Solution 1: Reduce the size of the valve port. When the valve port size do=1.5mm, the valve opening pressure difference at 12o℃ is 1.4MPa: When the valve port size do is reduced to 1mm, the valve opening pressure difference at 120℃ is 3.1MPa, which can meet the valve opening pressure difference requirement of more than 2MPa in the whole temperature range. The calculation results are shown in Figure 5.
Solution 2: Increase the coil drive voltage. When the working voltage U=12V, the valve opening pressure difference at 120℃ is 1.4MPa: When the working voltage U increases to 14V, the valve opening pressure difference at 120℃ is 2.1MPa, which can meet the valve opening pressure difference requirement of more than 2MPa in the whole temperature range, as shown in Figure 6.
When increasing the voltage to increase the valve opening pressure difference, it is best to adapt temperature sensor monitoring and increase the voltage when the temperature reaches a certain range to avoid increasing the voltage throughout the entire stroke, thereby increasing energy consumption.
4 Conclusion
Based on the calculation formulas of magnetomotive force, electromagnetic force, and winding resistivity, this paper analyzes the influence of temperature on the magnetomotive force of the coil, the electromagnetic force of the solenoid valve, and the valve opening pressure difference. Taking the typical room temperature of 20°C and high temperature of 120°C as examples, the magnetomotive force decays by 28%, the electromagnetic force decays by 48%, and the valve opening pressure difference decays by 62%. Although the valve opening pressure difference is adapted and even redundant under room temperature conditions, in order to ensure product reliability, the valve opening pressure difference must be able to reach a standard greater than 2MPa in the full temperature operating range. The valve opening capacity decay caused by temperature rise can be ensured by adapting the appropriate valve port size or increasing the voltage to ensure that the driving capacity meets the standard in the full temperature range.
Previous article:Omron programmable controller CP2E-ECT officially released
Next article:A new copper tube busbar and its fixing device design for medium voltage switchgear
Recommended ReadingLatest update time:2024-11-16 19:49
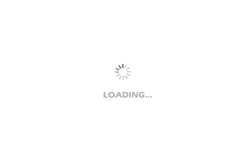
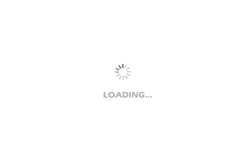
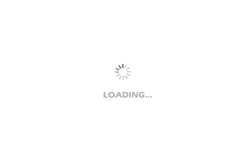
- Popular Resources
- Popular amplifiers
- Huawei's Strategic Department Director Gai Gang: The cumulative installed base of open source Euler operating system exceeds 10 million sets
- Analysis of the application of several common contact parts in high-voltage connectors of new energy vehicles
- Wiring harness durability test and contact voltage drop test method
- Sn-doped CuO nanostructure-based ethanol gas sensor for real-time drunk driving detection in vehicles
- Design considerations for automotive battery wiring harness
- Do you know all the various motors commonly used in automotive electronics?
- What are the functions of the Internet of Vehicles? What are the uses and benefits of the Internet of Vehicles?
- Power Inverter - A critical safety system for electric vehicles
- Analysis of the information security mechanism of AUTOSAR, the automotive embedded software framework
Professor at Beihang University, dedicated to promoting microcontrollers and embedded systems for over 20 years.
- Innolux's intelligent steer-by-wire solution makes cars smarter and safer
- 8051 MCU - Parity Check
- How to efficiently balance the sensitivity of tactile sensing interfaces
- What should I do if the servo motor shakes? What causes the servo motor to shake quickly?
- 【Brushless Motor】Analysis of three-phase BLDC motor and sharing of two popular development boards
- Midea Industrial Technology's subsidiaries Clou Electronics and Hekang New Energy jointly appeared at the Munich Battery Energy Storage Exhibition and Solar Energy Exhibition
- Guoxin Sichen | Application of ferroelectric memory PB85RS2MC in power battery management, with a capacity of 2M
- Analysis of common faults of frequency converter
- In a head-on competition with Qualcomm, what kind of cockpit products has Intel come up with?
- Dalian Rongke's all-vanadium liquid flow battery energy storage equipment industrialization project has entered the sprint stage before production
- Allegro MicroSystems Introduces Advanced Magnetic and Inductive Position Sensing Solutions at Electronica 2024
- Car key in the left hand, liveness detection radar in the right hand, UWB is imperative for cars!
- After a decade of rapid development, domestic CIS has entered the market
- Aegis Dagger Battery + Thor EM-i Super Hybrid, Geely New Energy has thrown out two "king bombs"
- A brief discussion on functional safety - fault, error, and failure
- In the smart car 2.0 cycle, these core industry chains are facing major opportunities!
- The United States and Japan are developing new batteries. CATL faces challenges? How should China's new energy battery industry respond?
- Murata launches high-precision 6-axis inertial sensor for automobiles
- Ford patents pre-charge alarm to help save costs and respond to emergencies
- New real-time microcontroller system from Texas Instruments enables smarter processing in automotive and industrial applications
- Three elements of switching power supplies and digital devices
- Online ESP32 Simulator
- 31 "Millions of Miles" Raspberry Pi Car——Ubuntu MATE System Installation
- ABB six-axis robot and Siemens 1500PLC user manual
- [Ateli Development Board AT32F421 Review] 7. Kuga registers jointly light up OLED
- Design and FPGA implementation of digital on-screen display control core.pdf
- EL817C Optocoupler Transmission Ratio Problem
- Keysight Technologies N9020A 3.6G spectrum analyzer special sale: 8500/unit
- STM32+photosensitive sensor+serial port receiving light intensity source program is successfully produced
- How does the uart.write function output three bytes of 0XFF 0XFF 0XFF (HEX data, not string data)?