A DC motor is a continuous actuator that converts electrical energy into mechanical energy. A DC motor does this by producing a continuous angular rotation that can be used to rotate pumps, fans, compressors, wheels, etc.
As well as conventional rotary DC motors, linear motors are also available, which are capable of producing continuous bushing motion. There are basically three types of conventional electric motors available: AC type motors, DC type motors and stepper motors.
Typical small DC motor
AC motors are commonly used in high power single or multi-phase industrial applications where constant rotational torque and speed are required to control large loads such as fans or pumps.
In this tutorial we will only be looking at simple light duty DC motors and stepper motors which are used in many different types of electronics, position control, microprocessor, PIC and robotics type circuits.
The DC motor or DC motor, to give it its full title, is the most commonly used actuator for producing continuous motion and rotation whose speed can be easily controlled, making them suitable for use in applications where speed control, servo control, and/or positioning is required. A DC motor consists of two parts, the "stator" being the stationary part, and the "rotor" being the rotating part. The result is that there are basically three types of DC motors that can be used.
Brushed Motor – This type of motor creates a magnetic field in a wound rotor (the part that rotates) by passing current through a commutator and carbon brush assembly, hence the name “brushed”. The magnetic field in the stator (the stationary part) is created by using wound stator field windings or permanent magnets. Generally, brushed DC motors are cheap, small, and easy to control.
Brushless Motor – This type of motor creates a magnetic field in the rotor using permanent magnets attached to it, and commutation is achieved electronically. They are generally smaller and more expensive than conventional brushed type DC motors, as they use “Hall Effect” switches in the stator to create the required sequence of rotation of the stator magnetic field, but they have better torque/speed characteristics, are more efficient and last longer than equivalent brushed types.
Servo Motors – This type of motor is basically a brushed DC motor with some form of position feedback control connected to the rotor shaft. They are connected to and controlled by a PWM type controller and are mainly used in position control systems and radio controlled models.
Ordinary DC motors have almost linear characteristics, with their rotation speed depending on the applied DC voltage and their output torque depending on the current flowing through the motor windings. The rotation speed of any DC motor can vary from a few revolutions per minute (rpm) to thousands of revolutions per minute, making them suitable for electronic, automotive or robotic applications. By connecting them to a gearbox or gear train, their output speed can be reduced while the motor's high-speed torque output can be increased.
"Brushed" DC Motors A traditional brushed DC motor is basically made up of two parts, the stationary body of the motor is called the stator, and the rotation inside that creates the movement is called the rotor or "armature" of the DC motor.
The motor wound stator is an electromagnetic circuit consisting of electrical coils connected together in a circular shape to produce the desired north pole, south pole, then north pole, etc. type rotating stationary magnetic field system, unlike an AC motor. The stator magnetic field rotates continuously at an applied frequency. The current flowing in these field coils is called the motor field current.
These electromagnetic coils that form the stator field can be electrically connected together (compound) in series, in parallel, or both with the motor armature. A series-wound DC motor has its stator field windings connected in series with the armature. Similarly, a shunt-wound DC motor has its stator field windings connected in parallel with the armature as shown.
Series and parallel DC motors
The rotor or armature of a DC motor consists of current-carrying conductors connected at one end to electrically isolated copper segments called a commutator. The commutator allows electrical connection to an external power source through carbon brushes (hence the name "brushed" motor) as the armature rotates.
The magnetic field set up by the rotor attempts to align itself with the stationary stator magnetic field, causing the rotor to rotate along its axis, but it is unable to align itself due to commutation delays. The speed of the motor depends on the strength of the rotor magnetic field, and the greater the voltage applied to the motor, the faster the rotor spins. By varying the applied DC voltage, the speed of the motor can also be varied.
Conventional (brush) DC motor
Permanent magnet (PMDC) brushed DC motors are typically much smaller and less expensive than their equivalent wound stator DC motor cousins because they have no field windings. In a PMDC motor, these field coils are replaced by strong rare earth (e.g., Cobolt or NdFeB) magnets with very high magnetic field energy.
The use of permanent magnets gives the DC motor a much better linear speed/torque characteristic than an equivalent wound-rotor motor because of the permanent (sometimes very strong) magnetic field, making it more suitable for use in models, robotics, and servo systems.
Although brushed DC motors are very efficient and cheap, the problem associated with brushed DC motors is that under heavy load conditions, sparks are generated between the two surfaces of the commutator and the carbon brushes, resulting in self-heating, short life, and electrical noise due to sparks, which can damage any semiconductor switching device such as a MOSFET or transistor. To overcome these disadvantages, brushless DC motors were developed.
"Brushless" DC Motors A brushless DC motor (BDCM) is very similar to a permanent magnet DC motor, but does not have any brushes to replace or wear out due to commutator sparking. Therefore, very little heat is generated in the rotor, extending the life of the motor. Brushless motor designs eliminate the need for brushes by using more complex drive circuits, as the rotor field is a permanent magnet that always stays in sync with the stator field, allowing for more precise speed and torque control.
The brushless DC motor is then constructed very similarly to an AC motor, making it a true synchronous motor, but with the disadvantage that it is more expensive than an equivalent "brushed" motor design.
The control of a brushless DC motor is quite different from the control methods of a normal brushed DC motor, because it is combined with some brushed DC motor control methods to detect the rotor angular position (or magnetic pole) required to produce the feedback signal required to control the semiconductor switching device. The most common position/pole sensor is the "Hall Effect Sensor", but some motors also use optical sensors.
Using a Hall Effect sensor, the polarity of the electromagnet is switched by the motor control drive circuit. The motor can then be easily synchronized with a digital clock signal, providing precise speed control. Brushless DC motors can be constructed with either an external permanent magnet rotor and an internal electromagnetic stator, or an internal permanent magnet rotor and an external electromagnetic stator.
The advantages of brushless DC motors over their "brushed" cousins are higher efficiency, improved reliability, lower electrical noise, good speed control, and more importantly, the absence of brushes or commutators which results in higher rotational speeds. Their disadvantages, however, are that they are more expensive and more complex to control.
DC servo motors are used in closed loop type applications to feed back the position of the output motor shaft to the motor control circuitry. Typical position "feedback" devices include resolvers, encoders and potentiometers used in radio controlled models (such as aircraft and boats, etc.).
Servo motors usually include a built-in gearbox for speed reduction and are able to directly transmit high torque. Due to the installation of the gearbox and feedback device, the output shaft of the servo motor cannot rotate freely like the shaft of a DC motor.
DC servo motor block diagram
A servo motor consists of a DC motor, a reduction gearbox, a position feedback device, and some form of error correction. The speed or position is controlled relative to a position input signal or reference signal applied to the device.
RC Servo Motor
The error detection amplifier looks at this input signal and compares it to the feedback signal from the motor output shaft to determine if the motor output shaft is in an error state, and if so, the controller makes the appropriate corrections to speed the motor up or slow it down. This response to the position feedback device means that the servo motor is operating within a "closed loop system."
In addition to large industrial applications, servo motors are also used in small remote control models and robotics. Most servo motors can rotate approximately 180 degrees in both directions, making them ideal for precise angular positioning. However, unless specifically modified, these RC-type servos cannot rotate continuously at high speeds like traditional DC motors.
Servo motors consist of multiple devices in one unit, a motor, a gearbox, a feedback device, and error correction for controlling position, direction, or speed. They are easily controlled using only three wires: power, ground, and signal control, so they are widely used in robots and small models.
DC Motor Switching and Control Small DC motors can be switched "on" or "off" by means of switches, relays, transistors or MOSFET circuits. The simplest form of motor control is "linear" control. This type of circuit uses bipolar transistors as switches (or Darlington transistors if higher current ratings are desired) to control the motor from a single power supply.
Previous article:Detailed explanation of the three major control points of servo, stepper and frequency conversion
Next article:PLC control of robot interference area and interlock signal control
Recommended ReadingLatest update time:2024-11-16 09:17
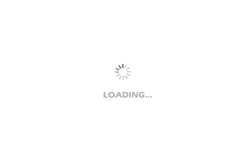
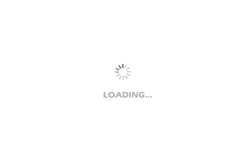
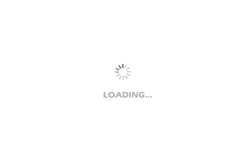
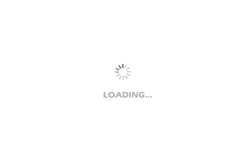
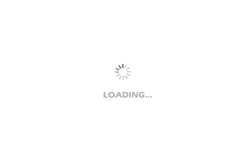
- Popular Resources
- Popular amplifiers
-
西门子S7-12001500 PLC SCL语言编程从入门到精通 (北岛李工)
-
New Energy Vehicle Detection and Diagnosis Experiment (Edited by Mao Caiyun, Zhou Xien, and Long Jiwen)
-
Virtualization Technology Practice Guide - High-efficiency and low-cost solutions for small and medium-sized enterprises (Wang Chunhai)
-
ESP32-S3 source code
- Huawei's Strategic Department Director Gai Gang: The cumulative installed base of open source Euler operating system exceeds 10 million sets
- Analysis of the application of several common contact parts in high-voltage connectors of new energy vehicles
- Wiring harness durability test and contact voltage drop test method
- Sn-doped CuO nanostructure-based ethanol gas sensor for real-time drunk driving detection in vehicles
- Design considerations for automotive battery wiring harness
- Do you know all the various motors commonly used in automotive electronics?
- What are the functions of the Internet of Vehicles? What are the uses and benefits of the Internet of Vehicles?
- Power Inverter - A critical safety system for electric vehicles
- Analysis of the information security mechanism of AUTOSAR, the automotive embedded software framework
Professor at Beihang University, dedicated to promoting microcontrollers and embedded systems for over 20 years.
- Innolux's intelligent steer-by-wire solution makes cars smarter and safer
- 8051 MCU - Parity Check
- How to efficiently balance the sensitivity of tactile sensing interfaces
- What should I do if the servo motor shakes? What causes the servo motor to shake quickly?
- 【Brushless Motor】Analysis of three-phase BLDC motor and sharing of two popular development boards
- Midea Industrial Technology's subsidiaries Clou Electronics and Hekang New Energy jointly appeared at the Munich Battery Energy Storage Exhibition and Solar Energy Exhibition
- Guoxin Sichen | Application of ferroelectric memory PB85RS2MC in power battery management, with a capacity of 2M
- Analysis of common faults of frequency converter
- In a head-on competition with Qualcomm, what kind of cockpit products has Intel come up with?
- Dalian Rongke's all-vanadium liquid flow battery energy storage equipment industrialization project has entered the sprint stage before production
- Allegro MicroSystems Introduces Advanced Magnetic and Inductive Position Sensing Solutions at Electronica 2024
- Car key in the left hand, liveness detection radar in the right hand, UWB is imperative for cars!
- After a decade of rapid development, domestic CIS has entered the market
- Aegis Dagger Battery + Thor EM-i Super Hybrid, Geely New Energy has thrown out two "king bombs"
- A brief discussion on functional safety - fault, error, and failure
- In the smart car 2.0 cycle, these core industry chains are facing major opportunities!
- The United States and Japan are developing new batteries. CATL faces challenges? How should China's new energy battery industry respond?
- Murata launches high-precision 6-axis inertial sensor for automobiles
- Ford patents pre-charge alarm to help save costs and respond to emergencies
- New real-time microcontroller system from Texas Instruments enables smarter processing in automotive and industrial applications
- Does anyone know about ST's new MPU? The model is STM32MP157A
- BlueNRG-x Documentation - Free Development Compiler Tool
- Guihang Shares Huayang Electric Co., Ltd. recruits embedded software and hardware engineers
- Participate in offline forum activities and give a speech on the evolution of semiconductor 5G testing
- [Zero-knowledge ESP8266 Tutorial] Quick Start 10-Dimming with PWM
- RISC-V SoC FPGA architecture brings real-time performance to Linux
- Download address of Guo Tianxiang's video tutorial on learning C51 microcontroller in ten days, which is recognized as the best in China
- The 1965 Tektronix oscilloscope TYPE453 takes you back to the distant past
- A filter to suppress broadcasts shared with forum friends
- Analysis of Simple Voltage-stabilized DC Power Supply Circuit