introduction
Flow rate, frequency response and accuracy are important indicators for evaluating the quality of electro-hydraulic servo systems. How to improve performance and meet various application scenarios has become an important topic that needs to be broken through in the research of electro-hydraulic servo systems. The electro-hydraulic servo valve is the core control component of the electro-hydraulic servo system, and its performance largely determines the performance of the entire system.
The continuous development of digital control technology has promoted the emergence of digital valves, such as 2D digital servo valves. Since the 2D digital servo valve integrates the pilot stage and the power stage on the valve core, it has the advantages of simple structure, small size, fast response speed, high accuracy, and good anti-pollution ability, which makes it well used in the military field.
The 2D digital servo valve uses a stepper motor as an electro-mechanical converter, and its performance largely determines the performance of the 2D digital servo valve.
Control Principle of 2D Digital Servo Valve
The mechanical part of the 2D digital servo valve is mainly composed of a valve core and a valve body. The name comes from the fact that the valve core can complete both horizontal and rotational movements in the valve body. The 2D digital servo valve
uses a servo screw mechanism to integrate the power stage and the pilot stage on the valve core. By changing the control signal and adjusting the internal algorithm of the controller, the current of the two-phase winding of the electro-mechanical converter (stepper motor) changes, the rotation angle of the electro-mechanical converter is changed, and the valve core is driven to rotate through the lever and fork mechanism. For the specific structure, please refer to Reference 3.
While the valve core rotates, due to the change in the pressure of the sensitive chamber, the valve core simultaneously moves linearly, changing the opening amount of the valve port and realizing the regulation of the flow rate.
The 2D digital servo valve uses a hybrid stepper motor as the electro-mechanical converter. Traditionally, stepper motors work in a stepping manner, which makes the valve resolution low. Although the subdivision method can increase the number of analog pole pairs and improve the resolution, it reduces the response speed of the valve, and there is a contradiction between resolution and response speed.
In fact, the hybrid stepper motor can be essentially regarded as a multi-pole permanent magnet induction synchronous motor. When the two-phase windings of the motor are respectively connected to currents with a phase difference of 90°, a rotating magnetic field will be generated inside the motor. Under the action of this rotating magnetic field, the motor rotor rotates. When the two-phase current changes for one cycle, the rotating magnetic field rotates for one cycle inside the current, and the motor rotor rotates through a pitch angle. Therefore, by controlling the two-phase current, the rotating motion of the rotating magnetic field can be driven to quickly position the rotor at any position.
Based on the above ideas, a dual closed-loop control method of current and position of the stepper motor is proposed here, as shown in Figure 1. In Figure 1, the purpose of the current closed loop is to generate a rotating magnetic field of a constant amplitude that drives the motor rotor to quickly position at any position.
The purpose of the position closed loop in Figure 1 is to achieve position control of the rotor without losing step, overcoming the inevitable loss of step under the traditional control of the stepper motor. Through the dual closed-loop control of current and position, the 2D digital servo valve electro-mechanical converter has both high response speed and resolution.
Figure 1 Control principle of 2D digital valve electromechanical converter
Controller hardware and software design
2.1 Controller Hardware Design
1) Design of the main control unit
The fuzzy PID control algorithm is used in the control of the electro-mechanical converter to achieve real-time adjustment of PID parameters and improve the dynamic and static characteristics. The main control chip selected in the design is the TMS320F28335DSP chip.
This chip is a floating-point digital signal processing chip that can calculate 32-bit multiplication and addition operations. The main frequency can reach up to 150MHz and can be used to control motors and various power equipment. The
main control chip mainly completes the processing of the sampling values of the two-phase current and the angular displacement values of the displacement sensor, and realizes algorithms such as PID control and phase compensation. The schematic diagram of the main control circuit is shown in Figure 2.
Figure 2 Schematic diagram of the main control circuit
2) Design of drive module
The electro-mechanical converter uses a two-phase hybrid stepper motor, which requires two H-bridge units for control. Each H-bridge unit consists of four MOS EFT tubes and other devices such as resistors, capacitors, and diodes. This makes the controller larger and is not conducive to integration with the valve body. To solve this problem, this design uses the A5988: a four-way DMOS full-bridge PWM motor driver chip.
The A5988 is a four-way DMOS full-bridge driver IC that can drive up to two stepper motors or four DC machines. Each full-bridge output is rated at 1.6 A and 40 V. The A5988 includes a fixed-off-time pulse width modulation (PWM) current regulator and a 2-bit nonlinear DAC (digital-to-analog converter). The DAC can control the stepper motor in full-step, half-step, quarter-step, or eighth-step mode, and can control the DC motor in forward, reverse, and coasting modes. The PWM current regulator uses Allegro's patented mixed decay mode to reduce audible motor noise, increase step accuracy, and reduce power dissipation.
An internal synchronous rectification control circuit is provided to improve power consumption during PWM operation. Protection features include hysteresis thermal shutdown, undervoltage lockout (UVLO) and crossover current protection. No special power-up sequencing is required. The drive circuit diagram is shown in Figure 3.
Figure 3 Driver module design
3) Current sampling module design
Current sampling generally uses a resistor in series in the loop, and uses Ampere's theorem to detect the voltage drop on the resistor to obtain the current flowing through the resistor. The sampling resistor is relatively precise and has a relatively small resistance value, generally around 0.01 to 0.1Ω. Since the amplitude of the detected current is large, the required sampling resistor is also large in power and volume. In order to reduce the volume of the controller, this design uses the ACS712 (or domestic chip CH701) linear Hall current sensor.
The sensor has a high-precision, low-bias and linear Hall sensor integrated inside. When the Hall sensor detects the magnetic field generated by the current flowing through the copper conductor path, it converts it into a proportional voltage. The maximum current that can flow through this sensor is 5A, and the impedance of the internal copper conductor path is 1.2mΩ, so the power loss is relatively small.
When there is no current flowing through the sensor, the voltage at the output port is 50% of the supply voltage, with an accuracy of 0.185V/A. The sampled output voltage needs to be converted by the amplifier and input into the AD module of the DSP. The current sampling module is mainly used to sample the two-phase current of the stepper motor, thereby forming a current closed loop and improving the control accuracy and response speed. The specific design circuit is shown in Figure 4.
Figure 4 Current sampling circuit
2.2 Controller software design
The software is mainly used to realize the dual closed loop of current and position, as well as phase compensation, etc. The duty cycle of the output PWM wave is adjusted through the algorithm to change the current size of the two-phase winding. The system program flow chart is shown in Figure 5.
The software design is mainly divided into the interrupt program design of modules such as ePWM, SPI and AD.
Figure 5 Program flow chart
1) ePWM interrupt subroutine
The ePWM interrupt subroutine mainly implements the current loop and position loop double closed loop based on the input signal, the angular displacement signal detected by the angular displacement sensor, and the two-phase current detected by the current sensor. The control accuracy and dynamic and static characteristics are further improved through PID and phase compensation algorithms. At the same time, the subroutine also completes the search for the zero position after power-on.
2) SPI interrupt subroutine
The SPI interrupt subroutine is mainly used to receive the rotation angle of the rotor of the electro-mechanical converter (stepper motor) output by the angular displacement sensor and process it. In order to improve the accuracy of the angular displacement signal, the angular displacement values sampled three times are sorted, and then the middle value is taken as the current angular displacement value.
3) AD interrupt subroutine
The input signal and the sampling values of the two-phase current must be sampled by AD, and then averaged and input into the DSP as the input signal and current sampling values. The AD module of F28335 has 16 sampling circuits, which can sample the input signal and current sampling signal multiple times, and then sort the sampling values, remove the large and small extreme values, and perform average calculation to obtain the sampling current and input signal.
in conclusion
Using CH701 as the current detection chip, changing the current detection method and the driving method of the electro-mechanical converter not only facilitates the integration of the valve body and the controller, but also improves the dynamic and static characteristics of the servo valve.
Through experiments, it can be known that under the control of the designed controller, the bandwidth of the 2D digital servo valve is about 180Hz, and the step rise time is 6.5ms, which improves the overall performance of the servo valve.
The CH701 Hall current sensor IC is an economical and accurate solution for AC or DC current sensing in industrial, automotive, commercial and communication systems.
The small package is ideal for space-constrained applications and saves costs by reducing the circuit board area. Typical applications include motor control, load detection and management, switching power supplies and overcurrent fault protection.
Previous article:How to correctly connect PLC and the input and output lines of 7 types of equipment
Next article:The fundamental difference between permanent faults and transient faults in digital circuits
Recommended ReadingLatest update time:2024-11-16 09:40
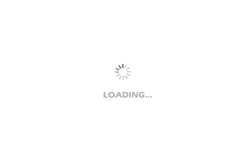
- Popular Resources
- Popular amplifiers
-
Introduction to Internet of Things Engineering 2nd Edition (Gongyi Wu)
-
Permanent Magnet Synchronous Motor Speed Control System Control Technology (by Hou Limin and Wang Wei)
-
Implementing a Deep Learning Framework with Python (Zhang Juefei, Chen Zhen)
-
A Complete Illustrated Guide to Operational Amplifier Applications (Written by Wang Zhenhong)
- Huawei's Strategic Department Director Gai Gang: The cumulative installed base of open source Euler operating system exceeds 10 million sets
- Analysis of the application of several common contact parts in high-voltage connectors of new energy vehicles
- Wiring harness durability test and contact voltage drop test method
- Sn-doped CuO nanostructure-based ethanol gas sensor for real-time drunk driving detection in vehicles
- Design considerations for automotive battery wiring harness
- Do you know all the various motors commonly used in automotive electronics?
- What are the functions of the Internet of Vehicles? What are the uses and benefits of the Internet of Vehicles?
- Power Inverter - A critical safety system for electric vehicles
- Analysis of the information security mechanism of AUTOSAR, the automotive embedded software framework
Professor at Beihang University, dedicated to promoting microcontrollers and embedded systems for over 20 years.
- Innolux's intelligent steer-by-wire solution makes cars smarter and safer
- 8051 MCU - Parity Check
- How to efficiently balance the sensitivity of tactile sensing interfaces
- What should I do if the servo motor shakes? What causes the servo motor to shake quickly?
- 【Brushless Motor】Analysis of three-phase BLDC motor and sharing of two popular development boards
- Midea Industrial Technology's subsidiaries Clou Electronics and Hekang New Energy jointly appeared at the Munich Battery Energy Storage Exhibition and Solar Energy Exhibition
- Guoxin Sichen | Application of ferroelectric memory PB85RS2MC in power battery management, with a capacity of 2M
- Analysis of common faults of frequency converter
- In a head-on competition with Qualcomm, what kind of cockpit products has Intel come up with?
- Dalian Rongke's all-vanadium liquid flow battery energy storage equipment industrialization project has entered the sprint stage before production
- Allegro MicroSystems Introduces Advanced Magnetic and Inductive Position Sensing Solutions at Electronica 2024
- Car key in the left hand, liveness detection radar in the right hand, UWB is imperative for cars!
- After a decade of rapid development, domestic CIS has entered the market
- Aegis Dagger Battery + Thor EM-i Super Hybrid, Geely New Energy has thrown out two "king bombs"
- A brief discussion on functional safety - fault, error, and failure
- In the smart car 2.0 cycle, these core industry chains are facing major opportunities!
- The United States and Japan are developing new batteries. CATL faces challenges? How should China's new energy battery industry respond?
- Murata launches high-precision 6-axis inertial sensor for automobiles
- Ford patents pre-charge alarm to help save costs and respond to emergencies
- New real-time microcontroller system from Texas Instruments enables smarter processing in automotive and industrial applications
- Audio Circuit Debugging Tips
- [TI recommended course] #Industry's first professional RGB LED driver LP50xx demonstration #
- How to get a multi-channel reference power supply
- TMS320F28335GPIO Example - Light up the LED
- Analysis of 2020 E-sports Contest C: The realization process of the 99-point ramp car
- MSP430F4152 development board schematic diagram
- Are there any recommended books for beginners in circuit development?
- MSP430 G2553 Launchpad implements capacitance measurement
- [GD32L233C-START Review] 12. Button - External Interrupt
- [Qinheng RISC-V core CH582] Environment configuration and lighting test