introduction
There is a cable joint approximately every 300 meters of high-voltage power supply cables in cities. In many cases, in order to reduce the difficulty of technology and construction, the cable joints are installed in the power supply cable junction box. The cable junction box is an indoor or outdoor device, usually installed on the street, roadside or community, used to branch, connect or convert cable lines. In some cases, the operating cable line can be disconnected to facilitate the maintenance of the cable line and electrical equipment. Due to a series of reasons such as the poor construction quality of the cable joints in the junction box and the construction workers' unfamiliarity with the construction process of prefabricated cable accessories, the cable joints are prone to overheating under long-term, high-current (overload) operation conditions, leading to accidents, seriously affecting the safe and reliable operation of the power system and causing huge economic losses.
According to the actual needs of power supply enterprises, this solution uses wireless technology to design a new type of cable joint temperature monitoring system terminal. It is located at each cable joint to collect temperature data and cable current data, and collects the measurement data in the branch box to the data concentrator at the bottom of the branch box through short-range micro-power wireless technology, and then uploads it to the PC in the monitoring center, realizing low-cost online and reliable monitoring of the operating temperature and current of the cable joints in the urban power supply cable branch box.
Hardware circuit design
Measuring principle
Both actual operation experience and theoretical analysis show that various faults occurring at cable joints are not a sudden process, but a process from quantitative change to qualitative change, which is usually manifested as a continuous increase in the temperature at the cable joint. In addition, in the power system, there is a law that the load current and temperature of power equipment are positively correlated: when the load current increases, the temperature will rise, and when the load current decreases, the temperature will drop.
The surface temperature of the cable joints in the distribution box is an important parameter that reflects its operating status. Continuous monitoring and statistical analysis of the cable joint temperature can enable operators to fully understand their working conditions, timely understand the aging of the cable joints, and propose maintenance plans based on production conditions when necessary to avoid or reduce the occurrence of faults, improve the safety and reliability of the power supply system, and thus promote power supply companies to increase revenue and save costs and improve economic benefits.
According to the electrical safety regulations of the junction box, the space distance between phase-to-phase connectors shall not be less than 1cm, the space distance between the connector and the side wall and top of the junction box shall not be less than 15cm, and the vertical distance between each connector and the split point of the three-core cable shall not be less than 70cm. The outer surface of the cable joint conductor of the junction box is an insulating sheath layer, and there is actually a voltage ranging from several hundred volts to thousands of volts on the surface of the insulating sheath layer. The temperature of the cable joint conductor mainly depends on the current I passing through the conductor, the contact resistance R and the ambient temperature TE. When the current and ambient temperature do not change much, it is mainly affected by the contact resistance. The measuring point temperature is the temperature of the joint conductor T and the ambient temperature TE. Although it cannot directly measure the actual temperature of the joint conductor part, it is approximately linearly related to the joint conductor temperature under the field environment. Therefore, for the monitoring of the temperature of the cable joint in the junction box, the surface temperature of the cable joint and the current passing through the cable joint, as well as the ambient temperature and humidity of the junction box are mainly measured.
Power supply system design
The design concept of the monitoring terminal power supply circuit is to use a special coil to induce an AC voltage of a certain power from the cable, and then provide it to the monitoring terminal after rectification, filtering and voltage stabilization. The AC voltage on the medium and high voltage cable with a current range of about 10A~300A is then converted into DC by a rectification and filtering circuit, and the DC voltage of about 5V is converted into a +3.3V DC constant voltage to supply the monitoring terminal by a voltage stabilization circuit. In addition, in order to prevent the back-end circuit from burning out due to excessive induced voltage of the special coil in the case of high cable current, an overvoltage protection circuit is added to the circuit to protect the device. As shown in Figure 1.
The difficulty of this circuit design lies in that when the cable current is small, the power supply should be guaranteed as much as possible; when the cable is under heavy load or even short circuit fault current, the power board should be adequately protected to prevent damage to the device.
The power supply includes energy supply coil, rectifier filter voltage regulator circuit, control coil, control circuit and lightning protection circuit.
The power supply coil is a special small CT (current transformer) that uses electromagnetic induction to obtain energy from the cable. The device uses silicon steel sheets with low saturation magnetic induction intensity and high magnetic permeability to make the iron core. The power supply coil/control coil and the rectifier filter voltage regulator circuit, control circuit and lightning protection circuit are fixed on one side of the iron core with the monitoring terminal to reduce the volume and weight. According to the principle of electromagnetic induction, the number of turns of the coil is determined to ensure that a stable 3.3V regulated output can be provided when the cable current is above 10A. The output of the power supply coil is connected to the lightning protection circuit and then to the rectifier filter voltage regulator circuit.
Since the current running on the high-voltage cable has a large variation range, and the power supply must be kept stable when the transient current reaches dozens of times the rated current, it is necessary to ensure that the power supply can still work normally when the current reaches 300A. When the cable current is too large, the iron core of the induction coil is in a magnetic saturation state. After the iron core is saturated, the magnetization curve is nonlinear, and the induced potential becomes similar to a pulse wave, causing the input voltage of the voltage-stabilized power supply module to be too high and burn out, which is not conducive to the realization of the power supply. This design adds a control winding and a control circuit. When the cable current is too large and too much energy is obtained, the induction voltage of the power supply coil is controlled to be within the appropriate working range. [page]
Circuit Design
The hardware structure of the system is shown in Figure 2. The core control chip of the system adopts the MXT8051 of Time Minxin. The XT8051 is an MCU with a high-speed single instruction cycle 8051 as the core. The circuit has a wealth of peripherals, including PWM, UART, WDT, Timer, etc., large-capacity memory, embedded 32Kx8 online programmable flash, 10-bit AD, 8-bit DA, several OPs, 36x4 LCD driver, POR and analog circuits such as programmable gain amplifier (PGA). The circuit integrates an on-chip debugging system, which can quickly diagnose complex SoCs through a standard JTAG interface. The debugging system has the functions of full-speed and single-step operation without occupying any hardware resources, supporting hardware breakpoints, software breakpoints, and observing internal special function registers, program pointers and internal RAM. The host computer performs online programming and online debugging through the standard JTAG interface and user-defined instructions. At the same time, debugging and programming software packages are provided, and the CPU can easily meet the system control requirements.
The nRF24L01 chip is a 2.4GHz single-chip wireless transceiver chip launched by Nordic, Norway. The chip has the advantages of high receiving sensitivity, few peripheral circuits, low transmission power, high transmission rate, and low power consumption. It works in the 2.4GHz free frequency band and supports multi-point communication. Its maximum transmission rate is 1Mb/s. It is designed using the SoC method and only a small number of peripheral components are needed to form a radio frequency transceiver circuit. The nRF2401A does not have a complex communication protocol. It is completely transparent to users and the same products can communicate freely.
Algorithm and software implementation
Implementation of temperature monitoring and current monitoring
The system needs to monitor current and temperature. The temperature monitoring uses the DS18B20 chip, which is a single bus temperature sensor. This system has a total of 6 temperature signals and requires 6 temperature sensors, which are hung on a bus. The operation process is: the microcontroller pre-stores the serial numbers of these 6 temperature sensors, first initializes all the temperature sensors on the bus, searches for the first temperature sensor, issues a temperature conversion command, and after 500ms, matches this temperature sensor again. After the match is correct, read the contents of the temperature register, and finally convert the contents of the temperature register into a decimal value and store it in the buffer of the microcontroller.
Current monitoring is implemented by CT. First, a 100:1 CT is used to obtain an alternating current from the cable. A 0.01Ω sampling resistor is added to the secondary circuit side to convert the current value into a voltage value. This voltage value is proportionally converted into a range that can be collected by the microcontroller AD through the operational amplifier LM358, and the signal is sent to the microcontroller. After the microcontroller collects the signal, it is multiplied by the proportional coefficient and converted into an effective value for display.
Realization of system functions
The system function is implemented as shown in Figure 3. The MCU first initializes the port. Since the MCU used has a bidirectional output, it is necessary to determine whether this port is input or output, whether the pull-up resistor is enabled, etc. before use. Especially for the SDA interface, it is both output and input during data transmission, so the input and output of the MCU must be set correctly. Segment LCD is a dynamically updated segment display device with low power consumption. Before use, the number of segments, the number of common ports, the frame rate, etc. of the segment LCD must be set. After the setting is completed, each segment of the LCD can be operated in the MCU register. Both PWM and AD must be divided by the main clock. Select the appropriate clock according to the needs. Make the external memory, temperature sensor, and wireless module work in the ready state, and set the operation address, transceiver rate, error checking, etc. After initialization, the system reads the memory configuration to determine which state the system is working in, and then performs temperature conversion and current acquisition according to the set state. After data acquisition is completed, the measured data is placed in the data buffer of the MCU, and then the data is sent out using the wireless module. Finally, switch to the next channel to measure data and repeat the above process.
Conclusion
The actual operation results show that the new cable joint online monitoring terminal proposed in this scheme is powered by an induction power supply, does not require an external power supply, and is maintenance-free. A short-range, micro-power wireless communication method is used between the monitoring terminal and the data concentrator, which effectively transmits data while achieving high-voltage isolation. The monitoring terminal hardware and software both adopt an ultra-low power design to achieve accurate temperature measurement. It can be foreseen that this product will have a good market prospect.
Previous article:Using Wireless Data Acquisition for Bridge Collapse Testing
Next article:Moment method analysis of a broadband circular array antenna
Recommended ReadingLatest update time:2024-11-16 17:55
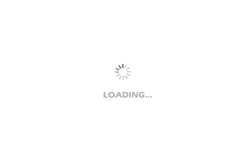
![[nrf52820] DONGLE adapter ESB (2.4G) master-slave solution multi-channel communication dynamic frequency modulation](https://6.eewimg.cn/news/statics/images/loading.gif)
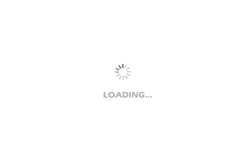
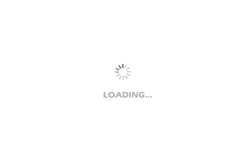
- Popular Resources
- Popular amplifiers
-
Build the Internet of Things with Arduino
-
Electronic competition thesis documents based on MSP430 microcontroller design + source code and some hardware PCB files
-
Based on NRF905 wireless transmission module RF design including schematic diagram and source program
-
Maker Robot Practice: Based on Arduino and Raspberry Pi
- Keysight Technologies Helps Samsung Electronics Successfully Validate FiRa® 2.0 Safe Distance Measurement Test Case
- From probes to power supplies, Tektronix is leading the way in comprehensive innovation in power electronics testing
- Seizing the Opportunities in the Chinese Application Market: NI's Challenges and Answers
- Tektronix Launches Breakthrough Power Measurement Tools to Accelerate Innovation as Global Electrification Accelerates
- Not all oscilloscopes are created equal: Why ADCs and low noise floor matter
- Enable TekHSI high-speed interface function to accelerate the remote transmission of waveform data
- How to measure the quality of soft start thyristor
- How to use a multimeter to judge whether a soft starter is good or bad
- What are the advantages and disadvantages of non-contact temperature sensors?
- Innolux's intelligent steer-by-wire solution makes cars smarter and safer
- 8051 MCU - Parity Check
- How to efficiently balance the sensitivity of tactile sensing interfaces
- What should I do if the servo motor shakes? What causes the servo motor to shake quickly?
- 【Brushless Motor】Analysis of three-phase BLDC motor and sharing of two popular development boards
- Midea Industrial Technology's subsidiaries Clou Electronics and Hekang New Energy jointly appeared at the Munich Battery Energy Storage Exhibition and Solar Energy Exhibition
- Guoxin Sichen | Application of ferroelectric memory PB85RS2MC in power battery management, with a capacity of 2M
- Analysis of common faults of frequency converter
- In a head-on competition with Qualcomm, what kind of cockpit products has Intel come up with?
- Dalian Rongke's all-vanadium liquid flow battery energy storage equipment industrialization project has entered the sprint stage before production
- Allegro MicroSystems Introduces Advanced Magnetic and Inductive Position Sensing Solutions at Electronica 2024
- Car key in the left hand, liveness detection radar in the right hand, UWB is imperative for cars!
- After a decade of rapid development, domestic CIS has entered the market
- Aegis Dagger Battery + Thor EM-i Super Hybrid, Geely New Energy has thrown out two "king bombs"
- A brief discussion on functional safety - fault, error, and failure
- In the smart car 2.0 cycle, these core industry chains are facing major opportunities!
- The United States and Japan are developing new batteries. CATL faces challenges? How should China's new energy battery industry respond?
- Murata launches high-precision 6-axis inertial sensor for automobiles
- Ford patents pre-charge alarm to help save costs and respond to emergencies
- New real-time microcontroller system from Texas Instruments enables smarter processing in automotive and industrial applications
- Code statistics of the most popular programming languages on GitHub
- This is a good comprehensive DC information that I have personally read
- [Allwinner V853 heterogeneous AI intelligent vision development board evaluation] Cross-compilation environment settings and applications
- LM2776 output voltage is abnormal
- What manufacturability issues should be considered when designing PCBs?
- Next-generation IoT development opportunities and use cases
- [Mill Edge AI Computing Box FZ5 Review] Initial Unboxing of the Development Board
- Defining large arrays in C2000
- A Quick Way to Estimate PCB Trace Resistance: Block Statistics
- SimpleLink MCU Code Porting Guide