6. Label input and output
Convenient maintenance PLC controls a complex system. What you can see are two rows of staggered input and output relay terminals, corresponding indicator lights and PLC numbers, just like an integrated circuit with dozens of pins. Anyone who does not look at the schematic diagram to repair the faulty equipment will be helpless and the speed of finding the fault will be very slow. In view of this situation, we draw a table based on the electrical schematic diagram and stick it on the console or control cabinet of the equipment, marking the electrical symbols and Chinese names corresponding to each PLC input and output terminal number, which is similar to the functional description of each pin of the integrated circuit.
With this input and output table, electricians who understand the operation process or are familiar with the ladder diagram of this equipment can start maintenance.
But for those electricians who are not familiar with the operation process and cannot read ladder diagrams, they need to draw another table: PLC input and output logic function table. This table actually explains the logical correspondence between the input circuit (trigger element, associated element) and the output circuit (actuator) in most operation processes.
Practice has proved that if you can skillfully use the input-output correspondence table and the input-output logic function table, you can easily repair electrical faults without drawings.
7. Infer faults through program logic
There are many types of PLCs commonly used in industry today. For low-end PLCs, the ladder diagram instructions are similar. For mid- to high-end machines, such as S7-300, many programs are written using language tables.
Practical ladder diagrams must have Chinese symbol annotations, otherwise it will be difficult to read. If you can have a general understanding of the equipment process or operation process before reading the ladder diagram, it will seem easier.
If an electrical fault analysis is to be performed, the reverse search method or reverse reasoning method is generally applied, that is, according to the input-output correspondence table, the corresponding PLC output relay is found from the fault point, and then the logical relationship that satisfies its action is reversed.
Experience shows that if one problem is found, the fault can be basically eliminated, because it is rare for two or more fault points to occur simultaneously in the equipment.
8. PLC self-fault judgment
Generally speaking, PLC is an extremely reliable device with a very low failure rate. The probability of damage to hardware such as PLC and CPU or software errors is almost zero. The PLC input point will hardly be damaged unless it is caused by strong electric intrusion. The normally open point of the PLC output relay will have a long contact life unless the peripheral load is short-circuited or the design is unreasonable, and the load current exceeds the rated range.
Therefore, when we look for electrical fault points, we should focus on the PLC's peripheral electrical components and not always suspect that there is a problem with the PLC hardware or program. This is very important for quickly repairing faulty equipment and resuming production.
Therefore, the electrical fault inspection and repair of the PLC control circuit discussed by the author does not focus on the PLC itself, but on the peripheral electrical components in the circuit controlled by the PLC.
9. Make full and reasonable use of software and hardware resources
(1) Instructions that do not participate in the control cycle or have been entered before the cycle do not need to be connected to the PLC;
(2) When multiple instructions control a task, they can be connected in parallel outside the PLC and then connected to an input point;
(3) Make full use of the PLC internal functional soft components and fully call the intermediate state to make the program complete and coherent and easy to develop. At the same time, it also reduces hardware investment and reduces costs;
(4) If conditions permit, it is best to make each output independent, which is convenient for control and inspection and also protects other output circuits; when an output point fails, it will only cause the corresponding output circuit to lose control;
(5) If the output is a forward/reverse controlled load, not only must the PLC internal program be interlocked, but measures must also be taken outside the PLC to prevent the load from moving in both directions;
(6) PLC emergency stop should be cut off using an external switch to ensure safety.
10. Other matters needing attention
(1) Do not connect the AC power cord to the input terminal to avoid burning the PLC;
(2) The grounding terminal should be grounded independently and not connected in series with the grounding terminal of other equipment. The cross-sectional area of the grounding wire should not be less than 2mm²;
(3) The auxiliary power supply is small and can only drive low-power devices (photoelectric sensors, etc.);
(4) Some PLCs have a certain number of occupied points (i.e. empty address terminals), do not connect the wires;
(5) When there is no protection in the PLC output circuit, a protective device such as a fuse should be connected in series in the external circuit to prevent damage caused by load short circuit.
Previous article:The structure and basic working principle of stepper motor
Next article:What are the main reasons for the axial movement of the motor rotor?
Recommended ReadingLatest update time:2024-11-16 09:53
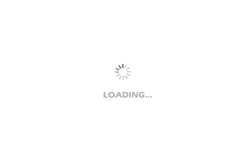
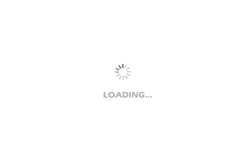
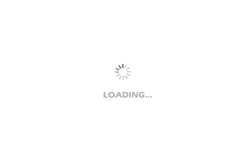
- Popular Resources
- Popular amplifiers
- Huawei's Strategic Department Director Gai Gang: The cumulative installed base of open source Euler operating system exceeds 10 million sets
- Analysis of the application of several common contact parts in high-voltage connectors of new energy vehicles
- Wiring harness durability test and contact voltage drop test method
- Sn-doped CuO nanostructure-based ethanol gas sensor for real-time drunk driving detection in vehicles
- Design considerations for automotive battery wiring harness
- Do you know all the various motors commonly used in automotive electronics?
- What are the functions of the Internet of Vehicles? What are the uses and benefits of the Internet of Vehicles?
- Power Inverter - A critical safety system for electric vehicles
- Analysis of the information security mechanism of AUTOSAR, the automotive embedded software framework
Professor at Beihang University, dedicated to promoting microcontrollers and embedded systems for over 20 years.
- Innolux's intelligent steer-by-wire solution makes cars smarter and safer
- 8051 MCU - Parity Check
- How to efficiently balance the sensitivity of tactile sensing interfaces
- What should I do if the servo motor shakes? What causes the servo motor to shake quickly?
- 【Brushless Motor】Analysis of three-phase BLDC motor and sharing of two popular development boards
- Midea Industrial Technology's subsidiaries Clou Electronics and Hekang New Energy jointly appeared at the Munich Battery Energy Storage Exhibition and Solar Energy Exhibition
- Guoxin Sichen | Application of ferroelectric memory PB85RS2MC in power battery management, with a capacity of 2M
- Analysis of common faults of frequency converter
- In a head-on competition with Qualcomm, what kind of cockpit products has Intel come up with?
- Dalian Rongke's all-vanadium liquid flow battery energy storage equipment industrialization project has entered the sprint stage before production
- Allegro MicroSystems Introduces Advanced Magnetic and Inductive Position Sensing Solutions at Electronica 2024
- Car key in the left hand, liveness detection radar in the right hand, UWB is imperative for cars!
- After a decade of rapid development, domestic CIS has entered the market
- Aegis Dagger Battery + Thor EM-i Super Hybrid, Geely New Energy has thrown out two "king bombs"
- A brief discussion on functional safety - fault, error, and failure
- In the smart car 2.0 cycle, these core industry chains are facing major opportunities!
- The United States and Japan are developing new batteries. CATL faces challenges? How should China's new energy battery industry respond?
- Murata launches high-precision 6-axis inertial sensor for automobiles
- Ford patents pre-charge alarm to help save costs and respond to emergencies
- New real-time microcontroller system from Texas Instruments enables smarter processing in automotive and industrial applications
- Pelvic floor muscle therapy instrument parameters technical parameters
- Design and Application of Power Monitoring System for Hubei Daguannan Expressway
- Analysis of installation techniques of magnetic flap level gauge for high liquid level tank
- SparkRoad Review (2) - Can I burn a Cortex-M0 soft core?
- GD32L233C rtos debut
- To become a high-level electronic engineer, in addition to programming and PCB drawing, please recommend other circuit design books. Thank you
- Disassembling a multi-turn potentiometer
- Mobile 5G device antenna tuning knowledge
- Last day: Apply for free evaluation, Bear Pi folding development board
- Those who are familiar with solar photovoltaic laminators, please come in!