1. Connection between PLC and main electrical equipment
Figure 6-4 shows the wiring diagram for input devices such as buttons, travel switches, and conversion switches. The PLC in the figure is a DC junction input, that is, all input points share a common terminal COM, and the COM terminal has a DC24V power supply. If it is a group input, you can also refer to the method in Figure 6-4 for group connection
2. Connection between PLC and rotary encoder
A rotary encoder is a photoelectric rotary measuring device that directly converts the measured angular displacement into a digital signal (high-speed pulse signal). Therefore, the output pulse signal of the rotary encoder can be directly input to the PLC, and the pulse signal is counted by the high-speed counter of the PLC to obtain the measurement result. Different types of rotary encoders have different output pulse phases. Some rotary encoders output three-phase pulses of A, B, and Z, some only have two phases of A and B, and the simplest has only A phase.
Figure 6-7 shows the connection diagram of the rotary encoder that outputs two-phase pulses and the FX series PLC. The encoder has 4 leads, 2 of which are pulse output lines, 1 is the COM terminal line, and 1 is the power line. The encoder power supply can be an external power supply, or it can directly use the DC24V power supply of the PLC. The "-" end of the power supply should be connected to the COM end of the encoder, and the "+" end should be connected to the power end of the encoder. The COM end of the encoder is connected to the COM end of the PLC input, and the A and B two-phase pulse output lines are directly connected to the input end of the PLC. When connecting, pay attention to the response time of the PLC input. Some rotary encoders also have a shielded wire, which should be grounded when used.
3. Connection between PLC and sensor
There are many types of sensors, and their output methods are also different. When using two-wire sensors such as proximity switches and photoelectric switches, due to the large leakage current of the sensor, an erroneous input signal may occur, causing the PLC to malfunction. In this case, a bypass resistor R can be connected in parallel to the PLC input terminal, as shown in Figure 6-8. When the leakage current is less than 1mA, its impact can be ignored.
Where: I is the leakage current of the sensor (mA), UOFF is the upper limit of the low level of the PLC input voltage (V), RC is the input impedance of the PLC (KΩ), and the value of RC varies depending on the input point.
4. Connection between PLC and multi-position DIP switch
If some data in the PLC control system needs to be modified frequently, you can use a multi-position DIP switch to connect to the PLC and set the data outside the PLC. Figure 6-5 shows a schematic diagram of a single-position DIP switch. A single-position DIP switch can input a decimal number 0 to 9 or a hexadecimal number 0 to F.
Figure 6-5 Schematic diagram of a single-bit dip switch
As shown in Figure 6-6, 4-position DIP switches are assembled together, and the COM terminals of each DIP switch are connected together and connected to the COM terminal on the PLC input side. The 4 data lines of each DIP switch are connected to the 4 input points of the PLC in a certain order. As can be seen from the figure, the use of DIP switches will occupy many PLC input points, so this method is generally not used unless it is absolutely necessary.
5. Connection between PLC and output device switch
When the PLC is connected to the output device, the voltage type and level of the corresponding output device (load) can be different for the output points of different groups (different common terminals), but the voltage type and level of the output points of the same group (same common terminal) should be the same. It is necessary to decide whether to connect in groups according to the type and level of the output device voltage. As shown in Figure 6-9, the connection method between the PLC and the output device is explained by taking FX2N as an example. The connection method in the figure is the case where the output devices have the same power supply, so the common terminals of each group are connected together, otherwise they must be connected in groups. The figure only shows the connection between the Y0-Y7 output points and the output device, and the connection methods of other output points are similar.
6. Connection between PLC and inductive load
The output end of the PLC is often connected to an inductive output device (inductive load). In order to suppress the voltage generated when the inductive circuit is disconnected and cause damage to the internal output components of the PLC, when the PLC is connected to an inductive output device, if it is a DC inductive load, a freewheeling diode should be connected in parallel at both ends; if it is an AC inductive load, a RC absorption circuit should be connected in parallel at both ends. As shown in Figure 6-10.
Figure 6-10 Connection between PLC and inductive output device
In the figure, the freewheeling diode can be selected with a rated current of 1A and a rated voltage greater than 3 times the power supply voltage; the resistance value can be 50~120Ω, the capacitance value can be 0.1~0.47μF, and the rated voltage of the capacitor should be greater than the peak voltage of the power supply. Pay attention to the polarity of the freewheeling diode when wiring.
7. Connection between PLC and seven-segment LED display
PLC can directly use switch output to connect to the seven-segment LED display, but if the PLC controls a multi-digit LED seven-segment display, many output points are required.
In the circuit shown in Figure 6-11, the chip CD4513 with latching, decoding and driving functions is used to drive the common cathode LED seven-segment display. The data input terminals A to D of the two CD4513 share the four output terminals of the PLC, where A is the lowest bit and D is the highest bit. LE is the latch enable input terminal. At the rising edge of the LE signal, the BCD number input from the data input terminal is latched in the register on the chip, and the number is decoded and displayed. If the input is not a decimal number, the display goes out. When LE is high, the displayed number is not affected by the data input signal. Obviously, the number of output points occupied by N displays is P=4+N.
If the PLC uses a relay output module, a pull-down resistor should be connected to each PLC output terminal connected to CD4513 to prevent the input terminal of CD4513 from being suspended when the output relay contacts are disconnected. When the state of the PLC output relay changes, its contacts may shake, so the data output signal should be sent first, and after the signal stabilizes, the data should be latched into CD4513 using the rising edge of the LE signal.
Previous article:What is Industrial Ethernet? What is the difference between Industrial Ethernet and ordinary Ethernet?
Next article:Several most commonly used PLC programming control circuits
Recommended ReadingLatest update time:2024-11-16 12:49
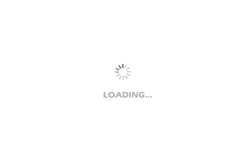
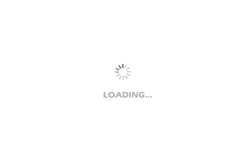
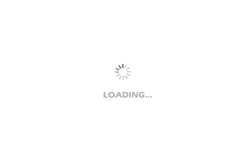
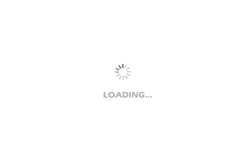
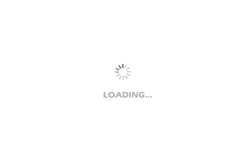
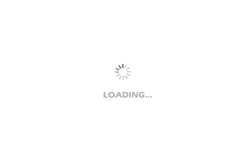
- Popular Resources
- Popular amplifiers
- Huawei's Strategic Department Director Gai Gang: The cumulative installed base of open source Euler operating system exceeds 10 million sets
- Analysis of the application of several common contact parts in high-voltage connectors of new energy vehicles
- Wiring harness durability test and contact voltage drop test method
- Sn-doped CuO nanostructure-based ethanol gas sensor for real-time drunk driving detection in vehicles
- Design considerations for automotive battery wiring harness
- Do you know all the various motors commonly used in automotive electronics?
- What are the functions of the Internet of Vehicles? What are the uses and benefits of the Internet of Vehicles?
- Power Inverter - A critical safety system for electric vehicles
- Analysis of the information security mechanism of AUTOSAR, the automotive embedded software framework
Professor at Beihang University, dedicated to promoting microcontrollers and embedded systems for over 20 years.
- Innolux's intelligent steer-by-wire solution makes cars smarter and safer
- 8051 MCU - Parity Check
- How to efficiently balance the sensitivity of tactile sensing interfaces
- What should I do if the servo motor shakes? What causes the servo motor to shake quickly?
- 【Brushless Motor】Analysis of three-phase BLDC motor and sharing of two popular development boards
- Midea Industrial Technology's subsidiaries Clou Electronics and Hekang New Energy jointly appeared at the Munich Battery Energy Storage Exhibition and Solar Energy Exhibition
- Guoxin Sichen | Application of ferroelectric memory PB85RS2MC in power battery management, with a capacity of 2M
- Analysis of common faults of frequency converter
- In a head-on competition with Qualcomm, what kind of cockpit products has Intel come up with?
- Dalian Rongke's all-vanadium liquid flow battery energy storage equipment industrialization project has entered the sprint stage before production
- Allegro MicroSystems Introduces Advanced Magnetic and Inductive Position Sensing Solutions at Electronica 2024
- Car key in the left hand, liveness detection radar in the right hand, UWB is imperative for cars!
- After a decade of rapid development, domestic CIS has entered the market
- Aegis Dagger Battery + Thor EM-i Super Hybrid, Geely New Energy has thrown out two "king bombs"
- A brief discussion on functional safety - fault, error, and failure
- In the smart car 2.0 cycle, these core industry chains are facing major opportunities!
- The United States and Japan are developing new batteries. CATL faces challenges? How should China's new energy battery industry respond?
- Murata launches high-precision 6-axis inertial sensor for automobiles
- Ford patents pre-charge alarm to help save costs and respond to emergencies
- New real-time microcontroller system from Texas Instruments enables smarter processing in automotive and industrial applications
- Register for the live broadcast to win [bracelet, camera, umbrella, mobile phone holder] Rohde & Schwarz USB 3.2 conformance test
- Newbie question, please help! I just learned analog electronics and built a simple circuit using Multisim
- 【Zero Knowledge ESP8266】Tutorial: Mobile APP Control RGB LED
- The application of CAN bus data in automobile digital technology is the starting point
- TI AM335 Embedded Hardware Design Reference Guide OK335xD
- Infineon Position2Go Development Kit Review @2. Official Tools
- Application of ISP chips in edge computing
- [Atria AT32WB415 Review] 2. Firmware burning (taking AT-Link burning as an example)
- MOS tube anti-reverse connection
- Why do DSPs with large on-chip RAM have high efficiency?