2. Configure the S7-300 single-station system to use the CPU integrated PN port as a Client for Modbus TCP communication
The following takes the S7-300 single-station system and Modbus Slave software as an example to introduce in detail how to configure the integrated PN port of the S7-300 single-station system CPU as a Client and the Modbus Slave as a Server for Modbus TCP communication.
2.1 Hardware and Software
The hardware devices used in this example are as follows:
name | quantity | Order Number |
S7-300 power supply module PS 307 10A | 1 | 6ES7307-1KA02-0AA0 |
S7-300 CPU317-2PN/DP | 1 | 6ES7317-2EK14-0AB0(V3.2) |
Network cable | Several |
|
Laptop | 1 |
|
The software used is as follows:
name | Order Number |
STEP7 V16 Update3 configuration and programming software |
|
Modbus Slave License-free Version | Available free online |
2.2 S7-300 single station system and Modbus Slave software configuration
Open the TIA software, create a new project file, name it "PN_MODBUS TCP Client", and insert an S7-300 station under the project, as shown in Figure 1 below:
Figure 1 New S7-300 Station
Open the device view and modify the IP address of the CPU. In this example, set the PN port IP address of the CPU to 192.168.0.220, as shown in Figure 17 below:
Figure 2 Setting the CPU IP address in the device view
2.3 Configuring technology objects
①Select and add the technological object "Modbus" --- "Other" --- "MODBUS TCP" --- "MB_PN_PARAM"
Figure 3 Adding a new process object
②Set “Connection Settings”
Connection ID: Connection reference identifier (range 1~4095), which will be used when calling the command later
Connection establishment: PLC acts as MODBUS TCP client and selects active.
Remote IP address: The IP address in the figure (192.168.0.228) is the IP address of the laptop
Local Device ID: Select the device type of the PLC
Local port: As a client, you do not need to specify a fixed port
Partner port: Port 502 in the figure is the port number of Modbus Slave
Figure 4 Configuration technology object
③Modbus setting "Internal"
Figure 5 Configuration technology object
③Modbus setting "data area"
In the figure below, 4 Modbus data areas are set
Figure 6 Configuration technology object
2.4 Add data blocks according to the data areas created in the technology object
According to the data area set in step 3.3 of the process object, add four data blocks, as shown in the figure below
Figure 7 Creating a data block
Figure 8 Creating a data block to store MODBUS coil data
Figure 9 Creating a data block to store MODBUS digital input types
Figure 10 Creating a data block to store MODBUS holding register data
Figure 11 Creating a data block to store MODBUS input register data
2.5 Create a data block with registry keys that can be used for authorization
Create an authorization key data block DB3 (name REG_KEY), select the type as "Global DB", open the DB block, create a variable "REG_KEY", and set the data type to "String[17]", as shown in the figure:
Figure 12 Creating a data block to store the authorization code
For how to obtain the authorization key, refer to //www.ad.siemens.com.cn/productportal/Prods/published/Comm/Comm_9.4/Comm_9.4.html
2.6 Calling OB121
Because the "MODBUSPN" instruction is in an unauthorized state before obtaining the authorization key, the CPU will report an error and shut down. In order to read the "IDENT_CODE" code of the CPU, the CPU needs to be running, and the programming error organization block OB121 must be added, as shown in the following figure:
Figure 13 Calling OB121
2.7 Calling communication instructions
Call the MODBUS TCP instruction (Communication---Others---MODBUS_TCP---MODBUSPN) and fill in the parameters.
In order to find the cause when communication fails, program segment 2 is written to capture the error code.
Figure 14 Calling the "MODBUSPN" instruction
2.8 Initialization Instructions
Create a startup organization block OB100 (name COMPLETE RESTART), the language is "STL", open the OB block, and set the initialization bit input pin register, as shown in the figure:
Figure 15 Initialize the "MODBUSPN" instruction
2.9 Communication Test
Example 1: The client reads the server's [digital input], offset 3, length 2 data
Figure 16 Communication test example
Example 2: The client reads the server's [input register], offset 0, length 3 data
Figure 17 Communication test example
Example 3: The client reads the server's [coil register], offset 0, length 8 data
Figure 18 Communication test example
Example 4: The client reads the server's [holding register], offset 0, length 3 data
Figure 19 Communication test example
Example 5: The client writes data to the server [holding register], offset 5, length 5 data
Figure 20 Communication test example
Example 6: The client writes data to the server [coil register], offset 0, length 8 data
Figure 21 Communication test example
3. Configure the S7-300 single-station system to use the CPU integrated PN port as a server for Modbus TCP communication
The following takes the S7-300 single-station system and ModScan32 software as an example to introduce in detail how to configure the integrated PN port of the S7-300 single-station system CPU as a server and ModScan32 as a client for Modbus TCP communication.
3.1 Hardware and software used in the examples
The hardware devices used in this example are as follows:
name | quantity | Order Number |
S7-300 power supply module PS 307 10A | 1 | 6ES7307-1KA02-0AA0 |
S7-300 CPU317-2PN/DP | 1 | 6ES7317-2EK14-0AB0(V3.2) |
Network cable | Several |
|
Laptop | 1 |
|
The software used is as follows:
name | Order Number |
STEP7 V16 Update3 configuration and programming software |
|
ModScan32 License-free version | Available free online |
3.2 S7-300 single station system and ModScan32 software configuration
Open the TIA software, create a new project file, name it "PN_MODBUS TCP Server", and insert an S7-300 station under the project, as shown in the following figure:
Figure 22 Create a new S7-300 Station
Open the device view and modify the IP address of the CPU. In this example, set the PN port IP address of the CPU to 192.168.0.220, as shown in Figure 17 below:
Figure 23 Setting the CPU IP address in the device view
3.3 Configuring technology objects
① Add a new process object, select "Modbus"---"Other"---"MODBUS_TCP"---"MB_PN_PARAM"
Figure 24 Adding a new process object
②Set “Connection Settings”
Connection ID: Connection reference identifier (range 1~4095), which will be used when calling the command later
Connection establishment: PLC acts as MODBUS TCP server and selects passive.
Remote IP address: You can specify or not specify the IP address of the connection partner.
Local Device ID: Select the device type of the PLC
Local port: Specify a fixed port
Partner port: Not specified
Figure 25 Configuring technology objects
③Modbus setting "Internal"
Figure 26 Configuring technology objects
④Modbus Setting "Data Area"
In the figure below, 4 Modbus data areas are set
Figure 27 Configuring technology objects
3.4 Add data blocks according to the data areas created in the technology object
According to the data area set in step 3.3 of the process object, add four data blocks, as shown in the figure below
Figure 28 Creating a data block
Figure 29 Creating a data block to store MODBUS coil data
Figure 30 Creating a data block to store MODBUS digital input types
Figure 31 Creating a data block to store MODBUS holding register data
Figure 32 Creating a data block to store MODBUS input register data
3.5 Create a data block with registry keys that can be used for authorization
Create an authorization key data block DB3 (name REG_KEY), select the type as "Global DB", open the DB block, create a variable "REG_KEY", and set the data type to "String[17]", as shown in the figure:
Figure 33 Creating a data block to store the authorization code
For how to obtain the authorization key, refer to //www.ad.siemens.com.cn/productportal/Prods/published/Comm/Comm_9.4/Comm_9.4.html
3.6 Calling OB121
Because the "MODBUSPN" instruction is in an unauthorized state before obtaining the authorization key, the CPU will report an error and shut down. In order to read the "IDENT_CODE" code of the CPU, the CPU needs to be running, and the programming error organization block OB121 must be added, as shown in the following figure:
Figure 34 OB121
3.7 Calling communication instructions
Call the MODBUS TCP instruction (Communication---Others---MODBUS_TCP---MODBUSPN) and fill in the parameters.
In order to find the cause when communication fails, program segment 2 is written to capture the error code.
Figure 35 Calling the "MODBUSPN" instruction
3.8 Initialization Instructions
Create a startup organization block OB100 (name COMPLETE RESTART), the language is "STL", open the OB block, and set the initialization bit input pin register, as shown in the following figure:
Figure 36 Initialization "MODBUSPN" instruction
3.9 Establishing a connection with the client
Enable the server side and establish a connection using ModScan32 according to the following settings:
Figure 37 Establishing a connection with the client
3.9 Communication Test
Example 1: The client reads and writes the server [coil register], offset 0, length 10 data
Previous article:S7-200 PROFINET communication and SINAMICS library configuration and programming steps
Next article:For permanent magnet motors, what aspects are included in the processes required to complete motor manufacturing?
Recommended ReadingLatest update time:2024-11-16 09:24
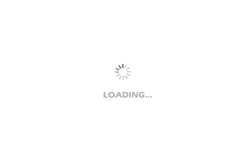
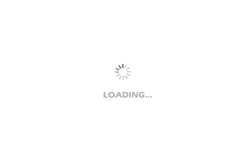
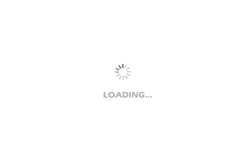
- Popular Resources
- Popular amplifiers
-
Network Operating System (Edited by Li Zhixi)
-
Introduction to Internet of Things Engineering 2nd Edition (Gongyi Wu)
-
Siemens PLC Programming Technology and Application Cases (Edited by Liu Zhenquan, Wang Hanzhi, Yang Kun, etc.)
-
Siemens PLC from Beginner to Mastery with Color Illustrations (Yang Rui)
- Huawei's Strategic Department Director Gai Gang: The cumulative installed base of open source Euler operating system exceeds 10 million sets
- Analysis of the application of several common contact parts in high-voltage connectors of new energy vehicles
- Wiring harness durability test and contact voltage drop test method
- Sn-doped CuO nanostructure-based ethanol gas sensor for real-time drunk driving detection in vehicles
- Design considerations for automotive battery wiring harness
- Do you know all the various motors commonly used in automotive electronics?
- What are the functions of the Internet of Vehicles? What are the uses and benefits of the Internet of Vehicles?
- Power Inverter - A critical safety system for electric vehicles
- Analysis of the information security mechanism of AUTOSAR, the automotive embedded software framework
Professor at Beihang University, dedicated to promoting microcontrollers and embedded systems for over 20 years.
- Innolux's intelligent steer-by-wire solution makes cars smarter and safer
- 8051 MCU - Parity Check
- How to efficiently balance the sensitivity of tactile sensing interfaces
- What should I do if the servo motor shakes? What causes the servo motor to shake quickly?
- 【Brushless Motor】Analysis of three-phase BLDC motor and sharing of two popular development boards
- Midea Industrial Technology's subsidiaries Clou Electronics and Hekang New Energy jointly appeared at the Munich Battery Energy Storage Exhibition and Solar Energy Exhibition
- Guoxin Sichen | Application of ferroelectric memory PB85RS2MC in power battery management, with a capacity of 2M
- Analysis of common faults of frequency converter
- In a head-on competition with Qualcomm, what kind of cockpit products has Intel come up with?
- Dalian Rongke's all-vanadium liquid flow battery energy storage equipment industrialization project has entered the sprint stage before production
- Allegro MicroSystems Introduces Advanced Magnetic and Inductive Position Sensing Solutions at Electronica 2024
- Car key in the left hand, liveness detection radar in the right hand, UWB is imperative for cars!
- After a decade of rapid development, domestic CIS has entered the market
- Aegis Dagger Battery + Thor EM-i Super Hybrid, Geely New Energy has thrown out two "king bombs"
- A brief discussion on functional safety - fault, error, and failure
- In the smart car 2.0 cycle, these core industry chains are facing major opportunities!
- The United States and Japan are developing new batteries. CATL faces challenges? How should China's new energy battery industry respond?
- Murata launches high-precision 6-axis inertial sensor for automobiles
- Ford patents pre-charge alarm to help save costs and respond to emergencies
- New real-time microcontroller system from Texas Instruments enables smarter processing in automotive and industrial applications