Who is the father of brushless motor?
The inventor and pioneer of brushless motors can be traced back to the 1960s, when German electrical engineer Werner Gartner first proposed the concept and design of brushless DC motors.
In the following decades, brushless motors have been widely studied and applied, and many scientists, engineers and entrepreneurs have made important contributions to the development of brushless motors.
However, if we talk about the father of brushless motors, we have to mention Japanese electrical engineer Takashi Kenjo. In the early 1980s, Kenjo and his team began to study brushless motor technology and developed the world's first commercial brushless motor in 1982. This motor uses a new type of permanent magnet material and a unique control algorithm, which greatly improves efficiency and performance, becoming an important milestone in the development of brushless motor technology. Subsequently, Kenjo also made many other contributions in the field of brushless motors and was hailed as the "Father of Brushless Motors."
What are the advantages of brushless motors
Compared with traditional brushed motors, brushless motors have the following advantages:
High efficiency: Because brushless motors use electronic controllers to achieve the potential switching of the rotor windings, eliminating the mechanical commutation losses present in brushed motors, the efficiency of brushless motors is usually 10% to 15% higher than that of brushed motors.
Low noise: There is no contact between the rotor winding and the stator winding of the brushless motor, and no brush noise is generated due to mechanical commutation. Therefore, the noise of the brushless motor is usually lower than that of the brushed motor.
Long life: Since brushless motors have no brushes, they have a longer lifespan. And because brushless motors have higher efficiency and lower heat loss, using brushless motors can reduce the thermal sublimation and mechanical loss of the motor, further extending the life of the motor.
High precision: Since brushless motors use electronic controllers to achieve potential switching of the rotor windings, more precise speed and torque control can be achieved. Therefore, brushless motors are suitable for applications that require high-precision speed and torque control.
The manufacturing cost of brushless motors is relatively high, and because they require the support of electronic controllers, the system design and control are relatively complex. When applying them, actual needs and costs must be considered.
What are the types of brushless motors?
The types of brushless motors can be classified according to rotor structure, stator structure and application areas.
Classification by rotor structure:
Outer rotor brushless motor: The rotor is located outside the stator and is usually used in high-speed, high-power applications such as electric vehicles and wind power generation;
Inner rotor brushless motor: The rotor is located inside the stator and is usually used in low-speed, low-power applications such as household appliances, power tools, etc.
Classification by stator structure:
Steel core stator brushless motor: The stator consists of a steel core and windings, usually used for high-speed, high-power applications;
Centerless stator brushless motor: The stator has no steel core and the windings are directly fixed to the housing. It is usually used for low speed and low power applications.
Classification by application field:
Industrial brushless motor: usually used in industrial automation, robotics, CNC machine tools and other fields;
Consumer electronics brushless motors: usually used in home appliances, power tools, smart phones and other fields;
Electric vehicle brushless motor: commonly used in electric bicycles, electric vehicles and other fields.
Working principle of brushless motor
The working principle of brushless motor is based on the law of electromagnetic induction and the Hall effect.
The brushless motor consists of two parts: a rotor and a stator. The stator has several groups of coils, and the rotor has permanent magnets or a magnetic field generated by electromagnetic induction.
When power is applied to the coil on the stator, a rotating magnetic field is formed. The speed and direction of this rotating magnetic field are determined by the power frequency and the number of poles of the stator coil. At the same time, the permanent magnets or electromagnetic induction poles on the rotor are affected by the rotating magnetic field, generating a rotational torque and driving the rotor to rotate. In order to keep the motor running, the current and voltage need to be adjusted in real time through electronic components to control the rotation speed and direction.
In brushless motors, permanent magnets and Hall elements are usually installed on the rotor to achieve rotor commutation. When the permanent magnets and Hall elements pass through the stator coil, the Hall element senses the change in the magnetic field of the stator coil, thereby triggering the electronic components to control the adjustment of current and voltage, allowing the motor to rotate continuously.
In general, brushless motors achieve efficient, reliable, low-noise, and low-loss operation through electromagnetic induction and electronic regulation technology, and are widely used in various industrial and consumer electronic devices.
Previous article:Working principle and structure of DC motor
Next article:Servo drive external wiring diagram_Servo drive failure and repair
Recommended ReadingLatest update time:2024-11-16 13:46
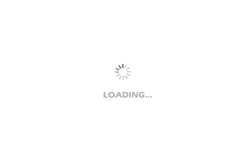
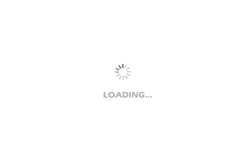
- Popular Resources
- Popular amplifiers
-
100 Examples of Microcontroller C Language Applications (with CD-ROM, 3rd Edition) (Wang Huiliang, Wang Dongfeng, Dong Guanqiang)
-
Dual Radar: A Dual 4D Radar Multimodal Dataset for Autonomous Driving
-
Real-time driver monitoring system via modal and viewpoint analysis
-
A review of learning-based camera and lidar simulation methods for autonomous driving systems
- Huawei's Strategic Department Director Gai Gang: The cumulative installed base of open source Euler operating system exceeds 10 million sets
- Analysis of the application of several common contact parts in high-voltage connectors of new energy vehicles
- Wiring harness durability test and contact voltage drop test method
- Sn-doped CuO nanostructure-based ethanol gas sensor for real-time drunk driving detection in vehicles
- Design considerations for automotive battery wiring harness
- Do you know all the various motors commonly used in automotive electronics?
- What are the functions of the Internet of Vehicles? What are the uses and benefits of the Internet of Vehicles?
- Power Inverter - A critical safety system for electric vehicles
- Analysis of the information security mechanism of AUTOSAR, the automotive embedded software framework
Professor at Beihang University, dedicated to promoting microcontrollers and embedded systems for over 20 years.
- Innolux's intelligent steer-by-wire solution makes cars smarter and safer
- 8051 MCU - Parity Check
- How to efficiently balance the sensitivity of tactile sensing interfaces
- What should I do if the servo motor shakes? What causes the servo motor to shake quickly?
- 【Brushless Motor】Analysis of three-phase BLDC motor and sharing of two popular development boards
- Midea Industrial Technology's subsidiaries Clou Electronics and Hekang New Energy jointly appeared at the Munich Battery Energy Storage Exhibition and Solar Energy Exhibition
- Guoxin Sichen | Application of ferroelectric memory PB85RS2MC in power battery management, with a capacity of 2M
- Analysis of common faults of frequency converter
- In a head-on competition with Qualcomm, what kind of cockpit products has Intel come up with?
- Dalian Rongke's all-vanadium liquid flow battery energy storage equipment industrialization project has entered the sprint stage before production
- Allegro MicroSystems Introduces Advanced Magnetic and Inductive Position Sensing Solutions at Electronica 2024
- Car key in the left hand, liveness detection radar in the right hand, UWB is imperative for cars!
- After a decade of rapid development, domestic CIS has entered the market
- Aegis Dagger Battery + Thor EM-i Super Hybrid, Geely New Energy has thrown out two "king bombs"
- A brief discussion on functional safety - fault, error, and failure
- In the smart car 2.0 cycle, these core industry chains are facing major opportunities!
- The United States and Japan are developing new batteries. CATL faces challenges? How should China's new energy battery industry respond?
- Murata launches high-precision 6-axis inertial sensor for automobiles
- Ford patents pre-charge alarm to help save costs and respond to emergencies
- New real-time microcontroller system from Texas Instruments enables smarter processing in automotive and industrial applications
- Will 5G really bring about big changes?
- Today I suddenly thought of this: If resistors of the same resistance are first connected in series and then in parallel, what is the resistance after N?
- Let’s talk about high technology today… Why is a chip so difficult to make?
- I thought foreign manufacturers were indifferent to the RISC-V core...
- 【Zero Knowledge ESP8266 Project】1 OLED Weather Clock
- Mobile 5G device antenna tuning revealed
- What is switching AC-DC conversion?
- About PIN-to-PIN compatibility between SI24R1 and NRF24L01P
- Huawei_Large-Scale Logic Design Guide.rar
- Announcement: Participants in the last round of the lottery will be given 11.11 yuan to purchase a multimeter, soldering station, and development board