PLC input/output (I/O) refers to the circuits that a PLC system uses to connect input and output devices. Input refers to the signals received by the PLC, such as changes in state or signals detected by a sensor or switch, while output refers to the signals that the PLC outputs to the devices it controls, such as control signals for motors or relays. Typically, a PLC's I/O modules have multiple channels and can connect multiple input or output devices at the same time. This allows the PLC to control multiple devices and receive multiple input signals at the same time. I/O modules are usually programmable, meaning they can be configured in the PLC program to provide the desired inputs and outputs.
The input and output design of PLC (Programmable Logic Controller) adopts circuit isolation and signal conversion technologies, which can realize precise control of various field devices. The principle is as follows:
1. Input port principle:
When a sensor or switch is triggered, it will output an electrical signal. The input port of the PLC will isolate the signal and convert it into a digital signal, and transmit the signal to the CPU through the internal circuit.
2. Output port principle:
The output port of the PLC converts the digital signal into an electrical signal. The electrical signal drives a relay or another output device in the output port to control the field device.
In short, the PLC input port inputs the electrical signal of the field equipment into the digital circuit of the control system, and performs logical operations and judgments. The judgment results are sent to the output port, and then converted into electrical signals and output to the actual equipment for control and operation.
PLC input and output signals are mainly divided into three types:
1. Digital signal: Digital signal is a binary signal with only two states, "1" and "0". PLC collects and outputs digital signals through digital input and output modules.
2. Analog signal: Analog signal is a continuously changing signal that can take any value. Physical quantities such as temperature, pressure, flow rate, etc. are analog signals. PLC needs to collect and output analog signals through analog input and output modules.
3. Special signals: Special signals refer to other signal types except digital signals and analog signals, such as encoder signals, pulse signals, communication signals, etc. PLC can collect and output special signals through special modules.
The wiring method of the PLC input and output depends on the PLC model and application scenario. Generally speaking, the common PLC input methods are as follows:
1. DC input: usually use 2 or 3 wire input. 2-wire input requires connecting the negative pole of the power supply to the input terminal, and 3-wire input requires connecting the positive and negative poles of the power supply to the input terminal.
2. AC input: The input end generally has two wires, and you need to pay attention to whether the input voltage is consistent with the rated input voltage of the PLC.
3. Optocoupler input: The input end is a photocoupler, which can use external voltage as the input signal, which is safe and reliable.
There are also many types of PLC outputs:
1. DC output: Generally there are two types: solid-state relay and mechanical relay, and the output voltage also has different options.
2. AC output: Similar to AC input, the output signal needs to closely match the device parameters.
3. Relay output: A common way to connect external devices to PLC. It is necessary to make sure that the power supply and current match.
4. Analog output: Outputs proportional digital signals, the most common ones are 0-10V and 4-20mA.
In short, ensuring the safety, matching, grounding and correct circuit connection of the input and output ports is the key to PLC operation. In actual application, parameter settings and connection methods are generally determined according to equipment requirements and PLC manuals or installation instructions.
Previous article:Common conversion methods for PLC data types
Next article:What is the difference between PLC input and output types
Recommended ReadingLatest update time:2024-11-16 09:30
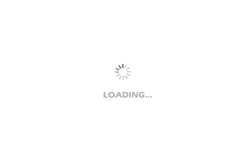
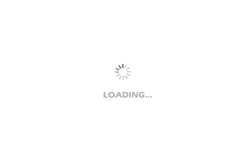
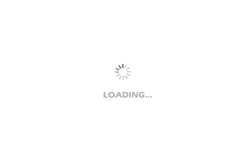
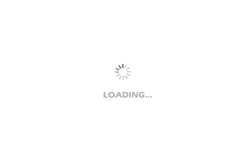
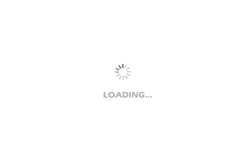
- Popular Resources
- Popular amplifiers
- Huawei's Strategic Department Director Gai Gang: The cumulative installed base of open source Euler operating system exceeds 10 million sets
- Analysis of the application of several common contact parts in high-voltage connectors of new energy vehicles
- Wiring harness durability test and contact voltage drop test method
- Sn-doped CuO nanostructure-based ethanol gas sensor for real-time drunk driving detection in vehicles
- Design considerations for automotive battery wiring harness
- Do you know all the various motors commonly used in automotive electronics?
- What are the functions of the Internet of Vehicles? What are the uses and benefits of the Internet of Vehicles?
- Power Inverter - A critical safety system for electric vehicles
- Analysis of the information security mechanism of AUTOSAR, the automotive embedded software framework
Professor at Beihang University, dedicated to promoting microcontrollers and embedded systems for over 20 years.
- Innolux's intelligent steer-by-wire solution makes cars smarter and safer
- 8051 MCU - Parity Check
- How to efficiently balance the sensitivity of tactile sensing interfaces
- What should I do if the servo motor shakes? What causes the servo motor to shake quickly?
- 【Brushless Motor】Analysis of three-phase BLDC motor and sharing of two popular development boards
- Midea Industrial Technology's subsidiaries Clou Electronics and Hekang New Energy jointly appeared at the Munich Battery Energy Storage Exhibition and Solar Energy Exhibition
- Guoxin Sichen | Application of ferroelectric memory PB85RS2MC in power battery management, with a capacity of 2M
- Analysis of common faults of frequency converter
- In a head-on competition with Qualcomm, what kind of cockpit products has Intel come up with?
- Dalian Rongke's all-vanadium liquid flow battery energy storage equipment industrialization project has entered the sprint stage before production
- Allegro MicroSystems Introduces Advanced Magnetic and Inductive Position Sensing Solutions at Electronica 2024
- Car key in the left hand, liveness detection radar in the right hand, UWB is imperative for cars!
- After a decade of rapid development, domestic CIS has entered the market
- Aegis Dagger Battery + Thor EM-i Super Hybrid, Geely New Energy has thrown out two "king bombs"
- A brief discussion on functional safety - fault, error, and failure
- In the smart car 2.0 cycle, these core industry chains are facing major opportunities!
- The United States and Japan are developing new batteries. CATL faces challenges? How should China's new energy battery industry respond?
- Murata launches high-precision 6-axis inertial sensor for automobiles
- Ford patents pre-charge alarm to help save costs and respond to emergencies
- New real-time microcontroller system from Texas Instruments enables smarter processing in automotive and industrial applications
- ON Semiconductor RSL10 Technical Features, Toolkits, Case Studies and Other Documents
- Is there a camera that works with the F746GDISCOVERY development board?
- Sub-library: Summary of official Chinese technical documents of accelerometers
- Re-study the comparator of MSP430
- Filter capacitor value after bridge rectification
- Please look at this circuit, why is the output signal like this, the DC operating point is fine
- Three-phase watt-hour meter transformer wiring
- How to export the sensor data on sensorile?
- Power amplifier application in the production of piezoelectric vibration-driven rotating soft robots
- Application of Doherty amplifier in 450W digital TV transmitter