Metal tube rotor flowmeter, also known as metal tube float flowmeter, is widely used and is generally used to measure medium, small and micro flows. The measured medium is generally clean, not easy to crystallize and solidify, and has low viscosity liquids, gases and steam, and the medium flow rate is required to change slowly. Whether the instrument is installed correctly is the fundamental guarantee for the subsequent stable operation of the instrument. Whether the instrument can be installed correctly is an important indicator for testing an instrument installation technician. In view of the various influencing factors encountered during the installation, this article introduces the following factors that should be paid attention to when installing the metal tube flowmeter.
1. Instrument installation direction
Most float flowmeters must be installed vertically on vibration-free pipes, without obvious tilt, and the fluid flows through the instrument from bottom to top. Figure 6 shows an example of pipeline connection, with a bypass pipe system installed to facilitate maintenance without interruption of flow. The angle between the center line of the float flowmeter and the plumb line generally does not exceed 5 degrees, and the θ of high-precision (grade 1.5 or above) instruments is ≤20°. If θ=12°, an additional error of 1% will be generated. The instrument has no strict requirements for the length of the upstream straight pipe section, but some manufacturers require a length of (2-5)D, which is actually not necessary.
2. Installation for dirty fluids
A filter should be installed upstream of the instrument. When a metal tube float flowmeter with magnetic coupling is used for fluids that may contain ferromagnetic impurities, a magnetic filter should be installed in front of the instrument.
Keep the float and cone clean, especially for small-diameter instruments, as the cleanliness of the float significantly affects the measured value. For example, a 6mm diameter glass float flowmeter, in the laboratory, measured what looked like clean water, with a flow rate of 2.5L/h. After running for 24 hours, the flow indication increased by a few percent, and the float surface was stained with foreign matter that could not be observed by the naked eye. The float was removed and wiped with gauze, and the original flow indication was restored. If necessary, a flushing pipe can be set as shown in Figure 7 for regular flushing.
3. Installation of pulsating flow
The pulsation of the flow itself, such as a reciprocating pump or regulating valve upstream of the intended instrument location, or a large load change downstream, should be replaced with a measuring position or remedial improvements should be made in the pipeline system, such as adding a buffer tank; if it is the oscillation of the instrument itself, such as the gas pressure is too low during measurement, the upstream valve of the instrument is not fully opened, the regulating valve is not installed downstream of the instrument, etc., targeted improvements should be made to overcome this, or an instrument with a damping device should be selected instead.
4. Installation to expand the range
If the required flow range is wide and the range exceeds 10, more than two glass tube float flowmeters with different flow ranges are often connected in parallel. One or more instruments are selected in series according to the measurement. When the flow rate is small, the value indicated by the instrument with a lower flow range is read. When the flow rate is large, the value indicated by the instrument with a large flow rate is read. The series method is easier to operate than the parallel method, and there is no need to frequently open and close the valve, but the pressure loss is large. You can also put two floats of different shapes and weights in one instrument. When the flow rate is small, take the reading of the light float, and take the reading of the heavy float after the float reaches the top. The range can be expanded to 50-100.
5. Drain the gas in the instrument for liquid
When using an angular metal float flowmeter whose inlet and outlet are not in a straight line, pay attention to whether there is residual air in the extended sleeve of the external float displacement when using it for liquid. It must be exhausted; if the liquid contains tiny bubbles, it is very easy to accumulate in the sleeve when flowing, and the air should be exhausted regularly. This is more important for small-caliber instruments, otherwise the flow indication will be significantly affected.
6. Necessary conversion of flow value
If the instrument is not specially customized to the manufacturer according to the medium parameters such as density and viscosity, the flow rate of liquid instruments is usually calibrated with water, and the flow rate of gas instruments is calibrated with air, and the fixed value is in the engineering standard state. When the fluid density, gas pressure and temperature of the use conditions are inconsistent with the calibration, necessary conversion should be made. The conversion formula and method are detailed in the instruction manual of each manufacturer.
7. Calibration and calibration of float flowmeter
The calibration and calibration of float flowmeter usually uses the standard table method, volumetric method and weighing method for liquid; the bell jar method is usually used for gas, and the soap film method is used for small flow.
The bulk products of some foreign manufacturers have been calibrated by dry method, that is, the size of the tapered tube and the weight size of the float are controlled to indirectly determine the flow value to reduce costs. Only high-precision instruments are calibrated by real flow. Some domestic manufacturers also strictly control the inner diameter and taper of the starting point of the tapered tube and the size of the float. The real flow calibration only serves to check the quality of the inner surface of the tapered tube. The instruments, tapered tubes and floats produced by such manufacturers are interchangeable and do not need to be replaced as a set.
Calibration of float flowmeters using standard tables is an efficient method, and various manufacturers have adopted and applied it. Some manufacturers make the standard table of a certain flow range into several sections of glass tube float flowmeters with smaller tapers, extend the length of the standard table scale, improve the accuracy of the standard table, and make the calibration work high-precision and high-efficiency. The
metal tube float flowmeter is suitable for flow measurement of small-caliber and low-velocity media; it is reliable in operation, requires little maintenance, and has a long service life; it does not require high straight pipe sections; it has a wide flow ratio of 10:1; it has a large dual-line LCD display, with optional on-site instantaneous/cumulative flow display, and can be equipped with a single-axis sensitive indication with backlight; it has a non-contact magnetic coupling transmission; it has an all-metal structure, suitable for high temperature, high pressure and highly corrosive media; it can be used in flammable and explosive hazardous places; it has optional two-wire, battery, and AC power supply modes; it has a multi-parameter calibration function; it has data recovery, data backup and power-off protection functions
Reference address:What factors should be considered when installing a metal tube float flowmeter?
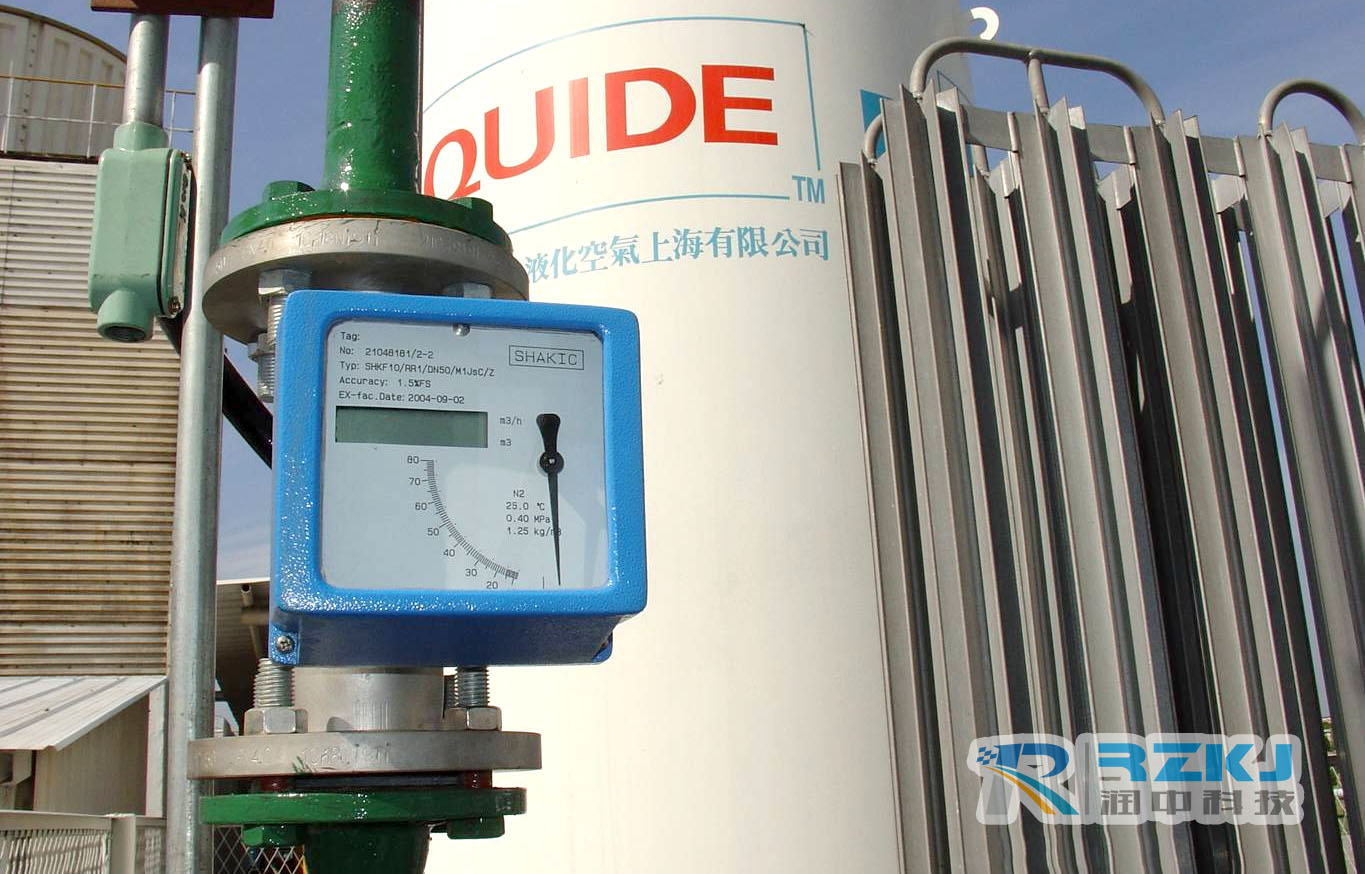
1. Instrument installation direction
Most float flowmeters must be installed vertically on vibration-free pipes, without obvious tilt, and the fluid flows through the instrument from bottom to top. Figure 6 shows an example of pipeline connection, with a bypass pipe system installed to facilitate maintenance without interruption of flow. The angle between the center line of the float flowmeter and the plumb line generally does not exceed 5 degrees, and the θ of high-precision (grade 1.5 or above) instruments is ≤20°. If θ=12°, an additional error of 1% will be generated. The instrument has no strict requirements for the length of the upstream straight pipe section, but some manufacturers require a length of (2-5)D, which is actually not necessary.
2. Installation for dirty fluids
A filter should be installed upstream of the instrument. When a metal tube float flowmeter with magnetic coupling is used for fluids that may contain ferromagnetic impurities, a magnetic filter should be installed in front of the instrument.
Keep the float and cone clean, especially for small-diameter instruments, as the cleanliness of the float significantly affects the measured value. For example, a 6mm diameter glass float flowmeter, in the laboratory, measured what looked like clean water, with a flow rate of 2.5L/h. After running for 24 hours, the flow indication increased by a few percent, and the float surface was stained with foreign matter that could not be observed by the naked eye. The float was removed and wiped with gauze, and the original flow indication was restored. If necessary, a flushing pipe can be set as shown in Figure 7 for regular flushing.
3. Installation of pulsating flow
The pulsation of the flow itself, such as a reciprocating pump or regulating valve upstream of the intended instrument location, or a large load change downstream, should be replaced with a measuring position or remedial improvements should be made in the pipeline system, such as adding a buffer tank; if it is the oscillation of the instrument itself, such as the gas pressure is too low during measurement, the upstream valve of the instrument is not fully opened, the regulating valve is not installed downstream of the instrument, etc., targeted improvements should be made to overcome this, or an instrument with a damping device should be selected instead.
4. Installation to expand the range
If the required flow range is wide and the range exceeds 10, more than two glass tube float flowmeters with different flow ranges are often connected in parallel. One or more instruments are selected in series according to the measurement. When the flow rate is small, the value indicated by the instrument with a lower flow range is read. When the flow rate is large, the value indicated by the instrument with a large flow rate is read. The series method is easier to operate than the parallel method, and there is no need to frequently open and close the valve, but the pressure loss is large. You can also put two floats of different shapes and weights in one instrument. When the flow rate is small, take the reading of the light float, and take the reading of the heavy float after the float reaches the top. The range can be expanded to 50-100.
5. Drain the gas in the instrument for liquid
When using an angular metal float flowmeter whose inlet and outlet are not in a straight line, pay attention to whether there is residual air in the extended sleeve of the external float displacement when using it for liquid. It must be exhausted; if the liquid contains tiny bubbles, it is very easy to accumulate in the sleeve when flowing, and the air should be exhausted regularly. This is more important for small-caliber instruments, otherwise the flow indication will be significantly affected.
6. Necessary conversion of flow value
If the instrument is not specially customized to the manufacturer according to the medium parameters such as density and viscosity, the flow rate of liquid instruments is usually calibrated with water, and the flow rate of gas instruments is calibrated with air, and the fixed value is in the engineering standard state. When the fluid density, gas pressure and temperature of the use conditions are inconsistent with the calibration, necessary conversion should be made. The conversion formula and method are detailed in the instruction manual of each manufacturer.
7. Calibration and calibration of float flowmeter
The calibration and calibration of float flowmeter usually uses the standard table method, volumetric method and weighing method for liquid; the bell jar method is usually used for gas, and the soap film method is used for small flow.
The bulk products of some foreign manufacturers have been calibrated by dry method, that is, the size of the tapered tube and the weight size of the float are controlled to indirectly determine the flow value to reduce costs. Only high-precision instruments are calibrated by real flow. Some domestic manufacturers also strictly control the inner diameter and taper of the starting point of the tapered tube and the size of the float. The real flow calibration only serves to check the quality of the inner surface of the tapered tube. The instruments, tapered tubes and floats produced by such manufacturers are interchangeable and do not need to be replaced as a set.
Calibration of float flowmeters using standard tables is an efficient method, and various manufacturers have adopted and applied it. Some manufacturers make the standard table of a certain flow range into several sections of glass tube float flowmeters with smaller tapers, extend the length of the standard table scale, improve the accuracy of the standard table, and make the calibration work high-precision and high-efficiency. The
metal tube float flowmeter is suitable for flow measurement of small-caliber and low-velocity media; it is reliable in operation, requires little maintenance, and has a long service life; it does not require high straight pipe sections; it has a wide flow ratio of 10:1; it has a large dual-line LCD display, with optional on-site instantaneous/cumulative flow display, and can be equipped with a single-axis sensitive indication with backlight; it has a non-contact magnetic coupling transmission; it has an all-metal structure, suitable for high temperature, high pressure and highly corrosive media; it can be used in flammable and explosive hazardous places; it has optional two-wire, battery, and AC power supply modes; it has a multi-parameter calibration function; it has data recovery, data backup and power-off protection functions
Previous article:Share several cases of electromagnetic flowmeter failure analysis in production
Next article:The four most typical pipe connection methods when installing electromagnetic flowmeters
- Popular Resources
- Popular amplifiers
Recommended Content
Latest Test Measurement Articles
- Seizing the Opportunities in the Chinese Application Market: NI's Challenges and Answers
- Tektronix Launches Breakthrough Power Measurement Tools to Accelerate Innovation as Global Electrification Accelerates
- Not all oscilloscopes are created equal: Why ADCs and low noise floor matter
- Enable TekHSI high-speed interface function to accelerate the remote transmission of waveform data
- How to measure the quality of soft start thyristor
- How to use a multimeter to judge whether a soft starter is good or bad
- What are the advantages and disadvantages of non-contact temperature sensors?
- In what situations are non-contact temperature sensors widely used?
- How non-contact temperature sensors measure internal temperature
MoreSelected Circuit Diagrams
MorePopular Articles
- LED chemical incompatibility test to see which chemicals LEDs can be used with
- Application of ARM9 hardware coprocessor on WinCE embedded motherboard
- What are the key points for selecting rotor flowmeter?
- LM317 high power charger circuit
- A brief analysis of Embest's application and development of embedded medical devices
- Single-phase RC protection circuit
- stm32 PVD programmable voltage monitor
- Introduction and measurement of edge trigger and level trigger of 51 single chip microcomputer
- Improved design of Linux system software shell protection technology
- What to do if the ABB robot protection device stops
MoreDaily News
- Brief Analysis of Automotive Ethernet Test Content and Test Methods
- How haptic technology can enhance driving safety
- Let’s talk about the “Three Musketeers” of radar in autonomous driving
- Why software-defined vehicles transform cars from tools into living spaces
- How Lucid is overtaking Tesla with smaller motors
- Wi-Fi 8 specification is on the way: 2.4/5/6GHz triple-band operation
- Wi-Fi 8 specification is on the way: 2.4/5/6GHz triple-band operation
- Vietnam's chip packaging and testing business is growing, and supply-side fragmentation is splitting the market
- Vietnam's chip packaging and testing business is growing, and supply-side fragmentation is splitting the market
- Three steps to govern hybrid multicloud environments
Guess you like
- ST MEMS waterproof pressure sensor LPS27HHW review summary
- The problem of not receiving data when building lorawan gateway with Raspberry Pi
- Two questions about registers
- UWB, Bluetooth, RFID, WIFI and indoor positioning technology
- 【micropython】NUCLEO_L073RZ and NUCLEO_L452RE have been added to the firmware library
- [NUCLEO-L552ZE Review] + Low Power Measurement Tool
- Lithium battery charging and discharging integrated chip
- Bluetooth module connection problem
- Ethernet LED is not on
- AM57x Processors for Smart Grid Applications