Ultrasound systems vary in their functionality and performance. For example, some high-end systems typically have 3D, 4D, and harmonic imaging modes, while some low-end systems may only have 2D B-mode imaging and spectral Doppler imaging modes. Functional differentiation mainly depends on the digital backend. High-end ultrasound systems require more and faster high-end DSP computing resources to achieve near real-time signal processing. Obviously, it is difficult to share signal processing units between high-end and portable systems. However, ignoring the different performance requirements, ultrasound systems generally have similar receive channel architectures.
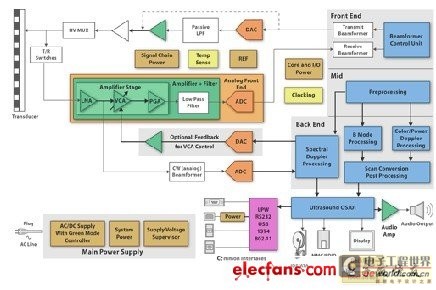
Figure 1 Ultrasonic system structure diagram
As shown in the figure, the ultrasound system receive analog front end consists of common blocks such as: low noise amplifier (LNA), time gain control (TGA) amplifier, voltage controlled amplifier (VCA), programmable gain amplifier (PGA), low pass filter and analog-to-digital converter (ADC). In any case, the performance of the AFE will greatly affect the performance of the entire system. Therefore, as long as there are AFE products that meet different performance requirements in pin-to-pin compatible packages, the AFE design can be standardized and reused in various systems. This standardization can be easily implemented in mid- and low-end systems, which do not require special analog signal conditioning.
However, most current AFE products cannot meet the needs of ultrasound product manufacturers. Therefore, some separate chips must be selected to meet the various performance requirements of pocket and desktop systems. For example, a desktop system may allow higher power consumption but must achieve lower noise, or vice versa, so a redesign is necessary.
Some new AFE devices, such as TI's AFE5805, maintain the same external pinout. They target a variety of ultrasound systems from portable to desktop. Pin-to-pin compatibility will allow ultrasound product manufacturers to standardize AFE designs and design innovative products with significant cost savings and fast time to market.
Relationship between analog front-end characteristics and system performance
Always remember that designing an ultrasound system is a complex matter and that every characteristic of the AFE affects the performance of the entire system. The ability to balance the various parameters for each system category is undoubtedly an art.
Power consumption is a key consideration for portable ultrasound systems. Low power consumption means longer operating time with less battery power. However, it affects other parameters such as input signal range, input equivalent noise, harmonic distortion, etc., although these performance degradations are usually acceptable for portable (low-end) systems.
In addition to power consumption, AFE noise is the second factor that ultrasound system designers need to consider. The received signal level of an ultrasound transmitter may vary from 10uVPP to 1VPP [1]. The smaller the signal that can be detected, the higher the sensitivity of the system. Both input equivalent current and input equivalent voltage noise affect system sensitivity. Generally speaking, noise parameters of 0.7 nV/rt(Hz)~1.5 nV/rt(Hz) (RTI) are used for high-end to low-end systems. Some real-world system applications have proven that these noise parameters are sufficient to produce high-quality images. Although a lower noise amplifier can be used, it will not significantly improve the final ultrasound image quality because the input equivalent current noise and transmit/receive (T/R) switch noise need to be considered. In addition to input equivalent voltage noise, flicker noise (i.e., 1/f noise) is also an important factor in imaging applications. In continuous wave (CW) mode with mixing, the low-frequency noise spectrum is shifted to the carrier frequency, thereby reducing the signal-to-noise ratio (SNR) of the relevant frequency. Amplifiers with white noise performance are superior to those with a wide operating frequency.
In some ultrasound applications, the gain control range plays an important role in achieving the image dynamic range. When the VCA has a higher gain control range, the final image has a wider dynamic range, resulting in higher image quality. Combined with the SNR of the ADC, the dynamic range of the system can be calculated by the following equation:
Dynamic Range = SNR + Gain Control Range (Equation 1)
For example, a system with a 12-bit, 70dB SNR and 40dB gain control range VCA can achieve a dynamic range of 110dB. In other words, considering the attenuation coefficient of 0.7dB/cmMHz of the human body, the imaging depth of 10cm and the 7.5MHz transmitter, a dynamic range of 105dB can be calculated by 10*2*0.7*7.5. In some current ultrasound systems, 10~15MHz probes are usually used to image a small range. Therefore, a dynamic range of more than 100dB is usually required, which leads to the conclusion that an AFE with a large gain control range is preferred. In addition, a higher overall gain AFE is an aid in detecting small signals and compensating for insertion losses caused by other circuits (for example, the insertion loss of passive high-order filters).
Amplifier saturation and overload recovery are also important system parameters. It is more valuable to evaluate and calculate these two parameters together rather than discussing them separately. Basically, the ideal input signal range of an amplifier is limited by its linear output voltage (related to the supply voltage) and gain.

Therefore, lower gain and higher supply voltage are beneficial to this parameter. However, low gain reduces the input equivalent voltage noise, while high supply voltage increases the total power consumption, so a compromise must be used. For some portable and mid-range systems, a parameter of 200-400mVPP is usually selected. Ultrasound amplifier saturation is usually caused by leakage of high voltage pulses or large signals reflected from near-surface objects with very different acoustic impedances. Such examples include epidermal tissue or bone, where only a small amount of clinical information is available. In most cases, the loss of information in these areas may not affect the clinical diagnosis. However, if the amplifier cannot recover in time, a large amount of information will be lost. The fast overload recovery time of the AFE ensures that the ultrasound system can obtain as much useful information as possible. The overload recovery time of the AFE can be expressed in the number of ADC clock cycles. An overload recovery time of one clock cycle is ideal.
Another effect of ultrasound amplifier saturation is increased harmonic distortion. With the widespread use of contrast agents, more and more systems (even portable systems) require low second harmonic distortion of the entire system to ensure smooth harmonic imaging. Generally speaking, the harmonic signal received by the transmitter can be as high as 40dB (below the fundamental signal), depending on the combination of contrast agent acoustic properties, transmitter voltage and tissue characteristics. Therefore, the amplifier's HD2 should be less than 40dBc, which enables the system to obtain ideal harmonic images. In addition, high HD2 may cause artificial Doppler shifts. In some clinical situations, this artifact may affect the accuracy of diagnosis. In the final Doppler image, the artificial Doppler shift will cause the directional isolation of the Doppler system. Some literature [2;3] shows that for some CW and PW Doppler systems, 45~50dB of directional isolation may be sufficient. Due to the above factors, when HD2 is less than 40dBc, the linear input range of the AFE should be specified.
Crosstalk, which affects image accuracy, is another parameter to consider for ultrasound systems. The main crosstalk in ultrasound systems is caused by some transducer arrays that are arranged at -30 to -35dBc, depending on the spacing, frequency, design, materials, etc. of the transducer elements. Generally speaking, the crosstalk of ICs or PCBs is much lower than -35dBc. Therefore, circuit crosstalk will not degrade system performance.
Ultrasonic Analog Front End
To meet the above criteria, an ultrasound AFE such as TI's AFE5805 is an ideal choice. Best-in-class BiCMOS and CMOS technologies are used to optimize power consumption and noise performance. The BiCMOS process is the best choice for the VCA portion of the AFE5805 because of its low power consumption, small chip size, and low flicker noise. The CMOS process is well suited for analog-to-digital converters. These innovative combinations can reduce size by 50%, reduce power consumption by 20%, and reduce noise by 40% compared to similar solutions. The constant noise performance shown in Figure 2 covers the entire operating frequency range. This allows the design of portable ultrasound systems to achieve higher image quality with minimal power consumption.
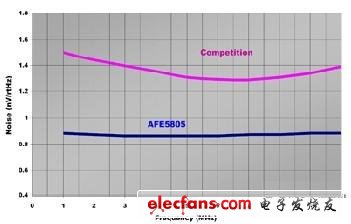
Figure 2: Excellent noise performance
Summarize
In the next few years, the demand for portable, low-cost ultrasound equipment is expected to grow rapidly in all regions of the world. For ultrasound equipment manufacturers, opportunities and challenges coexist. The advanced technology of the new ultrasound analog front end allows ultrasound equipment manufacturers to adjust the performance to suit various system sizes. Based on a single design, manufacturers can release multiple products, greatly saving the development cost and time of portable devices and high-channel density mid-range ultrasound systems.
Previous article:Design of motor protection device based on CAN bus
Next article:How to display 8 digits in decimal on a seven segment display?
- Popular Resources
- Popular amplifiers
-
Digital Ultrasound Imaging Principles and Architecture System Design
-
A Reconfigurable Ultrasound Transceiver ASIC With24×40Elements for 3-D Carotid Artery Imaging
-
An Element-Matched ElectromechanicalΔΣADC for Ultrasound Imaging
-
Design of Digital B-mode Ultrasound Keyboard Based on Single Chip Microcomputer
- Huawei's Strategic Department Director Gai Gang: The cumulative installed base of open source Euler operating system exceeds 10 million sets
- Analysis of the application of several common contact parts in high-voltage connectors of new energy vehicles
- Wiring harness durability test and contact voltage drop test method
- Sn-doped CuO nanostructure-based ethanol gas sensor for real-time drunk driving detection in vehicles
- Design considerations for automotive battery wiring harness
- Do you know all the various motors commonly used in automotive electronics?
- What are the functions of the Internet of Vehicles? What are the uses and benefits of the Internet of Vehicles?
- Power Inverter - A critical safety system for electric vehicles
- Analysis of the information security mechanism of AUTOSAR, the automotive embedded software framework
Professor at Beihang University, dedicated to promoting microcontrollers and embedded systems for over 20 years.
- Innolux's intelligent steer-by-wire solution makes cars smarter and safer
- 8051 MCU - Parity Check
- How to efficiently balance the sensitivity of tactile sensing interfaces
- What should I do if the servo motor shakes? What causes the servo motor to shake quickly?
- 【Brushless Motor】Analysis of three-phase BLDC motor and sharing of two popular development boards
- Midea Industrial Technology's subsidiaries Clou Electronics and Hekang New Energy jointly appeared at the Munich Battery Energy Storage Exhibition and Solar Energy Exhibition
- Guoxin Sichen | Application of ferroelectric memory PB85RS2MC in power battery management, with a capacity of 2M
- Analysis of common faults of frequency converter
- In a head-on competition with Qualcomm, what kind of cockpit products has Intel come up with?
- Dalian Rongke's all-vanadium liquid flow battery energy storage equipment industrialization project has entered the sprint stage before production
- Allegro MicroSystems Introduces Advanced Magnetic and Inductive Position Sensing Solutions at Electronica 2024
- Car key in the left hand, liveness detection radar in the right hand, UWB is imperative for cars!
- After a decade of rapid development, domestic CIS has entered the market
- Aegis Dagger Battery + Thor EM-i Super Hybrid, Geely New Energy has thrown out two "king bombs"
- A brief discussion on functional safety - fault, error, and failure
- In the smart car 2.0 cycle, these core industry chains are facing major opportunities!
- The United States and Japan are developing new batteries. CATL faces challenges? How should China's new energy battery industry respond?
- Murata launches high-precision 6-axis inertial sensor for automobiles
- Ford patents pre-charge alarm to help save costs and respond to emergencies
- New real-time microcontroller system from Texas Instruments enables smarter processing in automotive and industrial applications
- [MM32 eMiniBoard Review] Part 2: Environment Construction and Program Burning
- Principles of Automatic Control (Shiqun)
- The impact of water depth on power supply and communications.
- MSP430G2755 Main Memory Bootloader UART Porting Guide
- A simple temperature control circuit to help you understand the circuit diagram
- 【CH579M-R1】3. ADC internal temperature measurement, external channel and touch button test
- How to migrate from GCC Linker to SEGGER Linker in Embedded Studio?
- Based on PSOC6 development board simulation I2C solution X-NUCLEO-IKS01A3 LPS22HH
- 【CH579M-R1】+OTA first experience
- Xunwei i.MX6ULL Terminator to view the real-time value of variables