Long-term data logging using transient storage
When an abnormality occurs in the I2C bus signal, it is often impossible to clearly know which device has failed. Therefore, it is impossible to locate the problem point by setting a trigger. Most users will consider capturing all the waveforms first and then slowly analyzing them. However, the logic analyzer basically captures signals in a sampling manner. Regardless of whether the signal changes or not, the memory will continue to be consumed as the sampling and capturing action proceeds. The transitional storage function is a waveform data storage mode that only stores waveform data when the waveform transitions. In this way, when the data does not transition, the logic analyzer can continue to wait and does not store any data in the memory. Compared with the practice of storing data once at each sampling point, transitional storage will be able to record more data. As the transmission speed of I2C is shown in Table 1, the overall speed is not very fast. Therefore, it is very suitable to use transitional storage to extend the storage time.
Using I2C trigger to locate the problem point
For example, the I2C bus on the circuit board connects device A and device B, but during the long burn-in test, an error occurs on the I2C bus. It is known that when an error occurs, an invalid address will appear on the I2C bus, and it will appear several times during the burn-in test. How can a logic analyzer be used to clarify the problem? For such a problem, it is actually difficult to capture all the waveform data. Because the time point and number of problems are very uncertain, and the burn-in test that lasts for several days also makes it impractical to log all the data, and it is necessary to find the problem point in a large amount of data. It is also a very time-consuming and laborious task.
Therefore, the I2C trigger function in the logic analyzer can be used for positioning. First, input the valid addresses of device A (Addr: 12h) and device B (Addr: 34h). Then let the logic analyzer find the addresses that do not meet the above two conditions. The actual setting is shown in Figure 1.
Then, with the automatic storage function after capturing the waveform with the logic analyzer, during the burn-in process, each time the trigger is successful, it will be saved, and then the trigger point of the saved waveform can be checked. Making good use of the I2C trigger function can quickly assist in waveform positioning, which is much more meaningful than capturing more data. Similarly, making good use of the entire I2C parameter as a trigger condition, such as address matching or data matching or multi-stage triggering to specify a more accurate trigger, these are functions that cannot be achieved by simply using the edge trigger (Edge Trigger).
Problems with I2C trigger check timing violation
The I2C bus will regulate SCL and SDA to be sent at the specified time, otherwise the behavior of the entire bus will be wrong, resulting in communication failure. Sometimes the actual waveform time has exceeded the specification, but it cannot be picked out during development and verification, because sometimes the time error is not large, so that the product can still be used normally. But often the problem will not break out until mass production, causing the mass production defect rate to rise. Even problems will not appear until the user has the product. These are all results that product development is not happy to see.
As shown in Figure 2, you can enable the logic analyzer's time violation check as a trigger condition, set the time value to be checked, and then let the logic analyzer help pick out the time violation. The logic analyzer system uses a 200MHz sampling rate for sampling. Therefore, the minimum time width that can be checked is 5ns. In this way, it can assist users to use triggers to perform time violation checks. This method is very suitable for detecting the signal time of the I2C bus during burn-in testing.
Use Schmidt trigger circuit architecture to capture good quality I2C signals
When using a logic analyzer for measurement, some noise is often seen. But when using an oscilloscope, it seems that there is no noise. What is the reason? How to eliminate it? This is because the I2C bus is an open collector structure, and many devices are connected to the bus at the same time, and there are some electrostatic protection parts, etc. It may make the I2C waveform not necessarily a good square wave. Common I2C waveforms are shown in Figures 3 and 4. However, such waveforms are normal and acceptable in the I2C specification and there is no problem.
Because of this, general I2C chips will have a Schmitt trigger circuit at the signal input pin, so as to perfectly solve the problem of correctly processing the logic signal after the signal input. For this reason, the logic analyzer can also use this method to perform a more complete signal decoding operation. Figure 5 shows a general logic analyzer, which uses a single trigger level to distinguish between logic 0 and logic 1. This approach can easily produce many unexpected logic changes when the signal to be tested passes near the trigger level (Threshold). Make the captured signal look like noise or bounce phenomenon.
If a low-pass filter is used, the noise can be filtered out, but the high-frequency noise that may cause line problems is also filtered out. In any case, this is not an appropriate solution.
Figure 6 shows the image after the Schmidt trigger circuit is enabled. This architecture uses two sets of trigger voltages, Thres-high and Thres-low. The area between the two voltages is the so-called non-transition region. Within this range, no matter how the signal changes, it will not affect the logic judgment. In this way, the I2C signal can be captured normally, and the real high-frequency noise will not be missed, which also complies with the I2C chip design specifications.
Stacked oscilloscopes can simultaneously see I2C digital and analog signals
After using the I2C bus trigger and analysis function provided by the logic analyzer, the captured waveform begins the problem analysis stage. Often, many projects involve the cooperation of software and hardware, and many people are involved. If the corresponding analog signal cannot be seen at the same time, it will not be very helpful to clarify the problem. Especially for problems caused by the line, digital signals cannot clearly show the problem points.
However, simply stacking a logic analyzer with an oscilloscope is not helpful, because most of the time the length of time that a logic analyzer can capture is much longer than that of an oscilloscope. In this way, even if the oscilloscope displays the waveform, it is not in the correct position. Only by using the trigger function of the logic analyzer can the signal be located. In this way, the captured analog signal is meaningful. Figure 7 uses stacking and setting triggers to capture both digital and analog signals at the same time. The user can send it to someone who needs to see the waveform. The I2C bus digital decoding part allows the user to quickly understand the waveform he sees. The analog signal part faithfully presents the original appearance of the waveform. This combination of the two becomes the best measurement solution.
Previous article:Application of Vector Network Analyzer Wiltron360B in RF Simulation
Next article:Design of Metal Magnetic Memory Detector Based on DSP and CPLD
Recommended ReadingLatest update time:2024-11-23 10:54
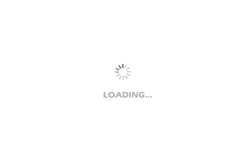
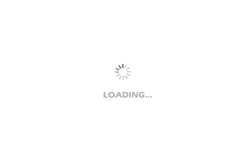
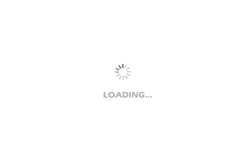
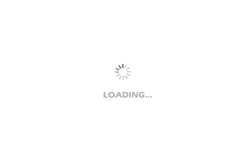
- New IsoVu™ Isolated Current Probes: Bringing a New Dimension to Current Measurements
- Modern manufacturing strategies drive continuous improvement in ICT online testing
- Methods for Correlation of Contact and Non-Contact Measurements
- Keysight Technologies Helps Samsung Electronics Successfully Validate FiRa® 2.0 Safe Distance Measurement Test Case
- From probes to power supplies, Tektronix is leading the way in comprehensive innovation in power electronics testing
- Seizing the Opportunities in the Chinese Application Market: NI's Challenges and Answers
- Tektronix Launches Breakthrough Power Measurement Tools to Accelerate Innovation as Global Electrification Accelerates
- Not all oscilloscopes are created equal: Why ADCs and low noise floor matter
- Enable TekHSI high-speed interface function to accelerate the remote transmission of waveform data
- Intel promotes AI with multi-dimensional efforts in technology, application, and ecology
- ChinaJoy Qualcomm Snapdragon Theme Pavilion takes you to experience the new changes in digital entertainment in the 5G era
- Infineon's latest generation IGBT technology platform enables precise control of speed and position
- Two test methods for LED lighting life
- Don't Let Lightning Induced Surges Scare You
- Application of brushless motor controller ML4425/4426
- Easy identification of LED power supply quality
- World's first integrated photovoltaic solar system completed in Israel
- Sliding window mean filter for avr microcontroller AD conversion
- What does call mean in the detailed explanation of ABB robot programming instructions?
- STMicroelectronics discloses its 2027-2028 financial model and path to achieve its 2030 goals
- 2024 China Automotive Charging and Battery Swapping Ecosystem Conference held in Taiyuan
- State-owned enterprises team up to invest in solid-state battery giant
- The evolution of electronic and electrical architecture is accelerating
- The first! National Automotive Chip Quality Inspection Center established
- BYD releases self-developed automotive chip using 4nm process, with a running score of up to 1.15 million
- GEODNET launches GEO-PULSE, a car GPS navigation device
- Should Chinese car companies develop their own high-computing chips?
- Infineon and Siemens combine embedded automotive software platform with microcontrollers to provide the necessary functions for next-generation SDVs
- Continental launches invisible biometric sensor display to monitor passengers' vital signs
- [Xianji HPM6750 Review 5] LittlevGL transplantation using SPI display
- [RVB2601 Creative Application Development] Project Talk
- How to measure BLE power consumption
- Programmability and flexibility are key, DSP becomes the protagonist in the field of consumer electronics
- TI Embedded Live Month - Registration starts now to support efficient, intelligent and low-power system design~
- Learning classic feelings: My learning experience - how to master DSP
- Four input modes of MCU
- How to replace TMS320C6416TGLZ7 chip
- I would like to ask how to connect the ground on the PCB board of the monitoring equipment and the board ground?
- Serial Interface