Correctly connecting the input and output lines is the prerequisite for ensuring the reliable operation of the PLC. To correctly connect the input and output lines of the PLC and the 7 types of equipment, you need to pay attention to the following aspects:
1. Connection between PLC and main electrical equipment
The following figure is a wiring diagram of PLC and main electrical input devices such as buttons, travel switches, and transfer switches. The PLC in the figure is a DC junction input, that is, all input points share a common terminal COM, and the COM terminal has a DC24V power supply. If it is a group input, you can also refer to the method in the figure below for group connection.
Using the mixed signal wireless transmitter DTD120FHC, the DCS control cabinet PLC in the control room can monitor the temperature and pressure of boilers and other equipment in real time, and remotely control the hot air valve position switch of the cement line through wireless means.
Wireless communication scheme diagram▼
2. Connection between PLC and rotary encoder
The figure shows the connection diagram of the rotary encoder with two-phase pulse output and FX series PLC. The COM terminal of the encoder is connected to the COM terminal of the PLC input, and the A and B two-phase pulse output lines are directly connected to the input terminal of the PLC. When connecting, pay attention to the response time of the PLC input. Some rotary encoders also have a shielded wire, which must be grounded when used.
3. Connection between PLC and sensor
There are many types of sensors, and their output methods are also different. When using two-wire sensors such as proximity switches and photoelectric switches, due to the large leakage current of the sensor, an erroneous input signal may occur, causing the PLC to malfunction. In this case, a bypass resistor R can be connected in parallel to the PLC input terminal, as shown in Figure 6-8. When the leakage current is less than 1mA, its impact can be ignored.
The two-way mixed signal wireless device DTD122FHCY is used to wirelessly transmit the collected sensor data such as the moisture content of the concentration tank and the clean water flow rate to the PLC of the local programmable control cabinet, and then the PLC program is used to judge and output control instructions to the scraper.
Wireless communication scheme diagram▼
4. Connection between PLC and multi-position DIP switch
The following figure shows 4-position DIP switches assembled together. The COM terminals of each DIP switch are connected together and connected to the COM terminal on the PLC input side. The 4 data lines of each DIP switch are connected to the 4 input points of the PLC in a certain order. As can be seen from the figure, the use of DIP switches will occupy many PLC input points, so this method should not be used unless it is absolutely necessary.
5. Connection between PLC and output device switch
Take FX2N as an example to explain the connection method between PLC and output devices. The connection method in the figure is the case where the output devices have the same power supply, so the common ends of each group are connected together, otherwise they must be connected in groups. The figure only shows the connection between the Y0-Y7 output points and the output device, and the connection methods of other output points are similar.
Using Mitsubishi PLC wireless communication terminal DTD435MC, Kunlun Tongtai uses Mitsubishi PLC FX2N programming port to read and write the corresponding registers of PLC stations through a dedicated protocol.
6. Connection between PLC and inductive load
In the figure, the freewheeling diode can be selected with a rated current of 1A and a rated voltage greater than 3 times the power supply voltage; the resistance value can be 50~120Ω, the capacitance value can be 0.1~0.47μF, and the rated voltage of the capacitor should be greater than the peak voltage of the power supply. Pay attention to the polarity of the freewheeling diode when wiring.
7. Connection between PLC and seven-segment LED display
In the circuit shown in the figure, the chip CD4513 with latching, decoding and driving functions is used to drive the common cathode LED seven-segment display. The data input terminals A to D of the two CD4513 share the four output terminals of the PLC, where A is the lowest bit and D is the highest bit.
Previous article:SG_Background Control of VASS KUKA Electric Servo Welding Gun
Next article:Design of 2D digital servo valve controller based on current sampling module
Recommended ReadingLatest update time:2024-11-16 10:52
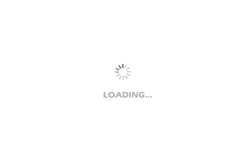
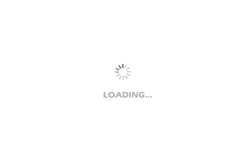
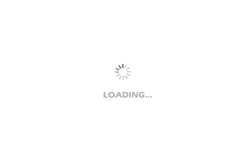
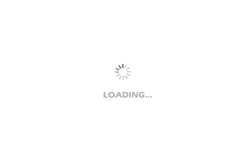
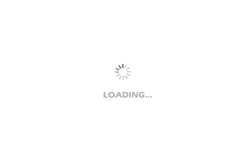
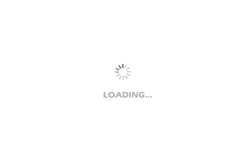
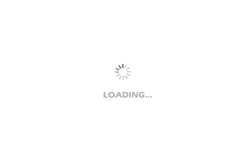
- Popular Resources
- Popular amplifiers
- Huawei's Strategic Department Director Gai Gang: The cumulative installed base of open source Euler operating system exceeds 10 million sets
- Analysis of the application of several common contact parts in high-voltage connectors of new energy vehicles
- Wiring harness durability test and contact voltage drop test method
- Sn-doped CuO nanostructure-based ethanol gas sensor for real-time drunk driving detection in vehicles
- Design considerations for automotive battery wiring harness
- Do you know all the various motors commonly used in automotive electronics?
- What are the functions of the Internet of Vehicles? What are the uses and benefits of the Internet of Vehicles?
- Power Inverter - A critical safety system for electric vehicles
- Analysis of the information security mechanism of AUTOSAR, the automotive embedded software framework
Professor at Beihang University, dedicated to promoting microcontrollers and embedded systems for over 20 years.
- Innolux's intelligent steer-by-wire solution makes cars smarter and safer
- 8051 MCU - Parity Check
- How to efficiently balance the sensitivity of tactile sensing interfaces
- What should I do if the servo motor shakes? What causes the servo motor to shake quickly?
- 【Brushless Motor】Analysis of three-phase BLDC motor and sharing of two popular development boards
- Midea Industrial Technology's subsidiaries Clou Electronics and Hekang New Energy jointly appeared at the Munich Battery Energy Storage Exhibition and Solar Energy Exhibition
- Guoxin Sichen | Application of ferroelectric memory PB85RS2MC in power battery management, with a capacity of 2M
- Analysis of common faults of frequency converter
- In a head-on competition with Qualcomm, what kind of cockpit products has Intel come up with?
- Dalian Rongke's all-vanadium liquid flow battery energy storage equipment industrialization project has entered the sprint stage before production
- Allegro MicroSystems Introduces Advanced Magnetic and Inductive Position Sensing Solutions at Electronica 2024
- Car key in the left hand, liveness detection radar in the right hand, UWB is imperative for cars!
- After a decade of rapid development, domestic CIS has entered the market
- Aegis Dagger Battery + Thor EM-i Super Hybrid, Geely New Energy has thrown out two "king bombs"
- A brief discussion on functional safety - fault, error, and failure
- In the smart car 2.0 cycle, these core industry chains are facing major opportunities!
- The United States and Japan are developing new batteries. CATL faces challenges? How should China's new energy battery industry respond?
- Murata launches high-precision 6-axis inertial sensor for automobiles
- Ford patents pre-charge alarm to help save costs and respond to emergencies
- New real-time microcontroller system from Texas Instruments enables smarter processing in automotive and industrial applications
- E-coin exchange
- How to easily stabilize an op amp with inductive open loop output impedance?
- Request a free ZVS buck regulator evaluation board
- Live broadcast at 13:00 this afternoon|2020 STM32 National Seminar in Shenzhen
- 7" Touch Screen Monitor Stand for Raspberry Pi SmartiPi Touch 2
- Up to $180,000! Apple temporarily issues large bonuses to prevent employees from leaving Meta
- [Rawpixel RVB2601 development board trial experience] 5. Key interrupt test
- Xunwei IMX6Q development board QT system Modbus transplantation and use (I)
- Infrared thermometer
- Reading notes of the good book "Operational Amplifier Parameter Analysis and LTspice Application Simulation" 01 cover page