Relay control circuit
Source: InternetPublisher:红水杯 Updated: 2011/10/10
CMOS integrated blocks that can drive relays to work. People always think that CMOS integrated blocks cannot directly drive relays to work. However, experiments have proved that some CMOS integrated blocks can not only directly drive relays to work, but also work stably and reliably. The model of the relay used in the experiment is JRC5M-DC12V miniature sealed relay (its coil resistance is 750Ω). Now the working principle of the CD4066 CMOS integrated block driven relay is analyzed as follows:
CD4066 is a four-way analog switch, and the integrated blocks SCR1~SCR4 are the control terminals, used to control the on and off of the four two-way analog switches. When SCR1 is connected to high level, pins ① and ② of the integrated block are turned on, +12V → K1 → pins ① and ② of the integrated block → the negative pole of the power supply, causing K1 to close; conversely, when SCR1 is input to low level, pins ① and ② of the integrated block are open circuit, K1 is released when it loses power. When SCR2~SCR4 input high level or low level, the state is the same as SCR1. In the circuit, a diode is connected in anti-phase and parallel at both ends of the relay coil. It is used to protect the integrated block and must not be omitted. Otherwise, when the relay changes from the pull-in state to the release state, a diode will be generated on the coil due to the action of the inductance. A higher back electromotive force can easily lead to breakdown of the integrated block. After the diode is connected in parallel, at the moment when the relay changes from attraction to release, the coil will form a short-term freewheeling loop through the diode, so that the current in the coil does not mutate, thus avoiding the generation of counter electromotive force in the coil and ensuring that the integrated block safety. The pull-in measures of relays under low voltage often fail to work properly because the power supply voltage is lower than the pull-in voltage of the relay. In fact, once the relay is closed, it can work reliably at about half of the rated voltage. Therefore, you can give the relay a starting voltage at the beginning to make it close, and then let it work at a lower power supply voltage. The circuit as shown in the figure can achieve this purpose.
Working principle: As shown in the figure. V1 is a single-junction transistor BT33C, which forms a relaxation oscillator with R1, R2, R3 and C1. SCR is a one-way silicon controlled thyristor. After pressing the start button AN1, the circuit is energized. Because the SCR has no trigger voltage, it does not conduct electricity. On, relay J does not operate, and the power supply quickly charges capacitor C2 through R4 and VD1 to a level close to the power supply voltage (Vcc-VD1 voltage drop). At the same time, the power supply charges capacitor C1 through R1. After a few seconds, the voltage on C1 is charged to the trigger voltage of V1. C1 immediately discharges through V1, forming a positive pulse on R3. This pulse is added all the way to the base of V2, causing V2 to quickly saturate and conduct, and the collector of V2 is the capacitor C2. The positive terminal is close to ground. Since C2 is charged with a positive voltage of positive and negative polarity at this time, the negative electrode of C2, that is, one end of the J coil, has a negative potential. The positive pulse on R3 goes through VD2 and C3 to trigger the thyristor to conduct, and the SCR cathode, that is, the other end of the J coil, is close to the power supply voltage. At this time, the J coil actually withstands about twice the power supply voltage, so J1-1 is closed. After releasing AN1, J1-1 protects itself. J1-2 cuts off the power supply of V1 and V2, and the relay works at a voltage close to the power supply. In the figure, AN2 is the stop button. When AN2 is pressed, J loses power and is released, J1-1 is disconnected, and the entire control circuit loses power. When making this circuit, it is generally recommended that the rated voltage of the relay be about 1.5 times the power supply voltage. Under normal circumstances, any type of one-way thyristor (or two-way thyristor) can meet the needs of this circuit. The withstand voltage of V2, C1 and C3 depends on the selection of the power supply voltage. The withstand voltage of C2 is preferably no less than twice the power supply voltage. Three additional circuits of relays Relays are a commonly used component in electronic circuits. In electronic switch drive circuits generally composed of transistors, relays and other components, some additional circuits are often added to change the working characteristics of the relay or provide protection. effect. The additional circuits of relays mainly have the following three forms:
1. Relay series RC circuit: The circuit form is shown in Figure 1. This form is mainly used in circuits where the rated operating voltage of the relay is lower than the power supply voltage. When the circuit is closed, the relay coil will generate electromotive force due to the self-induction phenomenon, which hinders the increase of current in the coil, thus prolonging the pull-in time. After connecting the RC circuit in series, the pull-in time can be shortened. The principle is that at the moment the circuit is closed, the voltage across the capacitor C cannot change suddenly and can be regarded as a short circuit. In this way, a power supply voltage higher than the rated operating voltage of the relay coil is added to the coil, thereby accelerating the increase in current in the coil and making the relay Quickly absorbs. After the power supply is stable, the capacitor C has no effect, and the resistor R acts as a current limiting function. 2. Relay parallel RC circuit: The circuit form is shown in Figure 2. After the circuit is closed, the RC circuit does not work when the current is stable. When the circuit is opened, the relay coil generates an induced electromotive force due to self-induction, and is discharged through the RC circuit, causing the coil to The current decay slows down, thereby prolonging the relay armature release time and acting as a delay. 3. Relay parallel diode circuit: The circuit form is shown in Figure 3, mainly to protect driving components such as transistors. When the transistor VT in the figure changes from on to off, the current flowing through the relay coil will decrease rapidly. At this time, the coil will generate a high self-induced electromotive force which is superimposed with the power supply voltage and added between the c and e poles of VT. It will cause the transistor to break down. After connecting the diode in parallel, the self-induced electromotive force of the coil can be clamped to the forward conduction voltage of the diode. This value is about 0.7V for silicon tubes and about 0.2V for germanium tubes, thereby avoiding breakdown of driving elements such as transistors. device. When connecting diodes in parallel, be sure to note that the polarity of the diode cannot be reversed, otherwise it will easily damage drive components such as transistors. Non-inductor analog relay This article introduces a non-inductor analog relay. Its circuit principle is shown in the figure below.
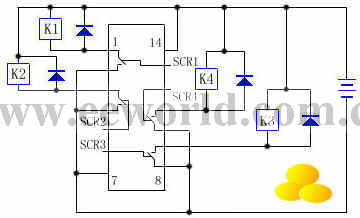
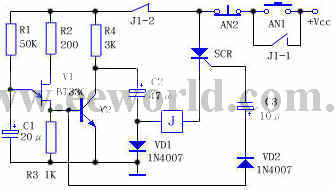
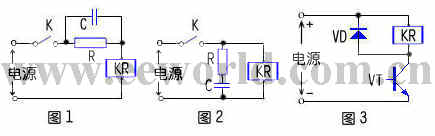
Latest Control Circuits Circuits
- Model rocket launch controller circuit
- Build a Smart Garage Door Opener Using a Raspberry Pi
- How to Make a Simple Chicken Incubator
- How to Build a Touch-Based Color-Changing Plant Using Arduino
- JDB-LQ-TQ/2 motor full voltage starting circuit
- Using P110C to control 6 DC motors simultaneously
- Car audio system anti-theft circuit
- Password type motorcycle anti-theft device
- Vibration anti-theft alarm circuit
- Multi-channel laser anti-theft alarm circuit
Popular Circuits
- Homemade disinfectant circuit
- Multi-channel patrol detection control circuit a
- Assembly line outage monitoring circuit
- Haier KFR-25GW air conditioner control circuit schematic diagram
- Galanz rice cooker control circuit
- Range hood detection control circuit
- Small power electric heater temperature detection control circuit
- Electric heater temperature detection control circuit
- Voltage servo motor and control circuit
- Wide input range non-synchronous voltage mode control circuit