Electronics continue to move toward lower supply voltages and higher load currents, which puts tremendous pressure on point-of-load DC/DC converters to maintain rapid performance improvements. For example, lower supply voltages mean that regulators must support higher step-down ratios for 12V or 24V rails while maintaining high efficiency. Regulation accuracy also becomes more important as supply voltages decrease, and accuracy must be maintained in the presence of parasitic IR drops and dynamic load transients. EMI generated by switching converters is also a concern, especially in RF applications.
Some applications require their power supplies to meet all of these stringent requirements: high power, high efficiency, high accuracy, high step-down ratio, fast transient performance and low EMI, all in a small footprint. The LTC®3833 is a high performance synchronous step-down DC/DC controller that meets this challenge. Figure 1 shows a typical application. The LTC3833 accepts an unregulated input voltage between 4.5V and 38V (40V absolute maximum) and down-converts it to a 0.67% accurate output voltage between 0.6V and 5.5V (6V absolute maximum).
Figure 1. 28V input, 2.5V output, 5A, 1.2MHz step-down converter. The high frequency capability of the LTC3833 enables designs to be squeezed into tight spaces.
It features a 20ns minimum on-time for high step-down ratios (high V to low V), and its control architecture provides for fast transient performance. The LTC3833 is available in a 20-lead QFN (3mm × 4mm) package and a TSSOP with exposed pad for enhanced thermal performance.
Fast transient performance and constant frequency
The LTC3833 uses a new, sophisticated controlled on-time architecture - a variation of the constant on-time control architecture, except that the on-time is controlled so that the switching frequency remains constant under steady-state conditions at line and load. This architecture takes advantage of all the benefits of a constant on-time controller, namely fast transient response and small on-time for high step-down ratios, while mimicking the behavior of a constant frequency controller.
The LTC3833 responds immediately to a load step without waiting until the next switching cycle like traditional constant frequency controllers. During a load step, the LTC3833 increases its switching frequency to speed response and reduce the droop on the output. Similarly, during load release, the LTC3833 reduces the switching frequency to prevent the input rail from further charging the output capacitor. Once the transient condition subsides, the LTC3833 returns the switching frequency to the nominal programmed value, or to the external clock frequency if synchronizing.
The LTC3833’s low 90ns minimum off-time allows high duty cycle operation, avoiding V switching only slightly above the required V. The low minimum off-time also factors into fast transient performance. If the switching converter’s control loop is designed for high bandwidth and high speed, the LTC3833’s minimum off-time will not limit performance. That is, under load step conditions, the time between consecutive on-time pulses can be as low as 90ns for high bandwidth designs.
Figure 2 shows a typical low voltage, high current application for a microprocessor power supply, where the LTC3833 quickly responds to a 20A load step and releases.
Figure 2a. 14V input, 1.5V output, 20A, 300kHz step-down converter. The LTC3833 excels in low voltage, high current applications such as those typical of microprocessor power supplies. It can quickly respond to sudden high swing current requirements of the microprocessor.
Figure 2b. The LTC3833 can quickly respond to sudden high switching current demands.
Wide frequency range for a variety of applications
The LTC3833 is capable of a full decade of switching frequencies from 200kHz to 2MHz (programmed with an external resistor on the RT pin). This wide range enables the LTC3833 to meet the requirements of a wide range of applications, from low frequencies requiring high efficiency to high frequencies requiring a small solution size to 2MHz applications that stay above the AM radio band while being able to downconvert from a high input rail and deliver high output current.
The choice of operating frequency is a trade-off between efficiency and component size. The lower the frequency, the higher the efficiency due to the reduction of switching-related losses in the converter. On the other hand, lower frequencies require larger inductors and capacitors to achieve a given output ripple. At higher frequencies, smaller components can be used to achieve the same output ripple, but at the expense of efficiency. Table 1 shows the trade-off between efficiency and inductor size required to maintain output ripple when the LTC3833 is used to generate a 1.8V output at multiple frequencies and input voltages. As can be seen in the table, switching losses are exacerbated at higher frequencies and higher V, mainly due to the higher V across the high-side MOSFET.
Efficiency↘Frequency, Inductance
200kHz, 2.00μH500kHz, 0.82μH1MHz, 0.47μH2MHz, 0.20μH
Vin
6V91%92%91%87%
22592%92%89%84%
25592%91%87%81%
24V91%88%83%73%
The wide frequency range of the LTC3833 also helps minimize EMI interference from the switching regulator. The switching frequency can be selected and maintained across the line and load so that the regulator’s operating frequency and harmonics fall outside the frequency band of the end application. This allows the end application to easily filter out the switching noise of the DC/DC converter. Figure 3 shows an example of a 5.5V application operating in the AM radio band (fSW > 1800kHz) that can be used to power electronics in an automotive infotainment system.
Figure 3. 14V input, 5.5V output, 4A, 2MHz step-down converter. The LTC3833 can operate at a switching frequency above the AM radio band (f > 1.8MHz), allowing the AM radio to adequately filter the switching noise and EMI from the step-down converter.
The LTC3833 provides additional protection against EMI and noise interference by allowing it to be synchronized to an external clock applied to the MODE/PLLIN pin. This allows the end application to control the switching cycle and timing of the DC/DC converter so that no interference occurs during critical time periods where sensitive signal processing may occur in the application.
High step-down ratio at high frequencies
The LTC3833 supports high-side MOSFET on-times as low as 20ns. This is important because lower minimum on-times translate into higher possible step-down ratios (Vin to Vout) at a given switching frequency. Higher switching frequencies require shorter on-times to achieve the same step-down ratio. Although the LTC3833’s minimum on-time is a function of Vin/5out and switching frequency, it scales in the right direction—with lowest minimum on-times at high Vin to low Vout at high frequencies.
Of course, high V. In high frequency applications, they are susceptible to minimum on-time limitations. Consider the application in Figure 1, which needs to convert 28V down to 2.5V at 1.2MHz. This requires an on-time of approximately 74ns, which the LTC3833 easily achieves. In contrast, most traditional current mode controllers cannot achieve a 74ns on-time. To operate at high frequencies, traditional current mode controllers require two stages of DC/DC conversion, with the first stage converting down to an intermediate voltage rail (e.g., 12V) and the second stage converting to the final desired voltage. This effectively doubles the solution size and reduces overall efficiency.
At very low on-times (20ns–60ns), the switching delay of the power MOSFET itself limits the minimum achievable on-time. Due care must be taken to select power MOSFETs with low turn-on and turn-off delays and, more importantly, little imbalance between their turn-on and turn-off delays. For example, the turn-off delay of most power MOSFETs is approximately 30ns greater than their turn-on delay. This difference directly increases the 20ns minimum on-time of the LTC3833, resulting in an effective minimum on-time of approximately 50ns. Figure 4 shows a high step-down ratio application operating at 2MHz, where there is an imbalance of approximately 12ns between the turn-on and turn-off delays of the high-side power MOSFET.
Figure 4. 24V input, 1.8V output, 15A, 2MHz step-down converter. The LTC3833 achieves very low on-times, enabling a single-stage converter design. Using a traditional controller with a longer minimum on-time would require two or more stages, meaning a more expensive, larger and less efficient design.
High precision, minimal effort
The LTC3833 features true remote differential output sensing. This enables precise regulation of the outputs even in high power distributed systems with high load currents and shared ground planes. Remote differential sensing is critical for low output voltages where small offsets caused by parasitic IR drops in board traces can lose several percentage points of regulation accuracy.
Remote differential output sensing combined with an accurate internal reference gives the LTC3833 excellent output regulation accuracy over line, load and temperature, even in the presence of offsets caused by trace losses on the PC board. The LTC3833 is able to achieve output accuracy values of ±0.25% at 25°C, ±0.67% from 0°C to 85°C, and ±1% from –40°C to 125°C. Total accuracy accounting for line, load and remote ground variations is ±1% from 0°C to 85°C and ±1.5% from –40°C to 125°C. Figure 5 shows the typical regulation accuracy of the LTC3833 over line, load and temperature.
Figure 5. Typical regulation accuracy of the LTC3833 over line, load and temperature.
The traditional remote differential output sensing scheme involves a unity-gain differential amplifier that directly senses the remote output and remote ground terminals (Figure 6). The output of the amplifier is then scaled down by an external resistor divider (which also programs the output voltage) and fed back to the core controller. In addition to the additional design effort involved in this scheme, the input and/or output common-mode range limitations of the unity-gain amplifier also reduce the output voltage range over which remote differential sensing can be used.
Previous article:How charge pumps implement the technique of increasing or inverting DC voltage
Next article:How to Design a Synchronous Buck Regulator Using SY8003
Recommended ReadingLatest update time:2024-11-15 14:22
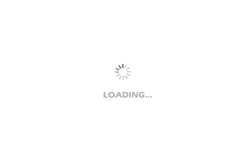
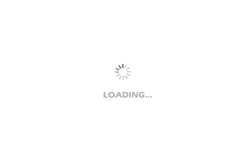
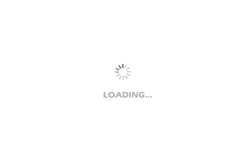
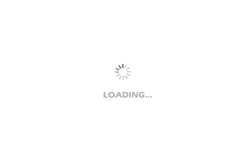
- Popular Resources
- Popular amplifiers
-
西门子S7-12001500 PLC SCL语言编程从入门到精通 (北岛李工)
-
New Energy Vehicle Detection and Diagnosis Experiment (Edited by Mao Caiyun, Zhou Xien, and Long Jiwen)
-
Virtualization Technology Practice Guide - High-efficiency and low-cost solutions for small and medium-sized enterprises (Wang Chunhai)
-
ESP32-S3 source code
- Sn-doped CuO nanostructure-based ethanol gas sensor for real-time drunk driving detection in vehicles
- Design considerations for automotive battery wiring harness
- Do you know all the various motors commonly used in automotive electronics?
- What are the functions of the Internet of Vehicles? What are the uses and benefits of the Internet of Vehicles?
- Power Inverter - A critical safety system for electric vehicles
- Analysis of the information security mechanism of AUTOSAR, the automotive embedded software framework
- Brief Analysis of Automotive Ethernet Test Content and Test Methods
- How haptic technology can enhance driving safety
- Let’s talk about the “Three Musketeers” of radar in autonomous driving
Professor at Beihang University, dedicated to promoting microcontrollers and embedded systems for over 20 years.
- LED chemical incompatibility test to see which chemicals LEDs can be used with
- Application of ARM9 hardware coprocessor on WinCE embedded motherboard
- What are the key points for selecting rotor flowmeter?
- LM317 high power charger circuit
- A brief analysis of Embest's application and development of embedded medical devices
- Single-phase RC protection circuit
- stm32 PVD programmable voltage monitor
- Introduction and measurement of edge trigger and level trigger of 51 single chip microcomputer
- Improved design of Linux system software shell protection technology
- What to do if the ABB robot protection device stops
- Sn-doped CuO nanostructure-based ethanol gas sensor for real-time drunk driving detection in vehicles
- Design considerations for automotive battery wiring harness
- Do you know all the various motors commonly used in automotive electronics?
- What are the functions of the Internet of Vehicles? What are the uses and benefits of the Internet of Vehicles?
- Power Inverter - A critical safety system for electric vehicles
- Analysis of the information security mechanism of AUTOSAR, the automotive embedded software framework
- Brief Analysis of Automotive Ethernet Test Content and Test Methods
- How haptic technology can enhance driving safety
- Let’s talk about the “Three Musketeers” of radar in autonomous driving
- Why software-defined vehicles transform cars from tools into living spaces
- Introduction to the method of board-level online compilation and downloading of C6000 DSP code
- Cadence Circuit Design Case Analysis
- Could you please tell me which manufacturers produce magnetic resistance switches? I only found one.
- Field Effect Transistor Basics and Application Practice
- Verilog Golden Reference Guide Chinese version.pdf
- [ART-Pi Evaluation] V: ATT-Pi WiFi networking and MQTT publishing and subscription evaluation in RTT Studio environment
- A chart to understand China Telecom's "5G SA Deployment Guide"
- Art on Silicon (3)
- MSP430F5529 multi-channel PWM output control servo and motor
- Discrete Difference Amplifiers vs. Integrated Solutions