01Related concepts
PLC: Programmable logic controller
The full name is programmable controller, which is an application system composed of a main control chip and peripheral circuits. It can pre-program instruction flows through programs to achieve specific functions. It is usually used in automation, industrial control and other fields. Its characteristics are high stability and easy programming and use.
Q: Why does PLC need to be used with an isolation barrier/isolator?
A: Because the working environment of the field equipment is relatively bad, if the signal sensor line to the PLC is broken and connected to other lines with different voltages or shorted to the equipment at the same time, strong electricity will enter the PLC input port, causing the entire module to burn and causing great losses. If this happens with the signal isolator, only the isolator will be damaged without damaging the PLC. In addition, it can prevent interference and stabilize the signal.
Analog signal:
The basic process signal (voltage, current, pressure, temperature, flow, etc.) input form in automated process control systems.
The process signals in the system are converted into unified voltage and current signals through the isolator, and these signals are transmitted to the controller (PLC) in real time.
DC 0~20mA, 4~20mA,
DC 0~5V, 1~5V, 0~10V
Pressure, temperature, flow, speed, valve opening, etc.
02. BM200 series isolated safety barrier
BM200 series isolated safety barrier:
Connected between intrinsically safe circuits and non-intrinsically safe circuits. A device that limits the voltage or current supplied to an intrinsically safe circuit to a certain safe range. Safety barriers are a general term, divided into Zener safety barriers and isolation safety barriers. Isolation safety barriers are referred to as isolation barriers.
Detection end isolation safety barrier:
Equipment that receives signals from hazardous areas, isolates them, and then transmits them to safe areas can effectively limit the energy in hazardous areas from being transmitted to intrinsically safe circuits.
Operation end isolation safety barrier:
The control signal received in the safe area is isolated and then transmitted to the control equipment in the dangerous area for reception. It can be used to limit the amount of electrical energy supplied from the control room in the safe area to the field instrument, that is, to prevent the generation of sparks that can detonate dangerous gases, thereby eliminating the detonation source.
Selection related parameters
03. BM100 series signal isolator
BM100 series signal isolator:
Increase the safety and reliability of the system, and improve measurement accuracy and anti-interference capabilities.
It is essential to isolate the analog signal measurement circuit to ensure the safety and reliability of the output.
Three types of current input
Two-wire system: mainly for the front-end output power supply products (pressure sensor)
Three-wire system: one power line, one signal line, and one reference ground (reference ground for power and signal)
Current source: two signal lines, two independent power lines (four-wire system)
Output power supply type
There is no separate power terminal, power and output share the same terminal.
Passive type
No power terminal required
Input: DC 4~20mA
Output: DC 4~20mA
04. Functions of Isolation Barrier and Isolator
In practical applications, the signal interference problem of control systems is sometimes very serious.
Wiring method using signal isolation barrier/isolator
• Cut off the propagation path of conducted interference,
• Reduce signal distortion caused by ground loops directly connected to the device,
•Improved the anti-interference ability of analog signals
Once an accident occurs and the device is damaged, replacing the isolator is more time-saving and cost-effective than replacing the PLC/DCS module. Therefore, it is recommended to determine the installation based on the actual situation.
05. Application scenarios
06. The difference between isolated safety barriers and signal isolators
Isolation fence application scenarios:
Petroleum, chemical industry, thermal power, gas, metallurgy
Isolator application scenarios:
Wind power, new energy, water treatment, robots, automobiles
The isolated safety barrier can replace the signal isolator, but the signal isolator cannot replace the isolated safety barrier. However, the costs are different, so it is recommended to choose according to actual usage needs.
Previous article:Application of frequency converter in slitting machine control
Next article:PLC working process and input and output processing principles
Recommended ReadingLatest update time:2024-11-16 10:34
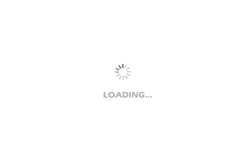
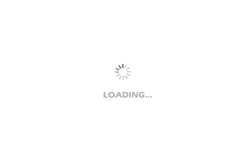
- Popular Resources
- Popular amplifiers
- Huawei's Strategic Department Director Gai Gang: The cumulative installed base of open source Euler operating system exceeds 10 million sets
- Analysis of the application of several common contact parts in high-voltage connectors of new energy vehicles
- Wiring harness durability test and contact voltage drop test method
- Sn-doped CuO nanostructure-based ethanol gas sensor for real-time drunk driving detection in vehicles
- Design considerations for automotive battery wiring harness
- Do you know all the various motors commonly used in automotive electronics?
- What are the functions of the Internet of Vehicles? What are the uses and benefits of the Internet of Vehicles?
- Power Inverter - A critical safety system for electric vehicles
- Analysis of the information security mechanism of AUTOSAR, the automotive embedded software framework
Professor at Beihang University, dedicated to promoting microcontrollers and embedded systems for over 20 years.
- Innolux's intelligent steer-by-wire solution makes cars smarter and safer
- 8051 MCU - Parity Check
- How to efficiently balance the sensitivity of tactile sensing interfaces
- What should I do if the servo motor shakes? What causes the servo motor to shake quickly?
- 【Brushless Motor】Analysis of three-phase BLDC motor and sharing of two popular development boards
- Midea Industrial Technology's subsidiaries Clou Electronics and Hekang New Energy jointly appeared at the Munich Battery Energy Storage Exhibition and Solar Energy Exhibition
- Guoxin Sichen | Application of ferroelectric memory PB85RS2MC in power battery management, with a capacity of 2M
- Analysis of common faults of frequency converter
- In a head-on competition with Qualcomm, what kind of cockpit products has Intel come up with?
- Dalian Rongke's all-vanadium liquid flow battery energy storage equipment industrialization project has entered the sprint stage before production
- Allegro MicroSystems Introduces Advanced Magnetic and Inductive Position Sensing Solutions at Electronica 2024
- Car key in the left hand, liveness detection radar in the right hand, UWB is imperative for cars!
- After a decade of rapid development, domestic CIS has entered the market
- Aegis Dagger Battery + Thor EM-i Super Hybrid, Geely New Energy has thrown out two "king bombs"
- A brief discussion on functional safety - fault, error, and failure
- In the smart car 2.0 cycle, these core industry chains are facing major opportunities!
- The United States and Japan are developing new batteries. CATL faces challenges? How should China's new energy battery industry respond?
- Murata launches high-precision 6-axis inertial sensor for automobiles
- Ford patents pre-charge alarm to help save costs and respond to emergencies
- New real-time microcontroller system from Texas Instruments enables smarter processing in automotive and industrial applications
- QuartusSetup-13.1.0.162.exe installation error
- The simulation application of common mode inductors is here, full of useful information for everyone!
- Use memset function to assign values to char array
- Overvoltage protection
- Get a sneak peek at TI's latest reference design! EE Benefits
- Four-pin active crystal oscillator circuit diagram
- What does RB mean in the package?
- EEWORLD University ---- IoT Moment: The True Definition of IoT
- 【NXP Rapid IoT Review】+ Bluetooth Operation (3 Receiving Data)
- When the MCU is running, the contents stored in the EEPROM are all changed to FF. What is the reason?