Programmable logic controller is a digital operation electronic system designed for use in industrial environments. It uses a programmable memory to store instructions for performing logic operations, sequential control, timing, counting and arithmetic operations, and controls various types of mechanical equipment or production processes through digital or analog input and output.
The input unit is the input interface between the PLC and the controlled device. It is the bridge for signals to enter the PLC. Its function is to receive signals from the main command element and the detection element. The input types include DC input, AC input, and AC/DC input.
The output unit is the connecting component between the PLC and the controlled device. Its function is to transmit the output signal of the PLC to the controlled device, that is, to convert the weak current signal sent by the central processor into a level signal to drive the actuator of the controlled device.
PLC output types are generally divided into the following three types:
1. Digital Output (DO): Digital output is usually a digital signal or binary signal, such as on/off or high/low, etc. It usually controls external devices such as motors, solenoid valves, etc. through relays or semiconductor switches.
2. Analog output (AO): Analog output is usually used to control devices that require continuous control, such as temperature, pressure, flow, etc. They usually use a current loop or a voltage loop to control the device, such as using a 4-20mA or 0-10V signal.
3. Pulse Output (PO): Pulse outputs are often used to count or measure position or speed in applications. They can provide a fixed digital pulse, such as a sensor signal, or obtain a different number of pulses through an encoder, thereby more accurately controlling the position and speed of the device.
The difference between PLC inputs and outputs lies in their function and how they are connected.
PLC input is to input the signals generated by external devices such as sensors and switches into the PLC so that the PLC can perform logical control. The most common input devices include digital input and analog input.
Digital inputs transmit information in the form of binary signals, usually representing the state of a signal generated by a switching device such as a switch, button, sensor, etc. Digital inputs are often connected via normally closed and normally open contacts.
Analog inputs are used to transmit continuous signals, such as temperature, pressure, flow sensors, etc. They usually output in the form of 0-10V, 4-20mA, etc. for PLC control.
PLC output is to transmit the control signal of PLC to the execution device to realize the control function. The most common output devices include digital output and analog output.
Digital outputs usually transmit information in the form of binary signals, such as switching devices such as solenoid valves, relays, lights, etc. Digital outputs are also usually connected via normally closed contacts and normally open contacts.
The signal continuity transmitted by analog output is usually used to control the continuity parameters of the actuator, such as the speed of the motor, the opening of the valve, etc. Analog output is usually connected in the form of PWM, 4-20mA, etc.
In general, the functions and connection methods of PLC inputs and outputs are very different. Inputs transmit signals to the PLC for its control, while outputs transmit the PLC's control signals to the actuators to realize the control functions.
Previous article:Working principle and wiring method of PLC input and output terminals
Next article:What are the characteristics and working methods of PLC
Recommended ReadingLatest update time:2024-11-16 09:46
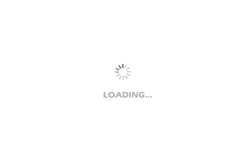
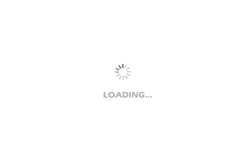
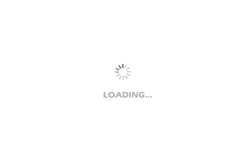
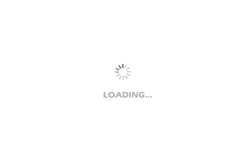
- Popular Resources
- Popular amplifiers
- Huawei's Strategic Department Director Gai Gang: The cumulative installed base of open source Euler operating system exceeds 10 million sets
- Analysis of the application of several common contact parts in high-voltage connectors of new energy vehicles
- Wiring harness durability test and contact voltage drop test method
- Sn-doped CuO nanostructure-based ethanol gas sensor for real-time drunk driving detection in vehicles
- Design considerations for automotive battery wiring harness
- Do you know all the various motors commonly used in automotive electronics?
- What are the functions of the Internet of Vehicles? What are the uses and benefits of the Internet of Vehicles?
- Power Inverter - A critical safety system for electric vehicles
- Analysis of the information security mechanism of AUTOSAR, the automotive embedded software framework
Professor at Beihang University, dedicated to promoting microcontrollers and embedded systems for over 20 years.
- Innolux's intelligent steer-by-wire solution makes cars smarter and safer
- 8051 MCU - Parity Check
- How to efficiently balance the sensitivity of tactile sensing interfaces
- What should I do if the servo motor shakes? What causes the servo motor to shake quickly?
- 【Brushless Motor】Analysis of three-phase BLDC motor and sharing of two popular development boards
- Midea Industrial Technology's subsidiaries Clou Electronics and Hekang New Energy jointly appeared at the Munich Battery Energy Storage Exhibition and Solar Energy Exhibition
- Guoxin Sichen | Application of ferroelectric memory PB85RS2MC in power battery management, with a capacity of 2M
- Analysis of common faults of frequency converter
- In a head-on competition with Qualcomm, what kind of cockpit products has Intel come up with?
- Dalian Rongke's all-vanadium liquid flow battery energy storage equipment industrialization project has entered the sprint stage before production
- Allegro MicroSystems Introduces Advanced Magnetic and Inductive Position Sensing Solutions at Electronica 2024
- Car key in the left hand, liveness detection radar in the right hand, UWB is imperative for cars!
- After a decade of rapid development, domestic CIS has entered the market
- Aegis Dagger Battery + Thor EM-i Super Hybrid, Geely New Energy has thrown out two "king bombs"
- A brief discussion on functional safety - fault, error, and failure
- In the smart car 2.0 cycle, these core industry chains are facing major opportunities!
- The United States and Japan are developing new batteries. CATL faces challenges? How should China's new energy battery industry respond?
- Murata launches high-precision 6-axis inertial sensor for automobiles
- Ford patents pre-charge alarm to help save costs and respond to emergencies
- New real-time microcontroller system from Texas Instruments enables smarter processing in automotive and industrial applications
- Using ir2110 driver to make a buck circuit
- Methods for solving faults in FPGA design and development based on EDA simulation technology.pdf
- Tuya Sandwich Wi-Fi & BLE SoC NANO Main Control Board WBRU+ Simple Development (Zero Code Solution)
- Super brain-burning question, about electric fishing? !
- There are a lot of questions recently, please don't mind.
- [SC8905 EVM Review] Upgrading and troubleshooting the use of I2Ctool on Nanxin power board
- Electromagnetism and quantum mechanics
- ST NUCLEO-L452RE Development Board Introduction
- Linux Command Detailed Dictionary
- ARM register analysis and exception handling methods