Can manufacturing move to the west?
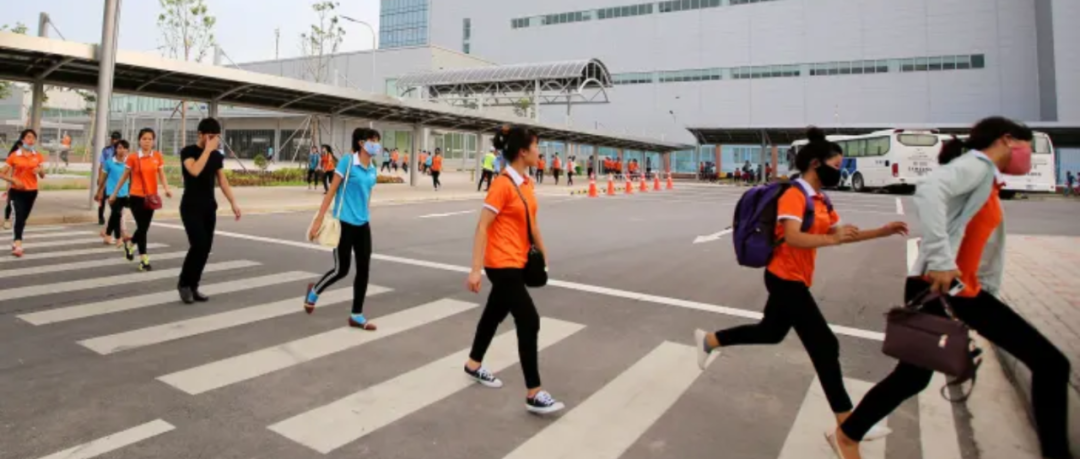
In 2020, the Nikkei website published a report with a very explosive title, "The Inside Story of the U.S.'s Effort to Eliminate China from the Tech Supply Chain." The report revealed such a story: A year ago in the summer, several U.S. officials visited an Apple supplier in Taipei and asked a straightforward question: Why not move more production capacity outside the mainland? Why not speed up the action?
"Manufacturing moving out of China" has been a hot topic in the past two years. The most popular destinations are India and Vietnam. The former has a weak industrial base, while the latter is too small to do anything but assemble mobile phones. In fact, the only destination that can really take over the manufacturing volume of the mainland is Southeast Asia.
Contrary to what many people usually think, Southeast Asia is not a collection of banana republics. Of the $154 billion worth of chips imported by China in the first half of this year, more than $30 billion came from ASEAN countries, accounting for nearly 20%, far exceeding the local specialties of Southeast Asia such as rubber, copper, aluminum, and seafood.
The biggest threat to China's manufacturing industry is actually Southeast Asia
Although there has always been a sense of crisis in China to "not let the manufacturing industry run away", the high land and labor costs in the eastern region have made it difficult to support too many labor-intensive industries such as electronic assembly and processing. With a population of 400 million and half of the country's land area, the vast western region has come to life. From this perspective, to answer whether the manufacturing industry can stay in China is actually to answer how can western China compete with Southeast Asia?
On one side is the country with its long coastline, convenient transportation at the crossroads of the world, rich natural resources, and the unsuspecting support and transfer of Western powers. On the other side is the world's largest labor market, an efficient and prudent technocratic government, and heavy industrial infrastructure capabilities accumulated over decades after the founding of the country.
The fight between the two did not start last year, but spanned more than 30 years. The two sides used the cards in their hands to fight three times in a row to decide who is the real world factory.
In the mid-1980s, the unstoppable rise of Japan's manufacturing industry and the subsequent Japan-US trade conflict gave rise to the first major transfer of production capacity in East Asia.
In 1985, the United States forced Japan to sign the Plaza Accord, hoping to use the sharp appreciation of the yen to weaken Japan's export competitiveness. However, Japan quietly started "entrepot trade" to deal with it, with a surge in foreign investment, investing $170 billion in five years, pouring a lot of yen into the four little tigers in Southeast Asia, more than half of which was investment in manufacturing.
The four little tigers were chosen as the destination by chance. Since 1980, the governments of Thailand's Prime Minister Prem Suthim, Malaysia's Mahathir, and the Philippines' Ramos have all carried out a series of reforms to promote development, but they can be summed up in three ways: relaxing foreign shareholding ratios, encouraging exports, and financial liberalization. To put it simply, it is to "open the door to foreign investment and welcome guests to play."
The effect of opening up is very significant. With the irrigation of cheap Japanese capital and the follow-up of other Western countries, the four little tigers have formed three relatively high-end manufacturing bases:
The first one: the semiconductor alliance between Malaysia and Singapore.
Thanks to the strong financial resources of Temasek and the transfer of production capacity from the West, Singapore's semiconductor industry has been rising since the 1960s, with Chartered Semiconductor, the world's third largest semiconductor manufacturer at the time, and STATS ChipPAC and UTAC, the world's third and tenth largest packaging and testing plants. With Singapore as its big brother, Malaysia also got a taste of the soup. Penang in Malaysia has a unique title: the Silicon Valley of the East.
In 1968, Intel opened its first factory in the United States. Four years later, it opened a subsidiary in Penang. To this day, Intel still has 10 modern assembly plants in Penang, which is its largest assembly plant, experimental base and design and R&D center in the world.
Intel's move in attracted a large number of Western companies, including AMD, HP, Clarion, National Semiconductor, Hitachi, and Bosch. In its heyday, it is said that one-third of the world's semiconductor packaging and testing was carried out here. Even today, Malaysia's packaging industry still accounts for 13% of the global market, making it the world's seventh largest semiconductor exporter, with an export value similar to that of Japan.
The second one: Japan’s layout and the Philippines’ passive components.
Compared with Singapore and Malaysia, which have the best of both worlds, the Philippines, which has a weaker foundation, has chosen to follow Japan completely.
Since the 1960s, Japan has gradually become the largest aid provider to the Philippines. Until the 1990s, more than 50% of the official development assistance (ODA) received by the Philippines came from Japan. Japan also deployed its signature passive components in the Philippines.
As raw materials for the electronics industry, the three major passive components of capacitors, inductors, and resistors have always been controlled by Japanese manufacturers, but what is often overlooked is that Japan's production capacity is a dual-headed layout: in addition to Japan, there is also a production base in the Philippines. Even today, semiconductor exports still account for 30% of the Philippines' total.
Third: PCB boards (printed circuit boards), hard disks and automobiles in Thailand
With the support of Japan, Thailand's automobile production once rivaled that of France, replacing rice and rubber to become Thailand's largest industry. Toyota, Nissan and Lexus automobile production lines are scattered on both sides of the Bangkok Bay, creating a boiling scene of "Eastern Detroit". In 2015, Thailand produced 1.91 million passenger cars and 760,000 commercial vehicles, ranking 12th in the world, more than the total of Malaysia, Vietnam and the Philippines.
Thailand accounts for 40% of the production capacity of PCB boards, which are called the mother of electronic system products, in Southeast Asia, ranking in the top ten in the world, and is on par with Italy. In terms of hard disks, Thailand is the second largest producer after China, and has always accounted for more than a quarter of the global production capacity.
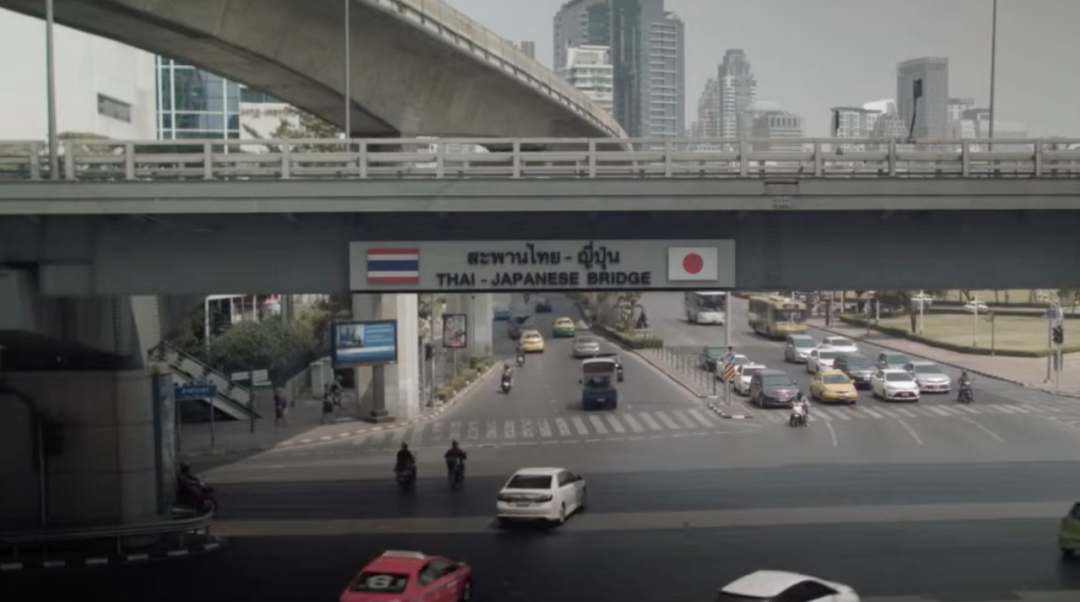
The "Thai-Japanese Friendship Bridge" on the streets of Thailand
With foreign exchange, the four little tigers naturally wanted to show off. In 1996, Thailand spent $300 million to import an aircraft carrier from Spain, becoming the third country in Asia to own an aircraft carrier (currently the main task of the aircraft carrier is to search and rescue fishermen) . In the same year, Malaysia's "Petronas Towers" were completed, becoming the first world's tallest building outside the United States. The World Bank added icing on the cake and released a report praising the achievements of the four little tigers.
The reform of the four little tigers perfectly complies with Japan's demand for going overseas, but it also lays a lot of hidden dangers: the free flow of foreign capital has increased the risk of the financial system, and financial liberalization has allowed domestic companies to borrow cheap funds from abroad and increase their debt. If exports cannot maintain their advantages, a storm is inevitable. Nobel Prize winner in economics Krugman said that the Asian miracle is just a myth and the four little tigers are just paper tigers.
Krugman's words are not pleasant, but his predictions are still very accurate. In 1997, the foreign debt of the four little tigers approached 90% of GDP. Soros and other international tycoons seized the opportunity to launch attacks, and the financial crisis broke out suddenly, and the exchange rates of various countries collapsed. In order to protect themselves, Japanese banks and financial speculators forced loans to Southeast Asia. In one year, more than 100 billion US dollars of capital flowed out of Southeast Asia. Factories stopped working, workers lost their jobs, and the wild geese fell like dominoes.
At the same time, China was in the "deep waters of reform". Special economic zones, triangular debts, layoffs, and tax sharing, each breakthrough was accompanied by fierce competition, but it built a more stable financial and fiscal system for China's opening up to the outside world. Subsequently, the WTO accession negotiations were concluded in Beijing, and overseas capital poured into China from Southeast Asia.
In 1991, Mahathir announced a "Malay Dream", namely Wawasan 2020, with the goal of making Malaysia a high-income country in 2020. Today, the term has been ridiculed by Malay netizens as a synonym for "daydream". In 2005, Intel set up a factory in mainland China, and related suppliers also moved out of Penang. A local investor recalled that Penang has since become a sleepy town.
In contrast, China has the world's factories Shenzhen and Dongguan, a developed manufacturing chain in the eastern coastal areas, and the world's largest human migration, the "Spring Festival Travel Rush". Guangdong's electronic information industry has grown tenfold in ten years since 2001, reaching 2.2 trillion yuan. The Chinese industry was able to complete the first round of counterattack, which can be described in one sentence: hard work on internal strength and crossing the river by feeling the way through Southeast Asia.

In the first round, facing cheap Japanese yen capital, Southeast Asia took the lead in adopting an open door approach and reaped the first dividends of industrial transfer. China chose the strategy of first consolidating the basic foundation and then gradually opening up. As a result, Southeast Asia's decade of accumulation was lost in the face of the financial crisis, while China first stabilized Hong Kong and then took advantage of the opportunity to rise when it joined the WTO.
However, as China's economy takes off, labor costs in the eastern coastal areas continue to rise, and the anxiety of "manufacturing transfer" has already sparked. Against this background, the arrival of the second round of confrontation is only a matter of time.
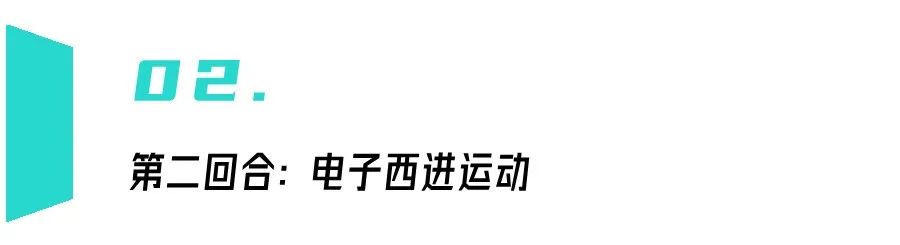
When it comes to finding the low-cost location for global manufacturing, Terry Gou is faster than Hong Kong reporters. He was the trigger for the second confrontation between China and Southeast Asia.
In November 2006, Vietnam was approved to join the WTO. Three months later, Terry Gou led a delegation to Bac Ninh Province, Vietnam for research. Terry Gou was "pleasantly surprised" to find that wages in Vietnam were only one-third of those in Shenzhen. It only took 14 hours to travel from Longhua, Shenzhen to northern Vietnam. Parts were sent in the evening and assembly could begin the next morning. It was no pressure to move the Shenzhen factory here.
So a few days later, Guo met with the President of Vietnam and decided to invest $1 billion in Vietnam over five years. He also bought more than 400 hectares of land in Bac Ninh to build a world-class foundry. The "Southward Plan" was ambitious.
As it turned out, man proposes, but heaven disposes. The financial crisis broke out the following year, and Foxconn's plan to build a factory in North Vietnam was also affected and forced to stop. On the contrary, China's strong stimulus policy once again stabilized the morale of industrial giants and international capital. "Chinese workers" ranked second in the "Person of the Year" selection of Time magazine in the United States. They were called the behind-the-scenes heroes of China's economy "maintaining 8% growth" after the financial crisis.
However, two years after the financial crisis, Foxconn Shenzhen Park had a "14-person suicide" incident. More than 200 news media from around the world flocked to the Longhua Park, turning Terry Gou's Forbidden City upside down. Every day, 40 tons of rice, 10 tons of flour, 30 tons of vegetables, 200 pigs, 60,000 eggs and 500 barrels of cooking oil are consumed here to feed 300,000 workers in the park. For them, Foxconn is Shenzhen, and Shenzhen is Foxconn.
Under huge public pressure, Foxconn raised the wages in the Shenzhen campus from 800 yuan to 2,000 yuan. Then, Apple CEO Cook personally visited the Foxconn factory in Shenzhen and left a message: the factory needs to be located closer to the workers' homes. In other words, the Shenzhen factory had to be relocated.
So where should the factory move to? At that time, there was such a data: if a computer was shipped from Shenzhen to Europe by sea, the freight cost was about 4 US dollars per unit; if it was shipped by air, the freight cost was between 20 and 40 US dollars. From this perspective, Southeast Asia has many ports and the transportation cost is better than that in mainland China. If doing business with Europe and the United States, Southeast Asia is a good choice.
Foxconn wanted to relocate its factory, and Shenzhen wanted to replace its old factory with a new one. In order to stop Foxconn from moving south , a "westward movement" was launched. For a period of time, officials from the investment promotion department followed wherever Guo Taiming's plane landed. Behind this was a huge plan consisting of reconstruction of major transportation arteries, construction of local bonded areas, and government-mobilized recruitment .
In August 2010, Huang Qifan, then mayor of Chongqing, led a team to Beijing and requested the General Administration of Customs and the Ministry of Railways to open a railway corridor from Chongqing to Europe. Behind the request was a subtle calculation: although the cost of railways was higher than that of sea transportation, the speed was far ahead. Considering that digital products value timeliness more and have a high unit price, railway transportation would be the preferred choice for the electronics industry.
After obtaining permission from Beijing and mediation from five countries, the land bridge was completely opened. It only takes 13-16 days to transport electronic products from Chongqing to Duisburg, Germany, which is only 1/3 of the time required for sea transportation. The transportation cost of high-value goods is even lower than that of sea transportation.
Chongqing-Xinjiang Eurasian Continental Bridge
As land transportation in the central and western regions was opened up, air transportation was also upgraded. In 2007, the reconstruction of Henan Xinzheng Airport was completed; in 2010, the third phase of Chongqing Jiangbei Airport expansion was completed; in 2011, Chengdu Shuangliu International Airport Cargo Terminal was completed and put into operation. The upgrade of the three major airports means that the annual air transportation capacity of the three provinces and cities combined exceeds one million tons, equivalent to 6 billion mobile phones.
Zhengzhou Airport
One of the major characteristics of Apple product manufacturing is that both ends are outside, that is, raw materials are imported from outside and the market is exported. Therefore, for the processing enterprise Foxconn, the most ideal situation is to be able to process and produce in the bonded area, thereby eliminating the process and cost of importing parts and exporting products. Therefore, a series of bonded area constructions are being promoted in full swing.
In 2009, Chongqing went to Beijing to apply for a bonded zone; more than a year later, Zhengzhou and Chengdu also applied. In order to speed up the operation of the bonded zone, Zhengzhou called for a "hundred-day battle" to complete the supporting factories and roads in three months. Soon, the bonded zone factory building close to the airport runway was built on the spot, and buses began to pick up workers to work at the Foxconn factory.
The third way the government tried to win over Foxconn was to recruit workers in person. Foxconn's Henan factory alone had 94 production lines and needed 350,000 workers to arrive quickly. In order to achieve the goal, the Henan Provincial Government held a special meeting on recruitment, which was broken down to 18 prefecture-level cities. Even in Zhengzhou, each community committee had to recommend 10 people. The Chengdu Labor Bureau set up a recruitment point at the railway station to recruit migrant workers on the spot.
As a result, although the electronics industry chain has partially left China's eastern coastal areas, most of it has been taken over by the central and western regions: Sichuan produces 70% of the world's iPads, Henan produces more than half of the iPhones, and Chongqing accounts for 40% of laptops. The combined output value of the electronics industry in the three provinces and cities exceeds 2 trillion yuan, equivalent to the entire GDP of Vietnam.
In 2012, Thailand suffered the worst flood in 50 years, with the disaster area covering one-third of the country, and the royal palace was not spared. Japanese companies producing PCBs in Thailand had to choose to stop production, and Apple also transferred these orders to mainland China, which has stronger buffering capacity and faster repair speed.
Three years later, Chinese chip packaging and testing company Tongfu Microelectronics acquired all of AMD's factories in Penang, Malaysia. Following closely, Huatian Technology bought Unisem, one of the twin packaging and testing companies in Malaysia, and the Eastern Silicon Valley came to an end.
In the second round of battle between mainland China and Southeast Asia, local governments in China used the three axes of new logistics trunk line + bonded area + mobilization recruitment to strike hard and quickly pull production capacity to the central and western regions while the industrial chain was still hesitating. But at this time, Southeast Asia also ushered in the biggest change since the Asian financial crisis: the arrival of the new "economic overlord" South Korea.
In 2012, Samsung Chairman Lee Kun-hee and his successor Lee Jae-yong visited Vietnam together and held a meeting there to discuss future plans. They eventually decided to move the mobile phone assembly business to Vietnam and created an ambitious "Lee Jae-yong Plan" for it. This also means that South Korea has begun to take over from Japan and start a large-scale layout in Southeast Asia.
In the same year, Samsung invested in building a mobile phone assembly plant in An Phong Industrial Zone, Bac Ninh Province in northern Vietnam. This huge factory standing in the rice fields was called "Samsung City" by the locals. It was used to manufacture 120 million mobile phones. The factory's electronic version read: "SEV (Samsung Vietnam) will become the world's largest mobile phone factory, and we are proud of it."
After the East Asian financial crisis, Japan's economic output remained stagnant for nearly 20 years, while South Korea, after climbing out of the bloodbath, began to grow rapidly, surpassing Russia to become the world's eighth largest industrial country, and its per capita GDP reached 70% of Japan's. However, South Korea's small mainland could not support the rapid rise of South Korean companies, so moving south became an inevitable choice. In 2014, South Korea surpassed Japan to become Vietnam's largest source of FDI.
Major sources of FDI (foreign direct investment) in Vietnam
In the past decade, Samsung has invested more than $17.3 billion in Vietnam. For smartphones alone, Vietnam's factories produce about 150 million units a year, accounting for about half of the world's total output. Overall, Samsung's exports in Vietnam reached $60 billion in 2018, accounting for one-third of Vietnam's national exports. More importantly, South Korea is personally nurturing the growth of the supporting industrial chain.
In 2014, Samsung planned to purchase 91 parts from Vietnam, but none of them met the standards. Therefore, in order to cultivate local suppliers in Southeast Asia, Samsung sent a large number of experts to Vietnam, providing financial support and technical support. As of 2019, 35 Vietnamese companies have become Samsung's first-tier suppliers, and 190 Vietnamese companies have participated in Samsung's supply chain.
Four years after South Korea's deployment, Trump, who won the election, also began to use tariffs and political pressure as leverage to pry China's industry. In addition to directly and roughly imposing tariffs on Chinese exports, the US government also lobbied everywhere. In September this year, officials from the American Institute in Taiwan even held a forum on supply chain restructuring with their counterparts in the European Union, Canada, Japan and other countries, openly advocating for transfer.
Foxconn originally produced sensitive network communication products in Nanning, Guangxi, but has now moved the production to Bac Ninh, Vietnam, to serve major American customers such as Cisco. Taiwan's leading foundry companies after Foxconn, such as Compal, Wistron, Pegatron, and Inventec, are also taking action.
Compal has restarted its factory in Vinh Phuc, North Vietnam. The first plant for network communication products will soon be fully loaded, and the second plant for PC production will also be put into production in the middle of next year. Some impatient companies can't even wait to buy land and build factories. For example, the communication equipment manufacturer "Qiyi" directly rented a factory building from Handa Precision. After all, if it is delayed for a month or two, the big American customer may not be retained.
In addition to Taiwanese companies that do OEM, many mainland parts factories in Apple's industrial chain are also facing pressure to relocate. A manager of Desay Battery mentioned that 70% of its customers' products are to be sold to the United States, and they are eager to come to Vietnam to ask for production. Luxshare Precision said that if necessary, the company will continue to transfer products affected by (tariffs) to Vietnam or other countries. According to Foxconn's plan, the first non-Chinese-made iPad will be launched in Vietnam next year.
Vietnam itself is not a threat, but if Vietnam is the core of assembly, coupled with the four tigers with a solid foundation in the electronics industry chain, it will form a powerful parts supplier and become a huge threat to China's domestic manufacturing industry. And this threat is brewing.
In 2015, Samsung invested 288 billion won to build an MLCC factory in Laguna, Philippines. Three years later, the Philippines' production capacity has exceeded 40 billion pieces per month, accounting for 40% of Samsung Electro-Mechanics' production capacity, more than double that of South Korea. In the first half of 2019, foreign direct investment in Penang, Malaysia, soared 11 times to about US$2 billion. American companies such as chipmaker Micron Technology and iPhone supplier Jabil Inc. have built factories in Penang.
Even the Thai electronics industry, which was hit hard by the floods, has seen a glimmer of new hope. In 2017, Seagate, the world's largest hard disk manufacturer, closed its Suzhou factory in China, one of its three major assembly bases, and instead planned to deploy half of its production capacity in Thailand.
With US policy pressure and South Korea spending money and sending people, several Southeast Asian countries have once again launched a competition for the electronics industry chain. How should China protect the results of its westward expansion?
Facing Southeast Asia’s third round of counterattack, China’s strategy is to use its strong infrastructure capabilities to build deep trenches and high fortifications to construct a wall to defend against the relocation of the industrial chain.
The direction of the manufacturing industry is certainly influenced by the maneuvers between countries, but it all comes down to two words: cost. As long as the cost can still widen the gap with foreign countries, no external forces can go against the economic law and make the manufacturing industry flow out.
When it comes down to costs, there are five basic elements: raw materials, labor, water and electricity, factory buildings, and taxes.
At present, Vietnam's labor costs are more than 20% lower than those in the west, and there are no tariffs imposed by the United States. The prices of raw materials, factories, energy, and other materials are almost the same as those in China. This is also the direct reason why many industrial chains are willing to follow Apple and Samsung in relocating. More importantly, Vietnam has also followed suit and started to develop various industrial parks and bonded areas, which has forced China to play new cards to protect its industries.
This card is to use the traditional skills of the infrastructure maniac to change the factor prices in the western region.
The first factor is energy. Giant hydropower stations and photovoltaic power stations are changing the energy structure of western China, one in the south and one in the north.
In 2016, near the Jinsha River at the junction of Sichuan and Yunnan provinces, hundreds of dump trucks and heavy excavators were coming from the nearby mountain roads. The construction here is the world's second largest hydropower station, the Baihetan Hydropower Station . The hydropower station is expected to be completed in 2022. After completion, it will generate more than 60 billion kWh of electricity per year, which is close to 1/3 of Vietnam's national electricity generation. The cost is as high as 177.8 billion yuan, equivalent to 1/3 of Vietnam's fiscal revenue in one year.
The preparation work for Baihetan was huge. First, more than 110,000 migrants from seven counties had to be resettled, and then 13 bridges and 30 kilometers of tunnels had to be built for transportation. It took five years to complete the periphery. The dam has 16 million-ton giant generators that are more than 50 meters high and weigh more than 8,000 tons. Each one weighs as much as the Eiffel Tower in France. It is also known as the "Mount Everest" of the hydropower industry.
Construction site of Baihetan Hydropower Station
In southwest China, 14 large hydropower stations have been started and completed alternately on the Jinsha River, which is led by China Yangtze Power, the Lancang River, which is led by Huaneng Hydropower, and the Yalong River, which is led by SDIC Power and Sichuan Energy. Their power will be more than four times the power generated by the Three Gorges Dam. Among them, the Baihetan, Luoxidu, and Wudongde hydropower stations will be the second, third, and seventh largest hydropower stations in the world, respectively. After 2022, China will undoubtedly take the first, second, and third place in the world's hydropower stations.
At the same time as the hydropower development in the southwest, photovoltaic power generation in the northwest was also carried out. In the past decade, photovoltaic power generation has long been ridiculed as "subsidy fraud", and Chinese photovoltaic companies have gone bankrupt one after another in the cruel choice of technical routes. However, in 2019, people were surprised to find that 19 provinces have been able to achieve the same cost of photovoltaic power generation as coal-fired power generation, and the cost is still being reduced by nearly 20%.
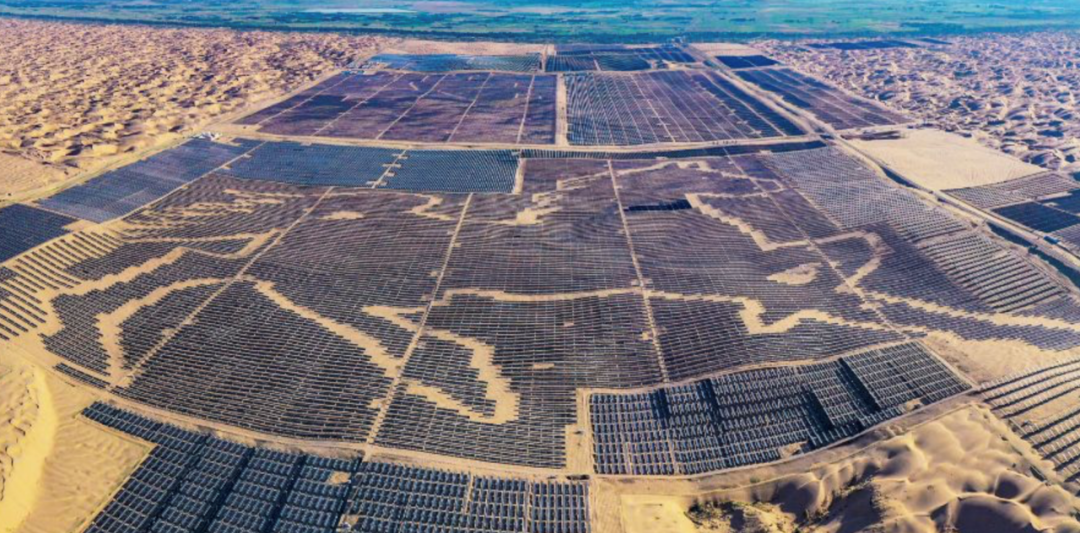
Another card is to improve transportation and reduce the transportation cost of raw materials. Specifically, it is to use dense highways and high-speed railways to integrate the west into a transportation network that is not inferior to the east, so that parts and raw materials in the east can be smoothly imported to the production base in the west at low cost.
In 2019, Guizhou's expressway mileage reached 6,453 kilometers, ranking seventh in the country, surpassing Jiangsu. However, behind this mileage, 47 of the world's top 100 high-speed bridges are in Guizhou. There are more than 1,400 tunnels in Guizhou, so half of the Guiyang-Guangzhou high-speed railway runs underground.
After changing the factor structure, the West has gained a few more big cards. For example, the decline in electricity prices will increase the attractiveness of the power-intensive semiconductor industry. Take TSMC as an example. Its annual electricity consumption is 13 billion kWh. If the price of electricity per kWh is reduced by 0.1 cent, it can save $200 million in electricity costs every year.
This means that the west can become a base for high-energy-consuming electronic manufacturing industries such as semiconductors. In fact, last year Samsung invested more than 10 billion US dollars in Xi'an to expand its chip factory. There are many industries like Samsung that have moved their component factories inland. BOE has continuously added funds to expand its Chengdu panel factory, and Tsinghua Unigroup is preparing to put its Chongqing storage chip base into production, which shows that the second westward movement is quietly underway.
This time, it is not a simple assembly plant, but a parts plant with more technological content. This also means that in a few years, the cost of parts raw materials and energy in the West will be significantly lower than that in Southeast Asia, thus offsetting the disadvantage in labor costs.
The third battle between the westward and southward movements, the footsteps were getting closer.
In the past four decades, whoever can become the world's factory, in addition to their own efforts, also depends on the layout of the economies with super-large multinational corporations behind them.
Thailand’s ability to become the “Detroit of the East” in the 1990s was inseparable from Japan’s full support. Vietnam’s rapid rise in the past decade was inseparable from the emerging economic alliance between Vietnam and South Korea. In essence, they are all an industrial country with the ability to plan and train a top henchman.
However, whether it is the Southeast Asian financial crisis or the subprime mortgage crisis, we can find the hidden dangers of this bundled development: in an economic crisis, once the big brother shrinks to protect himself and cuts off order demand and financial support, the little brother will be hurt and easily fall into a cycle of prosperity, recession and recovery, taking two steps forward and one step back. This also makes it difficult for these countries to make qualitative improvements in their industrialization levels.
To truly become a manufacturing powerhouse, rather than a "factory", we cannot just focus on the industrial transfer of leading countries, but also need internal strength: heavy industrialization can enable the development of local supporting facilities at low cost, strong infrastructure capabilities can lower the level of factors, and local super companies can master brands and demand. These points are exactly the internal strengths that China has practiced every time it fights with Southeast Asia.
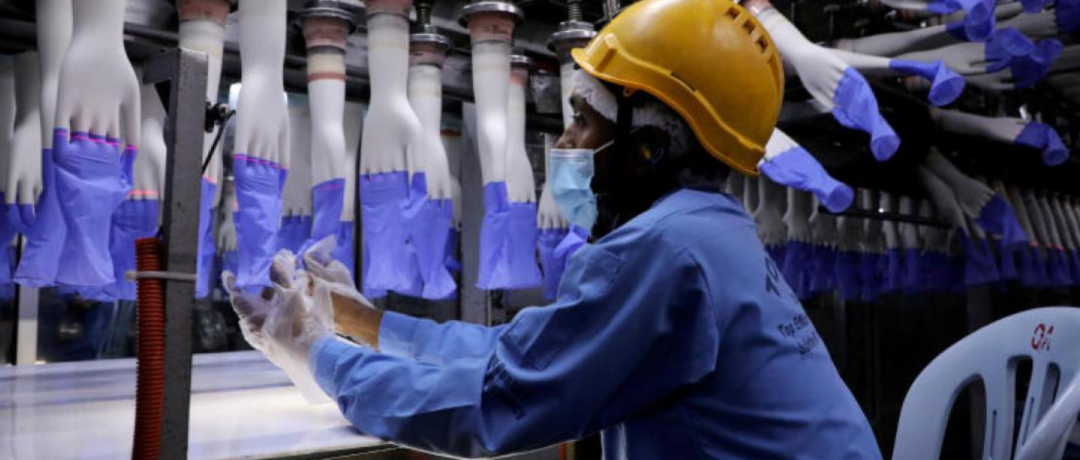
Top Glove is the world's largest rubber glove factory, located in Malaysia
More than 2,000 of their workers were infected with COVID-19 in the last month.
The first confrontation: Southeast Asia grabbed Japan's industrial transfer, but due to the low level of basic industrial development, Thailand had to import a large number of foreign equipment and parts, which was very costly. At the same time, China carried out drastic reforms, and its steel production exceeded 100 million tons, becoming the world's largest. Its basic skills became unique among developing countries.
The second battle: Southeast Asia wanted to compete for industries with lower land and labor factors. But China responded quickly and moved its industries inland first. Behind this was China's strong infrastructure capabilities, which could transform the uninhabited industrial parks in the central and western regions into rear industrial bases with complete transportation, factories, water and electricity in just two or three years.
The third battle: In addition to the early deployment of super projects and the reduction of factor costs, the global industrial chain has actually undergone a more profound change, that is, China itself has become a chess player and has the ability to deploy. Especially for high-end manufacturing, just one power outage can eliminate a large number of countries.
The fundamental reason for the different fates of the Four Little Dragons and the Four Little Tigers is that the former, under the leadership of authoritarian governments, gave birth to companies that could invest according to their own wishes and pace. Samsung's counter-cyclical capacity investment during the Asian financial crisis and TSMC's increased R&D spending during the subprime mortgage crisis all turned crises into opportunities. This is the difference between chess players and lackeys.
In the field of consumer electronics, China has already produced brands that grasp terminal demand and has a huge local supply chain, which means that the initiative itself is in China's own hands. The choice of going south or west is just a choice based on factor prices. Even if it goes south, it is just a spillover. The days when a few Western brands mastered the global supply chain and could determine the level of industrialization of a major country are actually over.
Gary Pisano, a professor at Harvard Business School, once mentioned in "Manufacturing Prosperity: Why America Needs a Manufacturing Renaissance": Americans once believed that innovation and manufacturing were separable, that innovation was something that white-collar workers did when they drank coffee and pondered in Starbucks, and that entrepreneurs sketched ideas on napkins during lunch. But in fact, without engineers working hard on manufacturing processes in factories, these innovations were just empty talk.
Reply to any content you want to search in the official , such as problem keywords, technical terms, bug codes, etc., and you can easily get relevant professional technical content feedback . Go and try it!
Since the WeChat official account has recently changed its push rules, if you want to see our articles frequently, you can click "Like" or "Reading" at the bottom of the page after each reading, so that each pushed article will appear in your subscription list as soon as possible.
Or set our public account as a star. After entering the public account homepage, click the "three dots" in the upper right corner, click "Set as Star", and a yellow five-pointed star will appear next to our public account name (the operation is the same for Android and iOS users).

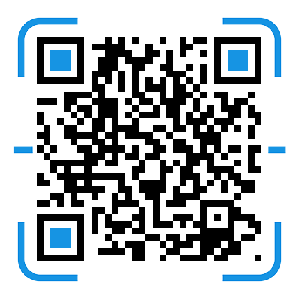
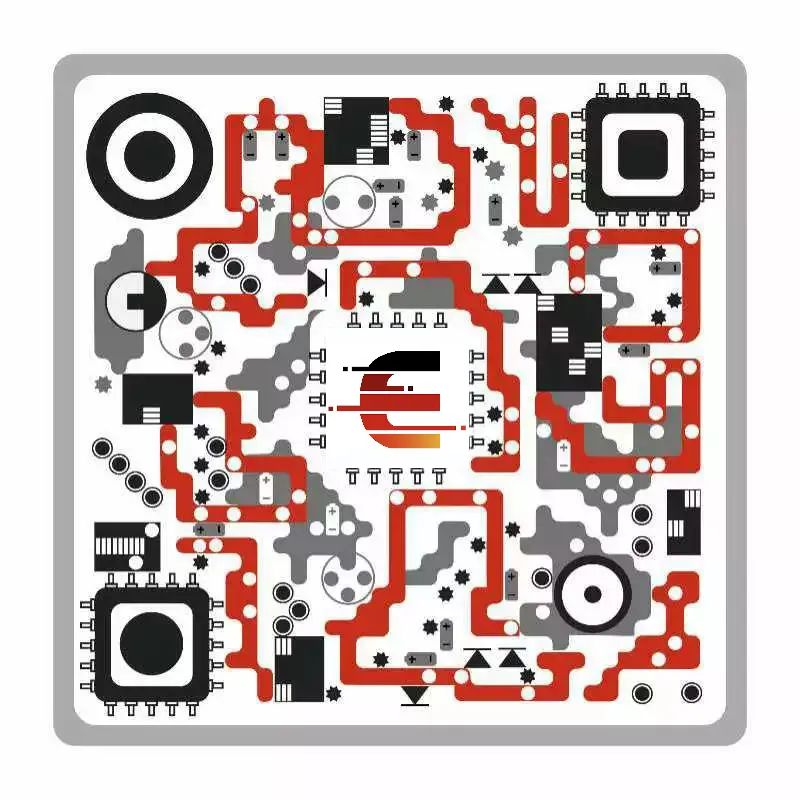
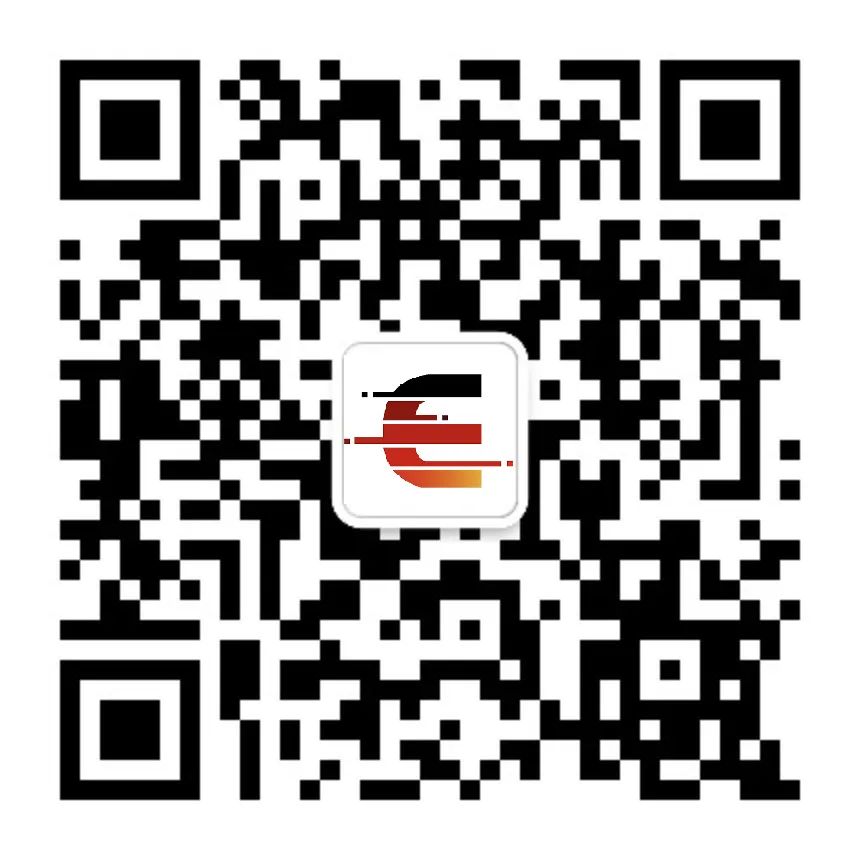
Featured Posts