【Abstract/Introduction】
Samtec has developed an innovative, easy-to-use alignment technology to ensure peak performance of precision, high-frequency compression-mount connectors in test and measurement applications. Below is an explanation of the trends we are seeing and an overview of the solutions we have developed for common alignment challenges that arise.
[Problem]
As data rates continue to increase (224Gbps PAM4), the need for precision, high-frequency compression-mount test connectors with bandwidths exceeding 90 GHz is increasing. This is due in part to the known performance advantages of compression mounting compared to solder-type connector solutions, as well as the effects of soldering process variations on PCB and connector construction.
Threaded compression connectors, where the connector is compressed onto the PCB using mounting hardware, operate at higher frequencies and are therefore becoming popular in test applications. In addition, as the number of high-speed connections on PCBs continues to increase, compression-mount connectors offer many additional advantages :
01. Relatively compact, which means that several can be placed side by side on a single PCB, taking up much less space than would traditionally be required.
02. Can be placed anywhere on the PCB. This allows them to be placed close to the device where the signal needs to reach.
03. Can be reused.
04. Can be easily connected to microstrip/CPWG or stripline on PCB
As frequency requirements increase, this will in turn affect the size of the signal pins and pads in the interconnect (including the threaded compression mount products we focus on in this article). This means that the higher the frequency, the smaller the signal pins and pads become. Therefore, alignment becomes more difficult.
Precise alignment of signal pins and pads is critical to peak connector performance. If misaligned, in some cases, it can not only lead to degraded performance, but can also cause the connection to fail completely (open circuit). However, when the connector is placed on the PCB, the signal pins and pads are not visible, so how can you confirm precise alignment? How can engineers easily and correctly confirm alignment within their systems to have confidence that the structure will perform as expected?
Some people often tend to use mounting screws to solve the problem of misalignment. However, one factor that must be considered is that the outer diameter of hardware screws is not precise compared to the size of the screw hole itself. Also, the manufacturability of the PCB may be limited and the tolerance may be much looser than the connector assembly position tolerance allows. Below we see an example of a mounting screw that is not perfectly aligned.
Even if care is taken during the assembly of connectors, the forces on the connectors can cause them to rotate when the screws are tightened into their final position. The images below provide an example, as shown: (a) and (b) are both 1.35 mm, 90 GHz connectors. Although visually magnified to clearly show the misalignment, it is very difficult to identify misalignment during the assembly process. Often this is not apparent until performance has degraded and further inspection is required. Even when misalignment becomes apparent, it is still very difficult to correct for precise alignment during board assembly. Misalignment to the order shown in "(a)" will result in capacitive loading at launch. The ground body of the connector is too close to the surface routing.
Additionally, if the connector moves around, it has the potential to degrade or even damage the pads on the PCB.
The TDR graph below illustrates that when measuring the same 1.35mm connector mentioned above, a capacitive drop of approximately 8 ohms is introduced when the amount of misalignment shown above occurs. When using very wide bandwidths, even small misalignments can have a large impact on the resulting performance. Furthermore, the time lost in performance analysis, troubleshooting, and corrective actions can be extremely costly.
When examining the same 1.35 mm connector in the frequency domain, we see that better alignment results in improved return loss over a large frequency range:
【Solution】
A new technology has been developed in the RF industry for achieving precise alignment when using threaded compression mounted connectors in test and measurement applications. This new technology comes from Samtec and could revolutionize the way these connectors are assembled on PCBs due to its ease of use. It is direct and simple in execution, yet highly effective in achieving optimal connector performance.
This technology provides a visual guide that was not possible before because the alignment of the connector's center pin to the pad was hidden when the connector was assembled to the PCB.
The visual guide uses a combination of alignment slots (or grooves) and targets. Alignment slots are milled into the feet of the compression mount connector. When creating the PCB layout, targets can be incorporated to match the location of these grooves, making it very easy to check the positional accuracy of the assembled connector.
Because the notch is aligned with the target on the PCB, any offset between the mounting hole location and the pad location is easily noticed; thus, eliminating any suspicion of assembly effects affecting subsequent performance measurements. The notch is aligned with the target, ensuring that the center pin of the connector is centered on the PCB pad. This technique can be used for both microstrip/CPWG and stripline connectors.
Here is a recommended PCB layout using a 1.35mm microstrip connector with a target:
The following shows the specifications for a 1.35 mm microstrip connector with alignment slots that match the recommended PCB layout above:
When looking at the VSWR graph below, of a perfectly aligned 1.35mm connector that was assembled using a visual alignment process (e.g. matching the alignment slot to a target on the PCB), we see excellent performance results; especially between 50GHz and 80GHz. At the connector's cutoff frequency, the VSWR is even lower than 1.2:1. In order to thoroughly understand the performance characteristics, we took ten samples.
When threading the instrument test cable onto a compression-mount connector, an anti-rotation tool can be used to secure the connector in place. The recommended procedure is:
01. Using the visual alignment feature mentioned earlier, secure the threaded compression mount connector to the circuit board.
02. Using the anti-rotation tool, screw the cable assembly connector onto the circuit board connector. Use the torque wrench to rotate the cable assembly connector and the anti-rotation tool to stabilize the circuit board connector to ensure minimal movement when completing the assembly process.
【in conclusion】
As data rates approach 224Gbps PAM4, the need for precision, high-frequency compression-mount test connectors continues to increase. However, proper alignment of the connector’s center pin to the pad is critical for optimal performance and expected behavior of the structure. This new vision alignment technology, which uses a connector body with alignment grooves to easily visually align with a target on the PCB, is being widely adopted by the industry and will likely continue to grow in popularity.
The alignment slots discussed above have been incorporated into Samtec's vertical compression mount 1.35mm, 1.85mm, 2.40mm, and 2.92mm board level connectors. Please contact us for product specifications or to place an order.
Previous article:Guoxin Sichen | 24-bit ADC SC1644 (can replace AD7173-8) for liquid flow meter
Next article:Intelligent Insertion Electromagnetic Flowmeter Installation and Use Instructions
Recommended ReadingLatest update time:2024-11-23 07:51
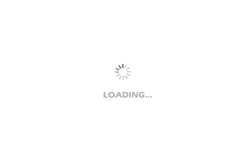
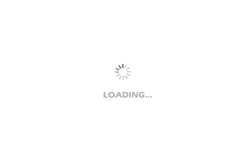
- New IsoVu™ Isolated Current Probes: Bringing a New Dimension to Current Measurements
- Modern manufacturing strategies drive continuous improvement in ICT online testing
- Methods for Correlation of Contact and Non-Contact Measurements
- Keysight Technologies Helps Samsung Electronics Successfully Validate FiRa® 2.0 Safe Distance Measurement Test Case
- From probes to power supplies, Tektronix is leading the way in comprehensive innovation in power electronics testing
- Seizing the Opportunities in the Chinese Application Market: NI's Challenges and Answers
- Tektronix Launches Breakthrough Power Measurement Tools to Accelerate Innovation as Global Electrification Accelerates
- Not all oscilloscopes are created equal: Why ADCs and low noise floor matter
- Enable TekHSI high-speed interface function to accelerate the remote transmission of waveform data
- Intel promotes AI with multi-dimensional efforts in technology, application, and ecology
- ChinaJoy Qualcomm Snapdragon Theme Pavilion takes you to experience the new changes in digital entertainment in the 5G era
- Infineon's latest generation IGBT technology platform enables precise control of speed and position
- Two test methods for LED lighting life
- Don't Let Lightning Induced Surges Scare You
- Application of brushless motor controller ML4425/4426
- Easy identification of LED power supply quality
- World's first integrated photovoltaic solar system completed in Israel
- Sliding window mean filter for avr microcontroller AD conversion
- What does call mean in the detailed explanation of ABB robot programming instructions?
- STMicroelectronics discloses its 2027-2028 financial model and path to achieve its 2030 goals
- 2024 China Automotive Charging and Battery Swapping Ecosystem Conference held in Taiyuan
- State-owned enterprises team up to invest in solid-state battery giant
- The evolution of electronic and electrical architecture is accelerating
- The first! National Automotive Chip Quality Inspection Center established
- BYD releases self-developed automotive chip using 4nm process, with a running score of up to 1.15 million
- GEODNET launches GEO-PULSE, a car GPS navigation device
- Should Chinese car companies develop their own high-computing chips?
- Infineon and Siemens combine embedded automotive software platform with microcontrollers to provide the necessary functions for next-generation SDVs
- Continental launches invisible biometric sensor display to monitor passengers' vital signs
- HT MCU large table reading
- Transformer Overview - Transformer Classic Article (Chinese PDF)
- How to use static protocol stack in BlueNRG series
- To understand the power supply, start with the physical diagram of the power supply's internal structure!
- Wanted Binghuo STM32F103-Badao development board
- [AT-START-F425 Review] + Transplanting u8g2 monochrome graphics library to drive 0.96-inch OLED
- One of the outstanding achievements in the field of communications: scattering communications
- Choosing a Power Management Solution for Handheld Products
- [NXP Rapid IoT Review] + Use of Bluetooth (1 Preliminary Exploration)
- 500 yuan for infrared counting microcontroller