit under test; the GPIB interface is used to communicate with various desktop instruments to obtain automatic or manual measurement results; the ADO interface is used to access the network database, and the data required by various users are continuously submitted to the database during the measurement process, which is convenient for subsequent test information management. It is worth mentioning that whether the operation of each measuring instrument can be synchronized, and whether the order and time of the instrument sending and receiving commands, reading/writing data, and executing instructions can be coordinated will directly affect the reliability of the system, the real-time nature of the test data, and the efficiency of the test system. System synchronization is mainly implemented by software in this system, and appropriate program flows are designed according to the user's service requirements and instrument characteristics.
In order to achieve the versatility of the program, Visual Basic/SQL is selected as a tool for data exchange between the test program and the database to separate the measurement data from the test process. The task of the test process is to read the data of the configuration database according to the test requirements, configure the test instrument, perform corresponding data acquisition, analysis and calculation, and write the results back to the test result database. In the computer, the database is installed, and data management and query software is also attached, and the user is provided with the option of installing other software. In this way, the PXI measurement and control computer will not occupy resources due to the need for database management; in addition, when the PXI measurement and control computer is not enabled, only the general computer is enabled, and the data of the measured board can also be sorted and analyzed. Visual Basic can better connect with the SQL database, query and manage the user's database, and apply Visual Basic in the computer to write data management and query software that facilitates user access to data.
2.2 Measurement and control software structure design
The system's measurement and control software is software running on the PXI measurement and control computer, and its main software hierarchy block diagram is shown in Figure 3. The software adopts a hierarchical structure, and while realizing functional testing, it also has data storage, query and playback functions, and has good practicality and operability.
3 Conclusion
The research and development of this topic is of great significance to the detection of circuits. First, the use of an automated test system greatly improves test efficiency, saves precious time, and can meet the needs of rapid equipment support under information conditions; second, it frees testers from tedious detection tasks, reduces labor intensity, and greatly saves manpower consumption; finally, after the entire test system is connected once, no human intervention is required. You only need to select the test items on the computer and fill in some basic data to start the test. Non-professionals can also complete the test process, which basically eliminates errors caused by human misoperation, improves the credibility of the test results, and ensures the safe use of the system.
Previous article:A New Method for Measuring the Static Capacitance of Quartz Crystal Resonators
Next article:Speed up and simplify serial data testing
Recommended ReadingLatest update time:2024-11-16 16:37
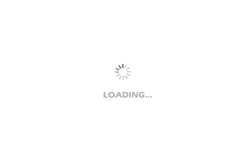
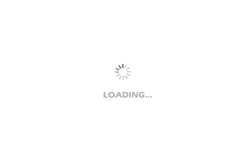
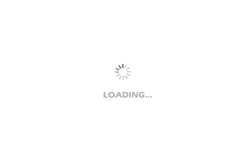
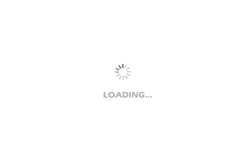
- Popular Resources
- Popular amplifiers
-
Real-time driver monitoring system via modal and viewpoint analysis
-
LabVIEW Programming and Application (Ji Shujiao, Shang Weiwei, Lei Yanmin)
-
Virtual Instrument and LabVIEW Programming (Higher Vocational) (Edited by Chen Dong and Cui Xiuhua)
-
A Practical Tutorial on ASIC Design (Compiled by Yu Xiqing)
- Keysight Technologies Helps Samsung Electronics Successfully Validate FiRa® 2.0 Safe Distance Measurement Test Case
- From probes to power supplies, Tektronix is leading the way in comprehensive innovation in power electronics testing
- Seizing the Opportunities in the Chinese Application Market: NI's Challenges and Answers
- Tektronix Launches Breakthrough Power Measurement Tools to Accelerate Innovation as Global Electrification Accelerates
- Not all oscilloscopes are created equal: Why ADCs and low noise floor matter
- Enable TekHSI high-speed interface function to accelerate the remote transmission of waveform data
- How to measure the quality of soft start thyristor
- How to use a multimeter to judge whether a soft starter is good or bad
- What are the advantages and disadvantages of non-contact temperature sensors?
- Innolux's intelligent steer-by-wire solution makes cars smarter and safer
- 8051 MCU - Parity Check
- How to efficiently balance the sensitivity of tactile sensing interfaces
- What should I do if the servo motor shakes? What causes the servo motor to shake quickly?
- 【Brushless Motor】Analysis of three-phase BLDC motor and sharing of two popular development boards
- Midea Industrial Technology's subsidiaries Clou Electronics and Hekang New Energy jointly appeared at the Munich Battery Energy Storage Exhibition and Solar Energy Exhibition
- Guoxin Sichen | Application of ferroelectric memory PB85RS2MC in power battery management, with a capacity of 2M
- Analysis of common faults of frequency converter
- In a head-on competition with Qualcomm, what kind of cockpit products has Intel come up with?
- Dalian Rongke's all-vanadium liquid flow battery energy storage equipment industrialization project has entered the sprint stage before production
- Allegro MicroSystems Introduces Advanced Magnetic and Inductive Position Sensing Solutions at Electronica 2024
- Car key in the left hand, liveness detection radar in the right hand, UWB is imperative for cars!
- After a decade of rapid development, domestic CIS has entered the market
- Aegis Dagger Battery + Thor EM-i Super Hybrid, Geely New Energy has thrown out two "king bombs"
- A brief discussion on functional safety - fault, error, and failure
- In the smart car 2.0 cycle, these core industry chains are facing major opportunities!
- The United States and Japan are developing new batteries. CATL faces challenges? How should China's new energy battery industry respond?
- Murata launches high-precision 6-axis inertial sensor for automobiles
- Ford patents pre-charge alarm to help save costs and respond to emergencies
- New real-time microcontroller system from Texas Instruments enables smarter processing in automotive and industrial applications
- LED light flickering problem, help
- Realization of various wavelet transforms based on FPGA
- Book a live broadcast with prizes: Enjoy purity - ams active noise reduction and proximity sensing bring a new level of headphone design
- Analog Front End AFE
- Is there any special way to route the wiring of this type of seat?
- Free review: GigaDevice GD32F310G-START
- Please advise, is there any impact if this reset detection chip is removed?
- [Silicon Labs BG22-EK4108A Bluetooth Development Evaluation] Evaluation 2 SOC_Blinky Service Configuration
- Programming classes are coming to primary and secondary schools. What do you think?
- Say goodbye to film! Design a smarter car sunroof