Today, let’s talk about the controller of the proportional control valve, mainly to understand the PWM control principle.
1. Digital signals and analog signals
The principle of the proportional control valve controller is that when the controller receives a current signal, it converts the current into a voltage of the required value.
The proportional control valve controller uses the PWM control method to convert the input current signal into an average voltage output.
The PWM control here is the abbreviation of Pulse Width Modulation, which is a pulse width modulation control method. That is, digital electrical signals can be used to obtain effects similar to analog signals.
In the electrical signal method, analog signals can naturally change the value of the signal continuously over time.
Therefore, the waveform has a curved shape and there are an infinite number of points.
However, digital signals are discontinuous and have only signal values of 0 and 1, so a waveform like a city wall will appear.
2. Take the brightness of a light bulb as an example to describe the role of the PWM signal
Here, PWM control is a technology that adjusts the pulse (waveform) width of a digital signal and follows the precise signal shape of an analog signal.
What methods can be used to achieve this?
These electrical signals basically change so quickly that they are difficult for humans to recognize.
Here, it is sufficient to appropriately adjust the "ON (no power)" and "OFF (no power)" of the digital transmission signal and adjust the duty cycle, which is the duration ratio of the "ON" state within a cycle.
For example, the digital signal 0 = 0V, 1 = 5V. When 0V, the light bulb is off; when 5V, the light bulb is on.
What happens if a 100% duty cycle is applied until some time T?
Because the ON-OFF ratio of the digital transmission signal is 100:0, the average voltage of 5V is output and the bulb will be 100% lit.
This time, I will give a 90% duty cycle until some time T.
That is, the ON:OFF ratio is 90:10.
Then, the average voltage will be 4.5V and the bulb brightness will be 90%.
This time, we set the duty cycle to 50% until a certain time T, and how about setting the ON:OFF ratio to 50:50?
Then, an average voltage of 2.5V will be output, making the bulb only 50% brighter.
Finally, if the duty cycle is 0% and the ON:OFF ratio is 0:100, then no current will flow and the bulb will be off.
In this way, the ON-OFF ratio of the rated voltage within one cycle can be adjusted, changing the average voltage output.
It is also possible to use digital methods to simulate analog signals that have multiple values.
When the controller sends an electrical signal to the solenoid coil of the proportional control valve through PWM control, the proportional control valve can adjust the balance between the spring force and the plunger magnetic force according to the signal value (average voltage value), thereby freely changing the degree of opening and closing of the flow path.
3. Describe the role of PWM using a proportional valve as an example
Let's connect the controller to a proportional control valve and take a look at its functionality.
When the flow path of the proportional control valve is opened to the maximum extent, the maximum air flow rate that can flow through the valve is 250L per minute, and the signal current value that can be input into the controller is 4mA~20mA.
At this point, if we want the valve to have a flow rate of about 20%, that is, 50 liters of air per minute.
Then, when the signal controller flow of the device is 20%, a signal current value of 7mA should be sent to the controller.
At this time, the controller receives the signal and applies the programmed average voltage DC7V to the valve, opening the valve's flow path by about 20% and allowing 50 liters of air to flow through per minute.
Previous article:PLC Programming: Technical Summary Using Siemens Products as Examples
Next article:TSMC's big move! 20 new wafer fabs added in Taiwan
Recommended ReadingLatest update time:2024-11-16 14:36
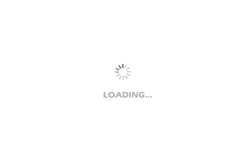
- Huawei's Strategic Department Director Gai Gang: The cumulative installed base of open source Euler operating system exceeds 10 million sets
- Analysis of the application of several common contact parts in high-voltage connectors of new energy vehicles
- Wiring harness durability test and contact voltage drop test method
- Sn-doped CuO nanostructure-based ethanol gas sensor for real-time drunk driving detection in vehicles
- Design considerations for automotive battery wiring harness
- Do you know all the various motors commonly used in automotive electronics?
- What are the functions of the Internet of Vehicles? What are the uses and benefits of the Internet of Vehicles?
- Power Inverter - A critical safety system for electric vehicles
- Analysis of the information security mechanism of AUTOSAR, the automotive embedded software framework
Professor at Beihang University, dedicated to promoting microcontrollers and embedded systems for over 20 years.
- Innolux's intelligent steer-by-wire solution makes cars smarter and safer
- 8051 MCU - Parity Check
- How to efficiently balance the sensitivity of tactile sensing interfaces
- What should I do if the servo motor shakes? What causes the servo motor to shake quickly?
- 【Brushless Motor】Analysis of three-phase BLDC motor and sharing of two popular development boards
- Midea Industrial Technology's subsidiaries Clou Electronics and Hekang New Energy jointly appeared at the Munich Battery Energy Storage Exhibition and Solar Energy Exhibition
- Guoxin Sichen | Application of ferroelectric memory PB85RS2MC in power battery management, with a capacity of 2M
- Analysis of common faults of frequency converter
- In a head-on competition with Qualcomm, what kind of cockpit products has Intel come up with?
- Dalian Rongke's all-vanadium liquid flow battery energy storage equipment industrialization project has entered the sprint stage before production
- Allegro MicroSystems Introduces Advanced Magnetic and Inductive Position Sensing Solutions at Electronica 2024
- Car key in the left hand, liveness detection radar in the right hand, UWB is imperative for cars!
- After a decade of rapid development, domestic CIS has entered the market
- Aegis Dagger Battery + Thor EM-i Super Hybrid, Geely New Energy has thrown out two "king bombs"
- A brief discussion on functional safety - fault, error, and failure
- In the smart car 2.0 cycle, these core industry chains are facing major opportunities!
- The United States and Japan are developing new batteries. CATL faces challenges? How should China's new energy battery industry respond?
- Murata launches high-precision 6-axis inertial sensor for automobiles
- Ford patents pre-charge alarm to help save costs and respond to emergencies
- New real-time microcontroller system from Texas Instruments enables smarter processing in automotive and industrial applications
- [ATmega4809 Curiosity Nano Review] Development Environment Setup
- This old Skyworth LCD TV again
- The difference and usage of passive crystal and active crystal oscillator
- Transformer driven half bridge
- CircuitPython 4.1.0 Beta 0 released
- [Solved] Why can’t I change my profile picture?
- The STM32F103VBT6 resets with a button. After releasing the button, it takes three or four seconds for the microcontroller to execute the program.
- "【TGF4042 Signal Generator】" High-frequency distortion measurement
- EEWORLD University ---- Tektronix TBS2000B Review Video
- 5G WiFi can save some energy