Virtual instruments based on various bus systems and development platforms are gradually playing an increasingly important role in the field of measurement and control and instrument science. At present, the altimeter used in aircraft, missile or radar is very widely used in China, and the height measurement accuracy of the altimeter is a crucial condition to ensure the normal operation of aircraft, missile or radar. In order to ensure the normal operation of the altimeter, it is necessary to conduct a simulation test before the altimeter is used. In view of the shortcomings of the low accuracy of traditional altimeter measurement equipment, it is necessary to design an altimeter test system with high accuracy. The use of digital acquisition technology and computer technology for signal processing has high measurement accuracy. At the same time, the LabWindows/CVI software platform combines C language and professional measurement and control tools for data acquisition, analysis and display, simplifies the design of the user interface, and enables the generated application to be transplanted on multiple platforms. The altimeter is tested using LabWindows/CVI virtual instrument technology, which has high usability and maintainability.
1 Test requirements analysis
The test object of the altimeter test system is a certain type of radio altimeter with frequency modulated continuous wave, constant beat automatic tracking type C band modulated by sawtooth wave signal. The altimeter consists of a transmitting assembly, a receiving assembly, a servo output assembly and a transmitting and receiving frequency discrimination assembly, and its working principle is shown in Figure 1.
At time t1, the frequency of the linear frequency modulation wave transmitted by the transmission combination of the altimeter to the sea surface through the antenna is f1, and the echo signal is received at time t2. Using the sawtooth wave linear frequency modulation system, the transmission frequency has changed to f2 at time t2. At this time, a small part of the transmission energy is taken out as the local oscillator signal and mixed with the echo signal in the mixer. After detection, the beat signal fb is obtained. The calculation formula for obtaining the height signal based on the beat signal is shown in the following formula.
In the formula: Tm is the sawtooth wave modulation period; △f is the frequency modulation bandwidth; H is the required height to be measured; c is the propagation speed of the electromagnetic wave.
When the test is in a dynamic equilibrium state, △f and c are constants, and fb is also a constant under transient equilibrium. At this time, the measured height is proportional to the modulation period. The altimeter working height can be measured by measuring the modulation period, as follows:
The function of the altimeter test system is to detect whether the altimeter is working properly. It is mainly through testing the height signal Pn and the height control signal Pc generated when the altimeter is working to determine whether the altimeter meets the test accuracy requirements. It is difficult to ensure the accuracy of the altimeter measurement by using the direct measurement method. To this end, this paper adopts the method of converting the height pulse signal into the number of pulses to ensure the accuracy of the measurement.
According to the height measurement principle of formula (2), the height is converted into the period length of the modulation period. In order to accurately test the height signal, the modulation signal uses a sawtooth wave pulse signal with a fixed period T1, and the measurement of the period is converted into the count N of the number of sawtooth waves in one modulation period. The calculation formula is as follows:
Where: T is the sawtooth wave period; K1 is the proportional coefficient of the height to the sawtooth wave. The length of this wave reflects the accuracy of the test. In this test system, K1 is 0.1 m/piece, that is, the accuracy of a sawtooth wave pulse is 0.1 m. [page]
2 Analysis of the structure of the test system
The resources for altitude signal testing mainly include test power supply, altitude simulator, data acquisition card, digitizer, industrial computer, display and adapter, etc. The altimeter test system uses the industrial computer as the main control device and realizes the test of the radio altimeter altitude through data acquisition based on LabWindows/CVI software. The overall block diagram of the system is shown in Figure 2.
First, the industrial computer sends a control command to the altitude simulator, and the altitude simulator generates a corresponding altitude signal to the radio altimeter; at the same time, the industrial computer sends a control signal, outputs a radio detection command through the digital I/O port of the digital acquisition card and the adapter, and puts the altimeter in working state. Then the industrial computer sends a control command to control the data acquisition card through the digital I/O port of the data acquisition card, and starts to collect the altitude control signal Pc. The industrial computer processes and stores it, and generates a control signal according to the rise and fall of the Pc signal, which serves as the start and end signal of the modulation period signal Pn. The industrial computer processes the signal collected by the digitizer and displays the number of sawtooth wave pulses tested on the display. The power module provides voltages of different volts throughout the test process to ensure the normal operation of each module.
3 Test software design The
design of the software test system using LabWindows/CVI software includes the following steps: functional module division, test process, virtual panel design, data processing and measurement result analysis, etc.
3.1 Functional division and test flow
The design adopts a modular design method, that is, the test software is divided into independent modules, and each module is independent of each other when writing and running the program. Modular programming is conducive to test software development, maintenance, debugging and operation. The test software module division is shown in Figure 3.
The initialization module includes a user login interface and a system self-check. The user login interface is a confidentiality measure designed to ensure that the user can use it alone, including user name and password verification. The test software can only be used when the user name and password are correct. The system self-check is a test of the hardware circuit during the altimeter test to ensure that the altimeter test system is in a normal state.
The data acquisition module is responsible for converting the measured signal into a digital signal. The altitude control signal Pc is converted into a digital signal to control the acquisition of the altitude signal Pn. The data processing calculation converts the collected digital signal into the required digital signal according to the corresponding proportional relationship. Error processing includes system error, measurement error and gross error processing. Gross errors can be processed by mathematical methods; the system error is obtained by powering on in the case of an altitude signal, and it is directly eliminated during the test; the measurement error can be reduced to the allowable range by averaging multiple measurements. [page]
The test interface is a sign of the humanized design of the software, which can be changed and maintained according to the needs of customers. The waveform of the measured signal is directly displayed on the virtual panel, the number of pulses and height information are displayed through digital controls, and finally the results are output and printed through Excel. According to the software functions shown in Figure 3, the corresponding software flow is designed as shown in Figure 4.
3.2 Virtual panel design
According to the above software flow chart and the division of software functional modules and combined with user needs, the altimeter test control panel is designed to control the program flow and display the test and analysis results. The following requirements should be followed when designing the panel:
(1) Use Chinese graphical interface;
(2) Prompt an error when the system test does not meet the requirements;
(3) All test information is displayed on the panel at the same time;
(4) The interface is beautiful and elegant, the colors are harmonious, the screen layout is reasonable, and the interface is friendly. The panel designed according to the above requirements is shown in Figure 5.
The upper left corner of the panel is used to display the waveform of the Pn signal. The digital control on the lower left corner displays the working status, test items and methods, and the measurement results of the measured data. It can be compared with the standard value to see if the error is within the allowable range. The upper right corner is the test control button, which is used to control the start, pause, end and print results of the test. The lower right corner is the operating instructions, which provide text prompts and instructions for the test process.
4 Error processing and result analysis
First, the Pn signal sampled by the digitizer is converted into a digital signal stored in the cache of the industrial computer. In order to ensure the accuracy of the measurement results, the measured signal needs to be error processed. The errors generated during the test mainly include systematic errors, random errors and gross errors.
The errors generated during measurement are mainly caused by data transmission delay, relay action delay and acquisition card acquisition delay. These errors are fixed and can be regarded as systematic errors. In addition, the electronic devices used also have certain errors under different temperature conditions. These errors vary randomly and are generally regarded as measurement errors. The interference signals that may appear during the test cause "burrs" to appear in the test results, which are regarded as gross errors. The test data is first processed for gross errors, then for systematic errors, and finally for random errors. [page]

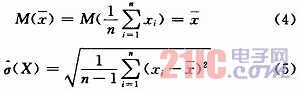
Any measurement error is composed of systematic errors and random errors. Under certain conditions, the error of the i-th measurement of the measured value x is:

where: the systematic error ε is constant when the measurement conditions are the same. When the number of measurements n→∞, the sum of the measurement errors δi tends to 0. The systematic error can be obtained by averaging multiple measurements.

The processing flow of gross errors is shown in Figure 6. First, calculate and estimate the standard deviation, and use c1 times the standard deviation as the judgment standard to determine whether the residual meets the test requirements.
If it does not meet the requirements, eliminate the bad value with the largest residual and re-judge until it meets the requirements. The processing flow of systematic errors is shown in Figure 7. Calculate the mean of n and n-1 measurements respectively, and then calculate the difference between the two. According to the set judgment standard of the n-1 measurement results, determine whether the difference meets the requirements. If it is not satisfied, increase the number of measurement data and re-judge until the requirements are met.
The advantage of this altimeter test system over traditional altimeter test equipment is that it can be digitized, that is, error processing can be performed on digital signals. The processing process of flowchart 6 and flowchart 7 is regarded as the optimization process of the test. The simulated altitudes of 10 m, 30 m, 80 m, 200 m, 500 m and 1 000 m are measured, and the measurement results before and after optimization are shown in Table 1. By comparison, it can be seen that the measurement accuracy of the optimized measurement results is much higher than that before optimization, that is, the effect after error processing has higher accuracy.
5 Conclusion
This altimeter test system adopts data acquisition technology and has higher accuracy. LabWindows/CVI virtual instrument technology makes the test panel more user-friendly, suitable for non-professionals in the field of radio altimeters to test equipment, and improves the practicality and maintainability of the test system. The pulse counting method is used to measure the working altitude of the altimeter, which shows the advantage of digital measurement method over analog data measurement. In addition, the digital acquisition card and digitizer used can also test other test technical indicators of the altimeter, improving the economy of the altimeter test system.
Previous article:Design of Gravity Meter Simulation and Test System Based on LabVIEW
Next article:Design of Multi-sensor Air Flow Test System Based on LabVIEW
- Keysight Technologies Helps Samsung Electronics Successfully Validate FiRa® 2.0 Safe Distance Measurement Test Case
- From probes to power supplies, Tektronix is leading the way in comprehensive innovation in power electronics testing
- Seizing the Opportunities in the Chinese Application Market: NI's Challenges and Answers
- Tektronix Launches Breakthrough Power Measurement Tools to Accelerate Innovation as Global Electrification Accelerates
- Not all oscilloscopes are created equal: Why ADCs and low noise floor matter
- Enable TekHSI high-speed interface function to accelerate the remote transmission of waveform data
- How to measure the quality of soft start thyristor
- How to use a multimeter to judge whether a soft starter is good or bad
- What are the advantages and disadvantages of non-contact temperature sensors?
- Innolux's intelligent steer-by-wire solution makes cars smarter and safer
- 8051 MCU - Parity Check
- How to efficiently balance the sensitivity of tactile sensing interfaces
- What should I do if the servo motor shakes? What causes the servo motor to shake quickly?
- 【Brushless Motor】Analysis of three-phase BLDC motor and sharing of two popular development boards
- Midea Industrial Technology's subsidiaries Clou Electronics and Hekang New Energy jointly appeared at the Munich Battery Energy Storage Exhibition and Solar Energy Exhibition
- Guoxin Sichen | Application of ferroelectric memory PB85RS2MC in power battery management, with a capacity of 2M
- Analysis of common faults of frequency converter
- In a head-on competition with Qualcomm, what kind of cockpit products has Intel come up with?
- Dalian Rongke's all-vanadium liquid flow battery energy storage equipment industrialization project has entered the sprint stage before production
- New breakthrough! Ultra-fast memory accelerates Intel Xeon 6-core processors
- New breakthrough! Ultra-fast memory accelerates Intel Xeon 6-core processors
- Consolidating vRAN sites onto a single server helps operators reduce total cost of ownership
- Consolidating vRAN sites onto a single server helps operators reduce total cost of ownership
- Allegro MicroSystems Introduces Advanced Magnetic and Inductive Position Sensing Solutions at Electronica 2024
- Car key in the left hand, liveness detection radar in the right hand, UWB is imperative for cars!
- After a decade of rapid development, domestic CIS has entered the market
- Aegis Dagger Battery + Thor EM-i Super Hybrid, Geely New Energy has thrown out two "king bombs"
- A brief discussion on functional safety - fault, error, and failure
- In the smart car 2.0 cycle, these core industry chains are facing major opportunities!
- PADS Logic View Operations
- An example of implementing multiple function assignments in Verilog without using state machines and decision functions.rar
- [Repost] Popular Science of Components: Semiconductor Thyristors
- [Xianji HPM6750 Review] Software Simulation SPI to Collect ADS1263 (32-bit ADC) Data
- About the application of PCB drawing board
- STM32F105RBT6
- Detailed explanation of ZigBee networking principle
- How to set up RTC and LPUART to work simultaneously when the HGI MCU is in deep sleep
- Holtek Launches Intercom Signal Receiver
- Some questions about starting xenon lamps