Online testing used to be the leading technology for PCB testing after assembly and occupied an absolute advantage in the market. However, with the development of electronic assembly technology, the density of PCBs is getting higher and higher, the distance between test points is getting smaller and smaller, and the number of test points is increasing. All of this has brought challenges to traditional testing technology. In addition, with the continuous emergence of various new testing technologies, where is the online testing technology going? We might as well take a closer look at the characteristics of online testing technology and the efforts made by equipment manufacturers to meet this challenge. According to different testing methods, online testers can be divided into two types: bed of nails test and flying probe test.
2 Bed of Nails Online Testing Technology
2.1 Structure and principle of bed of nails test equipment
The traditional needle bed online tester uses a special needle bed to contact the components on the soldered circuit board (see Figure 1), and uses hundreds of millivolts and currents less than 10mA for force isolation testing, so as to accurately measure the missing, wrong installation, parameter value deviation, solder joint welding, circuit board open and short circuit and other faults of the installed resistors, inductors, capacitors, diodes, transistors, thyristors, field effect tubes, integrated blocks and other general and special components, and accurately tell the user which component or open and short circuit is located at which point. The advantages of the needle bed online tester are fast testing speed, suitable for testing single-variety civilian household appliance circuit boards with extremely large-scale production, and the host price is relatively cheap. However, with the increase in the assembly density of circuit boards, especially the fine pitch SMT assembly and the shorter production cycle of new product development, the increasing number of circuit board varieties, the needle bed online tester has some difficult to overcome problems, such as the production of the needle bed fixture for testing, the long test cycle and the expensive price; some high-density SMT circuit boards cannot be tested due to test accuracy issues.
Some features of online testers:
(1) Instantly identify and confirm defects;
(2) It can detect most production problems;
(3) Includes a circuit analysis module, test generator and component library;
(4) Provide system software to support writing and evaluating tests;
(5) Model testing can be performed on different components.
To conduct online testing, the online tester must do two things: "touch" and "isolate". It must be able to touch all the components to be tested. Obviously, to test them one by one, the tester must touch every foot of each device. In addition, the online tester must be able to isolate the influence of surrounding devices on the device under test, because there are line connections between devices, and special isolation technology is required to prevent the device under test from being affected by other devices. To touch each test point on the PCB, a special test tool - a needle bed is required. There are many small elastic probes on the needle bed. Using them, you can touch the test points. Using these small probes also isolates the influence of surrounding devices on the device under test. Each PCB needs a test needle bed that matches it. The role of the needle bed is to connect the measuring instrument module inside the online tester and the node under test. Because the test can be analog, digital and mixed, each test needle can be connected to an analog or digital measuring instrument module under the control of the test program. Each tester has two groups of relays inside. One group is SCANNER, which connects any test point and the measuring instrument bus; the other group of relays is called MULTIPLEXER or MUX, which connects the measuring instrument bus and the measuring instrument module, as shown in Figure 2.
2.2 Testing of analog devices
Taking the measurement of resistance as an example, as shown in Figure 3, the measurement in an online situation is bound to be very different from the measurement of an independent resistor. The current flowing through Rx is shunted by R3 and R4, and the rest flows into the ammeter. Depending on the resistance characteristics of the shunt circuit, the error of the Rx resistance value calculated from this may be very large.
[page]
2.3 Measurement of digital devices
First, we need to review the characteristics of digital devices. Digital devices have only two levels: high level and low level, so the test program must be able to define the logic potential. Digital devices have many more pins than analog devices, so the tester cannot switch analog sources and measuring instruments between pins. Therefore, the tester must have a set of digital drivers that can drive the input of the digital chip to the ideal potential, and also a set of digital sensors that can detect its output logic potential.
Drivers and sensors (Driver/Sensor) exist in pairs. The output of the driver is always connected to the input of the sensor. Under program control, the same measurement node may be driven to a certain potential at one time, and at another time, its output may be measured by the sensor.
(1) Driver/Sensor Programming
To illustrate how a program controls an actuator/sensor, let's look at a simple two-input NAND gate example, as shown in Figure 7.
Only when all inputs of the NAND gate are high, the output is low, and for other combinations of states, the output is high. To measure this two-input NAND gate, the test procedure should work as follows:
1) Power on and ground the board under test
2) Define high and low levels
3)Specify the test pin
4) Define the drive and sense measurement timing
For the single NAND gate above, the test program will check the operation of all 4 inputs.
Each line of program statement represents a test vector. IC, IH and IL connect the driver to the specified input terminals A and B and give the assigned values; OS, OH and OL connect the sensing measurement terminal to the output terminal C and tell the expected value. All driver and sensing terminal values remain unchanged until the program command changes.
(2) Isolation and measurement of digital chips
Because the digital device under test must be powered on before it can be measured, and there are connections between the devices on the board, power will also be added to other devices. In this way, when the tester wants to add a driving signal to a certain input terminal of the chip under test (such as a high level), this input terminal may be maintained at the opposite potential (low level) by the output of another chip.
The digital driver solves this problem by instantly forcing the output of the chip under test to a specified level, regardless of the influence of other chips. This technology is called back drive technology.
Consider a typical TTL chip output state, as shown in Figures 8 and 9. In Figure 8, when Q1 is turned on and Q2 is turned off, the output is low. To make the output high instantly, the tester imposes a momentary current pulse, which flows back from the emitter of Q1 through the collector, so that the output terminal generates a high potential. Similar to Figure 9, when Q2 is turned on and Q1 is turned off, the output is high. To make the output low, the tester adds a low level at the output to absorb the current flowing through Q2. Because the digital test speed is very fast, the current pulse time is much less than 10ms (usually 5-10μs), and such a short pulse will not cause damage to the chip.
2.4 Limitations of Bed of Nails Test
[page]
The limitation of the bed of nails test is mainly reflected in the mechanical accuracy. We might as well calculate the total error caused by each link from PCB production, fixture manufacturing to testing, and it is not difficult to draw the conclusion:
(1) The drilling accuracy of the fixture. It is difficult to control the accuracy below 25μm when drilling a thick fixture plate with a needle bed in good condition. Moreover, for some high-precision PCB test fixtures, the number of layers can be as high as 8.
(2) During PCB testing, the alignment accuracy between the PCB and the fixture and between the fixture and the equipment should be accurate. In order to facilitate the placement and removal of the fixture on the needle bed, if pin positioning is used, the diameter of the pin and the pin hole should differ by 10-20μm.
(3) Deviation between PCB hole position and outer layer pattern. In the manufacture of multi-layer PCB, in order to avoid the inner layer from breaking and improve the qualified rate, it is often adopted to drill positioning holes according to the relative positions of each layer pattern after lamination. The higher the number of layers, the greater the difference between the position of the hole and the outer layer pattern. The position of the upper and lower surfaces of the PZB may also differ by ±0.15mm.
(4) Movement of the test probe. In a multi-layer fixture, if there is a slight deviation, the probe will rub or get stuck, which will cause a false open circuit alarm. Too high a density will cause the strength of each layer of the fixture to decrease, causing bending, etc., which will cause probe position deviation.
(5) PCB size stability and fixture and PCB size consistency error. For a type of PCB, due to differences in manufacturing conditions (batch manufacturing), ambient temperature and humidity will cause changes in the size of the film and substrate, resulting in small differences in the size of similar PCB graphics. If the board is large and the density is high, it will directly affect the test accuracy. Similarly, the size of the fixture may also have microscopic differences due to changes in the environment, which will have a great impact on the test accuracy.
(6) PCB warping causes the position of the test probe to change. In severe cases, the probe cannot contact the surface being tested, resulting in false alarms.
In summary, the limitation of test accuracy is the biggest problem faced by the bed-of-nails test. According to statistics, under the premise of ensuring the correctness of repeated tests and excluding the deviation of the positions of the upper and lower surfaces of the PCB, the minimum testable pitch for a 100mm×100mm PCB is 0.25mm, the minimum testable pitch for a 200mm×200mm PCB is 0.31mm, the minimum testable pitch for a 300mm×300mm PCB is 0.44mm; the minimum testable pitch for a 400mm×400mm PCB is 0.49mm.
It should be pointed out that as the density changes, the test products and test costs change accordingly. The output is proportional to the square function of the center distance, and the test cost is inversely proportional to the center distance function.
In addition, the number of test points is another limiting factor, especially today when BGA is widely used, which requires dense test points. If there are many BGAs distributed on the PCB and their spacing is limited, it may cause the problem of insufficient test pin allocation. For special tests, the total test armature is also very limited. For high-density packaging boards and local test points, the area that can be tested is also limited. For example, the conventional testable area is 500mm×500mm, and the testable area for high-density PCBs is only 200mm×200mm. This is the result of the limitation on the total number of test points.
For special test fixtures, the spring test is insufficient for fine pitch testing when conducting high-density PCB testing. According to current PCB density requirements, the test needle should be very thin, preferably less than 0.3mm, which is quite difficult to manufacture. The drilling positioning of the fixture is also a problem that special fixtures must face.
2.5 Improvements in Bed of Nails Testing
Faced with more and more problems in high-density PCB testing, the bed-of-nails testing technology continues to develop and improve, mainly reflected in the increase in the density of the bed-of-nails, the innovation and optimization of fixture design and manufacturing, the introduction of auxiliary testing, the optimization of data adoption, and the improvement of testing technology (switch cards).
(1) Changes in needle bed density
The center distance of a general needle bed test needle is 2540μm, which is called a single-density needle bed. With the increase in the number of test points and the improvement in test density, many manufacturers have launched double-density needle beds with a center distance of 1778μm. Figure 10 is a comparison between a single-density test needle bed and a double-density test needle bed. Now, some manufacturers are also developing four-density test equipment. Although the problem of test points can be solved to a certain extent, the problem of accuracy still exists.
(2) Innovation of fixture design and manufacturing technology
As the main factor affecting the test accuracy, the design and manufacture of the fixture is extremely critical. In many nail bed test equipment that successfully conducts high-density testing, the fixture design is often unique. For example, ECT's fixture design software carefully considers the inclination and friction of the test probe, so that the produced fixture and the center of the probe are directly opposite the test point, ensuring the accuracy is consistent with the design. In areas with fewer probes, the fixture is balanced in the three directions of x, y and z, and no bending deformation occurs to cause deviation. The automatic alignment system can also detect and compensate for the deviation between the positioning hole and the outer layer pattern. In the selection of fixture materials, modular materials that are least affected by temperature and humidity are used to ensure accurate and stable dimensions.
(3) Introduction of conductive rubber module
In some bed-of-nails test equipment, for some extremely delicate parts, such as TAB, flip chip, μBGA or QFP, the center distance of the test point is about 0.1mm, which makes it difficult to locate with a needle test. The use of a conductive rubber module for local testing can overcome the shortcomings of the bed-of-nails test. This module is connected to the fixture through a pneumatic tube and is automatically positioned by the corresponding fixture design software. If multiple areas need to use this module, the module can be used multiple times, but the conductive rubber module short-circuits all the test points in the covered area, and the internal short circuit cannot be measured. It is only used for the connectivity between the tested area and the outside world. If you want to test the internal short circuit, you must select these nets and use other methods (such as moving probes) to test.
(4) Improvement of switch card technology
To meet the requirements of test accuracy, the switch card is required to withstand high voltage, have no leakage in the "off" state, and compensate for resistance in the "on" state to ensure test accuracy. The switch card itself uses SMT packaging, occupies a small volume, and has ESD (electrostatic discharge protection).
Although the bed of nails testing technology faces severe technical challenges due to its own principles and method limitations, it still has advantages over other methods in some aspects, such as efficiency. In addition, with the improvement of fixture technology and the coordinated use of new technologies, it will also have strong vitality in the testing field.
3 Flying Probe Test Technology
Today, the design and production of electronic products are under great pressure of time to market, and the time cycle of product updates is getting shorter and shorter. Therefore, it is crucial to develop new products and achieve mass production in the shortest time for electronic product production. Flying probe test technology is the latest solution to some major problems of electrical testing. It uses probes to replace the needle bed, and uses multiple electrical probes driven by motors and capable of fast movement to contact the pins of the device and perform electrical measurements. This instrument was originally designed for bare boards and also requires complex software and programs to support it. Now it can effectively perform simulated online testing. The emergence of flying probe testing has changed the test methods of small batch and quick-turn assembly products. Tests that previously took several weeks to develop now only take a few hours, greatly shortening the product design cycle and time to market.
3.1 Structural characteristics of flying probe test system
The flying probe tester is an improvement on the traditional needle bed online tester. It uses probes to replace the needle bed. There are 8 test probes with 4 heads that can move at high speed on the xy mechanism, and the minimum test gap is 0.2mm, as shown in Figure 11. When working, the unit under test (UUT) is transported to the tester through a belt or other UUT conveying system, and then fixed. The probe of the tester contacts the test pad and the via to test the single component of the unit under test (UUT). The test probe is connected to the driver (signal generator, power supply, etc.) and the sensor (digital multimeter, frequency counter, etc.) through a multiplex transmission system to test the components on the UUT. When a component is being tested, other components on the UUT are electrically shielded by the probe to prevent reading interference.
[page]
The flying probe tester can check short circuits, open circuits and component values. A camera is also used on the flying probe test to help find missing components. The camera is used to check the shape of components with clear directions, such as polarized capacitors. With probe positioning accuracy and repeatability in the range of 5-15μm, the flying probe tester can accurately detect the UUT. Flying probe testing solves a large number of existing problems seen in PCB assembly: such as test development cycles that may be as long as 4-6 cycles: fixture development costs of approximately $10,000-50,000: the inability to economically test small batch production; and the inability to quickly test prototype assembly.
3.2 Test development and debugging
The programming of flying probe tester is easier and faster than that of traditional bed-of-nails online test system. For example, Teradyne's Javelin 1004 adopts Windows NT platform and intuitive user interface, as well as dedicated programming and test system, which shortens programming time. Users can convert PCB CAD data into PCB test data through FAB master software within 1-2 days, and control the probe by graphic flow chart. The program can be automatically produced and debugged with the help of component test form, which speeds up programming and debugging. The installation of test program is also very simple, which shows that flying probe system has excellent flexibility and rapid adaptability. On the contrary, the programming and fixture development of traditional bed-of-nails online test system may take 160 hours and debugging 140 hours.
3.3 Disadvantages of Flying Probe Test
Flying probe testing can solve many problems in a production environment due to its ease of programming, ability to test prototype assemblies in hours, and testing low-volume products without the typical fixture development expense. However, not all production test problems can be solved using flying probe testing.
Like anything, flying probe testing has its disadvantages, because the test probe makes physical contact with the solder on the via holes and test pads, which may leave small pits in the solder. For some OEM customers, these small pits may be considered cosmetic defects and cause rejection, because sometimes the probe will touch the component pin where there is no test pad, so loose or poorly soldered component pins may be missed.
Another shortcoming is that the flying probe test takes too long. The number of traditional needle bed test probes is 500-3000. The needle bed can complete all the requirements of online testing with one contact with the PCB, and the test time is only tens of seconds. However, there are only four flying probe probes. The flying probe needs many movements to complete the test completed by one contact of the needle bed, and the time is obviously much longer. In addition, the needle bed tester can use the top surface fixture to test the top and bottom components of the double-sided PCB at the same time, while the flying probe tester requires the operator to test one side, then flip it over and test the other side. It can be seen that the flying probe test cannot adapt well to the requirements of mass production.
3.4 Advantages of Flying Probe Test
Despite these shortcomings, the flying probe tester is still a valuable tool. Its advantages include:
(1) Shorter test development cycle. Production can start within a few hours after the system receives the CAD file. Therefore, the prototype circuit board can be tested within a few hours after assembly. Unlike the bed of nails test, the high cost of test development and fixtures may delay the production cycle for several days or even months.
(2) Lower testing cost, no need to make special test fixtures.
(3) Due to the simplicity and speed of setting, programming and testing, in fact, general technical assemblers can perform operational tests.
(4) High test accuracy. The positioning accuracy (10μm) and repeatability (±10μm) of the flying probe online test and the extremely small contacts and spacing enable the test system to detect PCB nodes that the bed of nails fixture cannot reach.
4 Complementarity between flying needle and needle bed
It should be noted that, compared with the bed of needles, flying probe is a technological innovation and is still developing. With the development of wireless communications and wireless networks, more and more PCBs will increase wireless access capabilities. The current bed of needles tester is only suitable for low-frequency bands. The probes in the radio frequency (RF) band will become small antennas, generating a large amount of parasitic interference, affecting the reliability of the test results. The bed of needles online tester can only detect the characteristics of the RF circuit at low frequencies. The test of the RF circuit is performed by the subsequent functional tester, which will inevitably reduce the defect coverage of the PCB. The number of probes in the flying probe online tester is very small, and it is easier to take measures to reduce RF interference, realize low-frequency and RF online testing of PCBs, and improve coverage.
Flying probe in-circuit tester and bed of nails in-circuit tester have complementary capabilities. Therefore, some PCB in-circuit test suppliers consider merging flying probe and bed of nails technologies, integrating flying probe and bed of nails structures in the same in-circuit tester to complement each other's advantages and achieve the goals of high-speed testing, easy programming and cost reduction.
The flying probe test system is still under development and cannot replace the bed-of-nails online tester at present. However, the performance of the flying probe online tester has reached the requirements of PCB mass production, such as automatic feeding, increasing the number of fixed probes at the bottom of the PCB, and shortening the programming time to 1 person/day. The flying probe online tester is gaining attention from EMS companies and is used not only in the development stage of electronic products, but also in online testing of multi-variety, small and medium-sized batches of PCBs.
5 Conclusion
Although online testing technology faces severe technical challenges due to its own limitations in principles and methods, it will continue to have tenacious vitality in the testing field in some aspects, such as the efficiency of bed-of-nails testing, the flexibility of flying probe testing, and the ability to perform electrical performance testing, coupled with technological improvements and the coordinated use of new technologies.
Previous article:Design of high-precision angle detection platform for MMA7361L
Next article:Design and implementation of a WLAN automated testing platform
Recommended ReadingLatest update time:2024-11-16 15:39
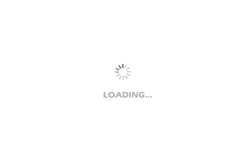
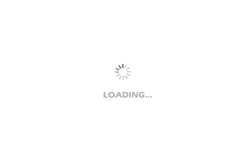
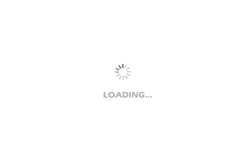
- Popular Resources
- Popular amplifiers
-
Radio Frequency Identification (RFID) System Technology and Application (Written by Ci Xinxin, Wang Subin, and Wang Shuo)
-
Modern Electronic Technology Training Course (Edited by Yao Youfeng)
-
More Hot Air (Tony Kordyban)
-
Printed Circuit Board Design Practical Tutorial Protel DXP 2004 SP4 (Edited by Liu Huiheng)
- Keysight Technologies Helps Samsung Electronics Successfully Validate FiRa® 2.0 Safe Distance Measurement Test Case
- From probes to power supplies, Tektronix is leading the way in comprehensive innovation in power electronics testing
- Seizing the Opportunities in the Chinese Application Market: NI's Challenges and Answers
- Tektronix Launches Breakthrough Power Measurement Tools to Accelerate Innovation as Global Electrification Accelerates
- Not all oscilloscopes are created equal: Why ADCs and low noise floor matter
- Enable TekHSI high-speed interface function to accelerate the remote transmission of waveform data
- How to measure the quality of soft start thyristor
- How to use a multimeter to judge whether a soft starter is good or bad
- What are the advantages and disadvantages of non-contact temperature sensors?
- Innolux's intelligent steer-by-wire solution makes cars smarter and safer
- 8051 MCU - Parity Check
- How to efficiently balance the sensitivity of tactile sensing interfaces
- What should I do if the servo motor shakes? What causes the servo motor to shake quickly?
- 【Brushless Motor】Analysis of three-phase BLDC motor and sharing of two popular development boards
- Midea Industrial Technology's subsidiaries Clou Electronics and Hekang New Energy jointly appeared at the Munich Battery Energy Storage Exhibition and Solar Energy Exhibition
- Guoxin Sichen | Application of ferroelectric memory PB85RS2MC in power battery management, with a capacity of 2M
- Analysis of common faults of frequency converter
- In a head-on competition with Qualcomm, what kind of cockpit products has Intel come up with?
- Dalian Rongke's all-vanadium liquid flow battery energy storage equipment industrialization project has entered the sprint stage before production
- Allegro MicroSystems Introduces Advanced Magnetic and Inductive Position Sensing Solutions at Electronica 2024
- Car key in the left hand, liveness detection radar in the right hand, UWB is imperative for cars!
- After a decade of rapid development, domestic CIS has entered the market
- Aegis Dagger Battery + Thor EM-i Super Hybrid, Geely New Energy has thrown out two "king bombs"
- A brief discussion on functional safety - fault, error, and failure
- In the smart car 2.0 cycle, these core industry chains are facing major opportunities!
- The United States and Japan are developing new batteries. CATL faces challenges? How should China's new energy battery industry respond?
- Murata launches high-precision 6-axis inertial sensor for automobiles
- Ford patents pre-charge alarm to help save costs and respond to emergencies
- New real-time microcontroller system from Texas Instruments enables smarter processing in automotive and industrial applications
- This flyback switching power supply based on TinySwitch-III
- I stayed up late to sort it out. Here is the gimbal information on the national competition list.
- Op amp amplifier - input offset voltage
- Research and Implementation of Serial Data Communication between C6000 and C2000 Series DSP
- Components Science Popularization: Semiconductor Laser
- Reward for designing sensor amplifier circuit (4000 RMB)
- Telephone Handle Side Tone Elimination Circuit
- Circuit simulation help Cadence Pspice
- Please recommend a domestic DAC 4-20mA current loop chip
- Detailed explanation of the working principles of thirty common resistor circuits